工厂布局优化:计算综合接近程度与选址策略

"如何计算综合接近程度-工廠布局合理化"
在工厂数字化和智能化转型的过程中,工厂布局合理化是至关重要的一步。合理的布局能够优化生产流程,提高效率,降低成本,确保产品质量,以及更好地适应市场需求。计算综合接近程度是评估工厂内部各个部门或作业单位之间关系紧密程度的一种方法,它有助于制定更有效的生产线和物流系统。
在描述中提到的"综合接近程度排序表",是通过将作业单位的相互关系量化,形成一个类似从至表的三角矩阵。这个矩阵展示了不同作业单位之间的关联强度,例如原材料库与铸造车间的关系为1229.8,这代表了它们之间的相互依赖程度。每个数值反映了在生产流程中,一个单位对另一个单位的影响,或者它们之间的距离、物流成本等因素。
工厂选址是布局优化的起点,遵循一系列原则,如最低成本原则、专业化分工原则等。在选择厂址时,需要考虑多方面因素,包括但不限于运输成本、原料供应、动力和能源成本、水和劳动力成本,以及非成本因素如社区环境、政治稳定性、扩展机会等。在评估这些因素时,可以采用多种分析方法,如优缺点比较法、加权因素法、因次分析法、重心法和线性规划中的运输法。
优缺点比较法是将不同因素列出来,对每个候选地点进行评分,以确定哪个地点总体上最有利。而加权因素法则是在考虑因素的重要性差异时,为每个因素赋予权重,并根据等级赋值,计算出每个方案的总得分,从而选出最优的厂址。
工厂内部的生产线布置和物流系统设计同样重要。生产线布置应考虑生产线的连续性和平衡性,以减少浪费和提高效率。物流系统设计则需优化物料流动路径,降低搬运成本,保证生产顺畅。仓储系统设计则需要确保库存管理的有效性,以支持生产活动并减少库存积压。
计算综合接近程度是工厂布局合理化的关键工具之一,它与选址、生产线布置、物流和仓储系统设计共同构成了工厂高效运作的基础。通过对这些方面的深入理解和优化,企业可以实现智能制造和工厂规划的目标,提高生产效率,降低成本,增强竞争力。
2021-12-07 上传
2021-10-11 上传
2021-11-06 上传
2022-03-15 上传
2022-11-24 上传
2022-06-29 上传
2021-08-07 上传
2300 浏览量
点击了解资源详情
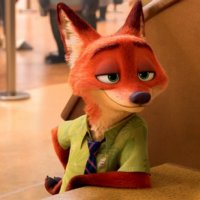
魔屋
- 粉丝: 26
- 资源: 2万+
最新资源
- 易语言36键MIDI电子琴
- bl1nd:我的 Ludum Dare 28 参赛作品的延续
- parallel_ASKI_并行计算_六面体协调网格;_模拟声学;_entirelyht3_网格_
- 简历
- Microsoft-Film-Industry-Analysis:文件,Jupyter笔记本和演示幻灯片,供我们分析有助于电影在熨斗学院取得成功的因素
- Eldinho2.github.io
- 作品答辩扁平化模板论文答辩.ppt.rar
- spree_advanced_cart:对 Spree 更有用的购物车实现
- nativescript-snapkit:使用Snapchat帐户登录到您的应用
- 易语言API录音
- 编程珠玑 第2版(修订版)_编程珠玑修订_资料_
- DataAnalytics
- robot_ws:这是机器人上的主要工作空间
- PeopleLung.fg7wzky7dm.ga4AST6
- svnautobuild-开源
- component-template-issue