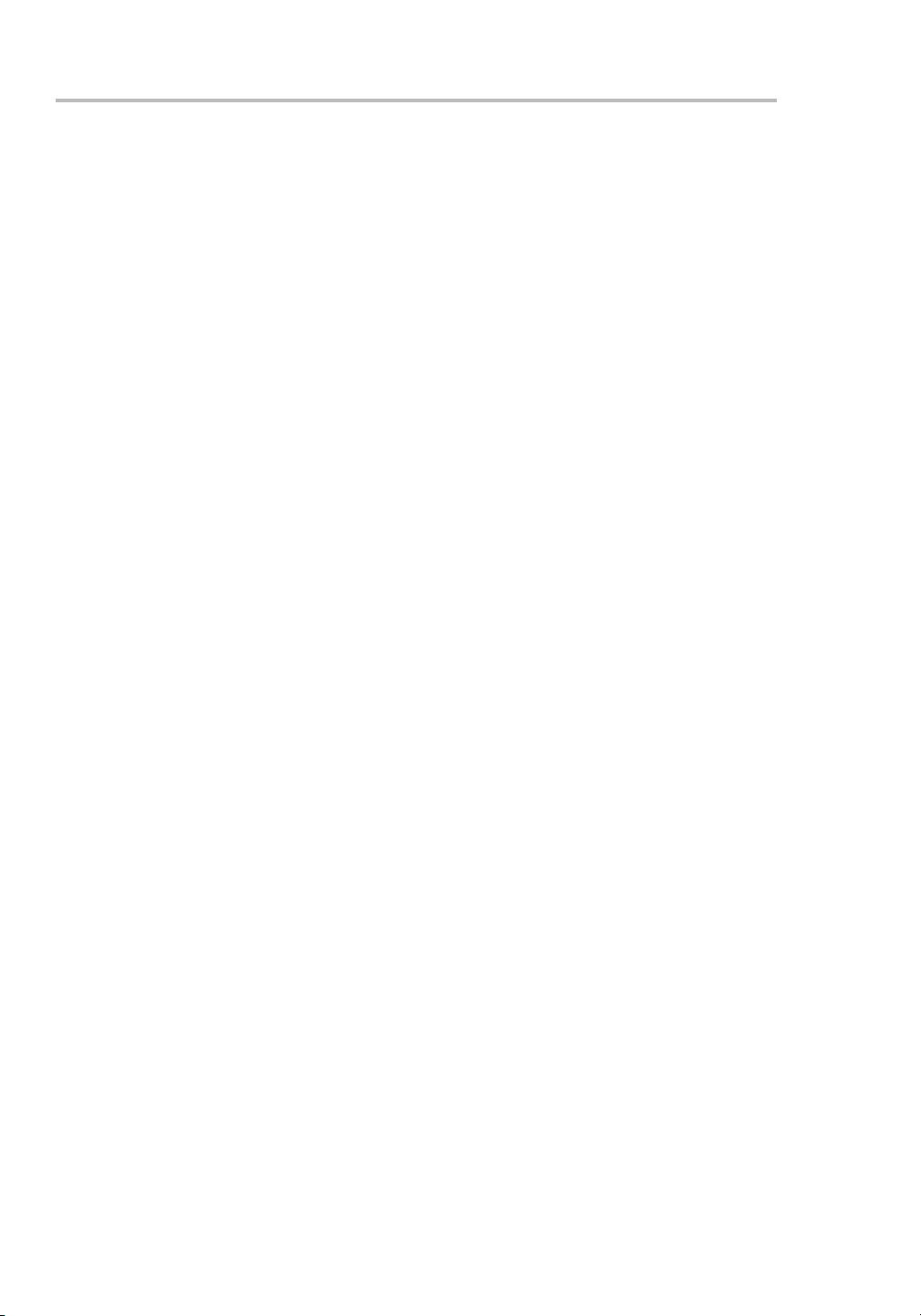
2 Introduction
known about early applications. This is even more remarkable given that most
of the ingredients for building acceleration and angular-rate sensors, such as fine
mechanics and precise spring technologies, were available from the late Middle
Ages on and were used in the construction of, for instance, beautiful precision
clocks.
Accelerometers
One of the most likely reasons for the late appearance of acceleration sensors (or
“accelerometers” for short) was the lack of indicator technologies, or, in modern
phrasing, the lack of interfaces. This is certainly the reason why some former
applications of acceleration switches that needed only very simple mechanical
interfaces can be found. An acceleration switch initiated an action at a certain
level of acceleration, as in the activation of a detonator in some bombs during
the First World War.
The first commercial accelerometer for broader application is credited to B.
McCollum and O. S. Peters and was developed around 1920 [
McCullom and
Peters 1924
]. It was based on a tension–compression resistance of a Wheatstone
half-bridge where the resistances were formed by carbon rings. The next techno-
logical step was the use of strain-gauge transducers starting from around 1938,
followed by the introduction of piezoelectric and piezoresistive transducers at
the end of the 1940s. These transducers could capture the forces caused by the
displacement of an elastically mounted mass within the sensor structure. Minia-
turization and the high robustness of this type of sensor paved the way for broad
applications in industry, terrestrial transport, aerospace, military uses, seismol-
ogy, science, and so on. The piezoelectric and piezoresistive transducer principles
were also among the first to be employed at the beginning of the entry into the
world of inertial microelectromechanical systems (MEMS) – the world of the
combination of micrometer- and nanometer-scale mechanical elements, sensors,
actuators, and electronic circuits on one carrier or even on one chip. This entry
was prepared in the late 1970s, for instance with the demonstration of a batch-
fabricated silicon accelerometer with piezoresistive transducers. The silicon bulk
micromachined proof mass was bonded between two glass wafers [
Roylance and
Angell 1979
]. The commercialization of similar devices began around 10 years
later and was very soon based on a variety of available transducer principles such
as the sensing of capacitance changes between fixed and movable plates, the fre-
quency measurement of resonant devices, the stabilization of a tunneling current
by a closed-loop system, the sensing of thermal changes between a heater and a
movable heat sink, and the sensing of changes of the thermal distribution within
an air bubble. This broad invasion of new and old ideas in the world of micro-
electronic technologies has opened the way to inexpensive mass applications of
inertial sensors in industry, cars, medicine, consumer goods, and so on.
Everybody knows the pioneering role of MEMS-based 50g accelerometers used
in airbag ignition devices, which became the first high-volume product in the area
of inertial MEMS. It was especially encouraging that within these successful high-
volume products an example of the full monolithic integration of sensor and