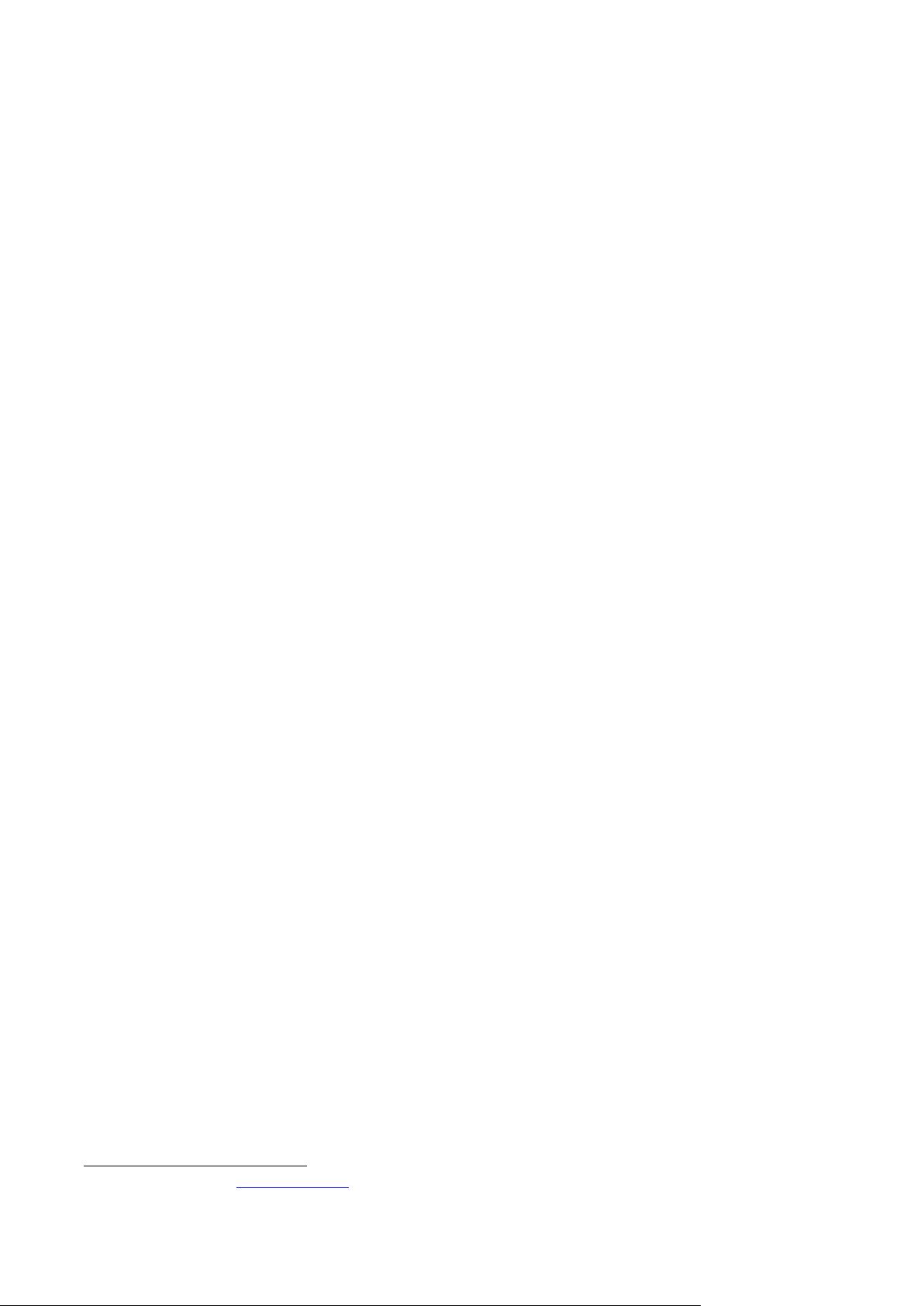
Development of an Airfoil-Based Aeroelastic
Energy Harvester driven by Alternating Airflow
Shenyu Liu, Fei Fei*, Changcheng Wu, Min Yang and Dehua Yang
Institute of Automation, Nanjing University of Aeronautics and Astronautics, Nanjing, 211106, China
{liushenyu, fei.fei, changchengwu, yang.min, dhyang}@nuaa.edu.cn
Abstract—Wireless sensor networks (WSNs) have been
widely used for intelligent monitoring applications. However,
due to the short lifetime of chemical batteries, the maintenance
of WSNs system has been high-cost and time-consuming.
This paper presents an airfoil-based energy harvester aiming
to scavenging aeroelastic energy from alternating airflows.
Two types of airfoil model (NACA6412 and NACA23012) are
used in the experiments to verify the performance of
prototypes in a wind tunnel. 15V peak-to-peak voltage can be
reached under airflow speed of 8.9m/s and -5 degree attack
angle, and the maximum power is about 7μW with 20kΩ load
resistance.
Keywords—WSNs; airfoil-based energy harvester;aeroelastic
energy
I. INTRODUCTION
The advent and development of WSNs and integrated
circuits technologies have greatly facilitated the monitoring
of environment, especially in remote or hazardous areas.
Compared with wired sensors, WSNs show its great
superiority, such as significantly reducing the use of
communication cables and installation costs. The operation
of WSNs nodes requires a stable source of electrical power,
while in many scenarios, the environment is diverse,
sometimes even in extreme condition. In most situations,
battery has a short working life as well as limited storage and
occupies the significant part of the node, meantime, it’s also
the most expensive part of the system, coupled with its
replacement and maintenance costs. As the power
consumption of nodes decreases from milliwatt to microwatt,
EH technology can truly replace the traditional battery for
continuous supply [1,2].
There are kinds of available energy sources in nature,
such as wind airflow and sunshine illumination, which can
provide energy to drive electrical devices via energy
harvesting technology. As a kind of clean and renewable
energy source, wind power generation has a tremendous
growth over the past decade and its global installed capacity
has increased by at least 10 times. However, when it comes
to small-scale structure, wind energy harvester made of
piezoelectric materials is mechanically simpler and more
efficient. The transformation from airflow energy into
electrical energy via wind-induced oscillations in an
un-uniform field is called aeroelastic energy conversion.
Although aeroelastic oscillation phenomenon is mostly
harmful to many of engineering structures, it is a kind of
*Corresponding author: fei.fei@nuaa.edu.cn. This work was
supported by the National Science Foundation of China under
Grant No. 61501226
high efficient energy conversion method in the perspective of
energy harvesting[2-5].
In recent years, harvesting energy from aeroelastic
oscillations has attracted significant attentions. Many
researchers proposed novel principles and optimized system
design parameters in order to develop high efficient wind
energy harvesters. Biccario et al. [6] proposed an idea of
using nanostructured piezoelectric transducers to scavenge
energy at ultra-low wind speed (lower than 2m/s). Angelo et
al. [7] studied a small-scale wind-induced flutter energy
harvester (WIFEH) consisted of coils, magnets and a flutter
membrane, the experimental results showed the maximum
values of 3.84V and 9.20V can be achieved under 2.3m/s and
5m/s airflow speeds. Ostia et al. [8] investigated a kind of
PZT cantilever wind-induced energy harvester with gears to
drive a wireless flame sensor with a minimum wind speed of
5m/s.
This paper demonstrates a novel airfoil-based aeroelastic
energy harvester coupling with PZT bimorph, aiming to
improve harvesting efficiency and capability under different
wind conditions. Two kinds of airfoil models (NACA6412
and NACA23012) are simulated to investigate airflow
velocity distribution using CFD method. Several 3D-printing
prototypes are fabricated to verify the feasibility of these
novel harvester structures, and all the experiments are
conducted under the airflow speed ranging from 2 to 9 m/s in
a wind tunnel.
II. THEORETICAL ANALYSIS
The airfoil-based aeroelastic energy harvesting utilizes
the flutter phenomenon, which is a kind of self-excited
vibration caused by the coupling effect of inertia force,
elastic force and aerodynamic load. When the flow passes
through the airfoil, there will be two kinds of vibrations,
torsional vibration and flexural vibration, respectively.
Because of the existence of nonlinear factors in the process,
the system structure will maintain a certain vibration
amplitude after the flow velocity exceeds the flutter critical
speed. For two-dimensional airfoil flutter problem, it can be
simplified with the two degrees of freedom model, as shown
in Fig.1 [9-11]. Point C is the centroid of model, point P is
the reference point,
is the flow speed,
is the
aerodynamic lift force per length and
is the
aerodynamic moment per length. The governing aeroelastic
equations can be given as follows:
(1)
(2)