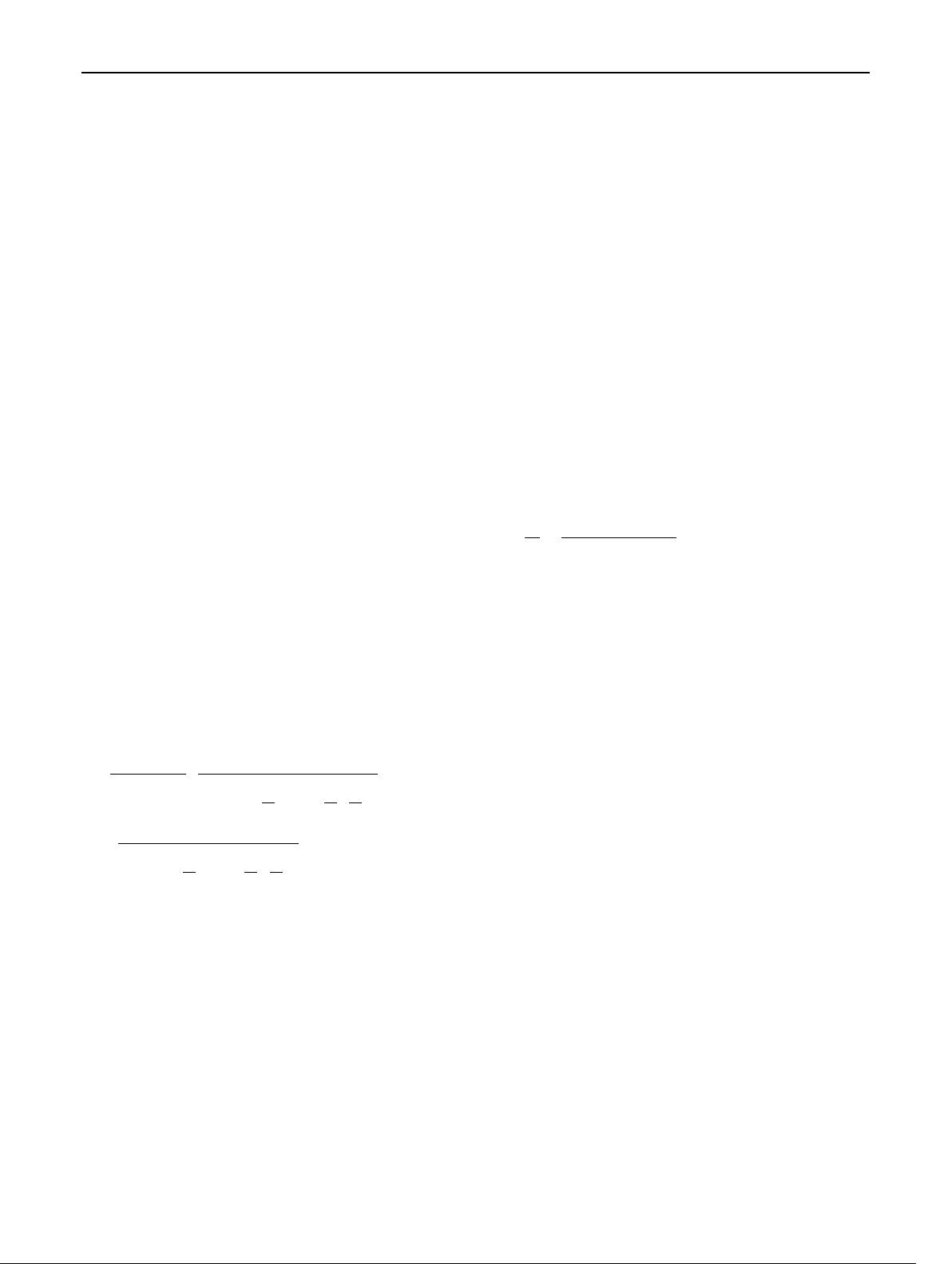
Meanwhile, the reflective grating moves in the sense
direction relative to the upper fixed grating. When incident
light passes vertically through the upper static grating to
the reflective grating, it is reflected and passes through the
fixed grating again, forming diffraction spots of different
orders. Because of the slight changes, the displacement
between the double-layer gratings results in a considerable
change in the reflectance characteristics (Carr et al. 2003).
We detect the Coriolis force by measuring the variation in
intensity of the ± 1 diffraction orders. Finally, we obtain
the input angular velocity, X, by measuring the change in
the photodetector output voltage.
3 Simulation analysis
The sensitivity of the optical micro-gyroscope based on
nano-grating detection is divided into three parts: struc-
tural, diffraction, and electrical. In this section, we describe
the modelling and analysis of each part as well as the
model of a complete micro-gyroscope system to obtain the
total sensitivity.
3.1 Design and simulation of structural
sensitivity
The structural sensitivity is defined as the ratio of the
change in magnitude of the displacement, B
y
, in the sense
direction of the micro-gyroscope due to the Coriolis effect,
to the change in the input angular velocity, X. Given the
sense structure of the micro-gyroscope (Fig. 1b), the
structural sensitivity of the designed micro-gyroscope has
the form:
S ¼
2 F
0
x
d
m
x
x
2
x
x
2
y
1
ffiffiffiffiffiffiffiffiffiffiffiffiffiffiffiffiffiffiffiffiffiffiffiffiffiffiffiffiffiffiffiffiffiffiffiffiffiffiffiffiffiffiffiffiffiffiffiffiffiffi
1
x
d
x
x
2
2
þ
1
Q
2
x
x
d
x
x
2
s
1
ffiffiffiffiffiffiffiffiffiffiffiffiffiffiffiffiffiffiffiffiffiffiffiffiffiffiffiffiffiffiffiffiffiffiffiffiffiffiffiffiffiffiffiffiffiffiffiffiffiffi
1
x
d
x
y
2
2
þ
1
Q
2
y
x
d
x
y
2
s
ð1Þ
where F
0
is the electromagnetic force, m
x
the drive mass,
and x
d
the drive frequency. The resonance frequencies of
the drive and sense modes, x
x
and x
y
, each have an
effective quality factor denoted by Q
x
and Q
y
, respectively.
From finite-element model simulations using ANSYS
software, the size of the micro-gyroscope structure was
optimized several times to achieve a final optimal resu lt.
Table 1 lists the specific structural dimensions and
parameter values of the mi cro-gyroscope. We obtained a
theoretical value for the structural sensitivity of the micro-
gyroscope of 6.402 nm/°/s.
A modal analysis of the structure was performed to
determine the drive and sense modes of the gyroscope (Li
et al. 2016). The first mode is the drive mode of the
structure (Fig. 2a), and the second mode is the sense mode
(Fig. 2b). From the simulation results, we concluded that
the drive and sense modes are well-matched, having mode
frequencies of 9287 Hz and 9288 Hz, respectively.
We analyzed the vibration characteristics of the micro-
gyroscope, including the harmonic response analysis and
the transient analysis. In the simulation, we input a drive
force of 5 lN. The angular velocity applied around the Z-
axis is 1 rad/s. From the harmonic response analysis of the
simulation, the results of the drive direction (Fig. 3a) and
of the sense direction (Fig. 3b) show that the displacement
amplitude is equal to 3.24,149 9 10
-7
m, with a frequency
of 9288 Hz. From a transient analysis, the simulation result
indicated the displacements of the drive direction (Fig. 4a)
and of the sense direction (Fig. 4b) to be
3.17,361 9 10
-7
m. The amplitudes of the sense direction
obtained by the two methods are close. Hence, the maxi-
mum structural sensitivity obtained from the simulation is
S
1
¼
B
y
X
¼
3:24149 10
7
m
57:32
=s
¼ 5:665nm=
=s; ð2Þ
which is close in value to that obtained from a theoretical
calculation.
3.2 Optical simulation and analysis of diffraction
sensitivity
The diffraction sensitivity is defin ed as the change in
intensity of diffraction incurred from the displacement of
the movable grating. Figur e 5 depicts the double-grating
scheme configured for the simulation, consisting of three
distinct regions: the upper grating, an air gap between the
two gratings, and the lower reflective grating. The lower
grating is designed to move horizontally in the plane,
whereas the upper grating is fixed. The geometrical
parameters of the grating (Fig. 5) determine the linearity of
the intensity of the transmitted light with the grating dis-
placement. They therefore need to be analyzed and
designed to achieve the highest detection sensitivity of the
displacement. Here, the lower grating layer moves hori-
zontally (X direction) relative to the fixed grating layer.
The periodicity of the grating is 800 nm. The center
wavelength of the incident light is 632 nm, and the duty
ratio of each grating is 0.5. In numerical simulations, we
studied the influence of five parameters (specifically, the
gap, D
1
,D
2
,D
3
, and D
4
, each independently) on the rela-
tionship between the displacement and the diffraction
efficiency.
Microsystem Technologies (2019) 25:1627–1637 1629
123