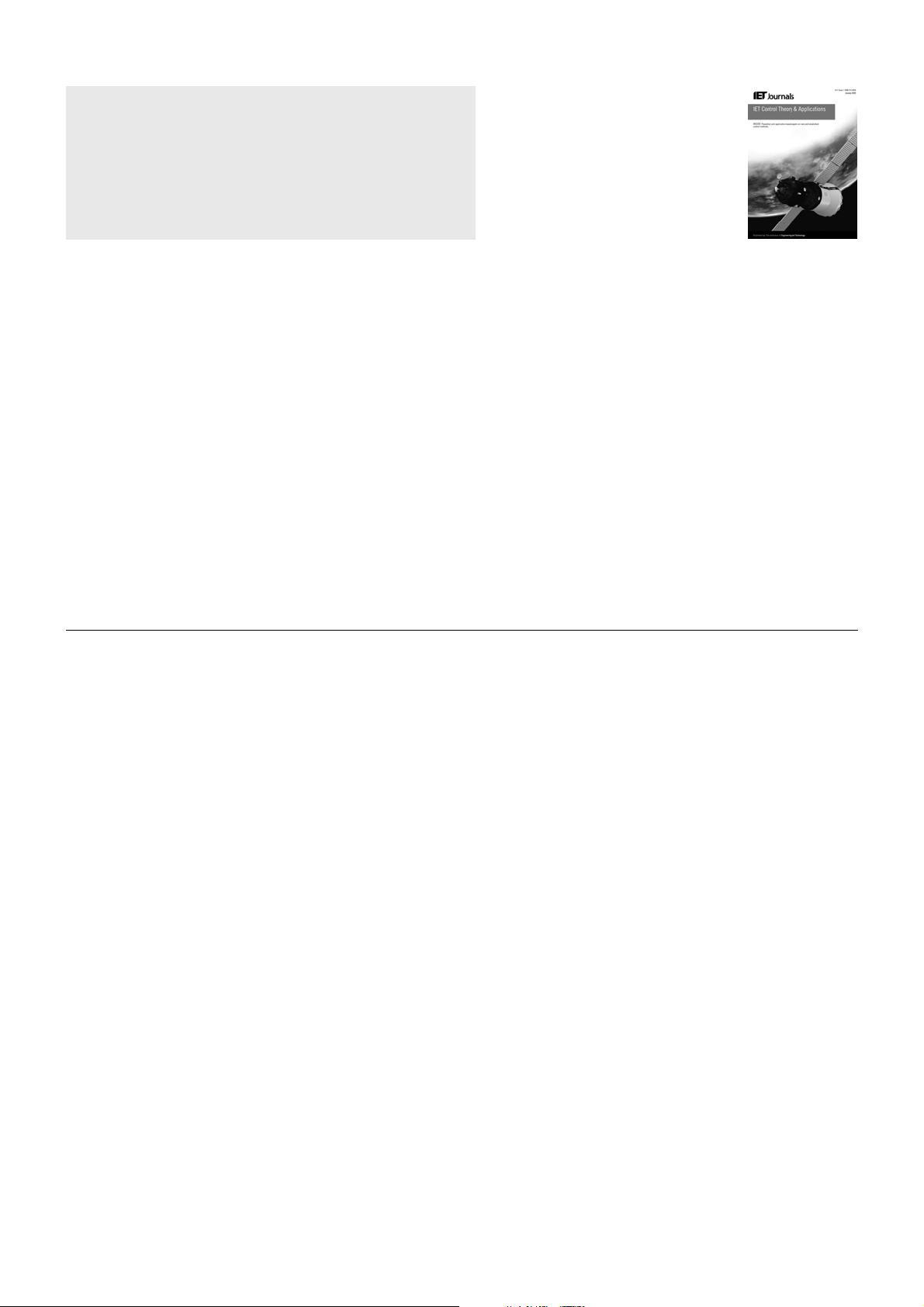
www.ietdl.org
Published in IET Control Theory and Applications
Received on 26th May 2011
Revised on 6th April 2012
doi: 10.1049/iet-cta.2011.0302
ISSN 1751-8644
Control and decision strategy for a class of Markovian
jump systems in failure prone manufacturing process
J. Zhu
1
L.P. Wang
1
M. Spiryagin
2
1
Department of Automation, University of Science andTechnology of China, Hefei 230027, People’s Republic of China
2
Center for Railway Engineering, Central Queensland University, Rockhampton 4702, Australia
E-mail: jinzhu@ustc.edu.cn
Abstract: This study investigates control and decision strategy for the failure prone manufacturing process, which is modelled
as a two-mode Markovian jump system (MJS). Considering the historical effects on the system, the mode transition rate
matrix (MTRM) is time-varying instead of homogeneous. A piecewise homogeneous MJS is thus proposed to characterise
this phenomenon, in which the MTRM is homogeneous during certain time intervals but non-homogeneous for the whole
time interval. By regarding each homogeneous MTRM as one event, all the MTRMs over the whole time interval will take
values in an event set and be governed by a higher-level Markov chain. To ensure such system operates normally with high
probability, the decisions including preventive maintenance and corrective maintenance are introduced to adjust the higher-
level Markov chain. Motivated by this, a new joint performance, consisting of both cost function for decision making and
controller design, is developed. Optimal decisions are obtained by an iterative algorithm whose convergence is proved, as
well as an optimal controller is designed. The effectiveness of this method is demonstrated by simulations.
1 Introduction
The past decades have witnessed the rapid development of
discrete event dynamic systems (DEDSs), which characterise
that state variables of such systems are driven by not
only continuous time, but also discrete events. DEDS can
find its applications in a wide area of communication
networks, voltage dividers and so on [1], resulting there is
an explosion on the research of this field. Among the studies
of DEDS, Markovian jump systems (MJSs) are arousing
lots of attention with fruitful results achieved recently, for
example, stability [2–4], filter [5, 6], control [7–17] and
solving coupled Lyapunov equations [18]. For systems of
such category, dynamical model remains unchanged until
random events occur. The occurrence of these events,
governed by a Markov chain, is called ‘mode jump’
and changes the system dynamical model correspondingly
[2]. According to the knowledge of stochastic process
[19], the probability of mode jump is represented by
a mode transition rate matrix (MTRM), and dynamical
model differs from one another with different mode taken.
Researches flourish on MJS because of whose powerful
modelling ability in many fields, such as target tracking
[20, 21], networked control systems [22, 23], failure prone
manufacturing process [24–26], fault-tolerant systems [27,
28] etc. Taking the failure prone manufacturing process
for example, the statuses of system consist of work status
and fault status, thus discrete mode jumps in continuous
dynamic are used to describe the machine’s status transition,
failure and reparation [2, 24–26]. Under the assumptions that
the MTRM is known and homogeneous, many literatures
about such process have been reported. Abou-Kandkil et al.
[24] consider the problems of optimal control for a multi-
machine multi-product manufacturing system subject to
machine failure; Boukas and Liu [25] study the production
and maintenance control of failure prone system consisting
of one machine and producing one part type; whereas a
two-stage continuous-flow system, which is separated by
a finite capacity buffer, is analysed in [26]. However,
assumptions are facing a big challenge while dealing with
the real-world failure prone manufacturing process.
In general, the failure prone manufacturing process
is a complex one whose statuses are divided into two
modes, work status and fault status. The system could
not remain work status permanently without any faults
in consideration of some factors such as unreliability of
components, external disturbances and so on [29, 30].
Similarly, the faulty machine has a chance to proceed if
it is fixed artificially. With the application of two-mode
MJS model, the system mode switches between work status
and fault status randomly, therefore this switching process
is modelled as mode jump. Moreover, the mode transition
rate from work status to fault status (‘going-wrong rate’ for
simplification) varies for systems with different historical
working situations, when noting a fact that even for the same
working period, an old system will go wrong with a higher
probability than a new one because of component aging,
fault or a combination of these. This means the MTRM
of such manufacturing process is no longer homogeneous
which is an intractable problem for controller design.
Considering the practical operation of manufacturing system
which is a long-term process, the MTRM could remain
IET Control Theory Appl., 2012, Vol. 6, Iss. 12, pp. 1803–1811 1803
doi: 10.1049/iet-cta.2011.0302 © The Institution of Engineering and Technology 2012