FMEA分析:控制计划与过程流程的结合应用
需积分: 35 168 浏览量
更新于2024-08-22
收藏 734KB PPT 举报
"控制计划/过程流程结合图例-失效模式效应分析"
失效模式效应分析(Failure Mode and Effects Analysis,简称FMEA)是一种系统性的预防性质量管理工具,用于识别、评估和防止产品或过程可能出现的潜在失效模式。该方法通过分析可能导致失效的原因,评估其可能产生的后果以及风险优先级(Risk Priority Number,RPN),从而制定相应的预防措施,确保产品质量和过程稳定性。
FMEA的目标主要包括:
1. 掌握FMEA的基本概念和应用时机,以便在产品设计和过程开发的早期阶段就进行考虑。
2. 发现并评价产品及过程中潜在的失效模式及其可能带来的后果,以便及时采取行动。
3. 寻找并实施策略以避免或减少这些潜在失效的发生,从而提高产品的可靠性与安全性。
4. 将整个分析过程记录在案,作为未来参考和持续改进的基础。
FMEA是团队合作的产物,整合了多个方面的知识,如顾客需求、工程规范、系统和组件描述、过程和供应商需求等。它与设计和过程改进紧密相连,通过系统设计和过程FMEA来消除潜在失效,同时,它也是一个动态的工具,需要随着产品生命周期的推进进行定期评审和更新。
失效模式是指在特定条件下,产品无法完成预期功能的情况。这可能包括性能超出规定的上下限、组件破损或损坏等。FMEA强调的是在问题发生前进行预测和预防,而非事后补救。在实际操作中,FMEA有时可能被误解为过于复杂或耗时,但其价值在于其能够帮助组织在产品生命周期的早期阶段发现问题,从而避免后期更昂贵的修复成本。
在实施FMEA时,需要创建一个过程流程清单,涵盖所有过程,并将其转化为详细的过程控制计划。通过PFMEA(Process FMEA)对主要过程进行分析,利用RPN值来量化风险,以便确定需要优先处理的问题。DFMEA(Design FMEA)则侧重于产品设计阶段的潜在失效分析。
控制计划/过程流程结合图例与FMEA的结合使用,有助于企业系统地管理过程,确保产品开发和生产过程中的质量控制,降低风险,提升客户满意度。
2017-11-03 上传
2021-05-26 上传
2021-05-30 上传
2021-05-29 上传
2021-11-07 上传
2021-05-30 上传
2021-05-29 上传
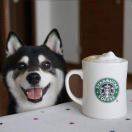
琳琅破碎
- 粉丝: 19
- 资源: 2万+
最新资源
- 黑板风格计算机毕业答辩PPT模板下载
- CodeSandbox实现ListView快速创建指南
- Node.js脚本实现WXR文件到Postgres数据库帖子导入
- 清新简约创意三角毕业论文答辩PPT模板
- DISCORD-JS-CRUD:提升 Discord 机器人开发体验
- Node.js v4.3.2版本Linux ARM64平台运行时环境发布
- SQLight:C++11编写的轻量级MySQL客户端
- 计算机专业毕业论文答辩PPT模板
- Wireshark网络抓包工具的使用与数据包解析
- Wild Match Map: JavaScript中实现通配符映射与事件绑定
- 毕业答辩利器:蝶恋花毕业设计PPT模板
- Node.js深度解析:高性能Web服务器与实时应用构建
- 掌握深度图技术:游戏开发中的绚丽应用案例
- Dart语言的HTTP扩展包功能详解
- MoonMaker: 投资组合加固神器,助力$GME投资者登月
- 计算机毕业设计答辩PPT模板下载