SCADA、DCS与PLC详解:智能工厂的关键控制器
需积分: 45 19 浏览量
更新于2024-08-14
收藏 8.89MB PPT 举报
SCADA(数据采集与监控系统),DCS(分布式控制系统),和PLC(可编程逻辑控制器)是工业自动化中三种关键的控制系统,它们在工业4.0和智能工厂的背景下扮演着重要角色。
1. SCADA:
- 重点与功能:SCADA主要关注于远程监控和控制,其核心是数据采集和集中显示,它将现场设备的数据传输到中央控制室,便于操作人员实时查看和管理。尽管SCADA可以实现部分逻辑功能,但它的优势在于简化操作界面,提供直观的监控界面(HMI)。
- 应用场景:广泛应用于各类广域环境,如水处理、能源传输、交通系统等,因其能够有效监控和远程操作,对于大型、分散的基础设施管理至关重要。
2. DCS:
- 特点:DCS系统是集中监控与分布式控制的结合,通过模块化设计减少单点故障影响,提高系统稳定性。它更适用于过程自动化,特别是对控制精度要求高的场合,如化工、炼油、制药等。
- 原理与功能:DCS将控制功能分布到各个生产单元,通过网络连接协调局部控制器,实现全面的生产过程控制。
3. PLC:
- 核心作用:PLC是控制层级的关键组件,它具有可编程能力,能实现复杂的逻辑控制、定时、计数等功能。PLC不仅支持工业设备的操作,还在SCADA和DCS系统中起着至关重要的执行作用,实现工艺流程的精确控制。
- 应用场景:PLC广泛用于各种工业环境,无论是SCADA系统还是DCS系统中,都不可或缺,是实现本地过程管理和设备控制的基础。
工业4.0与智能工厂的发展强调了信息技术的深度融合,如综合布线系统提供了标准化的通信基础设施,支持多种系统间的高效协同。智能制造系统架构考虑了设备层级、控制层级、车间层级、企业层级和协同层级的智能化整合,涉及生命周期管理、物联网技术的应用以及全球范围内的生产分工与合作。
《中国制造2025》的战略聚焦于10大重点领域,如物联网能源管控、高端装备制造业等,推动工业生产的智能化升级。历史上的工业革命阶段划分了各国的崛起和变迁,而工业4.0则进一步加速了全球范围内的数字化转型。
总结来说,SCADA、DCS和PLC是工业自动化控制的不同层次和手段,它们在智能工厂中各自承担着不可或缺的角色,共同构建起高效、灵活且智能的生产环境。随着科技的进步,这些系统将不断演进,推动工业4.0时代的持续创新和发展。
303 浏览量
415 浏览量
2023-05-12 上传
2019-09-25 上传
2021-09-19 上传
点击了解资源详情
点击了解资源详情
点击了解资源详情
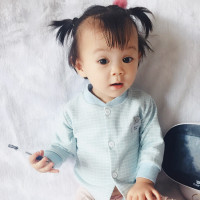
永不放弃yes
- 粉丝: 917
- 资源: 2万+
最新资源
- 行业文档-设计装置-一种带语音录入和播放功能的历史教具.zip
- rp-study.github.io:ACM IMC 2020论文“关于衡量RPKI依赖方”
- data_preprocessing:使用Pandas,Numpy,Tensorflow,KoNLPy,Scikit Learn进行数据预处理的方法
- First-android-app:那是我的第一个android应用。 它基于Google的教程
- redhat离线静默安装oracle11g资源
- MinecraftVirus:这是由GamerFiveYT制造的病毒
- spring boot动态多数据源demo
- R代表数据科学
- x86_64-支持x86_64特定的指令,寄存器和结构-Rust开发
- contact-functions
- 行业文档-设计装置-一种具有储冷功能的平行流蒸发器芯体.zip
- TinyMCE(可视化HTML编辑器) v5.0.4
- dusty:玩具多线程沙“游戏”
- Space Invaders Remake-开源
- hello-python-project:从头开始探索CLI工具的PyPI打包
- 欧姆食品