DCS集散控制系统详解:概念、构成与发展
需积分: 27 37 浏览量
更新于2024-07-11
收藏 9.77MB PPT 举报
"DCS概述-DCS集散控制系统"
DCS,即分布式控制系统,是一种以微处理器为核心,结合计算机技术、通信技术、CRT显示技术和控制技术的新型自动化控制系统。这种系统的特点在于将危险分散控制,同时保持操作和管理的集中,确保在工业生产过程中的安全性和效率。
DCS的发展可以追溯到20世纪70年代末期,当时美国Honeywell公司推出了世界上首套DCS系统——TDC2000。这一系统标志着控制设备的分散化,能够对应分散的过程对象,并通过数据通信网络与操作站相连,实现了控制和监控功能的分散,降低了系统风险。随后,其他国际知名企业如Foxboro、Bailey、YOKOGAWA、TOSHIBA、Siemens和Hartman&Braum等也纷纷推出自家的DCS产品,但初期的产品大多基于8位CPU,技术限制较为明显。
进入80年代初中期,第二代DCS出现,这一时期的DCS系统在技术上有了显著提升,CPU升级至16位或32位,系统功能更加强大,可处理的数据量更大,通讯速度更快,人机交互界面更加友好。同时,系统的开放性、兼容性和模块化设计也得到了加强,使得DCS在各个工业领域得到了广泛应用。
DCS系统通常由以下几个主要部分构成:
1. 过程控制站:负责现场设备的直接控制,通常包含输入/输出卡件,用于采集现场信号并执行控制策略。
2. 操作员站:提供用户界面,操作人员可以通过CRT显示器进行实时监控、操作和数据记录。
3. 数据通信网络:连接各控制站和操作员站,实现数据交换。
4. 工程师站:用于系统配置、编程和故障诊断。
5. 历史数据库:存储过程历史数据,用于性能分析和故障排查。
DCS在工程设计时需要考虑以下原则:
- 系统的可靠性和安全性:确保在恶劣环境下稳定运行,避免单点故障影响全局。
- 灵活性和扩展性:方便增加或修改控制回路,适应生产线的变化。
- 维护便捷:模块化设计便于维护和更换。
- 通信兼容性:支持多种通信协议,与其他系统集成。
DCS的验收测试、安装、联调与投运是关键步骤,包括硬件安装检查、软件配置验证、系统调试和模拟运行等,以确保系统在实际运行中达到预期性能。
在应对系统故障时,DCS的常见故障解析和预防措施至关重要,包括定期维护、备份重要数据、故障诊断工具的使用以及合理的接地和屏蔽设计,以降低系统受干扰的可能性。
随着技术的进步,当前的DCS系统已经融合了更多先进技术,如冗余设计、现场总线、以太网通信、先进控制策略等,进一步提升了系统的性能和可靠性。同时,新兴的控制系统,如PLC、SCADA、MES和IIoT等,也在不同场景下与DCS形成互补,共同推动工业自动化的发展。
点击了解资源详情
点击了解资源详情
点击了解资源详情
2022-11-03 上传
2022-11-03 上传
2022-11-03 上传
点击了解资源详情
点击了解资源详情
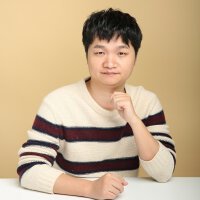
韩大人的指尖记录
- 粉丝: 32
- 资源: 2万+
最新资源
- 单片机英文资料 英文文献
- 从硬盘安装Linux操作系统
- flex cookbook
- at89c52芯片中文资料
- Matlab7官方学习手册
- C#面试题C#面试题
- ucos-ii中文版教程(第二版).pdf
- 通信元器件选用指南_新新电子有限公司供稿 方佩敏整理
- 图书管理系统需求 分析
- 银联销售点终端产品认证实施细则
- Globin-like蛋白质折叠类型识别
- A new look at discriminative training for hidden Markov models
- PCB高级设计讲义_射频与数模混合类高速PCB设计
- 3424aerwqerqwer
- C#向Excel报表中插入图片的2种方法
- 51学习笔记 简单的