MRP基础:原理、应用与杉德公司案例
需积分: 48 35 浏览量
更新于2024-08-14
收藏 2.86MB PPT 举报
本资源主要探讨了企业MRP设计原理及实现方案,涵盖了MRP(物料需求计划)的发展历程及其关键概念。从早期的定货点法到后来的时段式MRP和闭环MRP,直至MRPII(制造资源计划)和ERP(企业资源计划),这些阶段反映了制造业库存管理和生产计划的演进。
1. **定货点法** (1940年代):这是早期的基本库存管理策略,通过设定物料的定货点来决定何时补货,以解决不缺料和少积压的问题。定货点法依赖于历史消耗率和预先确定的提前期,但缺乏灵活性,且对需求预测准确性要求较高。
2. **时段式MRP** (20世纪60年代):引入了时间维度,考虑了物料需求的时间序列,解决了定货点法中的即时需求和到货时间不确定性。它通过分解物料需求为独立和相关需求,结合物料清单(BOM)和生产计划,提高了计划的精确性。
3. **闭环MRP** 和 **MRPII** (1970年代至1980年代):闭环MRP强调了反馈机制,将生产过程中的实际消耗和库存状态纳入计划,使得需求预测更为准确。MRPII在此基础上进一步发展,集成生产、物流、财务等多方面信息,实现资源优化配置。
4. **ERP** (1990年代):企业资源计划的出现,标志着管理信息系统向全面集成和模块化方向发展,能够处理企业全局的信息流和业务流程。
5. **SANDMRP设计方案**:这部分内容具体介绍了SAND公司针对MRP的实施策略,包括系统在实际企业中的应用,强调了如何创建和设计MRP基础数据,如车间WIP(在制品)和BOM结构,以及工艺路线等,确保MRP规则的有效执行。
6. **设计原则**:在设计MRP时,关键因素包括定义明确的Item(库存)数据、完善的BOM结构、精确的工艺路线以及合理的前提条件。应用MRP时,需要根据企业的实际情况,灵活运用独立需求和相关需求的方法,同时考虑到提前期、安全库存、最大库存等因素,制定出切实可行的采购和生产计划。
本资源提供了详尽的MRP系统设计框架,从历史背景到当前实践,帮助企业理解和实施有效的物料需求计划,提升生产效率和资源利用率。
2013-11-22 上传
2023-02-08 上传
2022-09-20 上传
点击了解资源详情
2023-05-15 上传
2023-06-25 上传
2023-05-15 上传
2024-05-19 上传
2023-06-10 上传
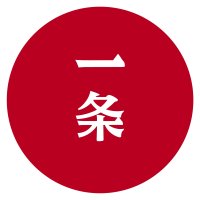
白宇翰
- 粉丝: 26
- 资源: 2万+
最新资源
- C++标准程序库:权威指南
- Java解惑:奇数判断误区与改进方法
- C++编程必读:20种设计模式详解与实战
- LM3S8962微控制器数据手册
- 51单片机C语言实战教程:从入门到精通
- Spring3.0权威指南:JavaEE6实战
- Win32多线程程序设计详解
- Lucene2.9.1开发全攻略:从环境配置到索引创建
- 内存虚拟硬盘技术:提升电脑速度的秘密武器
- Java操作数据库:保存与显示图片到数据库及页面
- ISO14001:2004环境管理体系要求详解
- ShopExV4.8二次开发详解
- 企业形象与产品推广一站式网站建设技术方案揭秘
- Shopex二次开发:触发器与控制器重定向技术详解
- FPGA开发实战指南:创新设计与进阶技巧
- ShopExV4.8二次开发入门:解决升级问题与功能扩展