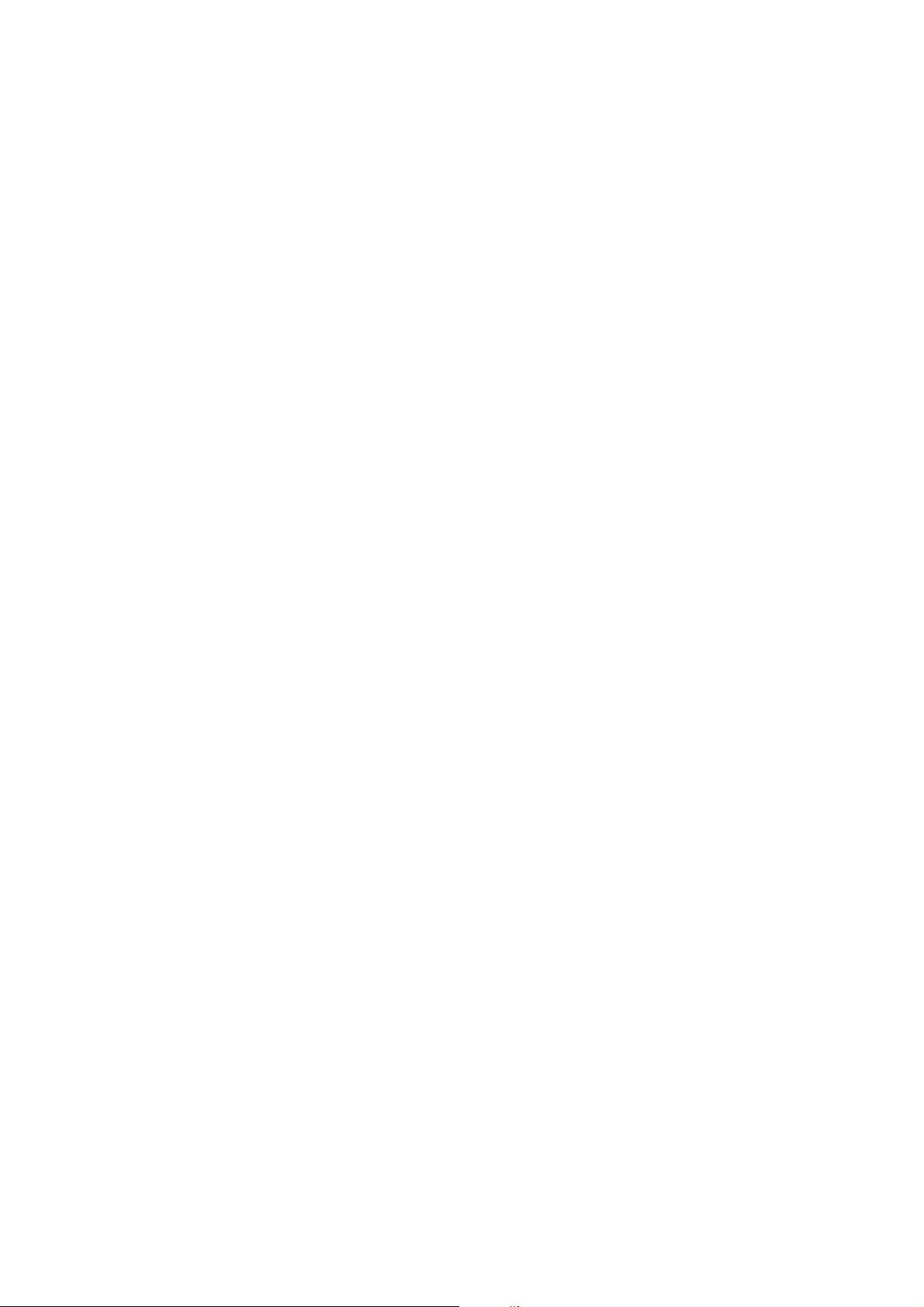
Simulation on Aircraft Generator Control System Using Genetic
Algorithms
xuejun ZHANG
1,*
, si SHEN
2
, guanhui YAN
1
,yonglu CHEN
3
1
(School of Electronic and Information Engineering, Lanzhou Jiao Tong University, Lanzhou Gansu 730070, China)
2
(School of Information Management, NanJing University, Nanjin Jiangsu 210093, China)
3
(China Flight Test Establishment, Xiƍan Shaanxi 710089, China)
Keywords: Genetic Algorithms; Simulation; Variable Speed
Constant Frequency; Brushless Doubly-Fed Generator;
Optimization.
Abstract
In this paper, a comprehensive model of cascade
brushless doubly-fed aeroplane generator is developed on the
analysis of aeroplane generator’s structure and the principle
of variable speed constant frequency electricity generating.
Furthermore, a simulation model of brushless direct current
machine derived from this model is established in
SIMULINK development environment to verify the validity
of the model. In order to overcome the defects of hypo-best PI
parameters by conventional method of trial and error, the real-
coded genetic algorithms is adopted to optimize the
parameters of rotate speed in which the fitness function is
considered sufficiently for capturing systemic error and
controlled output. The simulation results show that the best PI
parameters can be quickly educed by adopting stator field
orientation vector control theory and genetic algorithm. It is
guaranteed that the power system output remains constant
frequency and constant voltage of three phase ac under the
circumstances of speed changing. However, the control
strategy is considered as valid and effective.
1 Introduction
It is well known that variable speed constant frequency
system is a better solution for aircraft power generation than
constant speed and constant frequency system due to its
higher efficiency. Brushless doubly-fed machine is a new
type of variable speed constant frequency system emerged in
recent years [1]. Because of no brush and slip ring, it has a
firm and credible structure and seems more suitable for
aircraft generation system [2].The study of applying brushless
doubly-fed machine to aircraft power generator system has
been the focus of interest of many recent studies. However, to
the authors’ knowledge, little literature is available on the
brushless doubly-fed machine applied to aircraft power
generation system.
In the aircraft electrical system, airborne alternating
current electrical equipments mostly require 400Hz and 115V
ac supplies for their operation. However, the electrical power
directly from airborne generator is variable frequency ac, due
to changing for rotational speed in driving aero-engine.
Traditionally, there are two methods to get constant frequency
ac power: 1) using constant speed driver that converts the
variable speed of aero-engine into constant speed; and 2)
using electronic inverter that converts variable frequency
power from generator to constant frequency ac power [3,4].
But these methods suffer from high cost, complex technology
and inconvenient to carry etc.
With the goals of overcoming these shortcomings, we
design a variable speed constant frequency alternating current
aircraft power generator system with brushless doubly-fed
machine in this paper. In addition, a dual closed-loop control
system model is established for this generator system which
implements the method of trial and error to get PI parameters.
Further, we adopt the real-coded genetic algorithm (GA) to
optimize the parameters of rotate speed, which employ
selecting operator, crossover operator and mutation operators
to get optimal PI parameters. Then we run simulation on the
aircraft power generator system. The results show that
variable speed constant frequency alternating current aircraft
power generator system can ensure constant frequency and
constant voltage of three-phase ac output in the case of
rotational speed changing, and obtain the best PI parameters
quickly by using the stator flux-linkage orientation vector
controlling strategy and the genetic algorithm.
2 Mathematic Model for Aeroplane Generator
The brushless doubly-fed aircraft electricity generator is
composed with two coaxial wound-rotor asynchronous
induction motors, which is called as “power motor” and
“control motor”, respectively. The two rotors are connected
on one axle, and the windings of two rotors are directly joined
together with electrically. The stator winding of the power
machine is named power winding, which is directly
connected on inverse three-phase power; while the stator
winding of the control machine is named as control winding,
which is connected on transducer. This structure, no slip rings
and brushes, can improve reliability of the aircraft power
generator system and reduce the capacity of transducer.
Therefore, it is suitable for aircraft power generator system
[5].
The basic construction of brushless doubly-fed aircraft
power generator is a cascade-connection system composed of
two ac exciter. Figure 1 illustrates the direction and size of
rotating magnetic generated by each winding through
symmetrical three-phase ac power and direction of rotating
shaft. Suppose that the direction of rotating magnetic
generated by the stator winding and rotor winding of power
1858