APQP与FMEA:企业产品质量策划的关键工具详解
需积分: 23 29 浏览量
更新于2024-08-21
收藏 926KB PPT 举报
过程FMEA(Process Failure Mode and Effects Analysis)是一种用于识别、评估和控制制造过程中的潜在失效模式及其影响的重要质量策划工具,尤其在企业产品先期策划(APQP)框架下发挥着核心作用。APQP是ISO/TS16949、QS9000、EAQF94等国际质量管理体系标准中明确推荐的方法,旨在确保产品的早期质量规划和设计。
APQP分为五个阶段:第一阶段是计划和产品设计,包括确定项目和开发策略;第二阶段是过程设计与开发,涉及产品与过程确认;第三阶段是反馈、评定和纠正措施的策划;第四阶段是样件制作、试生产和批量生产的准备,如PPAP(生产件批准程序)、MSA(测量系统分析)和FMEA(用于过程和产品);最后阶段是SPC(统计过程控制)的实施,确保过程的稳定性和一致性。
在APQP中,FMEA是关键环节之一,特别关注产品设计文件、过程设计文件、控制计划、作业指导书以及防错措施。FMEA分析通常采用ISO/TS16949的技术工具,例如Potential Failure Mode and Effects Analysis(PFMEA),它的主要内容包括:
1. 基础过程开发改进模式:提供一种结构化的方法来识别和改进现有或新引入的过程。
2. 过程失效模式和影响分析(P-FMEA):对特定过程进行详细的分析,识别可能的失效模式(如设备故障、操作失误等)、它们可能产生的影响的严重程度,以及采取的预防和减轻措施。
3. P-FMEA输出:包括表格形式的报告,包含表头信息(如编号、描述等)、失效模式标识、潜在影响及严重度评估等。
4. P-FMEA建立过程:确保所有步骤得到系统的记录和跟踪,以提高分析的准确性和可追溯性。
5. 表格结构:从表头信息到详细列出的潜在失效模式、影响程度、严重度评级以及建议的预防和减轻措施。
APQP与防错策略紧密相连,旨在通过预防措施减少产品在交付给客户时出现问题的可能性。在关键环节,如产品设计、过程设计和控制计划制定时,防错原则被深入贯彻,以提升产品质量和流程效率。
过程FMEA是企业产品先期策划中不可或缺的一部分,它帮助组织提前发现并管理潜在风险,从而确保产品满足高质量标准,并有效降低质量问题发生的概率。通过遵循APQP的阶段性和系统化方法,企业能够建立一个全面的质量管理体系,提高产品和服务的整体性能和可靠性。
2021-11-10 上传
2021-10-11 上传
2021-11-25 上传
点击了解资源详情
2021-10-14 上传
2024-07-14 上传
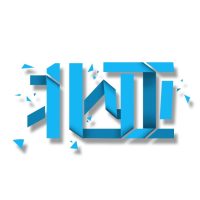
西住流军神
- 粉丝: 31
- 资源: 2万+
最新资源
- 黑板风格计算机毕业答辩PPT模板下载
- CodeSandbox实现ListView快速创建指南
- Node.js脚本实现WXR文件到Postgres数据库帖子导入
- 清新简约创意三角毕业论文答辩PPT模板
- DISCORD-JS-CRUD:提升 Discord 机器人开发体验
- Node.js v4.3.2版本Linux ARM64平台运行时环境发布
- SQLight:C++11编写的轻量级MySQL客户端
- 计算机专业毕业论文答辩PPT模板
- Wireshark网络抓包工具的使用与数据包解析
- Wild Match Map: JavaScript中实现通配符映射与事件绑定
- 毕业答辩利器:蝶恋花毕业设计PPT模板
- Node.js深度解析:高性能Web服务器与实时应用构建
- 掌握深度图技术:游戏开发中的绚丽应用案例
- Dart语言的HTTP扩展包功能详解
- MoonMaker: 投资组合加固神器,助力$GME投资者登月
- 计算机毕业设计答辩PPT模板下载