【工程实践】:如何在设计初期优化MTBF
发布时间: 2024-12-01 07:51:40 阅读量: 32 订阅数: 46 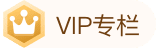
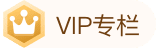
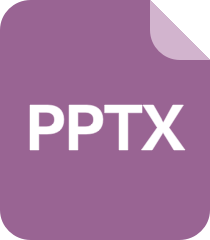
控制系统设计与工程实现培训课件.pptx
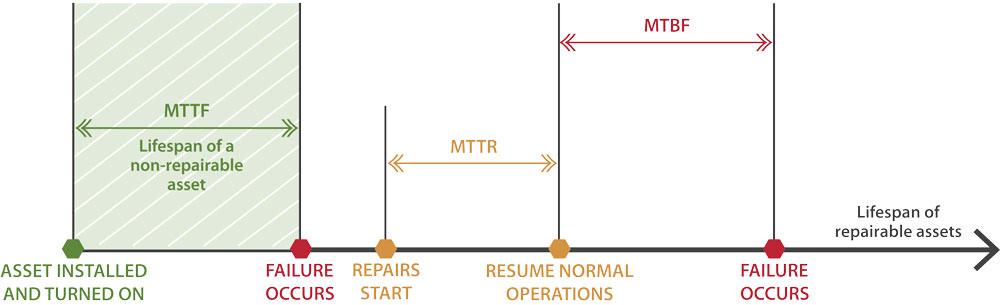
参考资源链接:[MTBF Telcordia_SR-332 Issue 4 2016.pdf](https://wenku.csdn.net/doc/6412b780be7fbd1778d4a871?spm=1055.2635.3001.10343)
# 1. MTBF的重要性及基本概念
## 1.1 MTBF的重要性
MTBF(Mean Time Between Failures,平均无故障时间)是衡量产品可靠性的关键指标之一,它直接影响着产品的市场竞争力与用户满意度。一个高的MTBF值意味着产品在正常使用情况下发生故障的间隔时间长,从而提高了产品的稳定性和用户的信任度。这对于企业来说,可以降低维修成本,提高客户满意度,并在激烈的市场竞争中占据有利位置。
## 1.2 MTBF的基本概念
MTBF指的是产品从开始使用到首次出现故障的平均时间长度。计算MTBF通常需要采集大量产品在真实使用环境下的故障数据,并采用统计学方法进行分析。对IT行业而言,MTBF对于评估技术设备的可靠性和预测维护周期具有至关重要的作用。MTBF不仅仅是一个简单的数值,它还关联着系统的复杂性、维护策略、以及用户的操作习惯等多个因素。
通过深入理解MTBF,IT行业的专业人员能够更好地进行产品设计与优化,确保产品在生命周期内的稳定运行,从而为客户带来更加安全可靠的服务。接下来的章节中,我们将详细探讨MTBF在设计阶段的应用,如何在工程实践中提升MTBF,以及实际案例分析和面临的挑战。
# 2. 设计阶段的MTBF理论分析
在现代工业设计中,MTBF(平均无故障时间)是一个关键的指标,它不仅关系到产品的质量和可靠性,还与生产成本、市场竞争力乃至品牌形象密切相关。为了深入理解MTBF在设计阶段的应用,本章节将从理论框架出发,阐述MTBF的定义、计算方法以及其与产品可靠性的关系;进一步探讨可靠性工程的基础理论,特别是可靠性设计原则以及故障模式与影响分析(FMEA);最后通过理论模型的应用来说明如何在设计阶段实际运用MTBF理论,以提高产品的可靠性。
## 2.1 MTBF理论框架
### 2.1.1 MTBF的定义和计算方法
MTBF是“Mean Time Between Failures”的缩写,即“平均无故障时间”,是指一个产品或系统从投入使用到出现第一次故障之间的时间平均值。MTBF是衡量产品或系统可靠性的重要指标之一,通常用小时作为时间单位。
MTBF的计算方法有多种,其中最常用的是基于历史故障数据的统计方法,此方法需要记录产品在特定时间段内的运行时间以及在这个时间段内发生的故障次数。计算公式如下:
\[ MTBF = \frac{总的运行时间}{总的故障次数} \]
对于尚未投入市场的新型产品,可以采用预测性分析方法,如FMEA(故障模式与影响分析)或使用相关组件的MTBF数据来估算整个系统的MTBF。
### 2.1.2 MTBF与产品可靠性的关系
MTBF与产品的可靠性之间存在直接关系。从定义上可以看出,MTBF值越大,表示产品发生故障的间隔时间越长,产品的可靠性越高。可靠性可以视为一种概率度量,描述产品在规定条件下和规定时间内无故障运行的概率。
为了更准确地理解MTBF和可靠性的关系,需要引入“故障率”(Failure Rate)的概念。故障率是在任意时刻t之后的一个小的时间间隔Δt内,产品发生故障的概率。通常情况下,产品在刚开始使用时故障率较高,随着使用时间的增加,故障率趋于稳定,随后又开始上升,形成所谓的“澡盆曲线”。
在“澡盆曲线”的稳定期间,MTBF值能够很好地反映这一时期的平均无故障时间,而产品的可靠性则可以用指数分布函数来表示:
\[ R(t) = e^{-\frac{t}{MTBF}} \]
其中,R(t)表示产品在时间t内无故障运行的概率。
## 2.2 可靠性工程基础
### 2.2.1 可靠性设计原则
可靠性设计是产品设计的关键部分,旨在通过合理的设计来确保产品的稳定性和可靠性。可靠性设计原则包括:
- **简化设计**:避免设计过于复杂,减少潜在的故障点。
- **标准化**:使用经过验证的标准化组件和模块。
- **适度冗余**:设计中引入必要的冗余,提高系统容错能力。
- **应力限制**:合理确定工作参数,避免过度负载。
- **质量控制**:在生产过程中实施严格的质量控制。
- **环境适应性**:考虑产品在不同环境下的性能和可靠性。
### 2.2.2 故障模式与影响分析(FMEA)
故障模式与影响分析(FMEA)是一种系统化的分析方法,用于识别产品设计和制造过程中可能出现的故障模式,评估故障可能产生的影响,并根据风险程度采取相应的预防或改进措施。FMEA的过程通常包括:
1. **故障模式识别**:列出所有可能的故障模式。
2. **故障影响评估**:分析每个故障模式对产品性能的影响。
3. **风险优先级评定**:通过风险优先数(RPN)评估每个故障模式的风险程度。
4. **风险缓解措施**:根据RPN制定相应的风险缓解措施。
### 2.3 MTBF理论模型的应用
#### 2.3.1 理论模型选择标准
在设计阶段,选择合适的MTBF理论模型至关重要。选择标准通常包括:
- **适用性**:模型必须适合产品类型和预期的应用场景。
- **准确性**:模型计算结果需要足够接近实际运行中的表现。
- **可操作性**:模型应易于理解和操作,便于工程人员应用。
- **灵活性**:模型能适应产品设计的变动,容易进行更新和优化。
#### 2.3.2 模型在设计阶段的应用实例
为了说明MTBF理论模型在设计阶段的具体应用,这里介绍一个实例:
假设一个企业正在设计一种新型的工业控制系统,该系统由多个模块组成。为了评估和提升系统的MTBF,设计团队首先建立了一个基于故障树分析(FTA)的理论模型。通过FTA,设计团队能够识别出可能导致整个系统故障的关键故障模式。然后,团队采用类似指数分布的数学模型来预测不同模块的MTBF,并依据模型结果对系统进行优化设计。比如,通过改进某关键模块的设计,减少其故障率,从而提高该模块及整个系统的MTBF。最终,设计团队能够通过模型预测系统的平均无故障时间,并与行业标准进行对比,以确保产品满足或超过了可靠性要求。
在本节内容中,我们通过深入的理论框架和可靠性工程基础,为理解MTBF在产品设计阶段的作用奠定了坚实的基础。通过实例分析,我们展示了如何将这些理论应用到实际的设
0
0
相关推荐







