精益生产:增值比率揭示改善潜力
需积分: 50 197 浏览量
更新于2024-08-24
收藏 4.43MB PPT 举报
本文主要探讨了精益思想在制造业中的应用,特别是通过增值比率来评估生产过程中的改进空间。精益生产起源于20世纪50年代的丰田汽车公司,其核心理念是针对微利时代的市场竞争和全球化需求,提出了五大精益生产原则。文章首先介绍了制造系统的发展历程,从亨利·福特的大规模流水线生产(Assembly Line)到丰田生产系统(Toyota Production System, TPS),后者强调了准时化(Just-In-Time, JIT)和拉动式生产模式(Pull System),以适应小批量、定制化的市场需求。
精益生产系统的关键点包括:
1. **低批量与定制化**:精益生产强调对小订单、多样化产品的处理能力,与大规模生产模式形成对比。
2. **同步生产**:确保生产活动与需求同步,避免过度库存,提高生产效率。
3. **敏捷生产组织**:响应市场变化快速,能灵活调整生产计划和资源配置。
4. **精益原则**:包括消除浪费(如过度生产、等待、运输等)、持续改进、授权员工参与决策等,旨在最大化增值时间。
增值时间是指在制造周期中,真正为客户创造价值的活动,例如产品改变形状、性能提升、组装和包装等环节。然而,实际统计显示,物料从进厂到出厂,只有大约10%的时间属于增值活动,这凸显了精益生产优化流程、减少非增值活动的重要性。
文章还涵盖了精益生产的具体实践工具和技术,如价值流分析(Value Stream Mapping)用于识别生产过程中的瓶颈和浪费,看板拉动(Pull System)作为拉动生产的可视化工具,以及精益指标的设定和推行策略的模拟演练。这些方法帮助企业在提高运行效率的同时,实现质量、成本和交货周期的优化。
在整个培训课程中,参与者将学习如何应用精益理念,进行现场管理和班组建设,以及如何构建柔性生产单元和精益供应链,以提升企业的整体竞争力。通过深入讨论和实战演练,参与者能够更好地理解和实施精益生产,提升企业运营效益。
2022-12-26 上传
2021-08-25 上传
2022-07-08 上传
2021-10-14 上传
2015-05-22 上传
2012-08-14 上传
2021-08-25 上传
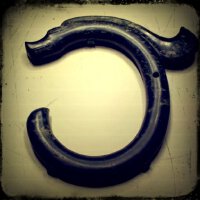
劳劳拉
- 粉丝: 20
- 资源: 2万+
最新资源
- 探索AVL树算法:以Faculdade Senac Porto Alegre实践为例
- 小学语文教学新工具:创新黑板设计解析
- Minecraft服务器管理新插件ServerForms发布
- MATLAB基因网络模型代码实现及开源分享
- 全方位技术项目源码合集:***报名系统
- Phalcon框架实战案例分析
- MATLAB与Python结合实现短期电力负荷预测的DAT300项目解析
- 市场营销教学专用查询装置设计方案
- 随身WiFi高通210 MS8909设备的Root引导文件破解攻略
- 实现服务器端级联:modella与leveldb适配器的应用
- Oracle Linux安装必备依赖包清单与步骤
- Shyer项目:寻找喜欢的聊天伙伴
- MEAN堆栈入门项目: postings-app
- 在线WPS办公功能全接触及应用示例
- 新型带储订盒订书机设计文档
- VB多媒体教学演示系统源代码及技术项目资源大全