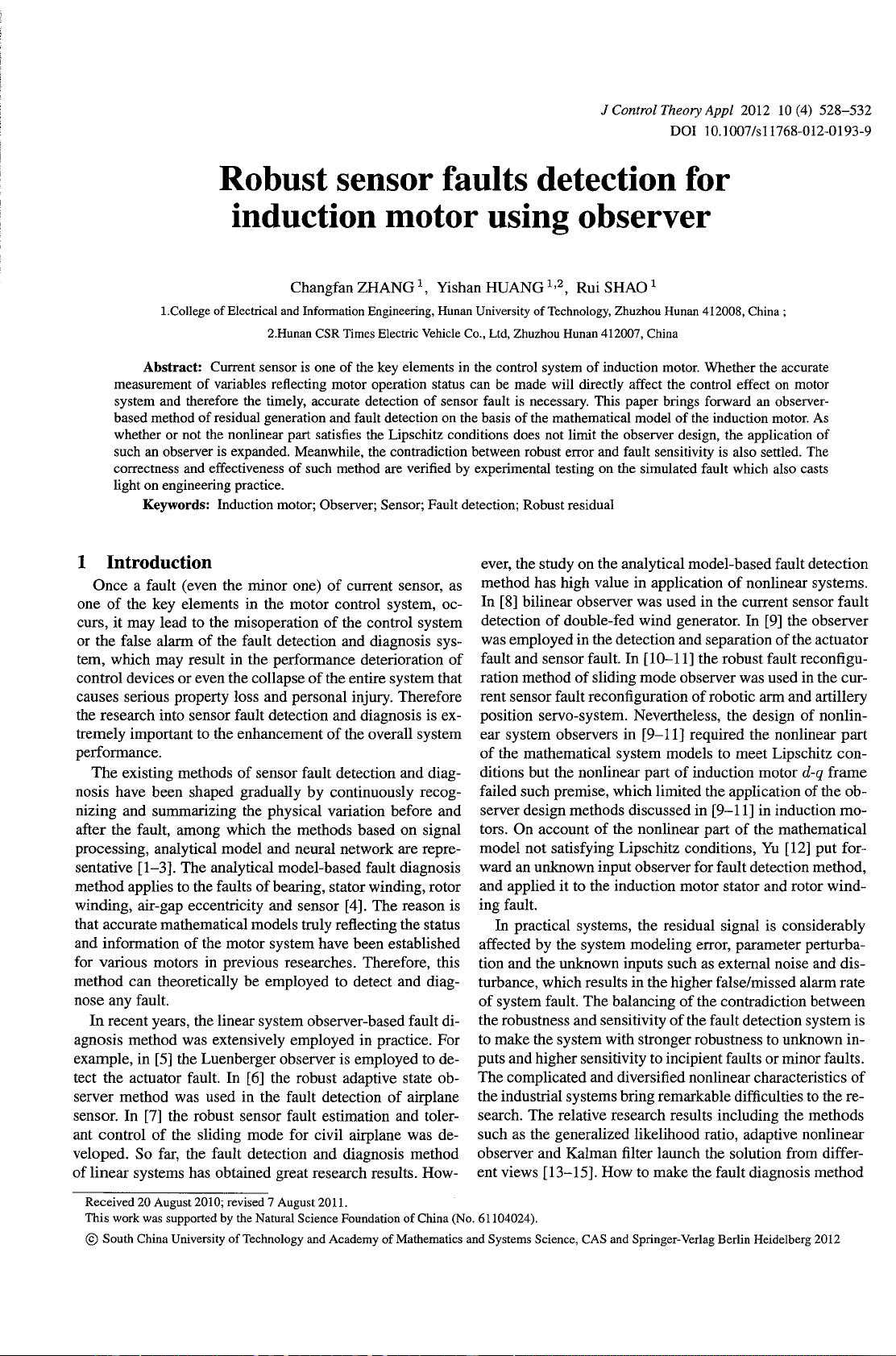
J Control
The
O/
γ
Appl
2012
10
(4)
528-532
DOI
1O
.1007/s11768-012-0193-9
Robust sensor faults detection for
induction
motor
using observer
Changfan
ZHANG
1, Yishan
HUANG
1,2, Rui SHAO 1
l.
Coll巳
ge
ofElectrical
and
Infonnation
Engineering
,
Hunan
University
ofTechnology
,
Zhuzhou
Hunan
412008
,
China;
2.Hunan
CSR
Times
Electric
Vehicle
Co.
,
Lt
d,
Zhuzhou
Hunan
412007
,
China
Abstract: Current sensor
is
one of
the
key
elements
in
the
control system of induction
motor.
Whether the accurate
measurement of variables reflecting motor operation status can
be
made
will direc
t1
y
a
仔
ect
the control effect
on
motor
system
and
therefore the timely, accurate detection of sensor fault
is
necess
缸
y.τ
'h
is
paper brings forward
an
obse
凹
er
based method of residu
a1
gen
巳
ration
and fault detection
on
th
巳
basis
of
the
mathematical
model
of
the
induction
motor.
As
whether or not
the
nonlinear
p
缸
t
satisfìes
the
Lipschitz conditions
does
not lirnit
the
observer design, the application of
such
an
observer
is
expanded.
M
巳
anwhile
,
the
contradiction between robust error
and
fault sensitivity
is
a1
so
settled.
The
correctness
and
effectiveness of such
method
缸
'e
verifìed
by
experiment
a1
testing
on
the
simulated fault which
also
casts
lighton
巳
ngineering
practice.
Keywords: lnduction motor; Observer; Sensor; Fault detection; Robust residual
1 Introduction
Once
a fault (even the minor one)
of
current sensor, as
one
of
the key e1ements in the motor contro1 system, oc-
curs
,
it
may 1ead to the
misop
巳
ration
of
the contro1 system
or the fa1se a1ann
of
the fault detection and diagnosis sys-
tem
, which may resu1t in the
p
巳
rformance
deterioration
of
contro1 devices
or
even the collapse
of
the entire system that
causes serious property 10ss and persona1 injury. Therefore
the research into sensor fault detection and diagnosis is ex-
treme1y important to the enhancement
of
the overall system
performance.
The
existing methods
of
sensor
fau1t
detection and diag-
nosis have been shaped gradu
a1
1y
by
continuous1y recog-
nizing and summarizing the physica1 variation before and
after the fau1t
, among which the methods based on signa1
processing
, an
a1
ytica1 mode1 and neur
a1
network are repre-
sentative [1-3]. The an
a1
ytic
a1
mode1-based
fau1t
diagnosis
method app1ies to the fau1ts
of
bearing, stator winding, rotor
winding
, air-gap
ecc
巳
ntricity
and sensor [4]. The reason is
由
at
accurate mathematica1 mode1s
tru1y
reftecting
由
e
status
and information
of
the motor system have been estab1ished
for various motors in previous researches. Therefore
, this
method
can theoretically
be
emp10yed to detect and diag-
nose any
fau1
t.
In
recent
ye
缸
s
,
the 1inear system observer-based
fau1t
di-
agnosis method was extensive1y emp10yed in practice. For
examp1e
, in [5] the Luenberger
obse
凹
er
is emp10yed to de-
tect the actuator
fau1
t.
In [6] the robust adaptive state ob-
server method was used in the fau1t detection
of
airp1ane
sensor. In [7] the robust sensor
fau1t
estimation and to1er-
ant contro1
of
the sliding mode for civil airp1ane was de-
ve1oped.
So
far, the fault detection and diagnosis method
of
linear
systems has obtained great research results. How-
Received
20
August
2010;
revised
7
August
201
1.
ever, the study on the ana1ytica1 mode1-based
fau1t
detection
method has high va1ue in application
of
non1inear systems.
In [8] bi1inear observer was used in the current sensor fau1t
detection
of
doub1e-fed wind generator. In [9] the observer
was emp10yed
in
the detection and separation
of
the actuator
fault and sensor
fau1
t.
In
[10
一
11]
the robust
fau1t
reconfigu-
ration method
of
sliding mode observer was used in the cur-
rent sensor fau1t reconfiguration
of
robotic
ann
and artillery
position servo-system. Neverthe1ess
, the design
of
non1in-
ear system observers in [9-11] required the non1inear
part
of
the mathematica1 system mode1s to meet Lipschitz con-
ditions but the non1inear
p
缸
t
of
induction motor d-q
frame
fai1ed such premise, which 1imited the application
of
the ob-
server design methods discussed in [9-11] in induction
mo-
tors.
On
account
of
the non1inear
p
缸
t
of
the mathematica1
mode1 not satisfying Lipschitz conditions
,
Yu
[1
2]
put
for-
ward an unknown input observer for fault detection method
,
and applied it to the induction motor stator and rotor wind-
ing
fau1
t.
In practica1 systems, the residua1 signa1 is considerab1y
affected
by
the system mode1ing
eηor
,
parameter perturba-
tion and the unknown inputs such as extema1 noise and dis-
turbance
, which resu1ts
in
the higher fa1se/missed a1ann rate
of
system
fau1
t.
The b
a1
ancing
of
the contradiction between
the robustness and sensitivity
of
the fau1t detection system is
to make the system with stronger robustness to unknown in-
puts and higher sensitivity to incipient faults
or
minor faults.
The
comp1icated and diversifìed non1inear characteristics
of
the industria1 systems bring remarkable diffìculties to the re-
search. The relative research results including the methods
such as the generalized likelihood ratio
, adaptive nonlinear
observer and Kalman filter launch the solution from differ-
ent views [13-15]. How to make the fault diagnosis method
Th
is
work
was
supported
by
the
Natural
Science
Foundation
of
China
(No.
61104024).
@
South
China
University
of
Technology
and
Academy
of
Mathematics
and
Systems
Science
,
CAS
and
Spring
巳
r-
Verlag
Berlin
Heidelberg
2012