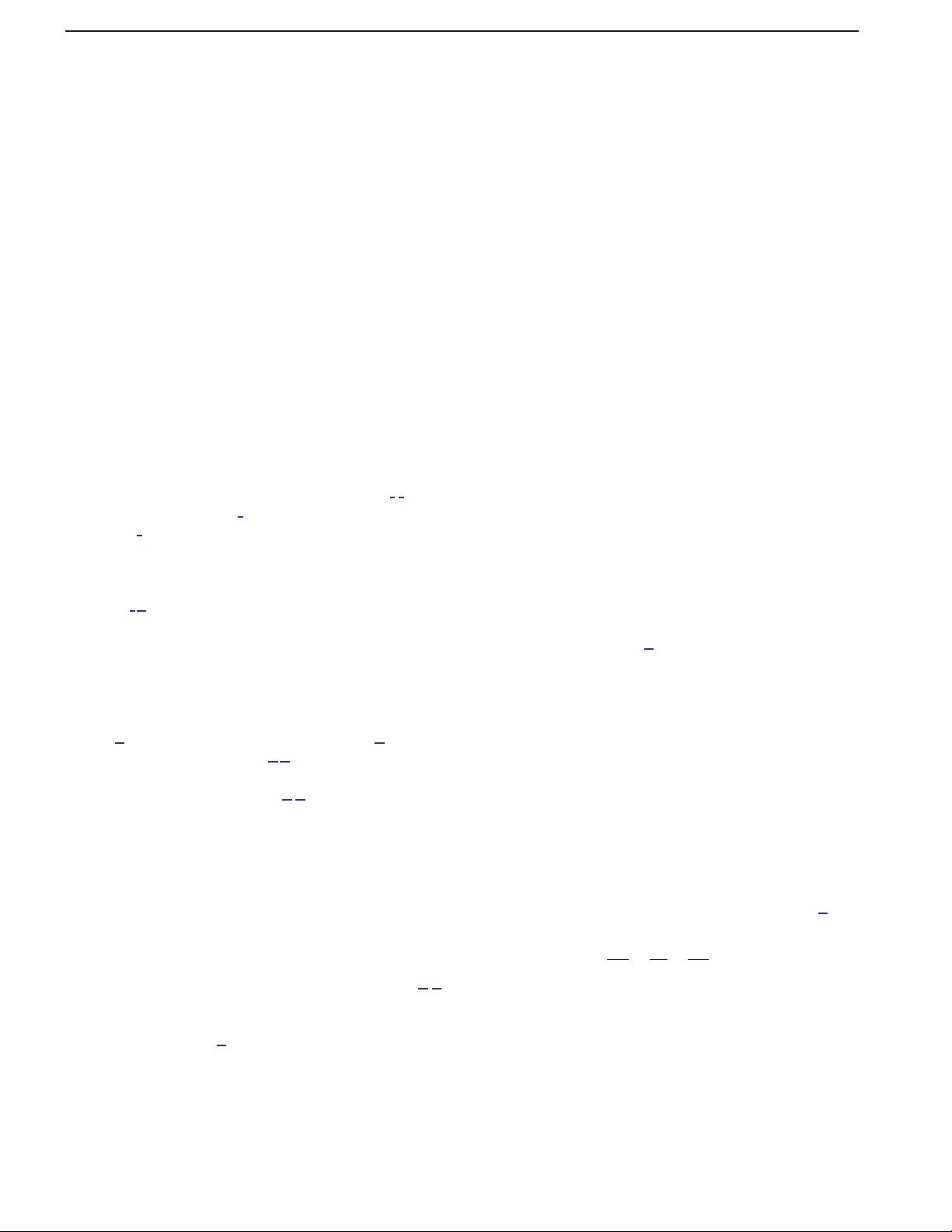
Vibration-insensitive fiber spool for laser stabilization
Junchao Huang (黄军超)
1,2
, Lingke Wang (汪凌珂)
1,2
, Yifei Duan (段怡菲)
1,2
,
Yafeng Huang (黄亚峰)
1,2
, Meifeng Ye (叶美凤)
1
, Lin Li (李 琳)
1
, Liang Liu (刘 亮)
1
,
and Tang Li (李 唐)
1,
*
1
Key Laboratory of Quantum Optics, Shanghai Institute of Optics and Fine Mechanics, Chinese Academy of Sciences,
Shanghai 201800, China
2
Center of Materials Science and Optoelectronics Engineering, University of Chinese Academy of Sciences,
Beijing 100049, China
*Corresponding author: litang@siom.ac.cn
Received April 1, 2019; accepted May 6, 2019; posted online July 17, 2019
Excess frequency noise induced by mechanical vibration is the dominant noise source at low Fourier frequencies
in fiber-delay-line stabilized lasers. To resolve this problem, a double-winding fiber spool is designed and
implemented that has ultralow acceleration sensitivity in all spatial directions. By carefully choosing the optimal
geometry parameters of the fiber spool, we achieve acceleration sensitivity of 8 × 10
−11
/g and 3 × 10
−11
/g
(g denotes the gravitational acceleration) in axial and radial directions, respectively.
OCIS codes: 140.3425, 120.7280, 060.2310.
doi: 10.3788/COL201917.081403.
Ultrastable lasers play a vital role in the field of precision
measurement science, such as optical clocks
[1–6]
, gra-
vitational wave detection
[7]
, and very-long-baseline inter-
ferometers
[8]
. State-of-the-art ultrastable lasers are real-
ized by locking to rigid Fabry–Pérot (FP) cavities using
the Pound–Drever–Hall technique. This kind of laser has
achieved a fractional frequency stability below
1×10
−16
[9,10]
. However, the system of this powerful
method is complex and bulky because it requires tight
alignment of free-space optical elements, precise polariza-
tion adjustment, spatial mode matching, and even
cryocooler, and consequently limits the transportable
applications of ultrastable lasers. These applications in-
clude the space mission of gravitational wave detection
(LISA)
[11]
, ultralow noise microwave synthesis
[12]
, and op-
tical frequency dissemination
[13,14]
. As an alternative to
high-finesse FP cavities, fiber-delay-line (FDL) stabilized
lasers have been demonstrated
[15–19]
. Because of its all-
fiber-based structure, this approach features compactness,
light weight, and high reliability. The FDL stabilized laser
is sensitive to seismic noise over the range from several
hertz to hundreds of hertz. Environmental vibration
causes fiber deformations that introduce phase fluctua-
tions of the propagating light and convert into excess fre-
quency noise for the stabilized laser. To overcome this
problem, a fiber spool with low acceleration sensitivity
is required. In the last two decades, the acceleration sen-
sitivity of the fiber spool has been fully investigated
[20–26]
.
Among the above studies, Li et al . firstly proposed a fiber
spool that could have ideal zero acceleration sensitivity
along its winding axis
[21]
. They wound optical fiber onto
a cylinder that is vertically supported at its midplane.
Under vertical vibration, the top half and the bottom half
deform with the same quantity except with the opposite
sign. By precisely tuning the supporting point, zero
acceleration sensitivity can be achieved. In practice, due
to the large sensitivity slope, however, it is difficult to ap-
proach this “zero point” due to the unavoidable fiber-
winding error and machining error. Additionally, this fiber
spool cannot maintain low acceleration sensitivity in the
radial (the direction in the spooling plane) and axial direc-
tions simultaneously because the “zero point” is very sen-
sitive to the geometry parameter. To resolve this problem,
Hu et al. proposed a fiber spool model with a symmetri-
cally mounted structure
[22]
. However, this model is not
practical because of its bulky volume and complex mount-
ing method. In this study, we propose a double-winding
fiber spool with integrated support configuration. The
double-winding feature can once more provide cancella-
tion of spool deformation compared to Li et al.’s model,
while the integrated support configuration avoids the
complex mounting structure of Hu et al.’s model to make
the fiber spool more compact and easily assembled. The
numeric analysis shows that this spool can achieve accel-
eration sensitivities of ∼10
−12
∕g (g denotes the gravita-
tional acceleration) in both the axial and radial
directions over a range of geometry parameters.
In an FDL laser stabilization scheme, the acceleration
sensitivity of the stabilized laser can be defined as
[22]
Γ
a
¼
Δν
ν
0
a
¼
Δτ
τa
¼
ΔL
La
; 1∕g; (1)
where ν
0
is the optical frequency, Δν is the vibration-
induced frequency noise, a is the vibration variation in
unit of g, τ is the delay time of the FDL, Δτ is the vibration-
induced variation of delay time, L is the fiber length, and
ΔL is the vibration-induced variation of fiber length. The
numeric analysis of the fiber spool is done by the finite
element method (FEM) with the hypothesis that fiber
COL 17(8), 081403(2019) CHINESE OPTICS LETTERS August 2019
1671-7694/2019/081403(5) 081403-1 © 2019 Chinese Optics Letters