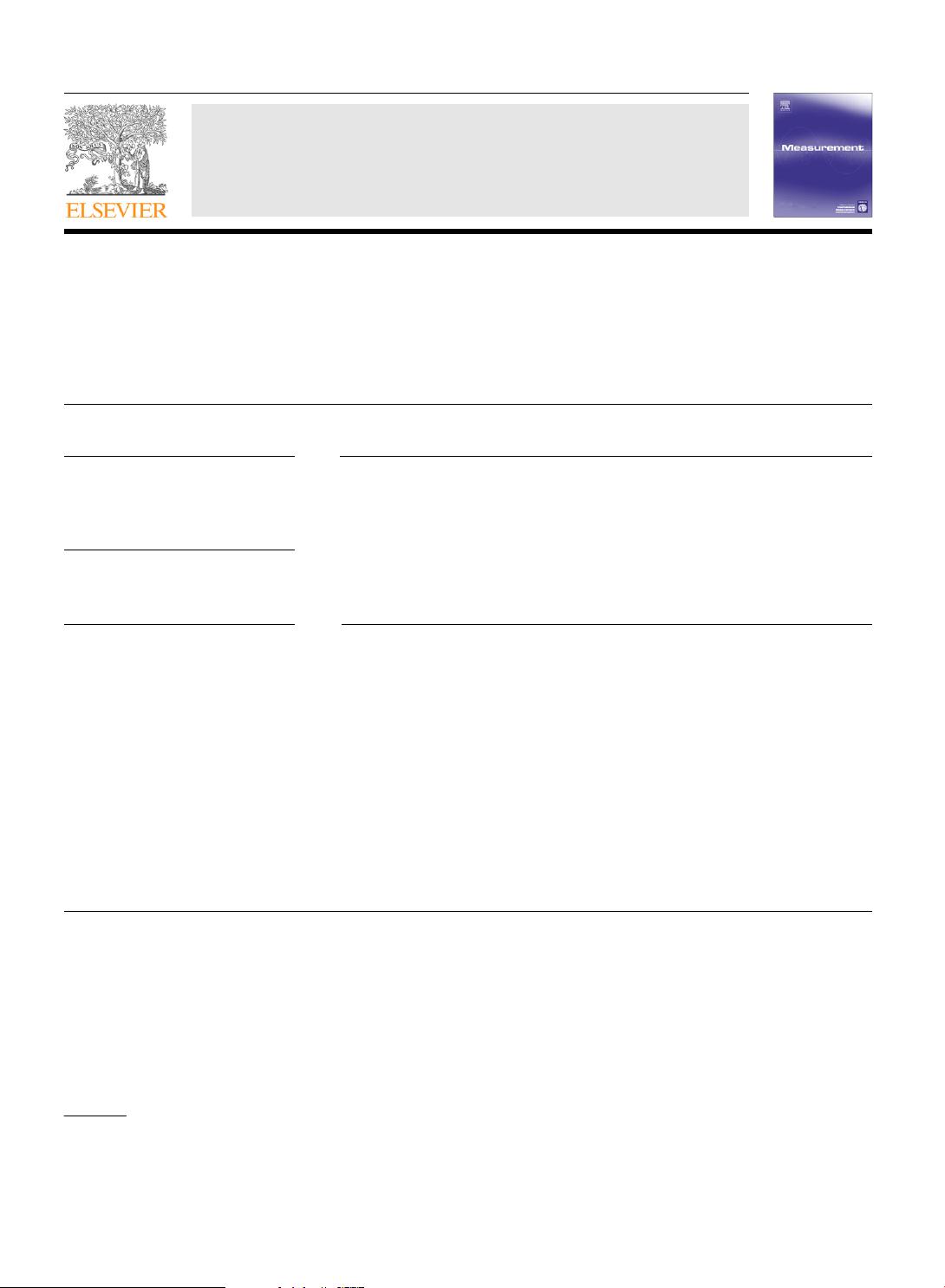
Review
Development of an auto-focus system based on the moiré method
Ju-Yi Lee
a,
⇑
, Yung-Hsing Wang
b
, Lyu-Jhen Lai
a
, Yu-Ju Lin
a
, Yu-Hsiu Chang
b
a
Institute of Opto-Mechatronics Engineering, National Central University, 300 Jhongda Rd., Jhongli City, Taoyuan County 320, Taiwan
b
Opto-Electronics Sensing Department of Laser Application Technology Center, Industrial Technology Research Institute, Tainan County 734, Taiwan
article info
Article history:
Received 27 December 2010
Received in revised form 26 July 2011
Accepted 29 August 2011
Available online 3 September 2011
Keywords:
Auto-focus
Moiré
Spiral grating
abstract
An auto-focus system based on the moiré effect and a feedback control method is pre-
sented. First, a collimated laser beam passes through a focusing lens then falls incident
on the surface of the sample. The deviation of the angle of the light reflected back is pro-
portional to the defocus distance from the sample. The reflected light then passes through
two spiral gratings, producing three types of moiré pattern which can be observed and
recorded by a linear CCD. The defocus distance can be derived from the spiral angle in
the moiré pattern. The results show that auto-focusing can be achieved by the moiré
method for glass and mirror samples in a cycle time of less than 0.1 s.
Ó 2011 Elsevier Ltd. All rights reserved.
Contents
1. Introduction . . . ........................................................................................ 1793
2. Principles . . . . . ........................................................................................ 1794
2.1. Moiré patterns resulting from the defocus distance . . . . . . . . . . . . . . ........................................ 1794
2.2. Measurement of the moiré pattern variation ........................................................... 1795
3. Experimental results and discussion. . . ..................................................................... 1796
3.1. S-curve testing with different samples . . . . . ........................................................... 1796
3.2. S-curve testing with different focal lenses and for different locations d of the linear CCD . . ..................... 1796
3.3. Auto-focus testing . . . . . . ........................................................................... 1797
3.4. Other applications: testing straightness error with the linear stage . ........................................ 1799
4. Conclusion . . . . ........................................................................................ 1799
Acknowledgment . . . . . . . . . . . . . . . . . . ..................................................................... 1800
References . . . . ........................................................................................ 1800
1. Introduction
Auto-focus technology is widely used in many inspec-
tion instruments and in industrial applications, such as
for automatic optical inspection (AOI), in the laser machin-
ing industry, and in microscopes [1,2]. For example, in the
Thin Film Transistor Liquid Crystal Display (TFT-LCD)
industry, the most important process for control of the
quality of the display is to inspect for visual defects. There
are three main steps to the manufacturing process: array,
cell, and module assembly [3]. In the array assembly
process, transistors are fabricated on a glass substrate.
Heating causes the middle of the LCD to become lower
than the others parts because of the huge expanse of the
panel. Deformation due to unequal heating will affect the
clarity of the image during the inspection process, making
it hard to reduce the reliable cycle time in the TFT-LCD
module manufacturing process.
0263-2241/$ - see front matter Ó 2011 Elsevier Ltd. All rights reserved.
doi:10.1016/j.measurement.2011.08.026
⇑
Corresponding author.
E-mail address: juyilee@ncu.edu.tw (J.-Y. Lee).
Measurement 44 (2011) 1793–1800
Contents lists available at SciVerse ScienceDirect
Measurement
journal homepage: www.elsevier.com/locate/measurement