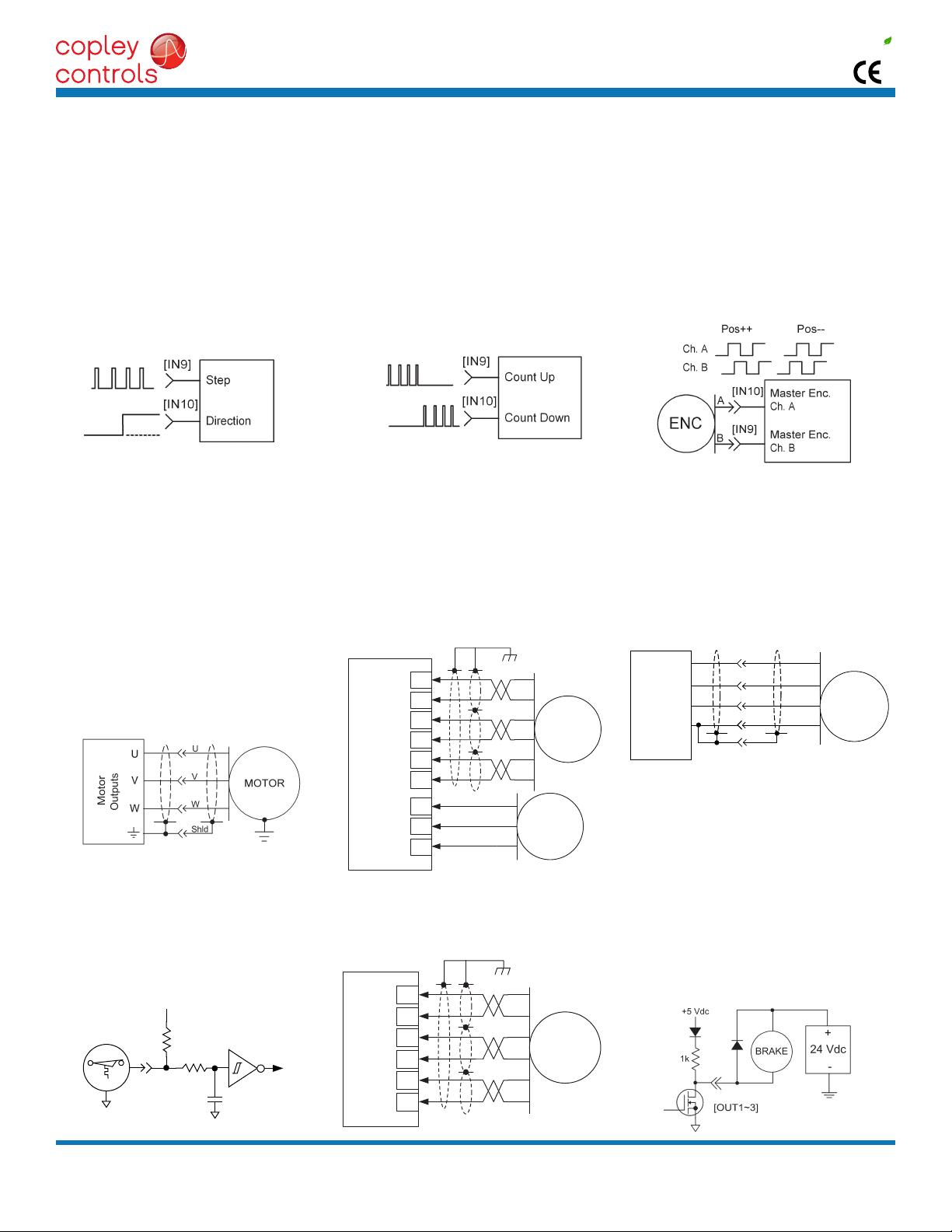
10 k
2.2 nF
74HC14
4.99k
[IN5]
+5V
19
Hall W
20Hall V
17
Hall U
22
Encoder /X
21Encoder X
24
Encoder /B
23Encoder B
25Encoder A
26Encoder /A
HALLS
U
V
W
Encoder
Motor
A
/A
B
/B
X
/X
22
Ref(-)
21Ref(+)
24
Cos(-)
23Cos(+)
25Sin(+)
26Sin(-)
Resolver
Motor
S3
S1
S2
S4
R1
R2
SECONDARY
ENCODER
Gnd
Gnd
A
+
[IN7]
B
+
[IN8]
+
5
V
d
c
+5 V
Accelnet
Micro Module
RoHS
ACK
Copley Controls, 20 Dan Road, Canton, MA 02021, USA Tel: 781-828-8090 Fax: 781-828-6547
P/N 16-01646 Rev 01 Page 5 of 25
STAND-ALONE MODE DIGITAL POSITION-CONTROL INPUTS
Accelnet Micro Module works with motion controllers that output pulses to command position.
These formats are supported:
Step/Direction
CU/CD
A/B Quadrature Encoder
In Step/Direction mode, a pulse-train controls motor position, and the direction is controlled by a DC level at the Direction input.
CU/CD (Count-Up/Count-Down) signals command the motor to move CW or CCW depending on which input the pulse-train is directed to. The motor can
also be operated in an electronic gearing mode by connecting the inputs to a quadrature encoder on another motor. In all cases the ratio between input
pulses and motor revolutions is programmable.
STEP/DIRECTION INPUTS COUNT-UP/COUNT-DOWN INPUTS QUAD A/B ENCODER INPUTS
MOTOR PHASE CONNECTIONS
The drive output is a dual H-bridge that converts
the DC buss voltage (+HV) into sinusoidal voltage
waveforms that drive the motor phases. Cable
should be sized for the continuous current rating
of the drive. Motor cabling should use twisted,
shielded conductors for CE compliance, and to
minimize PWM noise coupling into other circuits.
MOTOR CONNECTIONS
Motor connections are of ve types: phase, Halls, temperature sensor, encoder and resolver (option). The phase connections carry the drive output currents
that drive the motor to produce motion. The Hall signals are three digital signals that give absolute position feedback within an electrical commutation
cycle. A temperature sensor can shut down the drive to protect the motor from over-heating. The encoder and resolver signals give incremental position
feedback and are used for velocity and position modes, as well as sinusoidal commutation.
MOTOR ENCODER
Six dedicated inputs accept the encoder A, B,
and X (index) signals. Encoders with differential
outputs must be used.
MOTOR RESOLVER (-R option)
Resolvers use only six connections and do not
need +5V.
MOTOR TEMPERATURE SENSOR
Digital input [IN5] is programmable for use with a
motor overtemperature switch. The input should
be programmed as a pull-up to +5 Vdc if the motor
switch is grounded.
MOTOR BRAKE
Digital outputs [OUT1,2,3] can be programmed to
power a motor-mounted brake. These brake the
motor when they are in an unpowered state and
must have power applied to release. This provides
a fail-safe function that prevents motor motion
if the system is in an unpowered (uncontrolled)
state. Because brakes are inductive loads, an
external yback diode must be used to control the
coil voltage when power is removed. The timing
of the brake is programmable.
SECONDARY ENCODER
Inputs [IN7] & [IN8] accept the encoder A and B
signals. Encoders with single-ended active outputs
must be used.