压铸模具设计:非成型零件材料与热处理关键
需积分: 50 195 浏览量
更新于2024-08-24
收藏 7.39MB PPT 举报
"非成型零件材料选择及热处理要求-压铸模具设计与制造"
在压铸模具设计与制造中,非成型零件的选择和热处理是至关重要的环节,它们直接影响到模具的性能和寿命。非成型零件主要分为三类:滑动配合零件、支承和结构零件以及受力零件。
对于滑动配合零件,如推杆和推管,其主要任务是确保模具动作的顺畅。因此,材料必须具备良好的耐磨性和适当的强度。同时,由于这些零件经常需要进行热处理,所以还要求材料具有良好的淬透性,以保证热处理后的硬度均匀,同时减少因热处理导致的形变。
支承和结构零件,如动、定模套板和支承板,它们主要承担支撑和连接的作用,所以材料必须具备足够的强度和刚度,以承受压铸过程中的机械应力。通常选用45号钢或Q235-A等材料,并进行调质处理,以达到28~32HRC的硬度,保证零件的稳定性。
受力零件,如复位杆、导柱、导套、斜销、楔紧块和滑块导滑槽镶件等,它们在模具工作时承受较大的负荷。这类零件通常选用T10A或T8A等工具钢,经过热处理后达到50~55HRC的硬度,以增强其抗磨损和抗冲击的能力。
压铸成型技术是现代工业中一种高效的金属成型方法,其特点是高压高速填充,适用于锌、铝、镁、铜等轻金属合金,甚至扩展到铸铁和铸钢等重质材料。随着技术的发展,压铸正向着智能化、新材料研发、自动化设备提升、新型检测技术和工艺改进等方向迈进。压铸模具的设计不仅涉及浇注系统、模具形状、表面质量和脱模性能,还涉及到模具的强度、刚度、热交换控制等多个方面,是整个压铸生产流程中的核心环节。
压铸模设计的基础在于理解压铸工艺,包括确定合适的内浇口和排溢系统,保证熔融金属的填充效果;模具的精度直接影响压铸件的质量;模具的热管理则关系到压铸件的尺寸稳定性和模具寿命。因此,压铸模具设计者需要综合考虑材料、热处理、工艺参数等多个因素,以实现高质量的压铸生产。
2021-10-06 上传
2021-09-17 上传
2010-05-18 上传
2021-10-04 上传
点击了解资源详情
点击了解资源详情
点击了解资源详情
点击了解资源详情
2021-10-06 上传
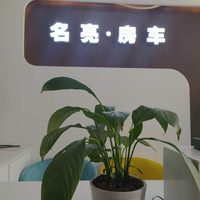
清风杏田家居
- 粉丝: 21
- 资源: 2万+
最新资源
- Angular程序高效加载与展示海量Excel数据技巧
- Argos客户端开发流程及Vue配置指南
- 基于源码的PHP Webshell审查工具介绍
- Mina任务部署Rpush教程与实践指南
- 密歇根大学主题新标签页壁纸与多功能扩展
- Golang编程入门:基础代码学习教程
- Aplysia吸引子分析MATLAB代码套件解读
- 程序性竞争问题解决实践指南
- lyra: Rust语言实现的特征提取POC功能
- Chrome扩展:NBA全明星新标签壁纸
- 探索通用Lisp用户空间文件系统clufs_0.7
- dheap: Haxe实现的高效D-ary堆算法
- 利用BladeRF实现简易VNA频率响应分析工具
- 深度解析Amazon SQS在C#中的应用实践
- 正义联盟计划管理系统:udemy-heroes-demo-09
- JavaScript语法jsonpointer替代实现介绍