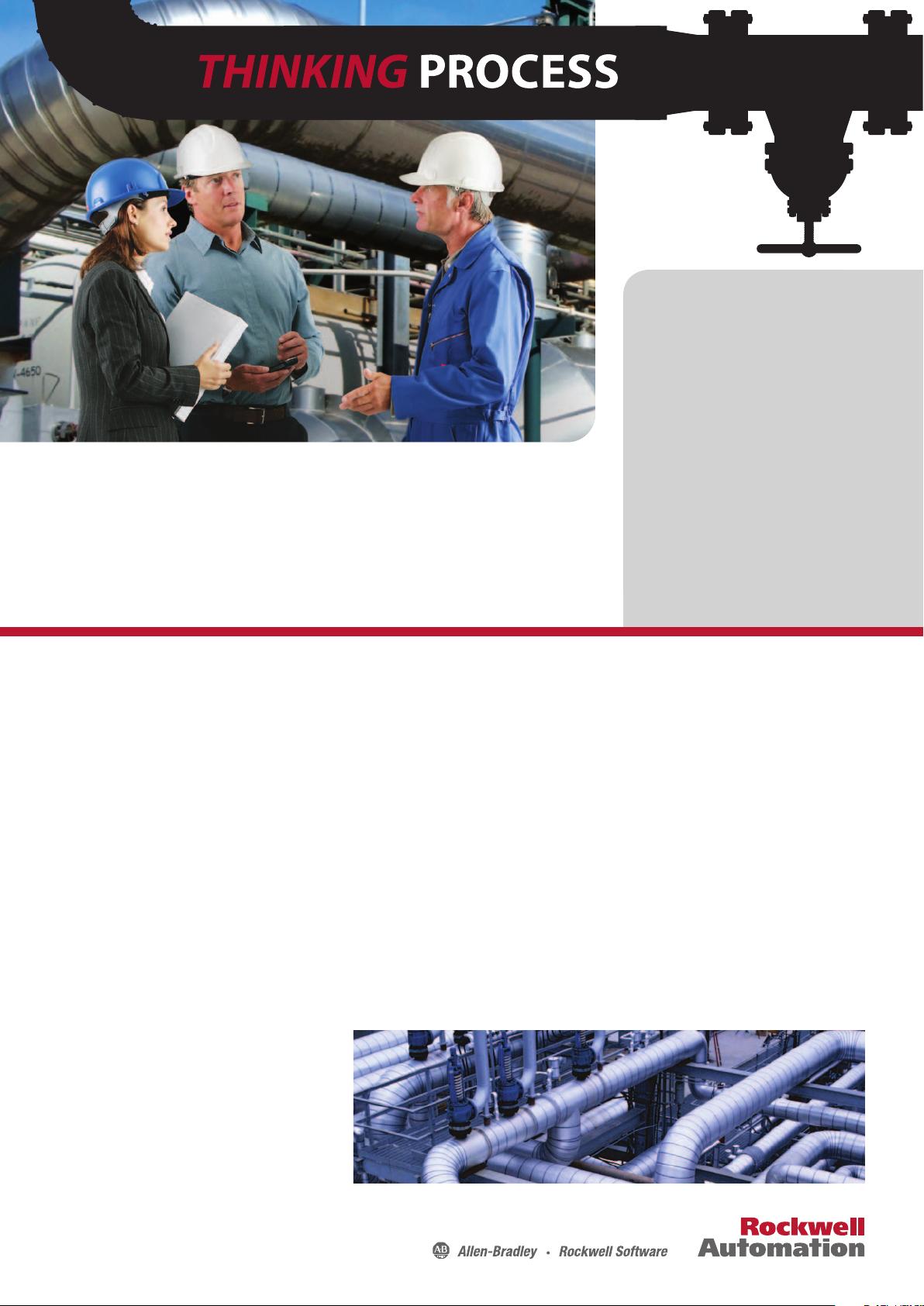
2010 – Issue 6
IN THIS ISSUE
This edition of Thinking Process focuses on migrating from legacy DCS
systems to the PlantPAx™ Process Automation System. We discuss benefits
of migrating from a legacy system using a three-phased migration
strategy to eliminate many of the costs, risks and complexities involved
with migrations. We also feature success stories that highlight successful
migrations, and we invite you to join us to learn more with a full week of
process education at our Process Solutions User Group (PSUG) and the
Automation Fair® event this fall.
The Risk vs. Return of DCS Migrations
Page 1-2 The Risk vs. Return of
DCS Migrations
Page 3 Three-Phased
Migration Process
Page 4 Migration Solutions
and Resources
Page 5-6 Colorado Springs Utilities
Page 7 Hwado Water
Treatment Facility
Page 8 Events
UPDATE
Increase productivity and profitability by
upgrading your control system in phases
The equipment is running for now, but it’s
taking longer and longer to find replacement
parts. You often look for them on eBay
because the parts houses you typically use
no longer have what you need, and the parts
that are in stock are getting more expensive.
Finding service is getting tougher too. Your
legacy system might be 20 or more years
old, and the engineers and technicians who
originally installed it are retiring. Even the
incumbent vendors are not supporting these
old systems anymore.
Things can’t last like this, but what can you
do? It’s difficult to justify a system migration
based only on what might happen. However, if
you’re able to demonstrate the improvements
that new technology can provide, your
argument for migration strengthens.
Beyond risk mitigation
Migration decisions can be broken down
into two categories – risk mitigation and
performance improvements. Risk mitigation
is about what keeps you up at night, and
performance improvements are what provide
a sustainable and competitive advantage.
As companies consider migrating, they want
to know and understand their potential gains
in both areas. However, it’s difficult to get
excited about future productivity gains if
it means crippling current production. Do I
have to update my system all at once? Do we
have to stop production? How can I budget
a project of this type? These questions are
universally voiced across industries when
migrations are discussed.
Companies today are most frequently
migrating away from legacy DCS that only
control the process, whether for a chemical
plant, steel mill or utility plant. Now,
companies can replace these dedicated
systems with a single, plantwide control
system, connecting the process, conveyor
lines, discrete manufacturing, drive, batch and
safety applications.
Migrating to newer equipment can offer many
benefits, such as increased information flow,
more production with greater throughput, less
training and spares and reduced energy costs.
A single, plantwide system allows for an
unlimited number of reports, which are
easy enough for you to create based on
the increased data available. This means
better control over quality, tighter process
management and greater potential for
a satisfied customer, all of which adds
competitive advantage.
In addition, expert data-sharing helps produce
higher quality products, increased operator
knowledge and provides corporate entities
with improved production capabilities.
Justifying funding for a migration
Often people seeking to justify equipment
migrations are middle managers who are
concerned with manufacturing a quality
product on time and at a cost point that
provides a competitive advantage. Formal
financial tools, such as Return on Investment
(ROI), Total Cost of Ownership (TCO), and