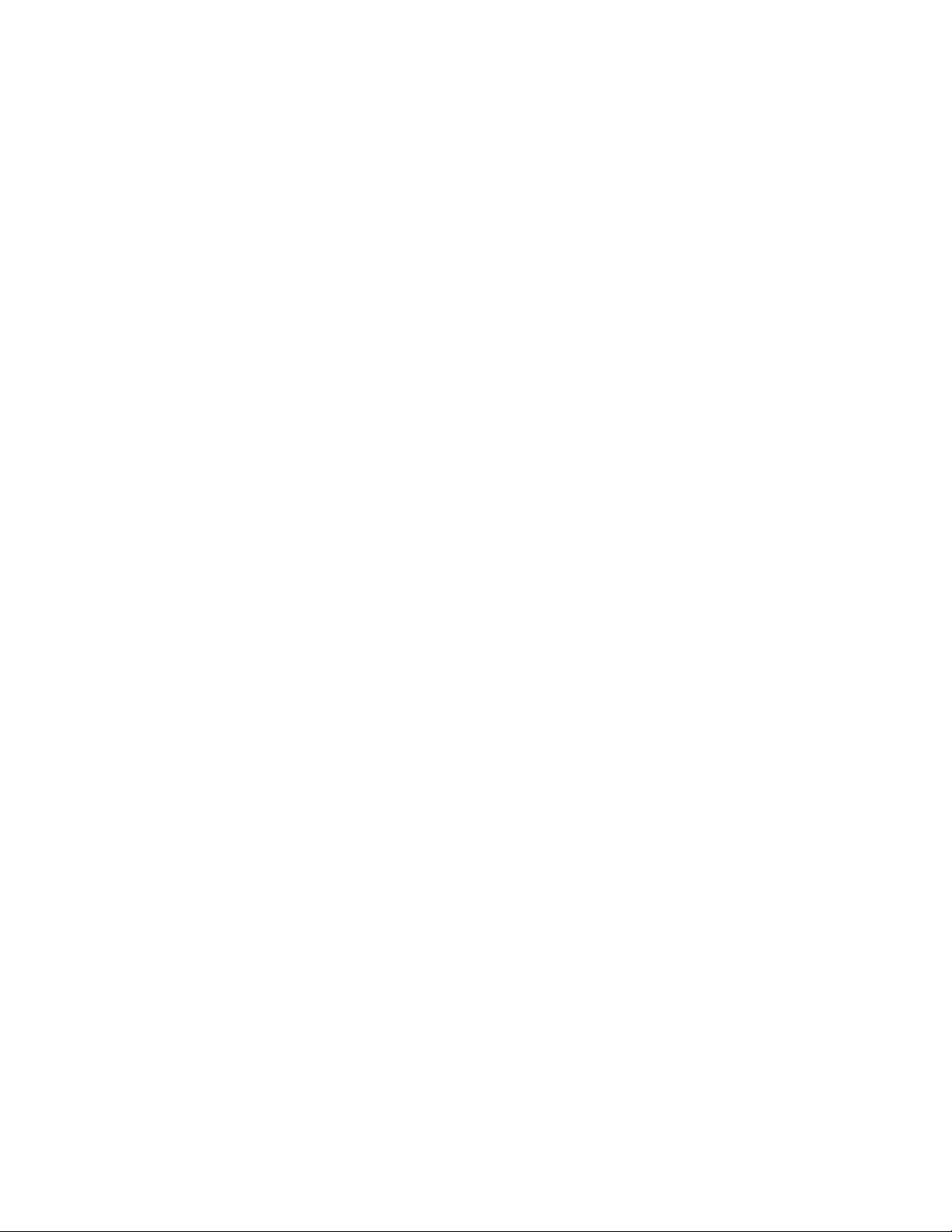
Chapter 1—Roadmap for Robotics in Manufacturing 11
acceptance of working with them in their professional life and will be less likely to view robots as a
threat. For example, two-thirds of the owners of iRobot’s autonomous vacuum cleaner have named their
Roomba, and one-third admit to taking their Roomba to visit friends.
2.4 A Vision for Manufacturing
U.S. manufacturing today is where database tech-
nology was in the early 1960s, a patchwork of ad
hoc solutions that lacked the rigorous methodology
that leads to scientific innovation. In 1970, Ted
Codd, an IBM mathematician, invented relational
algebra, an elegant mathematical database model
that galvanized federally funded research and edu-
cation leading to today’s $14 billion database indus-
try. Manufacturing would benefit enormously if
analogous models could be developed. Just as the
method to add two numbers together doesn’t de-
pend on what kind of pencil you use, manufactur-
ing abstractions might be wholly independent of the product one is making or the assembly line systems
used to assemble it.
Another precedent is the Turing Machine, an elegant abstract model invented by Alan Turing in the 1930s,
which established the mathematical and scientific foundations for our now-successful high-tech indus-
tries. An analogy to the Turing Machine for design, automation, and manufacturing could produce
tremendous payoffs. Recent developments in computing and information science now make it possible
to model and reason about physical manufacturing processes, setting the stage for researchers to “put the
Turing into ManufacTuring.” The result, as with databases and computers, would be higher quality, more
reliable products, reduced costs, and faster delivery [GK07, PCMR-11, FAM-11].
More effective use of robotics, through improved robotics technologies and a well-trained workforce, will
increase U.S. jobs and global competitiveness. Traditional assembly-line workers are nearing retirement
age. American workers are currently not well trained to work with robotic technologies and the costs of
insurance and healthcare continue to rise. Even when workers are affordable, the next generation of
miniaturized, complex products with short life cycles requires assembly adaptability, precision, and relia-
bility beyond the skills of human workers. Widespread deployment of improved robotics and automation
in manufacturing will: (a) retain intellectual property and wealth that would go off-shore without it, (b)
save companies by making them more competitive, (c) provide jobs for maintaining and training robots,
(d) allow factories to employ human-robot teams that safely leverage each others’ strengths (e.g., humans
are better at dealing with unexpected events to keep production lines running, while robots have better
precision and repeatability, and can lift heavy parts), (e) reduce expensive medical problems (e.g., carpal
tunnel syndrome, back injuries, burns, and inhalation of noxious gases and vapors), and (f) reduce time
in the pipeline for finished goods, allowing systems to be more responsive to changes in retail demand.
Investments in research and education in manufacturing can revitalize American manufacturing. Invest-
ing a small portion of our national resources into a science of cost-effective, resource-efficient manufac-
turing would benefit American consumers and would support millions of workers in this vital sector of
the U.S. economy. Such investments would benefit healthcare, agriculture, and transportation, and
would strengthen our national resources in defense, energy, and security. The resulting flurry of research
activity would invigorate the quality and productivity of “Made in the U.S.A.” for the next fifty years.
Image courtesy of Mixabest via Wikimedia Commons