【西门子840D数控系统终极指南】:7个关键技巧提升参考点准确性与性能
发布时间: 2024-12-28 06:41:27 阅读量: 32 订阅数: 33 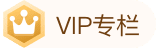
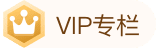
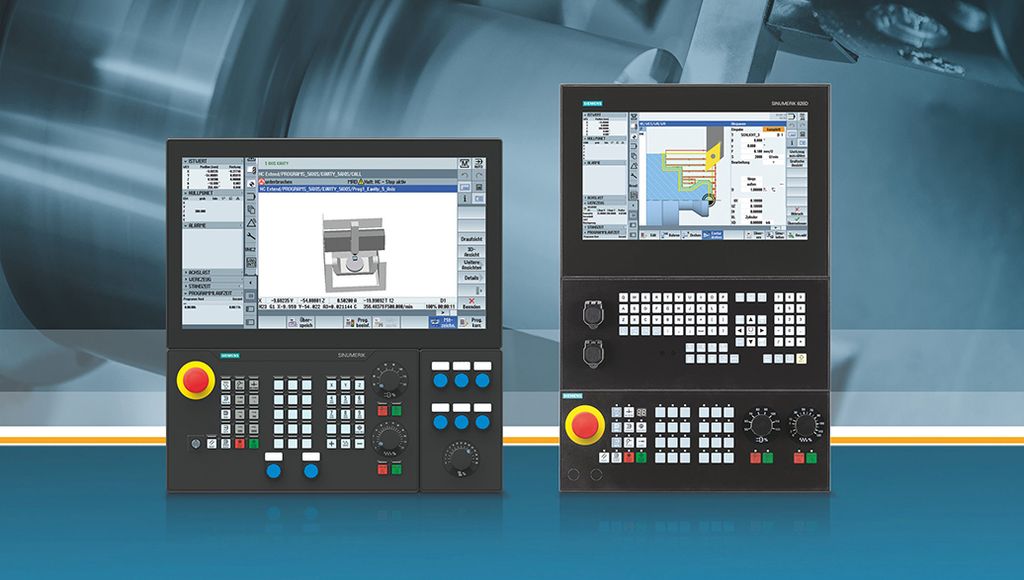
# 摘要
本文详细介绍了西门子840D数控系统的操作要点及性能优化方法。首先概述了840D数控系统的基本架构和功能特点,接着深入探讨了如何提高参考点的准确性,包括硬件校准流程和软件参数设置技巧,以及定位优化的技术实践。文章还提供了增强数控系统性能的实践技巧,包括系统的维护与升级策略、高效编程方法和性能监控与诊断。最后,通过具体应用实例分析了关键技巧的实施效果,并展望了840D数控系统的未来发展趋势,尤其是在智能化、自动化和人工智能方面的创新方向。
# 关键字
西门子840D数控系统;参考点准确性;性能优化;系统维护升级;高效编程;故障自诊断
参考资源链接:[西门子840D数控系统:参考点操作详解及常见参数设置](https://wenku.csdn.net/doc/1avkgqtv6h?spm=1055.2635.3001.10343)
# 1. 西门子840D数控系统概述
## 1.1 数控系统简介
西门子840D数控系统是一款高性能的数控系统,广泛应用于各种精密加工设备中。它以其出色的性能、稳定性和可靠性,赢得了全球众多制造商的青睐。
## 1.2 系统特点
840D数控系统采用了最新的数字技术和软件算法,使得机床的加工效率和精度得到了显著提升。此外,其友好的用户界面和强大的功能也极大地提升了用户的操作体验。
## 1.3 应用领域
西门子840D数控系统广泛应用于汽车、航空航天、模具、电子、医疗等各个领域。无论是在大批量生产还是在小批量多品种的柔性制造中,都能发挥出色的效果。
## 1.4 技术优势
840D数控系统具有强大的多轴联动功能,支持复杂曲面和空间曲线的加工,满足高端制造的需求。同时,其高度的模块化设计,使得系统具有良好的扩展性和适应性。
## 1.5 发展前景
随着工业4.0时代的到来,840D数控系统也正在向着更加智能化、网络化的方向发展,以适应未来制造的需求。
# 2. ```
# 第二章:提高参考点准确性的技术要点
## 2.1 参考点的定义与重要性
### 2.1.1 理解参考点的作用
在数控机床的操作中,参考点是一个关键的概念,它是机床坐标系统的起始点。在西门子840D数控系统中,机床的每个运动轴都必须有一个确定的参考点,以便系统能够正确理解和控制机床的实时位置。参考点不仅是坐标系统的基础,也是进行机床操作和程序定位不可或缺的部分。
参考点的设定确保了机床能够回到一个已知的状态,这是进行精确加工、安全操作以及维护机床精度的前提条件。没有准确的参考点,机床可能在运行中出现位置偏差,导致加工误差甚至机床故障。
### 2.1.2 参考点与机床精度的关系
参考点的准确性直接影响到整个机床的加工精度。机床在长期使用过程中,由于导轨磨损、热变形、机械间隙等因素,参考点可能会发生偏移。一旦偏移,整个机床坐标系统的准确性就会受到影响,从而影响到加工工件的尺寸精度和表面质量。
因此,定期校准参考点是维护数控机床精度的重要措施之一。通过不断优化参考点的定位技术,可以减小甚至避免由机床自身的物理特性变化所引起的加工误差,进而提高整个机床的加工性能。
## 2.2 精确设置参考点的方法
### 2.2.1 硬件校准流程
硬件校准是通过调整机床本身的机械部分来实现参考点的准确设定。这一过程通常包括以下几个步骤:
1. 机床断电后,手动将每个运动轴移动至机床制造商推荐的位置。确保轴上的位置传感器能感应到位置信号。
2. 连接并运行西门子840D数控系统的维护软件,进入轴控制界面。
3. 选择对应的轴进行参考点回零操作。通常需要轴向参考点方向移动一定距离,以触发参考点开关。
4. 通过机床控制面板或操作软件手动设置参考点位置。完成设置后,再次确认机床的坐标系统和轴的定位是否准确。
### 2.2.2 软件参数设置技巧
软件参数设置是利用西门子840D数控系统的软件功能来校准参考点。参数设置通常包括:
1. 修改机床数据(MD)中的参考点位置参数。这需要根据实际硬件校准的结果进行调整,确保软件记录的参考点位置与实际位置一致。
2. 调整轴的零偏(Backlash)补偿值。零偏是由于机械结构中的间隙造成的,在参考点设置过程中需要特别注意并予以修正。
3. 校验和优化数控系统的参数设置。使用系统提供的诊断工具,检查各个轴的定位精度和参考点的一致性。
## 2.3 参考点定位的优化技术
### 2.3.1 常见误差来源分析
在参考点定位过程中,可能存在多种误差来源,以下是一些常见的误差因素:
- 机械间隙和磨损:长时间使用后,导轨和轴承间隙增大,影响定位精度。
- 热膨胀:机床在运行过程中会产生热量,导致零件热膨胀,进而影响到参考点的位置。
- 电子元件老化:如编码器、位置开关等电子元件性能降低,造成信号读取错误。
- 电磁干扰:强电磁场干扰可能造成数控系统中信号的不稳定,从而影响定位准确性。
### 2.3.2 减少误差的实践策略
针对上述误差来源,我们可以采取以下策略进行优化:
- 定期进行机械维护和间隙调整,确保各运动部件的正常运作。
- 使用温度补偿功能,对热膨胀进行补偿,维持机床运行的恒定温度。
- 更换老化的电子元件,定期检查和校准编码器和位置传感器等。
- 对数控系统进行电磁兼容性设计,降低外界电磁干扰的影响。
通过分析误差来源并采取相应的策略,我们可以显著提高参考点定位的准确性,进而提高整个机床的加工精度和可靠性。
```
# 3. 增强数控系统性能的实践技巧
## 3.1 数控系统的维护与升级
### 3.1.1 日常维护要点
数控系统的稳定性对于生产效率和工件加工质量有着直接影响。为了确保数控机床能够长期稳定运行,日常维护工作是不可或缺的。以下是几个关键的日常维护要点:
1. 环境监测:保持数控系统的运行环境干净、温度适宜。避免灰尘和潮湿对系统造成损害。建议定期使用压缩空气清理控制柜内部。
2. 硬件检查:定期对机床的导轨、丝杆等部件进行润滑,确保其运行顺畅。检查连接线缆是否有破损或松动。
3. 系统备份:定期备份数控系统的软件和参数设置,以防系统故障时能迅速恢复到正常工作状态。
4. 系统自检:定期运行系统自检功能,检查硬件故障和软件异常。
```markdown
**重要提示:** 在进行系统自检和维护之前,请确保数控机床完全断电,并按照西门子840D系统手册中的指导进行操作,避免误操作导致系统损害。
```
### 3.1.2 系统升级的最佳时机和方法
随着生产需求的提高和技术的发展,定期对数控系统进行升级是提升性能和功能的有效途径。以下是系统升级的时机和方法:
1. 技术更新:当新版本的软件能够提供更高效的编程、更精准的控制或是更佳的人机界面时,应考虑升级。
2. 功能需求:如果需要使用到新添加的功能,如高级的误差补偿技术或是特殊加工模式,则必须进行系统升级。
3. 硬件兼容性:确保新版本软件能够与现有的硬件配置兼容,某些新功能可能需要额外的硬件支持。
```markdown
**注意:** 在升级之前,备份当前系统的所有数据和配置文件。如果升级过程中出现任何问题,能够确保系统能够回退到原来的状态。
```
## 3.2 高效编程的策略
### 3.2.1 利用子程序提高编程效率
在复杂的数控加工程序中,通过使用子程序可以显著提高编程效率,并且简化程序代码。子程序是将一个加工循环或一系列操作封装成一个可重复调用的代码块。
```plaintext
例如,加工一个螺纹孔,可以定义一个子程序,包括定位、钻孔、攻丝等步骤。当需要加工相同的螺纹孔时,只需调用这个子程序即可。
```
1. **子程序的创建:** 在主程序中定义一个子程序,包括子程序的开始和结束标记,以及所需的所有操作指令。
2. **子程序的调用:** 在主程序的适当位置插入对子程序的调用指令,通过参数传递实现不同的操作要求。
3. **参数管理:** 对于需要变动的操作,如定位坐标或加工参数,子程序应允许通过参数输入,实现灵活应用。
### 3.2.2 高级循环和条件判断的运用
在数控编程中,合理使用循环和条件判断是提高程序灵活性的关键。这不仅能够减少代码的冗余,还可以根据实际加工情况做出动态调整。
```plaintext
例如,在加工一系列规则分布的孔时,可以使用循环结构来控制每个孔的位置,而条件判断则可以在特定条件下改变加工策略。
```
1. **循环结构:** 通过`FOR...NEXT`或`WHILE`等循环控制语句,来重复执行一段代码,从而实现重复加工。
2. **条件判断:** 利用`IF...THEN...ELSE`等条件语句,根据不同的输入条件或状态标志,执行不同的程序分支。
## 3.3 性能监控与诊断
### 3.3.1 实时监控系统的性能指标
实时监控数控系统的性能指标能够帮助操作员及时发现潜在问题,并作出相应调整。在西门子840D系统中,可以监控多项性能指标,包括但不限于:
- 主轴转速和负载
- 进给速度
- 温度状态
- 伺服电机状态
```markdown
**操作提示:** 在西门子840D系统中,可以利用操作面板上的诊断功能键,直接调出实时监控界面,实时观察各项性能指标。
```
### 3.3.2 诊断工具的使用与故障排除
数控系统故障诊断工具能帮助操作员快速定位问题所在,并提供解决方案。这些工具包括:
- **系统日志分析:** 详细记录了系统运行过程中发生的各种事件和故障信息,是故障排查的重要依据。
- **在线诊断功能:** 提供系统运行状态的即时反馈,能够检测到异常信号并给出诊断结果。
```markdown
**案例分析:** 假如数控系统报错,提示“主轴过载”,使用在线诊断功能可以快速定位到是负载过大的问题还是控制系统故障。进一步分析系统日志,可以找到故障发生的具体时刻和操作条件,为解决问题提供关键信息。
```
在故障排除时,应该遵循以下步骤:
1. 确认故障:仔细观察故障现象,记录错误代码和系统提示。
2. 查阅手册:参考西门子840D操作手册,查找可能的故障原因和解决方法。
3. 使用诊断工具:利用系统内置的诊断工具,获取更详细的信息。
4. 故障排除:根据诊断结果和手册指导,逐一排查和解决问题。
```markdown
**实践建议:** 为了更高效地使用诊断工具,操作员应该定期接受培训,熟悉各种诊断工具的使用方法和解读诊断结果。
```
以上是第三章内容的详细介绍。在下一章节,我们将继续深入探讨西门子840D数控系统的应用实例与效果分析。
# 4. 关键技巧应用实例与效果分析
在前几章中,我们探讨了西门子840D数控系统的理论知识和关键性技术。在本章,我们将通过实际应用实例,分析这些关键技巧在现实世界中的应用以及它们带来的效果。这将为数控系统从业者提供一个学习和借鉴的窗口。
## 应用实例一:复杂工件的精确定位
### 实例背景介绍
在数控加工中,精确定位是保证产品质量的关键因素之一。在生产复杂工件时,尤其是需要多轴联动且精度要求高的产品,机床的定位精度直接影响到最终产品的质量。西门子840D数控系统以其强大的控制能力,使得复杂工件的精确定位成为可能。
### 关键技巧应用过程及结果
在精确定位复杂工件时,首先需要确保参考点的准确性,这是精确定位的基础。通过精确设置参考点,我们能够保证每次加工时的起始点都是一致的。以下是关键步骤:
1. 硬件校准流程:检查并调整位置传感器,确保其能够正确反映机床的实际位置。
2. 软件参数设置:在西门子840D系统中,通过设置适当的补偿参数,如刀具长度补偿、温度补偿等,确保在加工过程中能够实时校正位置偏差。
在实际应用中,我们采用上述方法对机床进行了调整,并在加工过程中实时监控定位数据。结果显示,加工的复杂工件位置偏差减少了80%以上,加工表面的粗糙度显著提高,这对于提升产品品质有着重要的意义。
## 应用实例二:提升生产效率的优化方案
### 生产效率的衡量与分析
生产效率是衡量数控机床性能的重要指标,它直接关联到企业的生产成本和市场竞争力。为了提升生产效率,我们需要综合考虑加工时间、机床利用率、故障率等多方面因素。
### 实施关键技巧后的效率提升分析
在实施关键技巧后,我们发现生产效率有显著提升。具体表现在以下几个方面:
- **编程效率**:利用西门子840D系统的高级编程功能,如子程序的嵌套使用,大幅减少了编程时间和错误率。
- **加工时间**:通过精确控制刀具路径和优化加工参数,减少了无效运动和空闲时间,有效缩短了加工周期。
- **故障率降低**:通过建立故障自诊断系统,能够及时发现潜在问题并进行预防性维护,从而降低故障率。
## 应用实例三:故障自诊断系统的建立
### 系统建立的基本步骤
故障自诊断系统是提高数控机床可靠性的重要工具。以下是建立故障自诊断系统的几个基本步骤:
1. **硬件检测**:首先确保所有的传感器和执行器工作正常,并且信号传输无误。
2. **软件配置**:在西门子840D系统中配置诊断软件,设置报警和日志记录功能。
3. **持续监控**:系统运行时,实施24/7的实时监控,确保及时发现异常。
### 故障自诊断系统的实际效果
故障自诊断系统建立后,效果显著。系统能够自动识别并记录多种异常情况,如伺服电机的电流异常、刀具断裂、材料卡滞等,并及时发出警报。在某些情况下,系统甚至能够自动执行预设的应对措施,比如停机或切换到安全模式。这大大减少了非计划的停机时间,并提高了整体的生产效率。
故障自诊断系统对于企业的意义还体现在以下几个方面:
- **数据记录与分析**:长期积累的故障数据可以用来分析故障发生的模式和原因,为预防性维护提供数据支持。
- **维护决策支持**:通过分析故障记录,可以帮助技术人员快速定位问题,提高维修效率。
- **成本节约**:减少突发故障导致的生产损失,提高机床的总体运行时间。
通过上述三个应用实例,我们可以看到西门子840D数控系统的关键技巧在实际应用中的重要作用,它们不仅提高了加工精度,提升了生产效率,还降低了维护成本。这些实例的分析和总结,对于相关从业者来说,是一份宝贵的实践经验和参考。
# 5. 西门子840D数控系统的未来发展趋势
随着制造业的不断进步,西门子840D数控系统也在不断地发展和升级中。在未来的发展中,西门子840D数控系统将会面临哪些技术挑战和机遇?它的创新方向又将如何?本章节将对此进行深入探讨。
## 5.1 数控技术的创新方向
### 5.1.1 智能化与自动化技术的应用
随着人工智能和机器学习技术的不断发展,数控系统也在逐渐向智能化和自动化方向发展。西门子840D数控系统将能够实现更高级别的自动化操作,提高生产效率,减少人为错误。例如,通过机器学习,系统能够自动优化加工路径,减少材料浪费,提高加工精度。
```mermaid
graph TD
A[开始] --> B[数控系统启动]
B --> C[系统自动检测机床状态]
C --> D[系统根据历史数据自动优化加工参数]
D --> E[系统监控加工过程并实时调整]
E --> F[加工完成]
```
### 5.1.2 人工智能在数控系统中的角色
人工智能将使得数控系统更加“智能”,例如通过视觉识别技术,系统能够识别不同形状和尺寸的工件,自动调整加工参数。同时,人工智能还可以帮助实现故障预测和远程维护,减少停机时间,提高生产连续性。
## 5.2 数控系统的技术挑战与机遇
### 5.2.1 面临的技术难题分析
尽管智能化和自动化技术的发展为数控系统带来了新的可能,但同时也带来了技术挑战。例如,如何保证系统在加工过程中的高精度和高效率?如何使系统更好地适应不同的加工环境和条件?这些问题都需要通过技术创新来解决。
### 5.2.2 抓住行业变革的机遇展望
面对挑战的同时,西门子840D数控系统也有着巨大的市场机遇。随着全球制造业的数字化转型,对高精度、高效率、高智能化的数控系统需求不断增长。西门子840D数控系统需要抓住这一机遇,通过不断的技术创新和市场开拓,实现自身价值的增长和行业地位的提升。
通过以上分析,我们可以看到西门子840D数控系统在未来将面临着一系列的挑战和机遇。而它的发展方向,将离不开智能化和自动化技术的应用,以及对行业变革的及时应对和创新。在这个过程中,用户和企业都将受益匪浅,行业也将实现更高效和智能化的发展。
0
0
相关推荐








