掌握计算极差图控制限:SPC入门与实例
需积分: 44 7 浏览量
更新于2024-07-11
收藏 2.93MB PPT 举报
本讲义围绕计算极差图控制限展开,讲解了统计过程控制(SPC)在质量管理中的应用,特别是针对如何通过SPC来改进生产过程、降低客户投诉、报废率等质量问题。首先,我们回顾了质量管理的发展历程,从操作人员的实践到独立检验部的设立,再到统计技术的引入和ISO 9000标准的制定,以及TQM和Six Sigma的兴起,这些都是为了更有效地实施SPC。
SPC的核心在于监控过程的变差,变差是指在程序中单个项目或输出之间不可避免的差异,分为普通原因和特殊原因。变差的例子包括操作变化、机器故障、仪器误差和产品质量特性变化。通过绘制质量特性的直方图,可以观察数据分布,识别出控制限(CL,上控制限UCL和下控制限LCL),通常使用3σ原则,即大约99.73%的数据应该落在平均值±3倍的标准差范围内,这被称为正常区(Zone 1和Zone 2),超出此范围的异常值可能指示过程不稳定或存在特殊原因影响。
在实施SPC的过程中,我们关注以下几个关键概念:
1. **测量**:精确度和一致性是衡量变差的重要手段,测量的准确性直接影响控制限的设定。
2. **总体与样本**:总体是研究对象的所有数据,样本则是从中抽取的部分,用于分析和推断总体特征。
3. **基本统计术语**:如平均值(μ或x),它是数值的集中趋势;方差(σ或S),它衡量数据分散程度。样本方差S是估计总体方差σ的一种方法。
通过这些概念,我们可以计算控制限,例如UCL = D + 3R和LCL = D - 3R,其中D是过程的平均值,R是过程的公差(一般取3σ)。控制限的设定有助于识别过程的稳定性,从而采取必要的纠正措施,确保产品质量满足客户要求,并避免仅依赖于改良声明,而应展示过程数据和经过审计的结果。
总结来说,计算极差图控制限是统计过程控制的核心步骤之一,通过监测和理解变差及其来源,企业能够提高生产效率,减少质量问题,满足客户期望,实现持续改进。
2021-09-23 上传
2021-09-23 上传
2021-09-22 上传
2009-12-02 上传
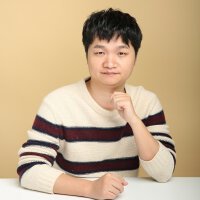
韩大人的指尖记录
- 粉丝: 30
- 资源: 2万+
最新资源
- 高清艺术文字图标资源,PNG和ICO格式免费下载
- mui框架HTML5应用界面组件使用示例教程
- Vue.js开发利器:chrome-vue-devtools插件解析
- 掌握ElectronBrowserJS:打造跨平台电子应用
- 前端导师教程:构建与部署社交证明页面
- Java多线程与线程安全在断点续传中的实现
- 免Root一键卸载安卓预装应用教程
- 易语言实现高级表格滚动条完美控制技巧
- 超声波测距尺的源码实现
- 数据可视化与交互:构建易用的数据界面
- 实现Discourse外聘回复自动标记的简易插件
- 链表的头插法与尾插法实现及长度计算
- Playwright与Typescript及Mocha集成:自动化UI测试实践指南
- 128x128像素线性工具图标下载集合
- 易语言安装包程序增强版:智能导入与重复库过滤
- 利用AJAX与Spotify API在Google地图中探索世界音乐排行榜