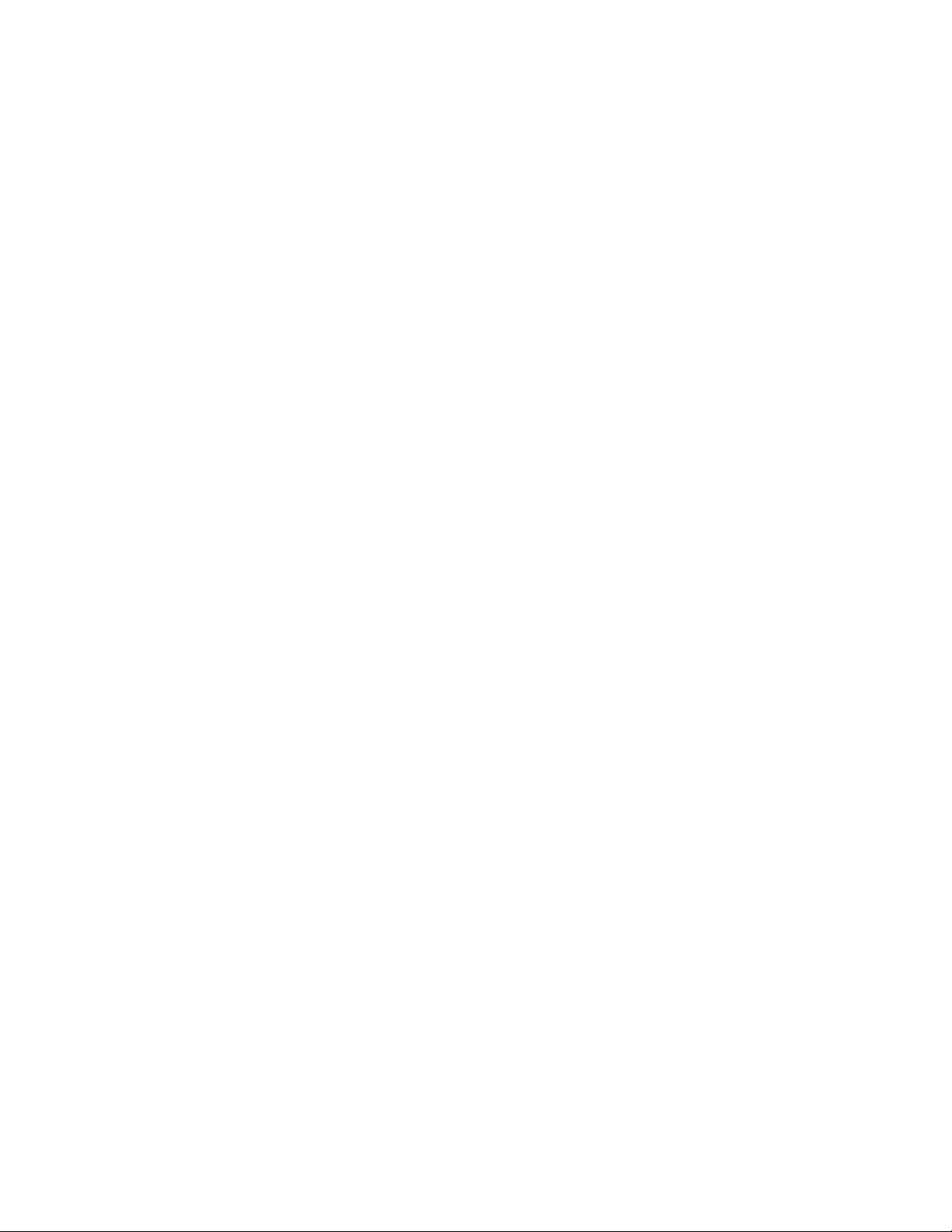
1
2000-01-0329
Experimental Study of CI Natural-Gas/DME
Homogeneous Charge Engine
Zhili Chen and Mitsuru Konno
Ibaraki Univ.
Mitsuharu Oguma and Tadanori Yanai
Graduate School, Ibaraki Univ.
Copyright © 2000 Society of Automotive Engineers, Inc.
ABSTRACT
In this study, a homogeneous mixture of natural-gas and
air was used in a compression ignition engine to reduce
NOx emissions and improve thermal efficiency. In order
to control ignition timing and combustion, a small amount
of DME was mixed with the natural-gas. Engine perfor-
mance and the exhaust characteristics were investigated
experimentally. Results show the following: the engine
can run over quite a large load range if a certain amount
of DME is added into natural-gas. By optimizing the pro-
portion of DME to natural-gas, NOx emissions can be
lowered to near zero levels if the mixture is lean enough.
Thermal efficiency is higher than that obtained with nor-
mal diesel fuel operation.
INTRODUCTION
Recent research into reducing NOx emission effectively
and increasing thermal efficiency in diesel engines has
shown that the new homogeneous charge compression
ignition combustion (HCCIC) is a promising way to
accomplish these tasks. However, certain problems in its
application need to be resolved
(1-4)
. The rest of this sec-
tion will discuss some of the problems reported by differ-
ent researchers in this field.
Conventional diesel fuel is not suitable for HCCIC
because of problems arising from inherent physical and
chemical characteristics of diesel fuel. For example: in
order to achieve a homogeneous diesel/air mixture, early
injection timings are required, because the vaporization
of diesel fuel is poor. However, if the temperature in a cyl-
inder becomes higher than the self-ignition temperature
of the charge during the compression stroke, self-ignition
will occur before TDC. Since ignition timing has to be
controlled around TDC, the amount of homogeneous fuel
has to be restricted to less than a certain level
(2)
.
Early fuel injection tends to splash the spray at the wall of
the cylinder. This bars the formation of the homogeneous
mixture, thus, emissions of THC, CO, and PM (more than
twice) will be increased and the engine thermal efficiency
will be decreased
(3)
. To resolve these problems, Hisashi
Akagawa et al
(4)
. employed a pintle type injection nozzle
and a reduced top-land-crevice piston to increase the
homogeneity and control THC and CO emissions. Intro-
ducing a large amount of EGR is also a good way to
delay ignition timing.
On the other hand, natural-gas is a better alternative than
diesel fuel as it easily forms a uniform mixture for HCCIC.
The recoverable reserves of natural-gas are almost the
same as that of crude oil based on energy content)
(5)
.
Therefore it would be wiser to use the gaseous fuel rather
than any synthetic liquid fuel converted from natural-gas
because the price of the latter would likely be higher
(6)
.
The application of natural-gas to an internal-combustion
engine should be by way of compression ignition if high
thermal efficiency and low NOx emission are expected.
However, the self-ignition temperature of natural-gas is
much higher than that of the conventional diesel fuel.
Therefore, even if natural-gas is introduced into an exis-
tent diesel engine, compression self-ignition will not
occur
(7)
. Therefore, in order to operate the compression
ignition engine with natural-gas, a method of raising the
compression temperature must be considered. Yasuharu
Kawabata et al. used a two-stage heater with an external
supercharging unit to raise the intake air temperature by
180 °C. However, since the ignition timing cannot be
effectively controlled by this method, the excess air ratio
range was restricted within narrow limits from 4.2 to 3.22
(8)
.
Another idea made by Seiichi Shiga et al
(9)
. for natural-
gas compression ignition in two-stroke engines (com-
pression ratios were set to 13.5 or 14.5) was to shut
down the exhaust throttle valves to as small as 10% of
the maximum. This was done to maintain a considerable
amount of burnt gas (from a previous cycle) in the cylin-
der, in order to keep a high compression temperature.
However, the engine operating conditions were restricted
Downloaded from SAE International by Jilin University, Wednesday, October 22, 2014