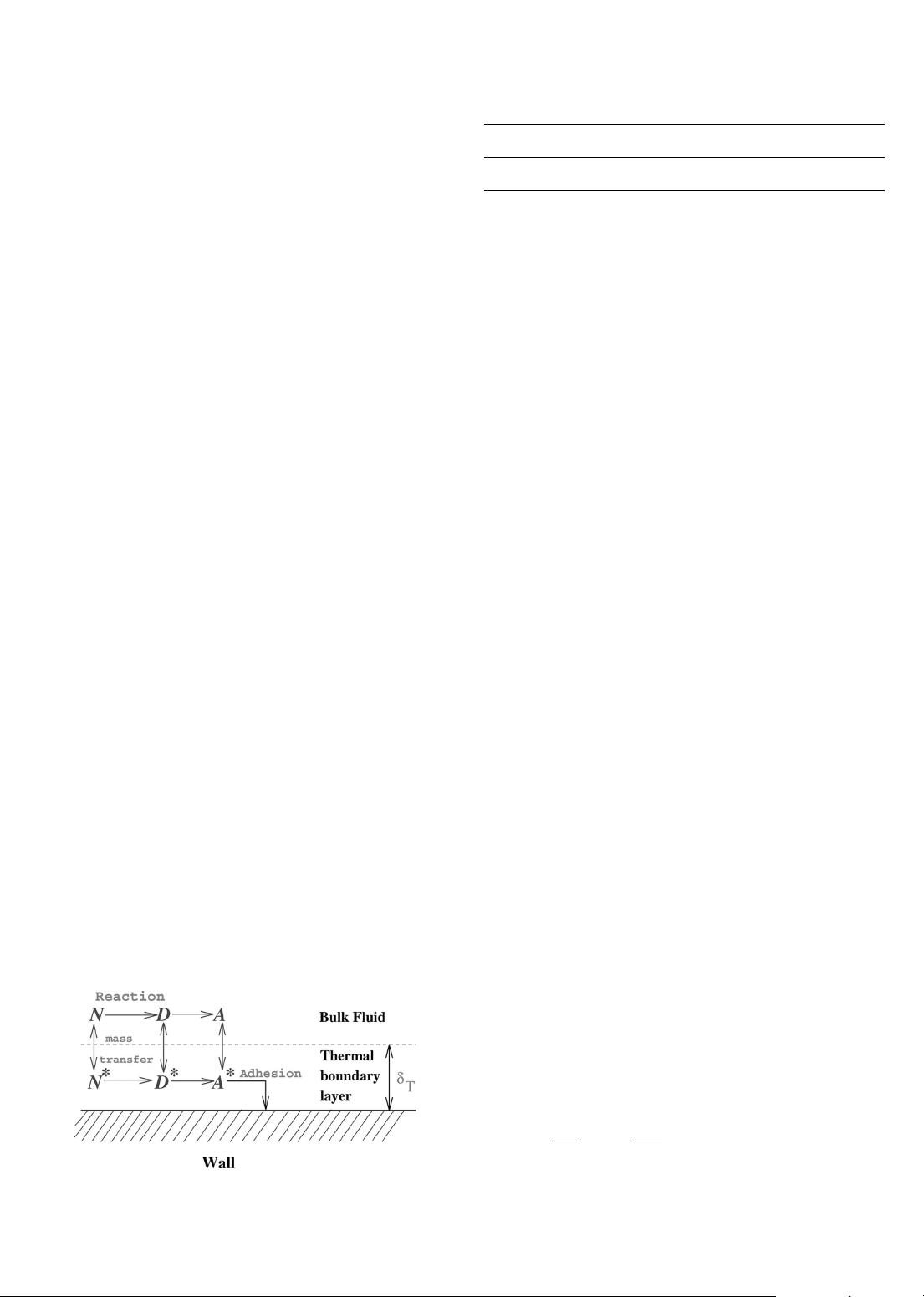
Fig. 1. The protein reaction scheme used in the fouling model.
Table 1
Kinetic data for the reactions of b}lactoglobulin
E
N
(kJ/mol) k
No
(1/s) E
D
(kJ/mol) k
Do
(m3/kg s)
261 312 3.37]1037 1.36]1043
primarily due to the existence of both counter current
and co-current #ows, the strong energy interactions
between #uids in adjacent channels, and the great variety
of complex geometries that can be found in industrial
applications.
With the increasing trend towards improved predictive
accuracy of process models in this work we present
fundamental dynamic models to perform a comprehens-
ive study of milk fouling in PHEs as a process a!ected by
momentum, heat- and mass-transfer phenomena. Such
models, under speci"ed assumptions, may have predic-
tive power over wide range of operating conditions and
with the recent developments in modelling tools can be
used for on-line applications. Moreover, accurate predic-
tion of fouling dynamics for a given system would pave
the way for obtaining optimal operating policies and
design characteristics of industrial heat exchangers
(Fryer, 1989; De Jong, 1996).
2. Description of fouling model
The fouling model used in this work relies on the
b-lactoglobulin reaction scheme as shown in Fig. 1. It
was adopted from Toyoda and Fryer (1997) and was "rst
proposed by De Jong et al. (1992). When milk is heated
above 653C, b-lactoglobulin becomes thermally unstable
and it (i) unfolds in molecular denaturation exposing
reactive sulphydry (-SH) groups and (ii) polymerizes irre-
versibly to give insoluble particles in aggregation (De
Jong et al., 1992). The key step in studying fouling is to
capture the interrelationship between the chemical reac-
tions which give rise to deposition and the #uid mechan-
ics associated with the heat transfer equipment. The
reaction scheme is described as follows:
f Proteins react in both the bulk and the thermal bound-
ary layer in the milk. Native protein N is transformed
to denaturated protein D, in a "rst-order reaction. The
denaturated protein then reacts to give aggregated
protein A in a second order reaction.
f Mass transfer between the bulk and the thermal
boundary layer takes place for each protein.
f Only the aggregated protein is deposited on the wall.
The deposition rate is proportional to the concentra-
tion of aggregated protein in the thermal boundary
layer.
f The fouling resistance to heat transfer is proportional
to the thickness of the deposit.
The reaction rate constants are expressed in the com-
mon form as:
k"k
0
exp(!E/R¹)
The pre-exponential factors k
o
and the activation ener-
gies, E, for the two reactions are taken from De Jong et al.
(1992) and given in Table 1.
3. A thermal dynamic model of PHEs
A plate heat exchanger consists of a number of parallel
#ow channels formed by metal plates which are separ-
ated by gasket material around the perimeter of each
plate (see Fig. 2). Nozzles for the #ow of #uids extend
through the frames to the plate packages. Heat is trans-
ferred through these plates from one #uid to another.
For the purpose of modelling, consider a di!erential
element of the PHE in channel j (Fig. 3). The modelling
assumptions are de"ned as follows:
f No di!usion of heat is considered in the axial direc-
tion.
f The #owrate and temperature pro"les are uniform
across the channel and plate width.
f Each #uid is split equally between all related channels.
f Heat losses to the environment are negligible.
f The head and follower parts of the PHE are assumed
to be insulated and serve as adiabatic plates.
Based on the fundamental energy conservation law the
following equations describe the heat transfer between
process #uid or heating medium in a channel j and its
adjacent plates p
j
and p
j`1
:
A
x
p
j
Cp
j
A
L¹
j
Lt
#n
j
u
x
L¹
j
Lx
B
";
j
A
j
(¹
p
j~1
!¹
j
)#;
j
A
j
(¹
pj
!¹
j
). (1)
M.C. Georgiadis, S. Macchietto / Chemical Engineering Science 55 (2000) 1605}1619 1607