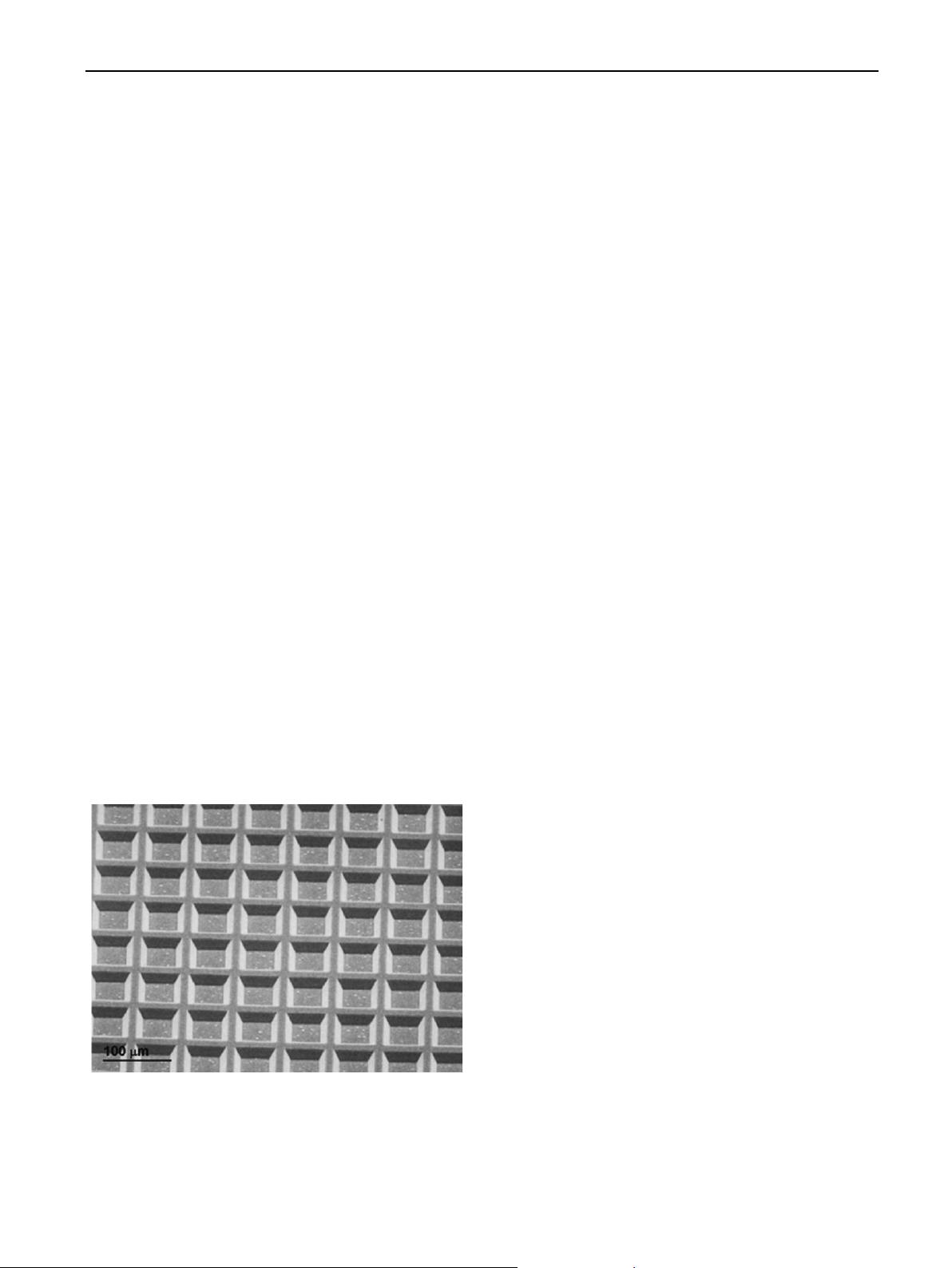
deposition and patterning of a silicon nitride or a silicon
dioxide layer as a mask, then (100)-oriented silicon wafers
are etched in KOH aqueous solution, obtaining pits with
triangular or trapezoidal cross-section, and with depth
depending on the mask-opening dimension (Fig. 7). The
so-micro machined silicon back plate is coated by a metallic
layer and, subsequently, a polymer film with a thickness
ranging from 2e13 mm, metalized on one side, is stretched
over it and kept in tension by a metallic frame. Thanks to
the small dimension of the micro membranes, suspended
by the rails, the working frequency of these transducers
can reach 1 or 2 MHz in air [17,19]. The membrane is forced
to stay in contact with the rails due to the electrostatic
pressure caused by the polarization voltage, and this
constraint prevents down displacement of the membrane
towards the substrate. But, as soon as the frequency
increases, upward displacements are allowed. Due to this
degree of freedom, and to the mutual mechanical coupling
of the micro-membranes, regions in phase and out of phase
appear on the surface of the membrane, destroying the
coherence of the acoustic radiation [17], and limiting the
range of frequency these transducers can operate.
Surface-micromachined capacitive ultrasonic
transducers
Wafer bonding, considered as a bulk process, is widely used
in micromachining, and older than surface micromachining
techniques. There are three basic wafer-bonding tech-
niques: anodic bonding, fusion bonding, and adhesive
bonding. Among these techniques, silicon fusion bonding
has earned a stable position in today’s technology, and is
now used for various applications: bond-and-etch back
silicon-on-insulator (SOI) wafers, SMART-CUT SOI wafers,
power devices, and many silicon microstructures, such as
pressure sensors and accelerometers. Silicon fusion bonding
is a direct bond between two silicon surfaces. It takes
place at high temperatures, forming strong covalent bonds
between the silicon wafers.
Most of these techniques are based on surface micro-
machining techniques [2,20], others are modified BiCMOS
processes [21], and others combine bulk and surface
micromachining for the realization of the membranes and
of the back plate [22].
In a surface-micromachining process, the micromechanical
structures are fabricated by deposition on the silicon wafer
of thin structural layers over thin sacrificial layers that can
be selectively removed. Thin film deposition techniques,
able to control the film’s mechanical properties, such as
internal stress or stress gradients, and dry and wet etchings
that remove sacrificial layers without damaging the struc-
tural ones, are essential for surface micromachining as
discussed below in this section.
The micromachining processes developed for the fabri-
cation of cMUTs can be classified according to the maximum
temperature used, which limits the degree of compatibility
with IC processing and hence the possibility of integration
of transducers and electronics on the same wafer.
The first process for the fabrication of cMUTs, based on
surface micromachining techniques, was developed at
Stanford University in Palo Alto, CA, USA [2]. The trans-
ducer is fabricated on a highly doped silicon wafer that
acts as the fixed electrode. The membrane’s structural
material is silicon nitride deposited by LPCVD over a sacri-
ficial layer of thermal oxide. Both the silicon nitride layer
and the backside of the silicon wafer are coated with
evaporated gold. Then a pattern of 3-mm diameter holes
on a bidimensional grid with 100-mm period is transferred
by lithography and etching through the gold and the
silicon nitride layer to reach the sacrificial oxide. Then
the membranes are released by wet etching of oxide in
pure hydrofluoridric acid. The membranes’ diameter is
controlled by timed etch. The major manufacturing issue of
this process consists in the membranes’ release. The risk of
fracture of the thin membranes and their sticking to the
substrate can be avoided by properly choosing layer thick-
nesses, thin films’ stresses, and membranes’ dimensions.
During drying after the sacrificial etching, capillary forces,
proportional to the membrane area, which can be balanced
by internal stress in the membrane, attract the membrane
toward the substrate [23]. A thin membrane separated
by a narrow gap from the back plate is the basic feature of
the cMUT, but a membrane that is too thin easily collapses
onto the substrate, and a thin gap limits the membrane’s
displacement during operation. A large value of the internal
stress in silicon nitride film increases the resistance to
collapse, but it can cause the membrane to break, resulting
in yield loss; furthermore, it affects the resonance vibra-
tion frequency of the membrane in air. As a consequence,
the cMUT presented by Haller and Khuri-Yakub [2] had
a 0.75-mm thick membrane suspended on a 1-mm thick gap.
The silicon nitride layer was deposited by LPCVD using
a mixture of ammonia and dichlorosilane at 800
C in order
to tune the residual stress of the membrane at a value of
280 MPa.
Another issue of the process is the timed etch of the
sacrificial layer. The etching rate decreases with time as
the etchant and the etch products must diffuse longer
through the small holes in the structural layer. The
membrane’s diameter depends on the etching duration and
only circular membranes can be obtained, as the etch
Fig. 7 Scanning Electron Microscopy (SEM) of a portion of
a CMUT silicon back plate fabricated by anisotropic etching of
silicon in KOH aqueous solution [68]. cMUT Z capacitive
micromachined ultrasonic transducer; KOH Z potassium
hydroxide.
12 M.S. Salim et al.