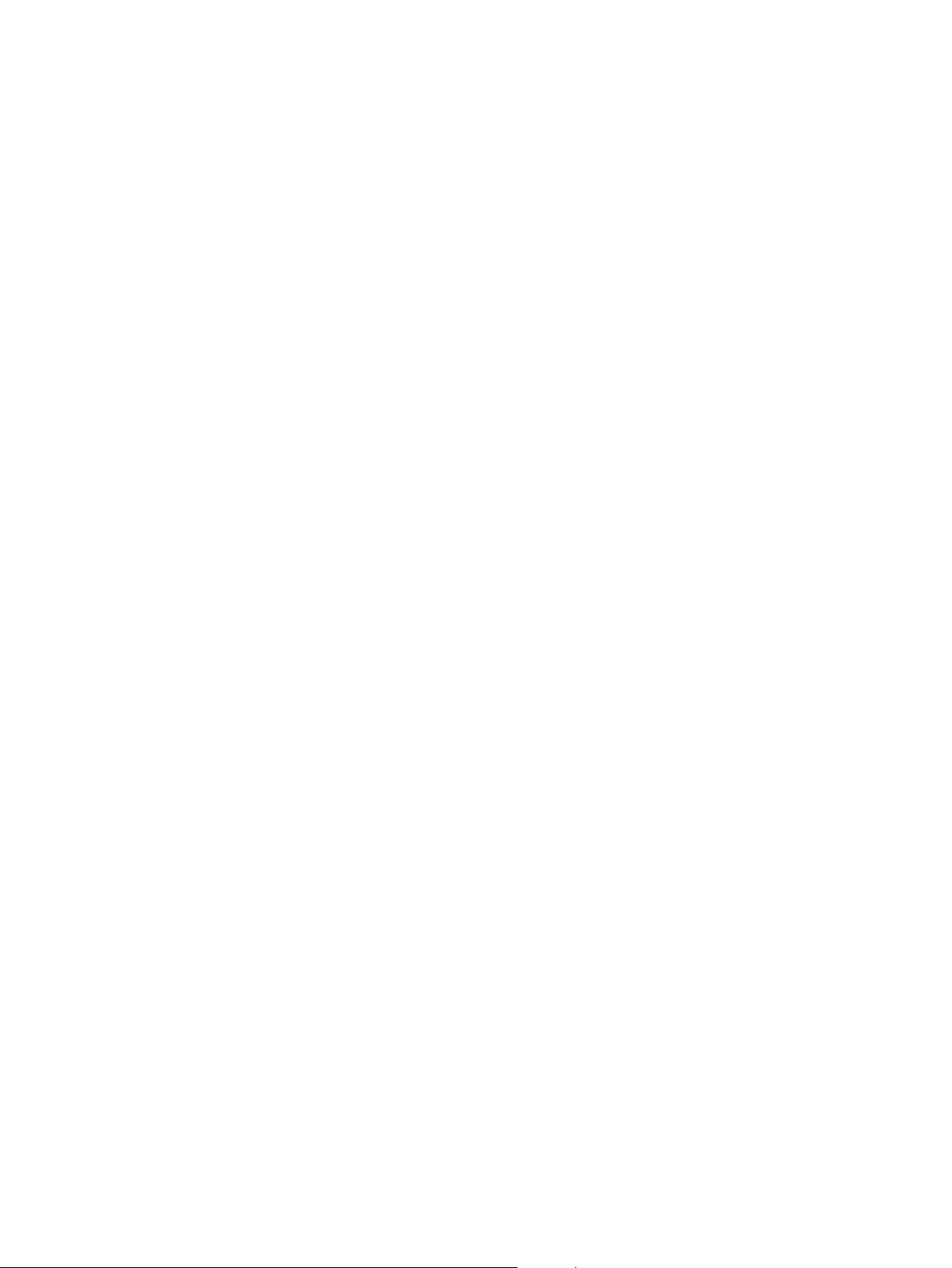
(2000) addressed performance planning through resource alloca-
tion in supply networks by developing a profit maximizing model
for distribution planning for the traditional make-to-stock supply
chains.
Demirli and Yimer (2008) propose a mixed integer fuzzy pro-
gramming (MIFP) approach to the production–distribution sched-
uling problem in BTO manufacturing supply chains with
uncertain cost parameters. The effect of price incentives on de-
mand characteristics of customizable BTO products is modeled as
a stochastic dynamic programming problem in Weng and Parlar
(2005). The use of modularity in the BTO product design as a solu-
tion to optimal return policy in internet marketing is presented in
Mukhopadhyay and Setoputro (2005).
Genetic algorithm (GA) based approaches have been applied to
different production, distribution and inventory related problems
in supply chain operations. A GA based approach is proposed by
Moon et al. (2002) to determine optimal schedule of machine
assignments and operations sequences in a make to stock supply
chain, so that the total tardiness will be minimized. In two-echelon
single vendor–multiple buyers supply chain model under vendor
managed inventory (VMI) mode of operation, Nachiappan and
Jawahar (2007) formulates a nonlinear integer programming
problem (NIP) with a GA based heuristic in order to find out the
optimal sales quantity for each buyer. A genetic algorithm solution
procedure for a mixed integer nonlinear programming model of a
dynamic integrated distribution network of third party logistic
providers (3PLs) is discussed in Ko and Evans (2007). Naso, Surico,
Turchiano, and Kaymak (2007) present a scheduling algorithm
that combines a GA and a set of constructive heuristics for the
just-in-time production and delivery of ready-mixed concrete on
a set of distributed and coordinated production centers. A hybrid
genetic algorithm (HGA) is implemented in Torabi, Ghomi, and
Karimi (2006), to solve the economic lot sizing and delivery
scheduling problem in a simple supply chain where the production
system is considered to be a flexible flow line. Lee, Jeong, and Moon
(2002) suggested a genetic algorithm based heuristic to solve an
advanced planning and scheduling (APS) model of a manufacturing
supply chain with outsourcing and due date requirements.
In this paper, a multi-product and multi-plant BTO supply chain
with manifold supply and distribution channels is considered for
analysis. We proposed a two-phase MILP model for procurement,
production, and distribution of customized products in a BTO man-
ufacturing system. As opposed to formulating the problem as a
fully integrated single model, the sequential two-phase approach
helps to develop a robust solution procedure by decoupling the
customized manufacturing operation from the standard compo-
nent fabrication process. The proposed modeling is comprehensive
in nature as it incorporates crucial pragmatic constraints resulting
from capacity limitations, material flow equations, product cus-
tomization and customer service requirements. The rest of the pa-
per is organized as follows. Brief description of the problem
considered for analysis and its mathematical formulation is pre-
sented in Section 2. In Section 3, we put forward a genetic algo-
rithm solution procedure adopted in solving the problem. Results
of numerical experimentation used to demonstrate the proposed
approach are illustrated in Section 4. Summary and concluding re-
marks are given in Section 5. Finally, list of notations used to for-
mulate the mathematical models are set out in the nomenclature
part.
2. Description and formulation of the problem
In general, the build-to-order supply chains operate as a pull
system driven by customer orders at the downstream end of the
network. The finished products manufactured by assembly plants
reach to end user consumers through channels of a distribution
system. Efficient supply and distribution systems are thus essential
entities for manufacturing firms to meet the demand of customers
for good quality products at reasonably low cost. The BTO supply
chain is essentially a hybrid of make-to-order (MTO) and assem-
ble-to-order (ATO) strategies. Standard parts and subassemblies
are acquired or manufactured in-house according to short-term
forecasts, while schedules for few customized components and
the final assembly of products are not executed until detailed prod-
uct specifications have been derived from booked customer orders,
see Sen, Pokharel, and YuLei (2004). As a strategy, the objective of
BTO is to provide custom-made products in a mass-scale. There-
fore, the customer order decoupling point (CODP) in BTO system
falls between the CODP’s of MTO and ATO systems.
As illustrated in
Fig. 1,
the BTO supply chain network consists of
two
major
subsystems
: a production-subsystem and a distribu-
tion-subsystem. The production-subsystem includes raw-material
suppliers, component fabricators and product assemblers. The dis-
tribution-subsystem while consists finished product warehouses,
intermediate distribution centers (DCs), retailers and downstream
customers. Therefore, the supply chain scheduling problem can
logically be decomposed into two sub-problems:
(i) Phase-1: Developing a dynamic model for assembling and
distribution planning of final products as per customer order
specifications and
(ii) Phase-2: Formulating a planning model for components fab-
rication and raw-materials procurement, based on the out-
puts of the previous model.
The material acquisition, production and distribution planning
and scheduling problem should be approached in an integrated
manner. The two sub-problems are interrelated to each other
and should be dealt sequentially. The issue of integrated approach
in planning and scheduling of BTO supply chains is addressed by
Demirli and Yimer (2008). Splitting the problem into two-phases,
however, offers a twofold advantage: both operational and model-
ing. From operational management perspective, this approach sim-
plifies planning and control of materials acquisition, processing
and distribution of products. From modeling perspective, the
two-phase approach gives an opportunity to develop more effi-
cient solution techniques without compromising the optimality
of a fully integrated problem.
The entire production–distribution plan operates in a rolling
horizon to allow changes in later periods as new plans are con-
structed. A plan is drawn for all periods in the horizon, but only
the first few periods that fall within the current delivery lead-time
will actually be implemented. When the plan for the first period is
frozen, a new plan is redone for periods from the second up to the
last period plus one. Due to latest information introduced in the
new run, the updated plan discloses more accurate results in the
short-term. The proposed sequential mathematical models are pre-
sented in the next two subsections. The list of notations used in
developing the models are given in nomenclature.
2.1. Phase-1: assembling and distribution plan of products (Model-I)
The production–distribution schedule in BTO systems is driven
by actual orders received from customers. Customers pick their pre-
ferred product styles from retailer catalogue and sign order requisi-
tions. Retailers are the market outlets from which final products are
delivered to customers while new orders are passed to assemblers.
They accumulate and make job orders to the assembly plants ahead
of the projected production and delivery lead-time. Efficient com-
munication channel between dealers and finished product assem-
blers is therefore a critical factor to ensure product availability and
A.D. Yimer, K. Demirli / Computers & Industrial Engineering 58 (2010) 411–422
413