如何设计一个基于PLC的饮料灌装生产线控制系统,并确保其在生产过程中具备高效率和稳定性?
时间: 2024-11-16 10:27:05 浏览: 35
针对设计基于PLC的饮料灌装生产线控制系统,首先需要了解其在自动化技术中的核心作用。选择合适的PLC型号是关键,它需要具备足够的输入/输出接口、高速的处理能力和稳定的运行性能。硬件设计应包括选择与PLC兼容的传感器、执行器、电机驱动器等组件,并确保它们与PLC之间的接口设计合理,满足生产流水线的控制需求。例如,流量计用于监测灌装速度,压力传感器用于检测灌装压力,确保精度控制。软件设计方面,应采用梯形图、指令列表或结构化文本等PLC编程语言编写控制程序,实现对各个执行元件的精确控制。同时,应用PID控制算法可以提高灌装过程的准确性。为了进一步提升生产效率,可以集成先进的通信协议,如Profibus或Profinet,实现数据的实时监控和故障的快速诊断。最后,系统的集成与测试阶段需要反复调试,优化控制逻辑和参数设定,以达到最佳的生产效果。案例研究和效果评估将帮助验证系统的稳定性和效率提升,为未来的优化和升级提供依据。在整个设计过程中,参考《PLC控制下的饮料灌装生产线系统设计毕业论文》可以提供更详尽的设计思路和实施细节,帮助理解并解决实际问题。
参考资源链接:[PLC控制下的饮料灌装生产线系统设计毕业论文](https://wenku.csdn.net/doc/52tie7mmov?spm=1055.2569.3001.10343)
相关问题
请详细介绍如何设计一个基于PLC的饮料灌装生产线控制系统,以及如何确保其在生产过程中具备高效率和稳定性。
为了设计一个基于PLC的饮料灌装生产线控制系统,并确保其高效率和稳定性,可以参考这篇《PLC控制下的饮料灌装生产线系统设计毕业论文》。该论文全面地讲解了从系统设计到实施的各个环节,为你提供了详尽的理论基础和实践指导。
参考资源链接:[PLC控制下的饮料灌装生产线系统设计毕业论文](https://wenku.csdn.net/doc/52tie7mmov?spm=1055.2569.3001.10343)
在设计这样一个系统时,首先需要对整个生产线的工作流程有深刻的理解,包括瓶子的搬运、灌装、封口、贴标等工序。基于这些需求,我们才能确定PLC系统的控制目标和性能参数。
硬件设计方面,选择合适的PLC模块及其接口对于整个系统至关重要。你需要确保PLC与传感器、执行器等硬件设备兼容,且能够处理高速信号和实时数据。数据采集和传输系统的构建也必须考虑到信号的准确性和抗干扰能力。
在软件设计层面,编写PLC程序是实现控制逻辑的关键。利用梯形图或语句表等编程语言,你可以实现对灌装速度和量的精确控制。PID控制算法的应用能够保证灌装的精度,而报警系统则能在设备异常时及时响应。
系统集成与测试是确保设计成功的重要环节。你需要在模拟环境下测试系统的各项功能,如故障自动检测和处理机制,确保在实际生产中能够稳定运行。实际运行的测试则需要考虑多种情况,如不同灌装量、不同速度下的表现等。
最后,案例研究与效果评估是检验系统设计是否满足预期目标的重要手段。通过数据分析,可以评估系统在提升生产效率、降低成本以及减少误差等方面的具体效果。
总结来说,设计一个高效率和稳定的PLC控制饮料灌装生产线,需要综合考虑硬件选择、软件编程、系统集成、测试验证等多方面因素。通过严谨的设计流程和测试,可以确保控制系统在实际生产中的表现满足工业自动化的要求。
参考资源链接:[PLC控制下的饮料灌装生产线系统设计毕业论文](https://wenku.csdn.net/doc/52tie7mmov?spm=1055.2569.3001.10343)
设计一个基于PLC的饮料灌装生产线控制系统时,需要考虑哪些核心要素以及如何实现生产效率的最大化和系统的稳定性?
为了设计一个高效的基于PLC的饮料灌装生产线控制系统,你需要深入理解PLC的基本工作原理和特点,并结合实际的生产需求进行周密的规划和设计。以下是需要考虑的核心要素以及实现方案的详细描述:
参考资源链接:[PLC控制下的饮料灌装生产线系统设计毕业论文](https://wenku.csdn.net/doc/52tie7mmov?spm=1055.2569.3001.10343)
1. 需求分析:首先明确饮料灌装生产线的具体要求,包括灌装速度、精度控制、物料追踪、故障处理等,确保控制系统的设计能覆盖这些需求。
2. 硬件选择:选择合适的PLC型号,考虑其处理能力、I/O点数、通信接口等是否满足生产线的需求。同时,设计传感器和执行器的接口电路,以实现精确的流量控制和状态监测。
3. 软件逻辑设计:编写PLC程序,采用梯形图或指令列表等编程语言来实现控制逻辑。在程序中应用PID控制算法以精确控制灌装量,设计故障诊断和报警系统以提高系统的稳定性。
4. 系统集成:将PLC控制系统与生产线上其他设备(如传感器、执行器、HMI等)集成,确保数据采集和传输的实时性和准确性。
5. 系统测试:在实际生产环境中测试系统的性能,包括灌装精度、响应时间、故障恢复等,确保系统稳定运行。
6. 优化与调整:根据测试结果,对系统进行必要的优化和调整,比如调整控制参数,改进硬件结构或软件程序,以达到生产效率最大化。
在实现高效率和系统稳定性方面,可以通过以下几个关键点来确保:
- 使用高速处理的PLC以降低系统的响应时间。
- 对灌装过程进行动态监控,及时调整控制参数以适应变化的生产条件。
- 引入先进的故障预测和维护策略,以减少停机时间。
- 通过实时数据采集和分析,不断优化生产流程,减少浪费。
通过上述方法的综合运用,可以在确保生产线高效稳定运行的同时,为生产商提供灵活的生产调整能力和高质量的产品输出。为了进一步深入了解相关的技术和策略,你可以查阅《PLC控制下的饮料灌装生产线系统设计毕业论文》这份资料,它不仅详细介绍了系统的设计和实施过程,还包含实际案例分析和系统效果评估,能够为你的设计和应用提供全面的支持和参考。
参考资源链接:[PLC控制下的饮料灌装生产线系统设计毕业论文](https://wenku.csdn.net/doc/52tie7mmov?spm=1055.2569.3001.10343)
阅读全文
相关推荐
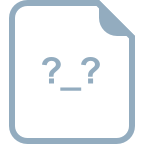
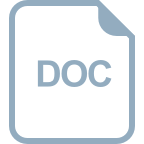
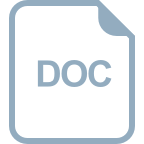













