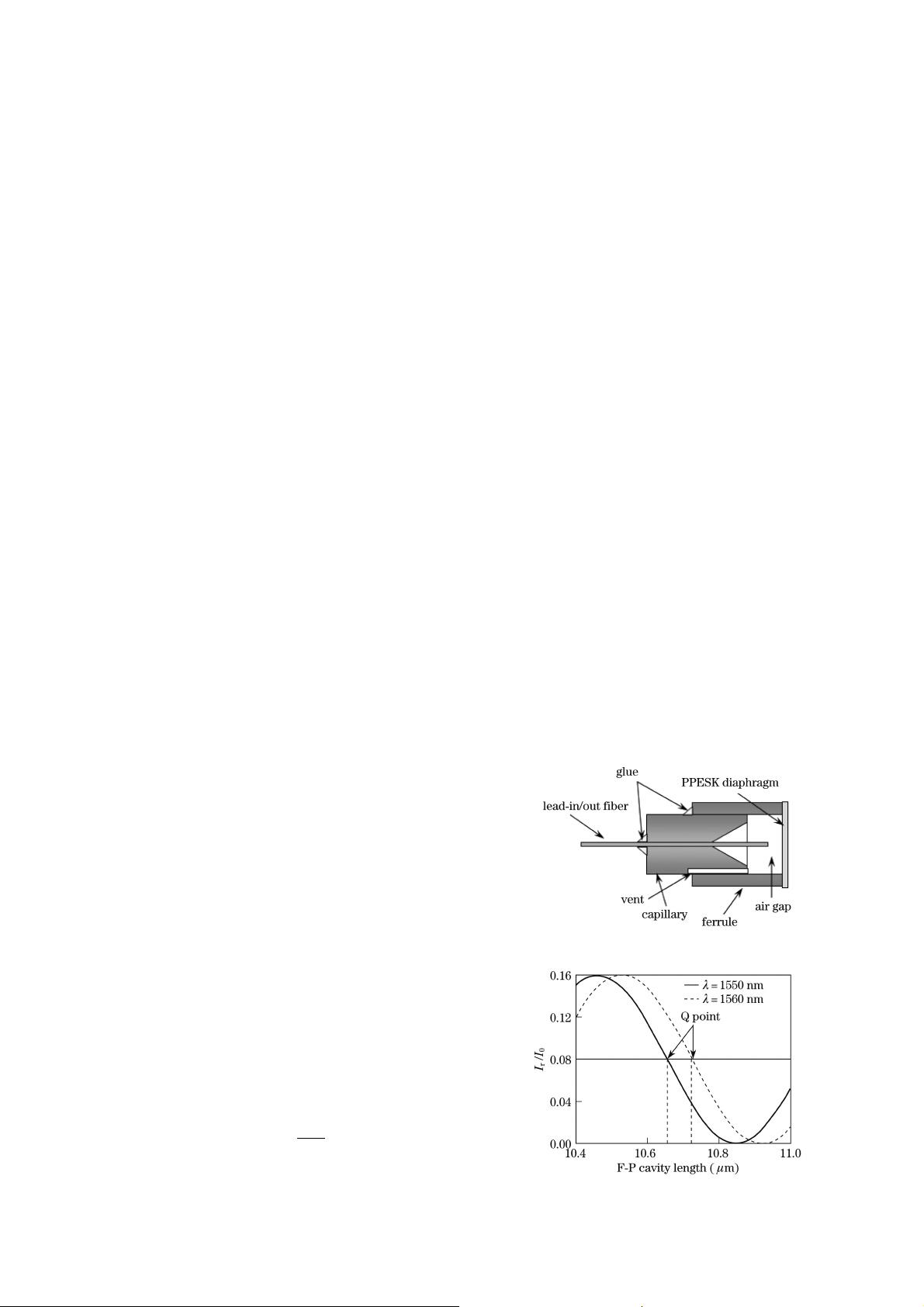
266 CHINESE OPTICS LETTERS / Vol. 8, No. 3 / March 10, 2010
Polymer diaphragm based sensitive fiber optic Fabry-Perot
acoustic sensor
Qiaoyun Wang (|||) and Qingxu Yu (uuuRRR)
∗
School of Physics and Optoelectronic Technology, Dalian University of Technology, Dalian 116023, China
∗
E-mail: yuqx@dlut.edu.cn
Received May 20, 2009
A sensitive polymer diaphragm based fiber Fabry-Perot (F-P) sensor for aeroacoustic wave measurement
is presented. A novel polymer material poly (phthalazinone ether sulfone ketone) (PPESK) diaphragm is
used as the acoustic sensing element. The effective dimensions of the diaphragm are 4 mm in diameter and
6 µm in thickness. Owing to the good mechanical and optical features of the diaphragm and application of
the interferometric/intensity demodulation, a system sensitivity of 31 mV/Pa is achieved in the frequency
range of 0.1–12.7 kHz, and a signal-to-noise ratio (SNR) of 29 dB at 1 kHz is obtained. The linear response
of the sensor is from 0.35 to 2.82 Pa, corresponding to 85 – 103 dB sound pressure level (SPL) (re: 20
µPa). The sensor has the potential to be used as a universal and low-cost optical microphone.
OCIS co des: 060.2370, 120.2230, 050.2230.
doi: 10.3788/COL20100803.0266.
Fiber optic acoustic sensors have been researched for
decades because of the advantages over conventional
acoustic sensors, such as electrically passive, immunity
from electromagnetic interference, resistance to corro-
sion, remote sensing operation
[1]
, light weight, and small
size. Diaphragm-based extrinsic Fabry-Perot interfero-
metric (EFPI) fiber optic sensor, as a branch of fiber
optic acoustic sensors, has become a hot topic in the
acoustic signal detection due to its high sensitivity and
wide frequency response. Various kinds of diaphragm-
based EFPI fib er optic sensors, such as a silica diaphragm
spliced with a silica capillary
[2−5]
, a glass or a silicon
diaphragm bonded to a silicon base
[6−8]
, and a dipped
polymer membrane on a hollow fiber tip
[9,10]
have been
developed, and some of these sensors are applied in the
detection of hydroacoustic waves and partial discharge in
power transformer
[8]
. But most of these sensors do not
suit aeroacoustic detection due to the mismatch of the
acoustic impedance with the sensors diaphragm.
In this letter, an ultra-sensitive diaphragm-based fiber
optic EFPI aeroacoustic sensor is proposed. A new poly-
mer diaphragm of poly (phthalazinone ether sulfone ke-
tone) (PPESK) is used as the sensing element. Theo-
retical analysis of the diaphragm structure and fabrica-
tion of the sensor are presented. The configuration of
the diaphragm-based fiber optic EFPI acoustic sensor is
shown in Fig. 1. A low-finesse Fabry-Perot (F-P) inter-
ferometer is formed between the end surface of optical
fiber and the inner surface of PPESK diaphragm. Light
propagates along the lead-in fiber, and then the partial
light is reflected by the fiber end face and the inner sur-
face of diaphragm. The reflection light which contains
the F-P interferometric signal travels back along the same
fiber. For a low-finesse F-P interferometer, the reflected
optical intensity can be expressed by
[11,12]
I
r
= 2RI
0
·
1 − cos(
4πL
λ
)
¸
, (1)
where I
0
is the incident optical intensity, R is the reflec-
tivity of the fib er end face and the inner surface of di-
aphragm whose refractive index is nearly the same as that
of the fiber core, λ is the wavelength of the light source,
and L is the length of F-P cavity. When the length of
F-P cavity changes one half of the light wavelength, the
reflected intensity will change a period. The relationship
between I
r
/I
0
and L with different wavelengths is shown
in Fig. 2. For an interferometric/intensity modulated
sensor, the initial static operating point of sensor should
be set at the quadrature point (shown in Fig. 2 as Q
points) of the sinusoidal curve.
When a pressure is applied to the diaphragm, the de-
formation of diaphragm will cause the changes of the
F-P cavity length and the reflected optical intensity. In
our experiment, only the diaphragm center deflection is
of interest. For a rigidly clamped round diaphragm, the
Fig. 1. Configuration of fiber acoustic sensor.
Fig. 2. Relationship between the cavity length and intensity
with different wavelengths.
1671-7694/2010/030266-04
c
° 2010 Chinese Optics Letters