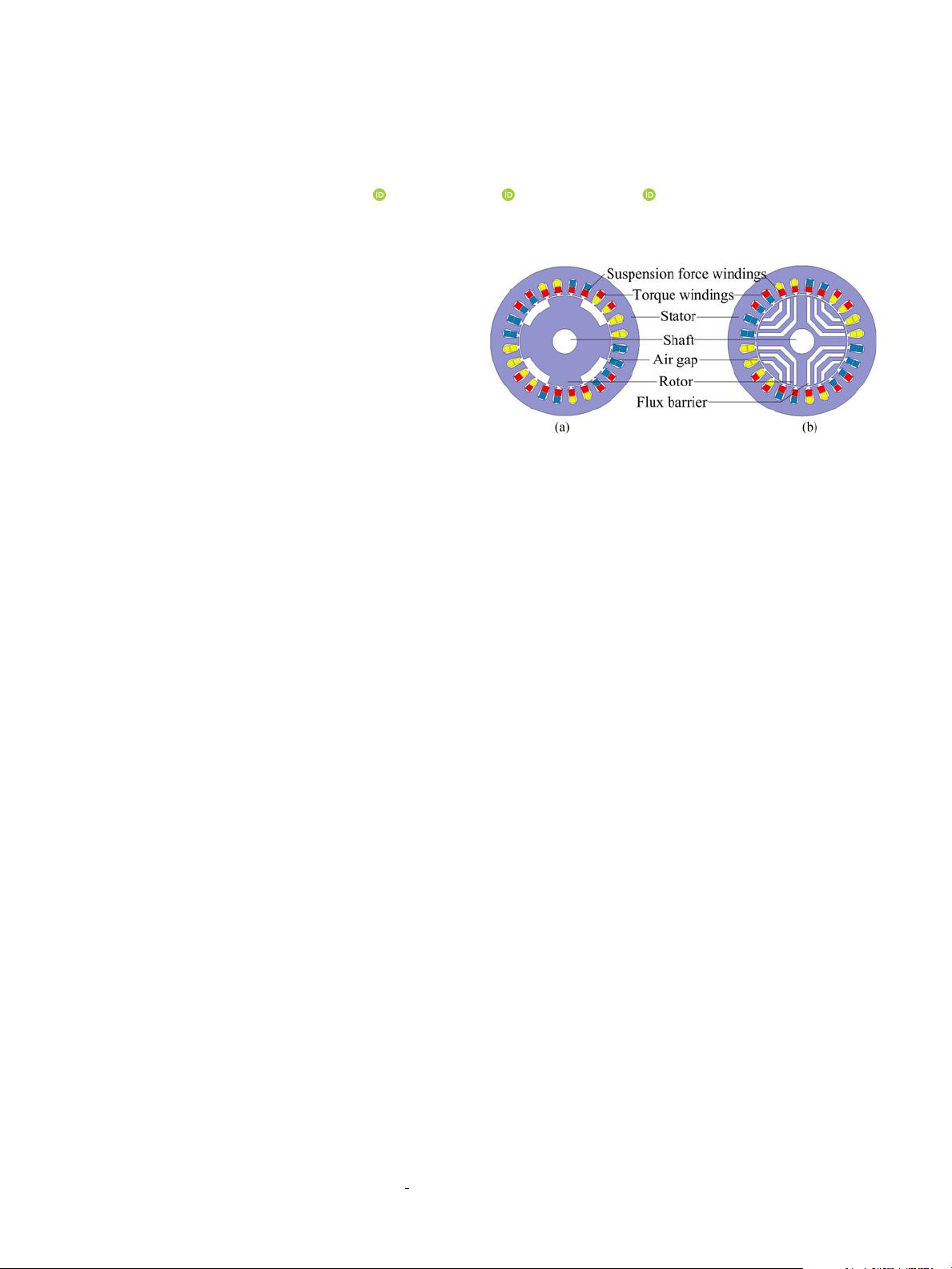
IEEE TRANSACTIONS ON APPLIED SUPERCONDUCTIVITY, VOL. 28, NO. 3, APRIL 2018 5202905
Optimization Design of Bearingless Synchronous
Reluctance Motor
Haifei Ding , Huangqiu Zhu , and Yizhou Hua
Abstract—In order to overcome common drawbacks of the low
torque density and power factor for conventional bearingless syn-
chronous reluctance motors (BSynRMs), a novel BSynRM rotor
structure with ferrite magnets is designed in this paper. First, the
basic structure and operation principle of the BSynRM are in-
troduced, and the mathematical models of torque and suspension
forces are deduced. Second, based on the finite element analysis
method, the parameters of flux barriers layer, rotor rib width, and
permanent magnets are optimized to increase the salient pole ratio
and the difference between d and q axes inductance. Third, the
performance of torque, suspension forces, and power factor for the
optimized motor is compared with that of the traditional BSynRM.
The research results show that the torque density and power fac-
tor increase about 54.4% and 56.3% respectively at optimal angle,
whereas the average suspension force decreases about 15.7% owing
to magnetic saturation. The optimized motor is validated to have
good suspension and speed regulation performance.
Index Terms—Bearingless synchronous reluctance motor
(BSynRM), optimization design, power factor, torque density.
I. INTRODUCTION
T
HE normal operation of a traditional motor cannot be sep-
arated from bearing support. But some problems, such as
friction and wear, mechanical vibration, and noise, may be pro-
duced by bearings during the operation of traditional motors. In
the middle and later period of twentieth century, the magnetic
bearings solved problems above effectively [1]. At the same
time, the magnetic bearings may also cause problems, such as
longer axial length, relatively complex structure and control, as
well as higher costs. So the motors supported by magnetic bear-
ings are difficult to realize high speed operation, which limits
their scope of application.
The bearingless synchronous reluctance motors (BSynRMs)
inherit the merits of magnetic bearings and synchronous reluc-
tance motors (SynRMs). According to the similarity in structure
between the magnetic bearings and SynRMs, the windings used
to produce the radial suspension force in magnetic bearings are
Manuscript received August 26, 2017; accepted January 7, 2018. Date of pub-
lication January 16, 2018; date of current version January 29, 2018. This work
was supported in part by the Key Research and Development Project of Jiangsu
Province (BE2016150), in part by the Priority Academic Program Development
of Jiangsu Higher Education Institutions (2014), and in part by the Gradu-
ate Student Practice Innovation Project of Jiangsu Province (SJLX16_0427).
(Corresponding author: Huangqiu Zhu.)
The authors are with the School of Electrical and Information Engineer-
ing, Jiangsu University, Zhenjiang 212013, China (e-mail: zhuhuangqiu@
ujs.edu.cn).
Color versions of one or more of the figures in this paper are available online
at http://ieeexplore.ieee.org.
Digital Object Identifier 10.1109/TASC.2018.2793192
Fig. 1. Cross sections of BSynRMs with different rotor. (a) Salient pole rotor.
(b) Flux barrier rotor.
superimposed in the stator windings of SynRMs. The BSyn-
RMs, thus, have the advantages of simpler structure, higher
critical speed, and smaller volume [2].
Common drawbacks of the conventional BSynRM with
salient pole rotor are the low torque density and power fac-
tor, which can be overcome by increasing the salient pole ratio
and the difference between d- and q-axis inductance. A new
BSynRM with multi-flux barriers rotor can produce torque and
suspension forces effectively, but the power factor is not sig-
nificantly improved [3]. In general SynRMs, rotor structures
with auxiliary permanent magnets have been reported to have
good torque and power factor characteristics [4], [5]. In this
paper, the structure and working principle of the BSynRM are
introduced, and the mathematical models of radial suspension
forces and torque are established. Then, the optimal design of
the BSynRM is carried out based on the simple variable method.
The effects of different rotor dimensions, including flux barriers
layer, rotor rib width and permanent magnets, are studied using
the finite element analysis method (FEM). The good suspension
and torque performance of the optimized motor can be gotten
by means of vector control strategy.
II. M
OTOR TOPOLOGY AND OPERATING PRINCIPLE
A. Topology of the BSynRM
The types of BSynRM rotor include salient pole rotor and
flux barriers rotor, as shown in Fig. 1. The power factor and
torque density of the BSynRM with the latter rotor have been
improved compared with the former. The stator windings of the
BSynRM are divided into outer torque windings and inner sus-
pension force windings. Fig. 2 shows that the rotor of BSynRM
is supported by a self-aligning ball bearing, which makes the
1051-8223 © 2018 IEEE. Personal use is permitted, but republication/redistribution requires IEEE permission.
See http://www.ieee.org/publications
standards/publications/rights/index.html for more information.