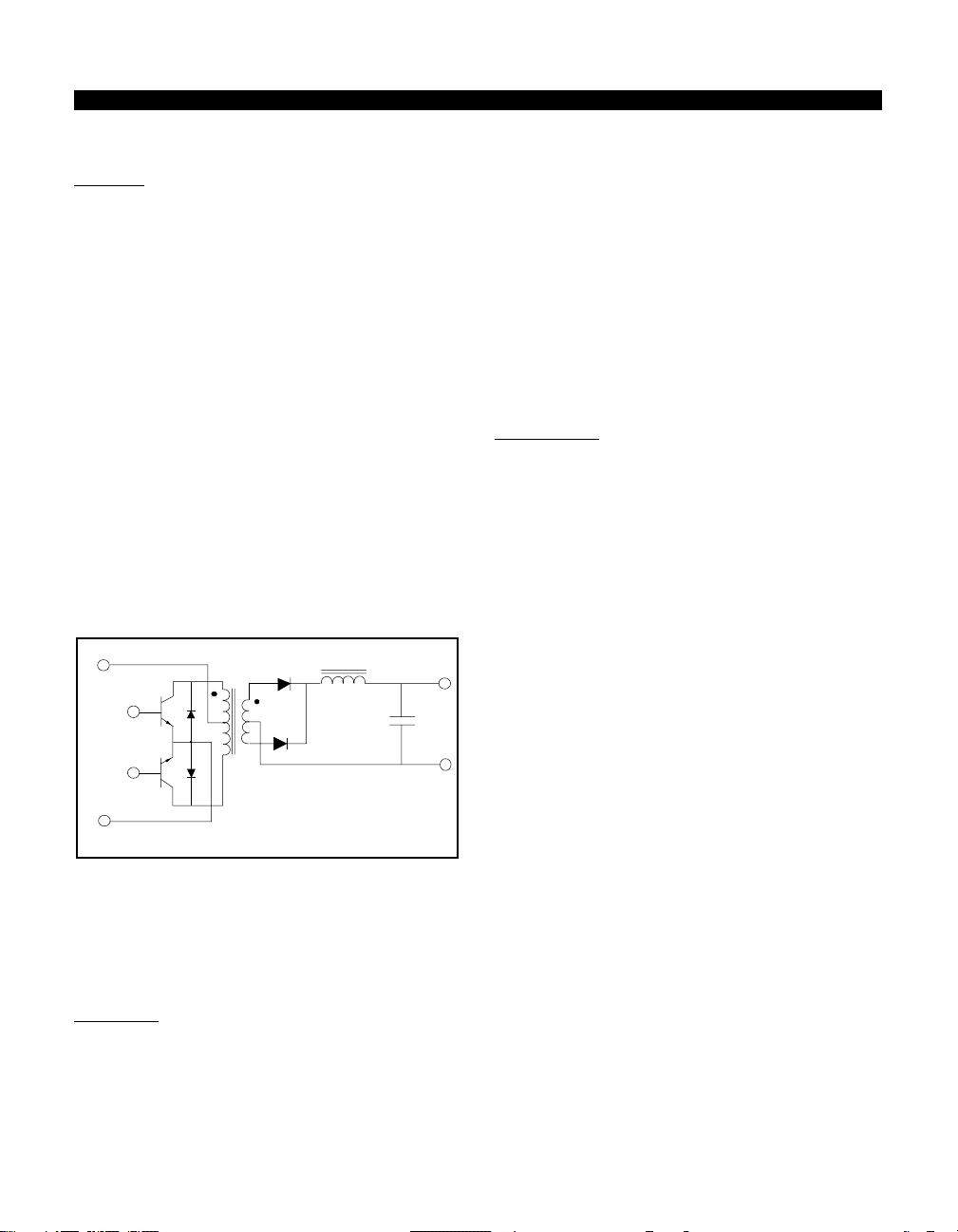
S.M.P.S. Power Semiconductor Applications
Philips Semiconductors
(c) The Push-pull converter.
Operation.
To utilise the transformer flux swing fully, it is necessary to
operate the core symmetrically as described earlier. This
permits much smaller transformer sizes and provides
higher output powers than possible with the single ended
types. The symmetrical types always require an even
number of transistor switches. One of the best known of the
symmetrical types is the push-pull converter shown in
Fig. 10.
The primary is a centre-tapped arrangement and each
transistor switch is driven alternately, driving the
transformer in both directions. The push-pull transformer is
typically half the size of that for the single ended types,
resulting in a more compact design. This push-pull action
produces natural core resetting during each half cycle,
hence no clamp winding is required. Power is transferred
to the buck type output circuit during each transistor
conduction period. The duty ratio of each switch is usually
less than 0.45. This provides enough dead time to avoid
transistor cross conduction. The power can now be
transferred to the output for up to 90% of the switching
period, hence allowing greater throughput power than with
the single-ended types. The push-pull configuration is
normally used for output powers in the 100 to 500W range.
Fig. 10 Push-pull converter.
The bipolar switching action also means that the output
circuit is actually operated at twice the switching frequency
ofthe powertransistors, ascan be seenfromthewaveforms
in Fig. 11. Therefore, the output inductor and capacitor can
be even smaller for similar output ripple levels. Push-pull
converters are thus excellent for high power density, low
ripple outputs.
Advantages.
As stated, the push-pull offers very compact design of the
transformer and output filter, while producing very low
output ripple. So if space is a premium issue, the push-pull
could be suitable. The control of the push-pull is similar to
theforward, in that it is againbasedon the continuous mode
buck. When closing the feedback control loop,
compensation is relatively easy. For multiple outputs, the
same recommendations given for the forward converter
apply.
Clamp diodes are fitted across the transistors, as shown.
This allows leakage and magnetisation energy to be simply
channelled back to the supply, reducing stress on the
switches and slightly improving efficiency.
The emitter or source of the power transistors are both at
the same potential in the push-pull configuration, and are
normally referenced to ground. This means that simple
base drive can be used for both, and no costly isolating
drive transformer is required. (This is not so for the bridge
types which are discussed latter.)
Disadvantages.
One of the main drawbacks of the push-pull converter is
the fact that each transistor must block twice the input
voltage due to the doubling effect of the centre-tapped
primary, even though two transistors are used. This occurs
when onetransistor isoff and the other is conducting. When
both are off, each then blocks the supply voltage, this is
shown in the waveforms in Fig. 11. This means that TWO
expensive, less efficient 800 to 1000V transistors would be
required for a 220V off-line application. A selection of
transistors and rectifiers suitable for the push-pull used in
off-line applications is given in Table 4.
A further major problem with the push-pull is that it is prone
to flux symmetry imbalance. If the flux swing in each half
cycle is not exactly symmetrical, the volt-sec will not
balance and this will result in transformer saturation,
particularly for high input voltages. Symmetry imbalance
can be caused by different characteristics in the two
transistors such as storage time in a bipolar and different
on-state losses.
The centre-tap arrangement also means that extra copper
is needed for the primary, and very good coupling between
the two halves is necessary to minimise possible leakage
spikes. It should also be noted that if snubbers are used to
protect the transistors, the design must be very precise
since each tends to interact with the other. This is true for
all symmetrically driven converters.
These disadvantages usually dictate that the push-pull is
normally operated at lower voltage inputs such as 12, 28
or 48V. DC-DC converters found in the automotive and
telecommunication industries are often push-pull designs.
At these voltage levels, transformer saturation is easier to
avoid.
Since the push-pull is commonly operated with low dc
voltages, a selection guide for suitable power MOSFETs is
also included for 48 and 96V applications, seen in Table 5.
Vo
T1 D1
Co
n : 1
TR1
D2
L1
TR2
Vin
119