没有合适的资源?快使用搜索试试~ 我知道了~
首页"e-Traction PCM 2.0集成手册:控制系统整合指南"
"e-Traction PCM 2.0集成手册:控制系统整合指南"
需积分: 5 0 下载量 150 浏览量
更新于2024-04-12
收藏 10.05MB PDF 举报
The e-Traction PCM Integration Manual is a comprehensive guide for integrating the Control PCM 2.0 system into various applications. This manual, authored by the expert team at TheControl, covers all aspects of the integration process and serves as a valuable resource for developers and engineers working with e-Traction technology.
The manual begins with an overview of the Control PCM 2.0 system, detailing its key features and capabilities. It then provides step-by-step instructions for integrating the PCM into different types of vehicles, including electric buses, trucks, and other commercial vehicles. The manual covers all aspects of the integration process, from hardware installation to software configuration and testing.
One of the highlights of the manual is its detailed troubleshooting section, which provides solutions to common issues that may arise during the integration process. The manual also includes best practices and recommendations for optimizing the performance of the Control PCM 2.0 system, ensuring that users can get the most out of their e-Traction technology.
Throughout the manual, the authors emphasize the confidential and privileged nature of the information contained within. Readers are reminded that the document is intended for internal use only and should not be distributed or copied without prior authorization from e-Traction.
In conclusion, the e-Traction PCM Integration Manual is a valuable resource for developers and engineers working with the Control PCM 2.0 system. With its detailed instructions, troubleshooting tips, and best practices, this manual is essential reading for anyone looking to successfully integrate e-Traction technology into their vehicles.
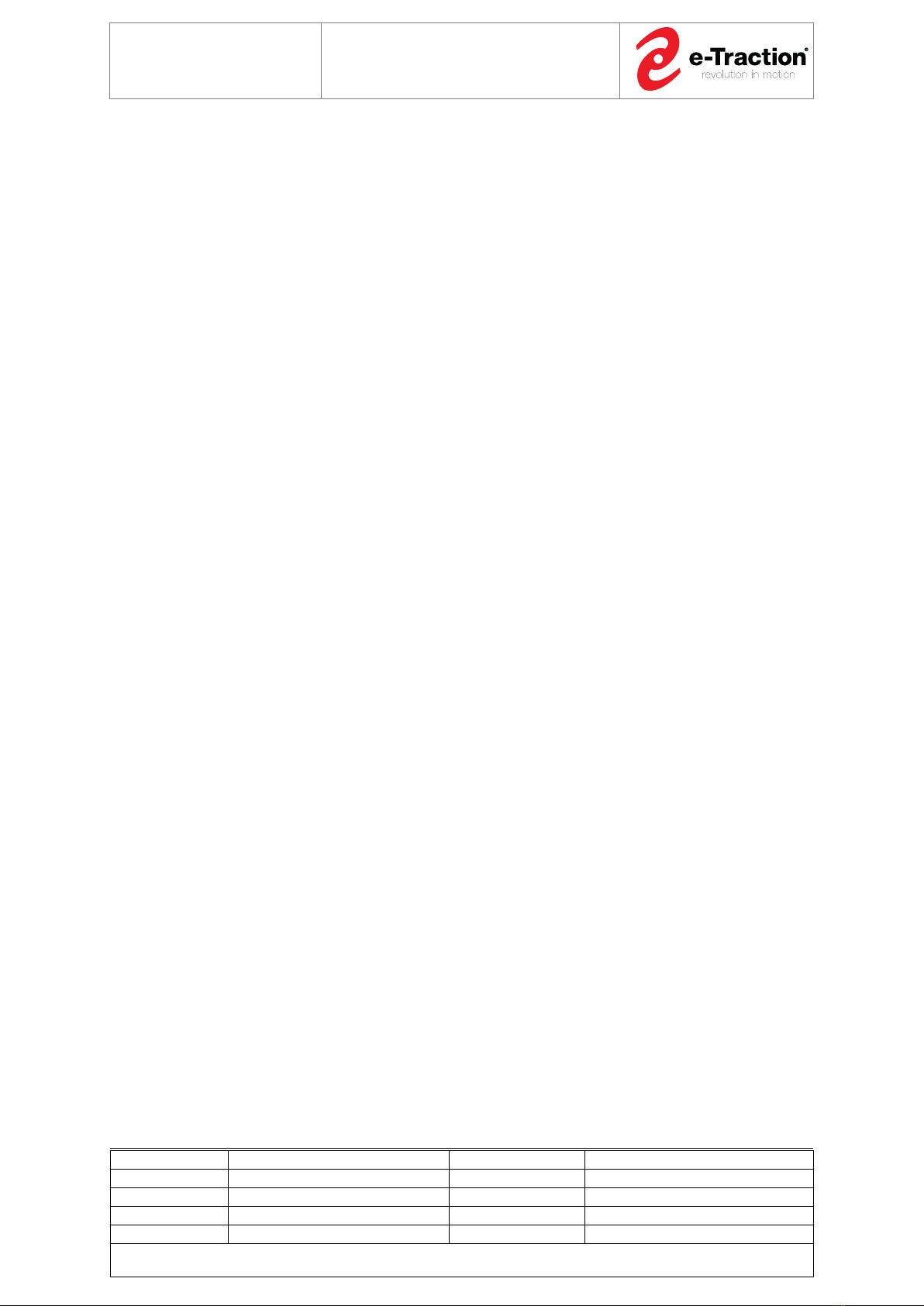
Integration Manual
TheControl PCM 2.0
Page 16 of 245
Author
TheControl Team
Date
2020-12-11
Project
TheControl PCM 2.0
Version
1.5
Document Name
TheControl PCM Integration Manual
Status
Draft
Classification
Confidential
Template Information
TMP_General_document rev63
Approved by
G. Kwintenberg
Approval Date
2020-12-11
All information contained in this document is confidential and privileged to e-Traction and may not be distributed or copied to any
person other than the addressee without prior written consent of © e-Traction Europe B.V.
If the EBS is not controlling the brake light when TheMotion is applying regenerative (electrical braking) the BCM shall activate
the brake light when requested by the Powertrain Control Module (PCM). The PCM will also inform the BCM about the
driveline status and the torque and mechanical power that is generated by the wheels of TheMotion system. See Body Control
Module (BCM) for the details of the integration between the BCM and PCM.
1.6.1.1 Human Machine Interface (HMI)
The Human Machine Interface (HMI) consists of a large display that is visible for the driver at all times. The information
regarding the status of the vehicle (health, warning or error information) is shown on this display or with separate LEDs close
to this display. Also, information such as the vehicle speed or actual torque can be shown here for the drivers’ information.
1.6.2 Drive Neutral Reverse (DNR) selector
The Drive Neutral Reverse (DNR) selector is a device, typically a button box or a rotary switch with at least three options:
Drive, Neutral and Reverse. The driver can select these options to request the vehicle to drive in forward, reverse or do not
generate any torque (neutral). The Powertrain Control Module (PCM) will validate if the request will be accepted based on
the actual vehicle speed, the position of the accelerator pedal and the position of the brake pedal or parking brake. The
Motion System supports CAN communication based DNR selectors. See DNR selector handling for the details of the
integration between the DNR selector and the PCM.
1.6.3 Electronic Braking System (EBS)
The Electronic Braking System (EBS) is in control of the pneumatic braking system which is controlled by the driver with the
brake pedal. The parking brake is also part of the input of the driver that is relevant for TheMotion system. The electrical
parts of the braking system regulate the pressures applied to the different brake discs of all wheels. The speed of all the
wheels is monitored with wheel speed sensors and in case the speed of one or more wheels decreases too much during
braking, the Anti-lock Braking System (ABS) of the EBS will become active. In case one or more driven wheel speeds increase
too much the Anti-Slip Regulation (ASR) of the EBS becomes active. In both cases will the EBS request a brake torque limit
(ABS) or a drive torque limit (ASR) to the retarder (ABS) or engine (ASR). Because TheMotion is responsible for both driving
and electrical braking both limits will be respected by TheMotion system. The Powertrain Control Module (PCM) monitors
both limits communicated via the CANbus interface and will limit the torque requests towards TheWheel if necessary. The
mechanical braking remains the complete responsibility of the EBS.
Brake-by-wire exists on heavy duty commercial vehicles under the name EBS. This system provides the electronic activation
of all braking system components including retarder and engine brake. The EBS also supports trailers and communicates
between the towing vehicle and trailer using the ISO 11992 protocol. EBS still relies on compressed air for braking and is only
controlling the air through valves which means that it is not depending on higher voltages used by the electromechanical or
electro-hydraulic brake systems where electric power also is used to apply the brake pressure. EBS enhances the precision of
the braking over conventional braking, which shortens the braking distance. The fall back of an EBS in case of failure is to use
the ordinary air brake control pressure, so even in the event of a failure of the electronics the vehicle shall be able to make a
safe stop. In modern versions the brake pedal position and brake pedal switch status are sent by the EBS.
The EBS communicates with TheMotion system by means of standardized CAN communication (SAE J1939). Since this
standard currently does not support hybrid/electric vehicles, Wabco offers this integration by means of proprietary
communication. TheMotion system is supporting this proprietary communication protocol. The interaction between the EBS
and TheMotion system is largely based on torque requests and torque limits. For example, in the case of an ASR event, the
EBS will request a limit on the drive torque to reduce the tire slip. In the case of an ABS event the EBS will request a torque
limit to reduce the amount of regenerative brake torque applied by TheMotion system to prevent lock-up of wheels.
The EBS can also be extended to support Electronic Stability Control (ESC). This means that the EBS will be extended with
additional sensors such as: Steering Angle Sensor (SAS), lateral acceleration and yaw rate sensor. See paragraph Integration
with the brake system for the details of the integration between the EBS and the PCM.
The EBS can also have additional functionalities like the hill holder functionality. The EBS will engage the brake when the
vehicle starts rolling in reverse.
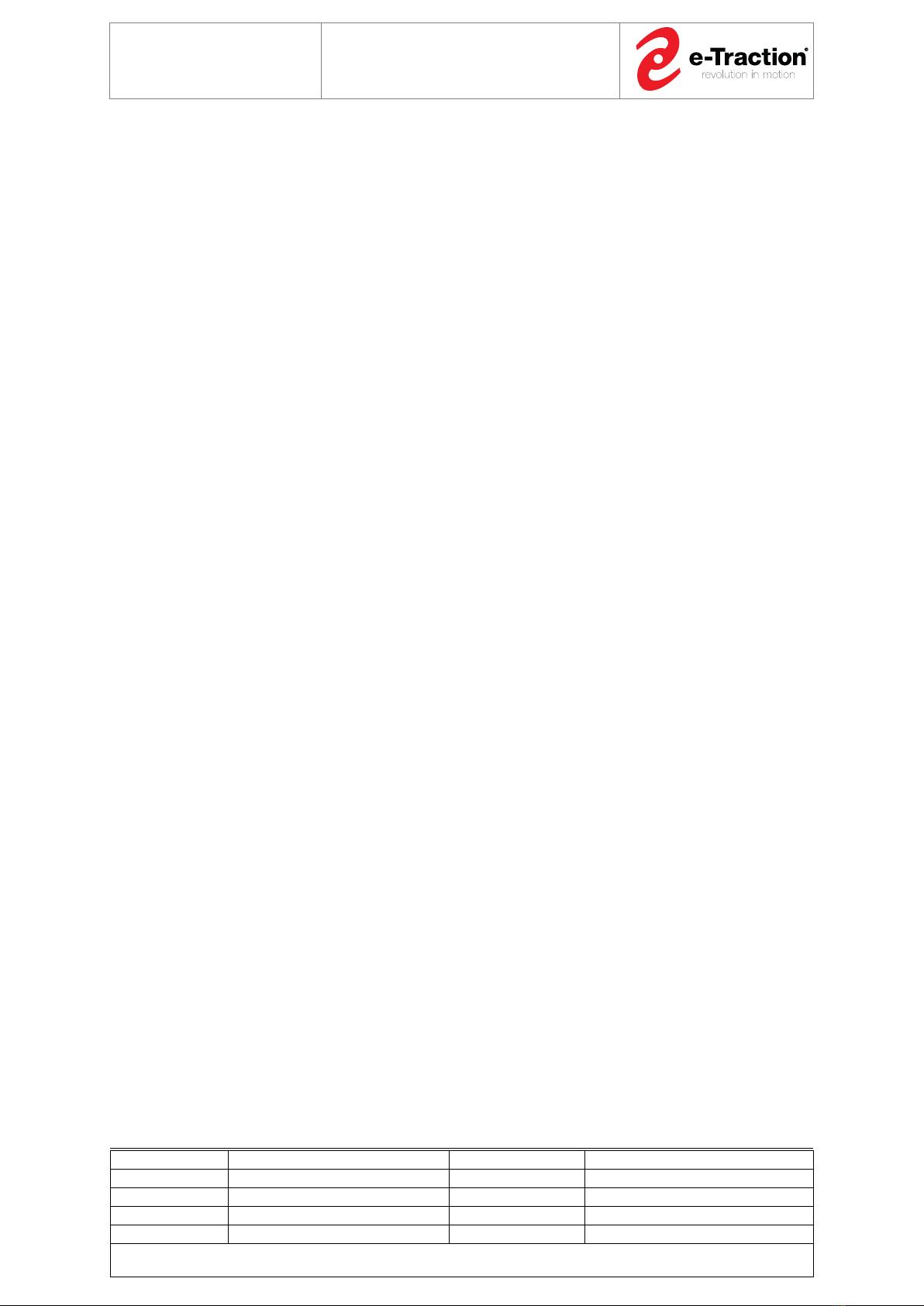
Integration Manual
TheControl PCM 2.0
Page 17 of 245
Author
TheControl Team
Date
2020-12-11
Project
TheControl PCM 2.0
Version
1.5
Document Name
TheControl PCM Integration Manual
Status
Draft
Classification
Confidential
Template Information
TMP_General_document rev63
Approved by
G. Kwintenberg
Approval Date
2020-12-11
All information contained in this document is confidential and privileged to e-Traction and may not be distributed or copied to any
person other than the addressee without prior written consent of © e-Traction Europe B.V.
1.6.4 Vehicle Energy Manager (VEM)
The Vehicle Energy Manager (VEM) is an Electronic Control Unit (ECU) that handles all functionality regarding the high voltage
system, battery charging, energy conversion, range-extender control and high voltage related safety systems. This component
informs the TheMotion system about the state of the high voltage system. Furthermore, it communicates the limits of the
Rechargeable Energy Storage System (REESS) in which TheMotion system is allowed to operate. These limits are the maximum
DC current the driveline is allowed to discharge and charge the REESS. For the exchange of data between the VEM and
TheMotion system proprietary CAN messages are defined. If the REESS is based on lithium technology then it typically
contains a Battery Management System (BMS). The VEM has direct interaction with the BMS for the exchange of status and
control information. See Interaction with energy management for the details of the integration between the VEM and the
PCM.
1.6.5 Electronically Controlled Air Suspension (ECAS)
The Electronically Controlled Air Suspension (ECAS) system is responsible for the following functionality: increased ride
comfort due to lower spring rate and lower natural frequency, maintaining a constant vehicle height irrespective of the
vehicle load, precise load-dependent activation of the brakes through use of the air bellows pressure a control pressure for
the proportioning valves of the brake system, kneeling function, which causes on side of the vehicle facilitate lower level
entry and exit.
The ECAS system receives a CAN message that is sent by TheMotion system to optimize its functions. In this message
TheMotion system reports actual speed of the vehicle and the signal that indicates if the brake pedal is pressed or not.
See Retrofit functionality for the details of the integration between the ECAS and the PCM.
1.6.6 Steering Angle Sensor (SAS)
As described in paragraph Electronic Braking System (EBS) the Steering Angle Sensor (SAS) is part of the EBS when Electronical
Stability Control (ESC) is installed on a vehicle. The SAS is used for determination of the wheel steering angles. The sensor is
mounted to the steering column of the vehicle and provides a measuring value for the absolute angle (position) of the steering
wheel. This includes the capability of identification of the steering wheel zero position (center position) by means of sensor
calibration. The wheel angles are an important input variable for the electric differential functionality that is part of
TheMotion system. This sensor is considered optional from the systems perspective but note that in this case the electric
differential functionality is not present. Therefore, if the EBS of the vehicle is not extended with ESC functionality, a SAS is
advised. See Steering wheel angle sensor handling for the details of the integration between the SAS and the PCM.
1.6.7 Tachograph
The tachograph is an optional external vehicle system. A tachograph is a device fitted to a vehicle that automatically records
its speed and driven distance, together with the driver's activity selected from a choice of modes. To the tachograph a sensor
is connected that measures the speed. Typically, this sensor is mounted to the vehicle gearbox. Since TheMotion system is
not equipped with a gearbox, the sensor is mounted on one of the wheels. The tachograph communicates its speed and
vehicle information on the vehicle CANbus. This information is used by TheMotion system for plausibility of other
vehicle/wheel speed sources. This plausibility is important for acquiring the right signal quality in terms of functional safety.
Furthermore, the tachograph also provides time and date information by means of the TD message. This time and date
information is used to time-stamp diagnostic information. Currently is the tachograph vehicle speed not used in the PCM.
1.6.8 Rechargeable Energy Storage System (REESS)
The REchargeable Energy Storage System (REESS) is typically a rechargeable high voltage battery which delivers the energy
for the vehicle. This battery is typically based on lithium technology and can be recharged using a charge system and by
energy recuperation during braking. In addition to this a range extender (e.g. diesel engine or fuel cell system) can also charge
this battery system.
The REESS shall at all times deliver at least 400 Vdc and shall not exceed 800 Vdc. The REESS is responsible for communicating
the actual voltage and the maximum discharge and charge currents to the Vehicle Energy Manager (VEM) so these can be
sent to the Powertrain Control Module (PCM). The REESS, typically monitored by a Battery Management System (BMS), is
responsible for sending the correct values to protect the REESS. TheMotion system is responsible for respecting these limits
to guarantee a safe and durable operation of the REESS.
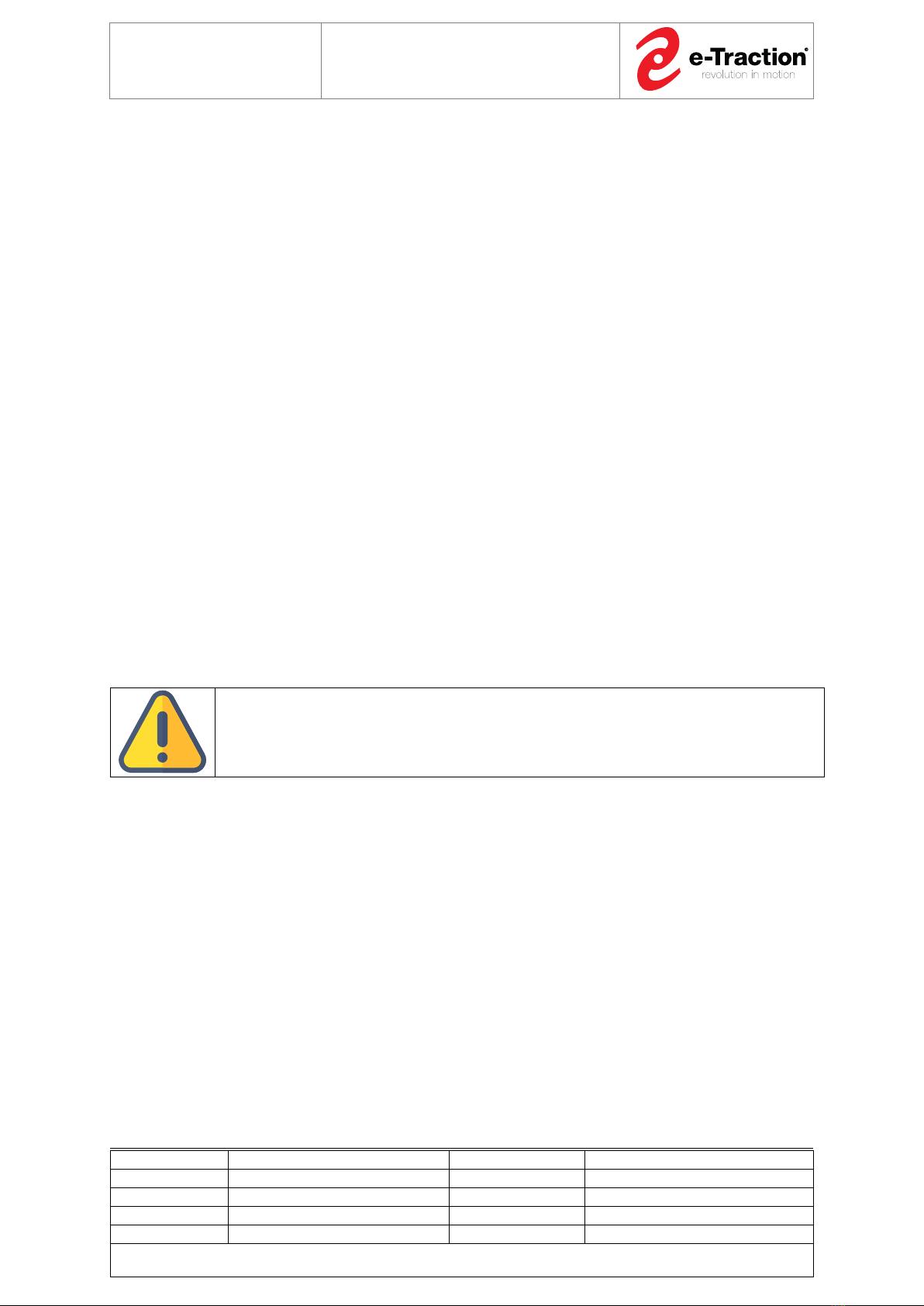
Integration Manual
TheControl PCM 2.0
Page 18 of 245
Author
TheControl Team
Date
2020-12-11
Project
TheControl PCM 2.0
Version
1.5
Document Name
TheControl PCM Integration Manual
Status
Draft
Classification
Confidential
Template Information
TMP_General_document rev63
Approved by
G. Kwintenberg
Approval Date
2020-12-11
All information contained in this document is confidential and privileged to e-Traction and may not be distributed or copied to any
person other than the addressee without prior written consent of © e-Traction Europe B.V.
1.6.9 Accelerator pedal
The accelerator pedal provides the main driver input to the TheMotion system. This component is connected by a hardwired
electrical connection for safety reasons. Furthermore, this connection is redundant such that a plausibility check can be
performed. The Powertrain Control Module (PCM) has calibration parameters which will make sure a wide range of
accelerator pedals is supported.
Typically, an accelerator pedal consists of a potentiometer which varies the electrical resistance. The PCM will supply the
voltage to this component and can determine the pedal position from (0 - 100 %) by reading the feedback voltage. In addition
to this, the accelerator pedal shall have a second channel which consists of a potentiometer or switch. This second channel
is also supplied by the PCM. With the feedback of this second channel the PCM can determine if the pedal press measured
on the first channel is plausible or not. If a wire would break or the system would make a mistake in the measurement this
will be detected and TheMotion system will disable the drive torque and send a Diagnostic Trouble Code (DTC).
See paragraph Accelerator pedal for the electrical integration of the accelerator pedal and paragraph Accelerator pedal
handing and Accelerator pedal percentage to torque mapping for the details of the integration between the accelerator pedal
and the PCM.
1.6.10 Cooling system
The cooling system is a liquid cooling system consisting of a radiator(s), water pump, cooling fan(s) and temperature sensor(s).
The coolant is typically a mix of glycol and water and is used to transfer the heat dissipated by TheWheel and TheDrive to the
radiator were this heat is exchanged with the ambient air around the vehicle. The coolant flow in the system should be at
least 30 l/min at the input of each TheWheel which should be maintained by the coolant pump controlled by the Body Control
Module (BCM). The maximum pressure to the coolant system is 2 bar measured at the input of each TheWheel. It is not
necessary to measure this pressure always but it should be checked during the commission of the vehicle.
The minimum coolant flow is necessary to guarantee the operation of TheMotion system within its specification including
the specified lifetime of the system. In addition to this, the coolant temperature should be regulated around 40 °C and be at
maximum 60 °C to make sure TheMotion system can deliver the specified power and torque. If the temperature is above 50
°C the driver should be informed by the Human Machine Interface (HMI) with a yellow warning indication of the coolant
temperature. If the temperature is above 60 °C the driver should be informed by the HMI with a red error indication of the
coolant temperature. This is also the responsibility of the Body Control Module (BCM). TheMotion system will continue to
operate but the performance will be limited.
A coolant system which is not able the deliver the required minimum coolant flow, regulate the
temperature or cannot provide the minimum coolant pressure, can lead to an incorrect and unsafe
operation of TheMotion system.
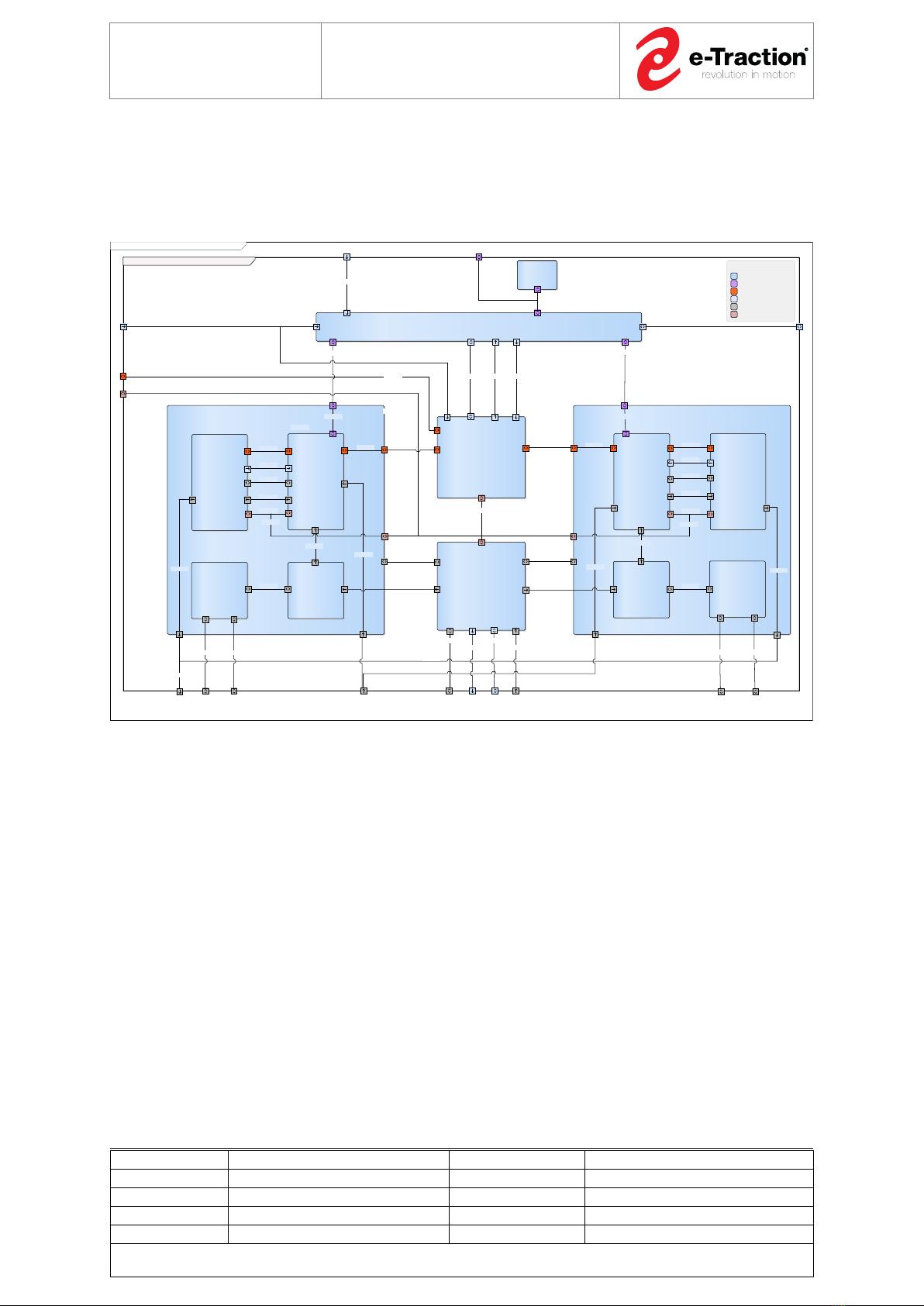
Integration Manual
TheControl PCM 2.0
Page 19 of 245
Author
TheControl Team
Date
2020-12-11
Project
TheControl PCM 2.0
Version
1.5
Document Name
TheControl PCM Integration Manual
Status
Draft
Classification
Confidential
Template Information
TMP_General_document rev63
Approved by
G. Kwintenberg
Approval Date
2020-12-11
All information contained in this document is confidential and privileged to e-Traction and may not be distributed or copied to any
person other than the addressee without prior written consent of © e-Traction Europe B.V.
1.7 TheMotion overview
TheMotion system is prepared for compatibility and to control up to 8 in-wheel motors. However, the current system that is
released is compatible and can support the control up to 4 in-wheel motors. The inside of TheMotion system, which was
drawn as a green block in the system overview in Figure 1, is shown in Figure 2. All e-Traction components are drawn as blue
blocks in the figure below and the color of the interfaces distinguishes the interfaces between CAN communication (purple),
high voltage (orange), potential equalization (brown), low voltage (light blue) and mechanical interfaces (gray). The interfaces
that are shown on the outside of this figure match with the interfaces to the vehicle system of Figure 1.
Figure 2: TheMotion system overview with one driven axle
The figure shows the following e-Traction components: the Powertrain Control Module (PCM), the Power Distribution Unit
(PDU), TheWheel, TheDrive, the Sub-frame and E-Traction Diagnostic Service Application (EDiSA). A short description of all
the components in TheMotion system is written below. In Figure 2 the system is shown when the system consists of two in-
wheel motors (one driven axle). When more in-wheel motors are used in the system more connections are used.
ibd [block] TheMotion 2-Wheel [TheMotion (Complete Overview)]
HV DC
Supply
AcceleratorPedal
LV
Control
LV
Supply
CAN
Coola nt
In
Coola nt
Out
Ground
Sub-
Frame
Mount
EBS
Pneumatics
LV EBS
Sensors
Tachograph
SpeedSensor
Left Inner
Tyre
Mount
Left Outer
Tyre
Mount
Right
Inner Tyre
Mount
Right
Outer Tyre
Mount
ibd [block] TheMotion 2-Wheel [TheMotion (Complete Overview)]
HV DC
Supply
AcceleratorPedal
LV
Control
LV
Supply
CAN
Coola nt
In
Coola nt
Out
Ground
Sub-
Frame
Mount
EBS
Pneumatics
LV EBS
Sensors
Tachograph
SpeedSensor
Left Inner
Tyre
Mount
Left Outer
Tyre
Mount
Right
Inner Tyre
Mount
Right
Outer Tyre
Mount
CAN
EDiSA
CAN
HV
DCLink
Set 2
HV
DCLink
Set 1
Ground
LV
Control
LV
Supply
HV DC
Supply
LV
Feedback
HVIL
PDU1
HV
DCLink
Set 2
HV
DCLink
Set 1
Ground
LV
Control
LV
Supply
HV DC
Supply
LV
Feedback
HVIL
CAN1
CAN2
CAN3
LV
Supply
LV
Control
LV PDU
Control
AcceleratorPedal
PDU
HVIL
LV PDU
Feedback
PCM
CAN1
CAN2
CAN3
LV
Supply
LV
Control
LV PDU
Control
AcceleratorPedal
PDU
HVIL
LV PDU
Feedback
Wheel
Mount Left
Ground
Wheel
Mount Right
Sub-
Frame
Mount
Mechanical
Brake Left
Mechanical
Brake
Right
Tachograph
Speed
Sensor
LV EBS
Sensors
EBS
Pneumatics
TheWheel Sub-Frame
Wheel
Mount Left
Ground
Wheel
Mount Right
Sub-
Frame
Mount
Mechanical
Brake Left
Mechanical
Brake
Right
Tachograph
Speed
Sensor
LV EBS
Sensors
EBS
Pneumatics
Ground
Mechanical
Mount
Coola nt
Input
Coola nt
Output
CAN
HV DC
Supply
Right: TheWheel
Ground
Mechanical
Mount
Coola nt
Input
Coola nt
Output
CAN
HV DC
Supply
Ground
Mechanical
Mount
Coola nt
Input
Coola nt
Output
CAN
HV DC
Supply
Left: TheWheel
Ground
Mechanical
Mount
Coola nt
Input
Coola nt
Output
CAN
HV DC
Supply
Angle Sensor
Rotor
Rim
Mount
Mechanical
Brake
Rotor
Angle Sensor
Rotor
Rim
Mount
Mechanical
Brake
Coola nt
In
Coola nt
Out
HV 3-Phase
AC
Temperature
Sensors
TheDrive
Mount
Ground
Stator
Coola nt
In
Coola nt
Out
HV 3-Phase
AC
Temperature
Sensors
TheDrive
Mount
Ground
Angle Sensor
Stator
CAN
Coola nt
In
Coola nt
Out
Ground
HV 3-Phase
AC
HV DC
Supply
Mechanical
Mount
Temperature
Sensors
TheDrive
Angle Sensor
Stator
CAN
Coola nt
In
Coola nt
Out
Ground
HV 3-Phase
AC
HV DC
Supply
Mechanical
Mount
Temperature
Sensors
Angle Sensor
Rotor
Rim
Mount
Mechanical
Brake
Rotor
Angle Sensor
Rotor
Rim
Mount
Mechanical
Brake
Coola nt
In
Coola nt
Out
HV 3-Phase
AC
Temperature
Sensors
TheDrive
Mount
Ground
Stator
Coola nt
In
Coola nt
Out
HV 3-Phase
AC
Temperature
Sensors
TheDrive
Mount
Ground
Angle Sensor
Stator
CAN
Coola nt
In
Coola nt
Out
Ground
HV 3-Phase
AC
HV DC
Supply
Mechanical
Mount
Temperature
Sensors
TheDrive
Angle Sensor
Stator
CAN
Coola nt
In
Coola nt
Out
Ground
HV 3-Phase
AC
HV DC
Supply
Mechanical
Mount
Temperature
Sensors
E-Traction Component
Communication Port
High Volta ge Port
Low Volta ge Port
Mechanical Port
Potential Equalization Port
Legend
Mechanical
Mount
Inner
Tyre
Mount
Outer
Tyre
Mount
Rim Assembly
Mechanical
Mount
Inner
Tyre
Mount
Outer
Tyre
Mount
Mechanical
Mount
Inner
Tyre
Mount
Outer
Tyre
Mount
Rim Assembly
Mechanical
Mount
Inner
Tyre
Mount
Outer
Tyre
Mount
SYS_IF_25
SYS_IF_28
SYS_IF_27
SYS_IF_26
SYS_IF_11
SYS_IF_35
SYS_IF_02
SYS_IF_09
SYS_IF_08
SYS_IF_07
SYS_IF_26
SYS_IF_05
SYS_IF_32
SYS_IF_10
SYS_IF_09
SYS_IF_13
SYS_IF_27
SYS_IF_23
SYS_IF_24
SYS_IF_33
SYS_IF_21
SYS_IF_01
SYS_IF_22
SYS_IF_18
SYS_IF_38
SYS_IF_24
SYS_IF_06
SYS_IF_10
SYS_IF_19
SYS_IF_38
SYS_IF_12
SYS_IF_25
SYS_IF_21
SYS_IF_41
SYS_IF_20
SYS_IF_36
SYS_IF_04
SYS_IF_16
SYS_IF_29
SYS_IF_07
SYS_IF_33
SYS_IF_22
SYS_IF_41
SYS_IF_03
SYS_IF_32
SYS_IF_39
SYS_IF_37
SYS_IF_04
SYS_IF_13
SYS_IF_08
SYS_IF_33
SYS_IF_34
SYS_IF_28
SYS_IF_17
SYS_IF_33
SYS_IF_23
SYS_IF_06
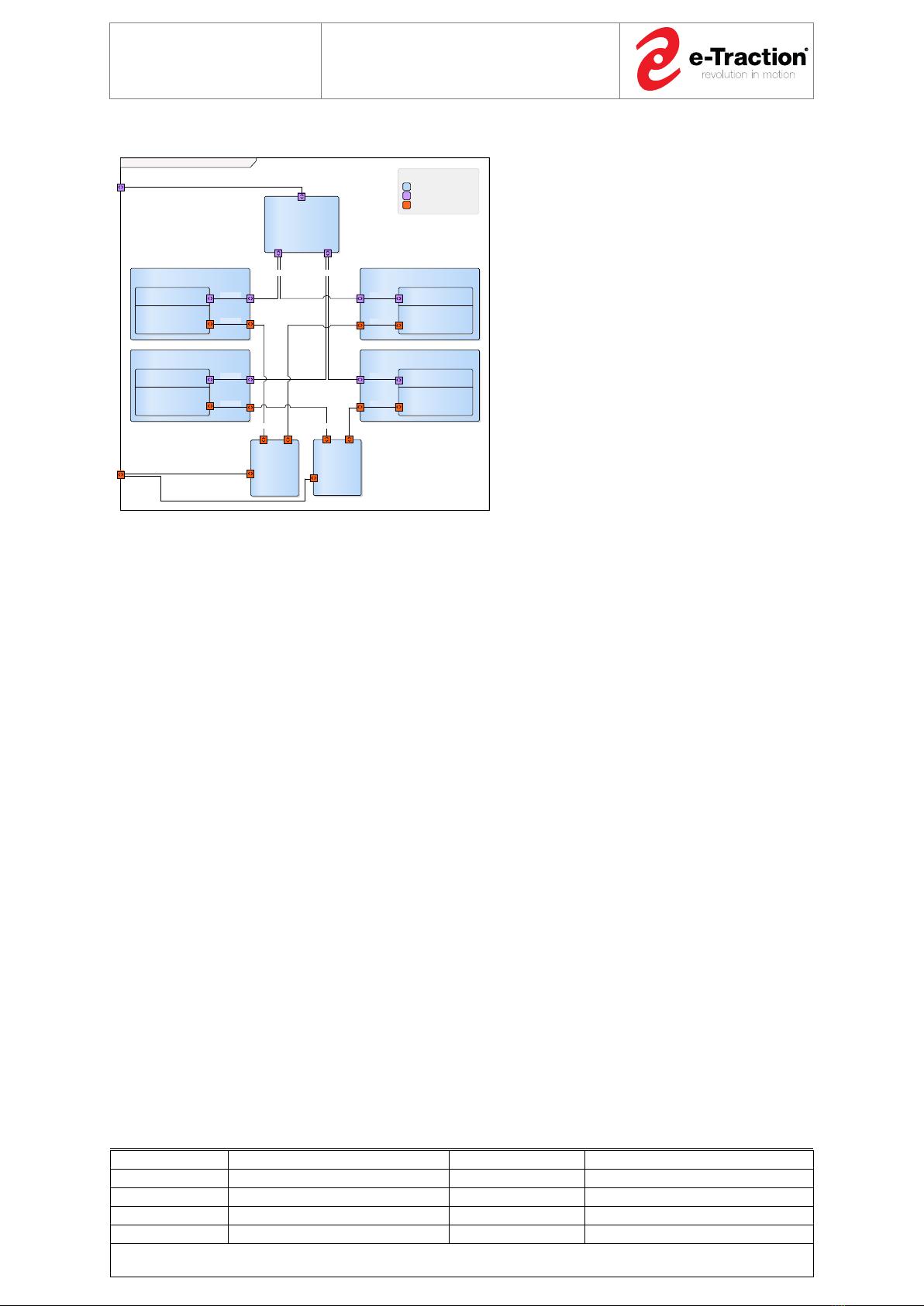
Integration Manual
TheControl PCM 2.0
Page 20 of 245
Author
TheControl Team
Date
2020-12-11
Project
TheControl PCM 2.0
Version
1.5
Document Name
TheControl PCM Integration Manual
Status
Draft
Classification
Confidential
Template Information
TMP_General_document rev63
Approved by
G. Kwintenberg
Approval Date
2020-12-11
All information contained in this document is confidential and privileged to e-Traction and may not be distributed or copied to any
person other than the addressee without prior written consent of © e-Traction Europe B.V.
When the system consists of two driven axles, two PDUs are implemented in the system. The schematics of the CAN and HV
connections between these components and the four driven wheels are shown in Figure 3.
Figure 3: TheMotion simplified system overview with two driven axles
1.7.1 Powertrain Control Module (PCM)
The Powertrain Control Module (PCM) is responsible for all driveline related functionality such as: torque control of the
TheWheel, brake system interaction, protection and limitation and detection and control of safety hazards, dynamic speed
limiting, cruise control and the electric differential. The PCM has CANbus interfaces with the vehicle systems and in
TheMotion system with TheWheel. The PCM has low voltage electrical interfaces with the vehicle and the Power Distribution
Unit (PDU).
1.7.2 Power Distribution Unit (PDU)
The Power Distribution Unit (PDU) distributes the high voltage from the Rechargeable Energy Storage System (REESS) to
TheWheel. It has a redundant connection to the wheels in case of one driven axle to the REESS to make sure that if one wheel
or HV component fails the vehicle can continue to operate. In case of two driven axles the redundancy is guaranteed per PDU.
The PDU is controlled and monitored by the Powertrain Control Module (PCM).
The PDU consists of four contactors: two main and two pre-charge contactors. It also contains two HV fuses and two pre-
charge resistors. The HV cables from the REESS can be connected with two connectors, one for battery plus and one for
battery minus. There are two connectors to connect the PDU to two wheels, these connectors have a combined plus and
minus.
If a vehicle has four driven wheels (two driven axles), two identical PDUs are used to connected the four wheels to the REESS
and the PCM. It is also possible to have alternative PDU configurations if this is a demand of the customer.
1.7.3 TheWheel
TheWheel is the In-Wheel Motor (IWM), which is a Permanent Magnet Synchronous Machine (PMSM) with an outer rotor.
The stator is fixed to the Sub-frame and the rotor is connected to the rim which is connected to the tire. This means all
electrical machines directly drive the vehicle without any transmission. The power electronics, called TheDrive, is also
mounted inside TheWheel. This means TheWheel only has a CANbus interface with the Powertrain Control Module (PCM), a
high voltage interface with the Power Distribution Unit (PDU) and a cooling circuit interface with the vehicles Cooling system.
The cooling of the electric machine and the power electronics inside TheDrive are shared. Currently 2 or 4 TheWheels on one
vehicle are supported by the PCM. To make a distinction between the different TheWheel components a number is used. The
wheel number x can vary from 1 to 4. The allocation of wheel number x with respect to the location of the vehicle is as follows:
- Uneven wheel numbers are always located on the left side of the vehicle.
- Even wheel numbers are always located on the right side of the vehicle.
- The wheel numbers are enumerated in a vehicle front to rear pattern.
CAN
HV DC Supply
ibd [block] TheMotion 4-Wheel [TheMotion (CAN + HV Overview)]
CAN
HV DC Supply
CAN1
CAN2
CAN3
PCM
CAN1
CAN2
CAN3
CAN
HV DC Supply
Rear Right: TheWheel
CAN
HV DC Supply
CAN
HV DC Supply
Rear Left: TheWheel
CAN
HV DC Supply
CAN
HV DC Supply
Front Right: TheWheel
CAN
HV DC Supply
CAN
HV DC Supply
Front Left: TheWheel
CAN
HV DC Supply
CAN
HV DC Supply
TheDrive
tags
CAN ID = SA_TD1
CAN Terminator = 120 [ohm]
CAN
HV DC Supply
CAN
HV DC Supply
TheDrive
tags
CAN ID = SA_TD2
CAN Terminator = 120 [ohm]
CAN
HV DC Supply
CAN
HV DC Supply
TheDrive
tags
CAN ID = SA_TD3
CAN Terminator = 120 [ohm]
CAN
HV DC Supply
CAN
HV DC Supply
TheDrive
tags
CAN ID = SA_TD4
CAN Terminator = 120 [ohm]
CAN
HV DC Supply
E-Traction Component
Communication Port
High Voltage Port
Legend
HV DC Supply
HV
DCLink
Set 1
HV
DCLink
Set 2
PDU1
HV DC Supply
HV
DCLink
Set 1
HV
DCLink
Set 2
HV
DCLink
Set 2
HV
DCLink
Set 1
HV DC Supply
PDU2
HV
DCLink
Set 2
HV
DCLink
Set 1
HV DC Supply
SYS_IF_07
SYS_IF_06
SYS_IF_07
SYS_IF_02
SYS_IF_05
SYS_IF_04
SYS_IF_03
SYS_IF_04
SYS_IF_07
SYS_IF_06
SYS_IF_04 SYS_IF_04
SYS_IF_01
SYS_IF_07
剩余244页未读,继续阅读
2022-07-15 上传
2021-05-28 上传
2021-05-17 上传
2021-03-09 上传
2022-02-17 上传
2021-03-29 上传
2021-05-26 上传

lixiaobin091826
- 粉丝: 3
- 资源: 12
上传资源 快速赚钱
我的内容管理 展开
我的资源 快来上传第一个资源
我的收益
登录查看自己的收益我的积分 登录查看自己的积分
我的C币 登录后查看C币余额
我的收藏
我的下载
下载帮助

最新资源
- JHU荣誉单变量微积分课程教案介绍
- Naruto爱好者必备CLI测试应用
- Android应用显示Ignaz-Taschner-Gymnasium取消课程概览
- ASP学生信息档案管理系统毕业设计及完整源码
- Java商城源码解析:酒店管理系统快速开发指南
- 构建可解析文本框:.NET 3.5中实现文本解析与验证
- Java语言打造任天堂红白机模拟器—nes4j解析
- 基于Hadoop和Hive的网络流量分析工具介绍
- Unity实现帝国象棋:从游戏到复刻
- WordPress文档嵌入插件:无需浏览器插件即可上传和显示文档
- Android开源项目精选:优秀项目篇
- 黑色设计商务酷站模板 - 网站构建新选择
- Rollup插件去除JS文件横幅:横扫许可证头
- AngularDart中Hammock服务的使用与REST API集成
- 开源AVR编程器:高效、低成本的微控制器编程解决方案
- Anya Keller 图片组合的开发部署记录
安全验证
文档复制为VIP权益,开通VIP直接复制
