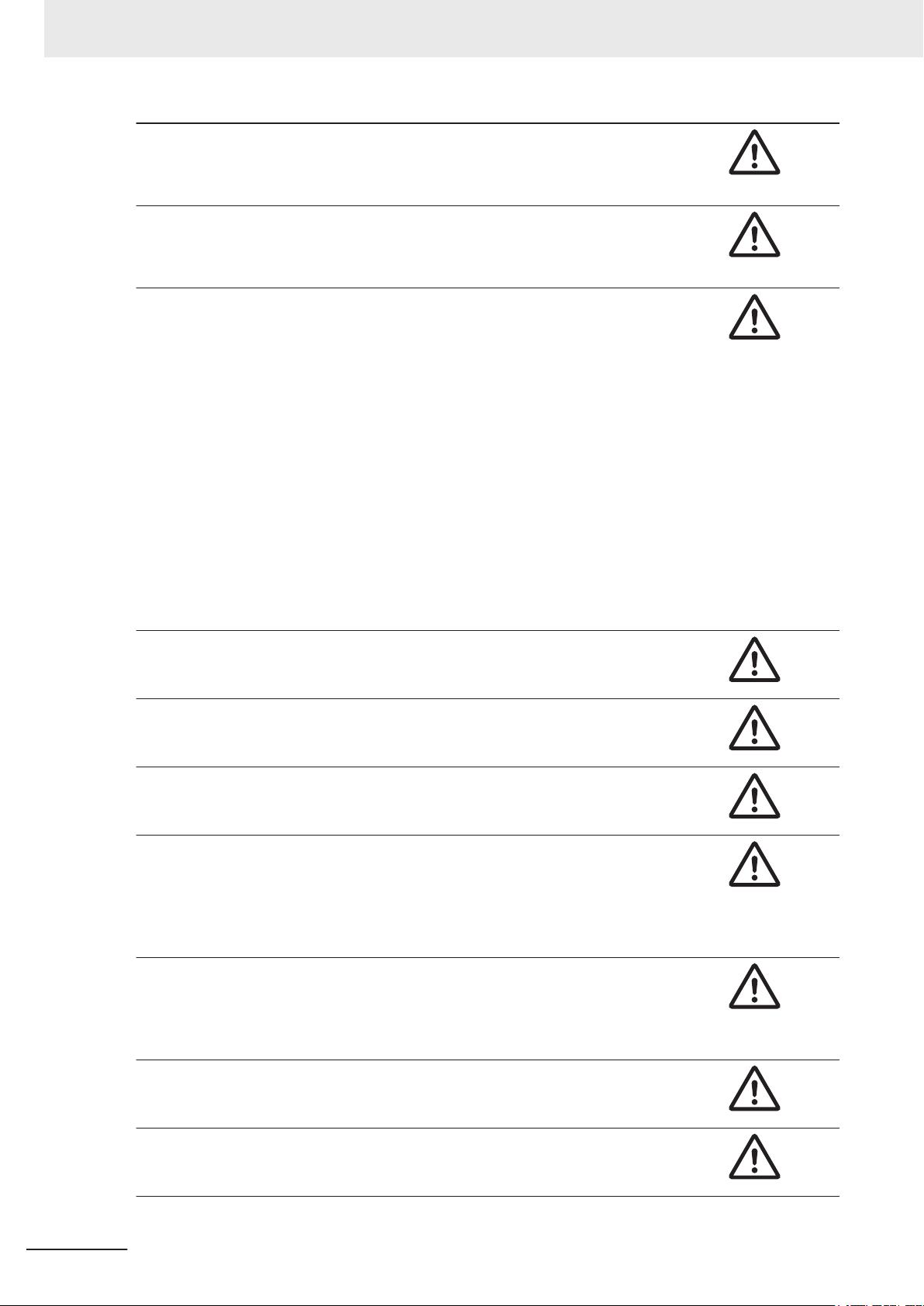
FH series does not comply with the laws and regulations for industrial robot safety. When us-
ing the FH series in a robot system that includes an industrial robot, be sure to check for
compliance with laws and regulations regarding the safety of industrial robots. T
ake steps to
ensure safety as needed.
It is your responsibility to implement appropriate safety measures based on the results of risk
assessment. Compliance with the Robot Safety Guide and all of the information contained in
our Robotic System Product Information does not guarantee that personal injury or damage
to equipment caused by an industrial robot will be avoided.
During maintenance, disconnect the robot's AC power supply and lock out or tag out the
power supply to prevent powering up. If the following safety measures are not taken, the
subject robot may cause death or serious injury or damage to the robot itself or its peripheral
equipment.
• W
orkers who install, operate, teach, program, or maintain the system should read the "Ro-
bot Connection Guide (Cat. No. Z448, Z447)" and "Robot Safety Guide (Cat. No. I590)"
and take a training course on their responsibilities with the robot.
• Those who design a robot system must read this document and the Robot Safety Guide
and follow the safety regulations and laws in the area where the robot will be installed.
• Do not use the subject robot for any purpose other than those described in this document
and the manuals referred to in the Robot Connection Guide. If you are not sure whether
your application is compatible, please contact us.
• The user is responsible for installing safety barriers around the robot to prevent workers
from entering the work area and coming into contact with it while it is in operation.
• During maintenance, the power to the robot and the main power supply must be locked
out and tagged out (measures and indication of prohibition from being turned on) to pre-
vent them from being turned on.
If you proceed to the next step before registering the HandEye calibration start position, the
robot may operate unintentionally
. Be sure to register the start position.
The robot is driven by pressing the Jog Move button and the Robot Move button. The opera-
tion must be done by shoes who have completed special health and safety training. The sys-
tem must be operated so that it can be stopped at any time by an emergency stop button.
Check the measurement results before operating the robot. Otherwise the robot may act in
an unintended manner
. Change the workpiece position and angle and check the operation
thoroughly.
If the robot is operated with an incorrectly shaped hand, the robot may pick and hold the
workpiece in an unintended position and/or posture, damaging the workpiece, container
, or
hand and causing it to fly out into the environment. Check the dimensions of the drawing and
the actual product and make registration securely. Change the workpiece position and angle
of picking/placing and check the operation thoroughly. The system must be operated so that
it can be stopped at any time by an emergency stop button.
If the robot is operated with an incorrectly selected picking and holding DB or hand data, the
robot may pick and hold the workpiece in an unintended position and/or posture, damaging
the workpiece, container
, or hand and causing it to fly out into the environment. Select the
proper picking and holding DB in the picking and holding plan setting. Make sure to perform
offline measurement before operating the robot to confirm that the proper hand is selected.
If the robot is operated with incorrect environment data, it may act in an unintended manner,
resulting in contact with humans, scattering of workpieces, and contact with surrounding ob-
jects. Make sure that the proper environment file for the robot is loaded.
If the robot is operated after changing the floor or container height, it may collide with the
floor
. If the container position or floor level is changed, register the floor level and container
again.
Safety Precautions
14
FH Series Vision System Hardware Setup Manual for 3D Robot Vision (Z436-E1)