【模拟与测试案例分析】:发那科DCS系统中文手册指导下的实操技巧
发布时间: 2024-12-21 08:00:03 阅读量: 1 订阅数: 6 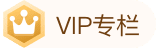
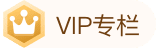
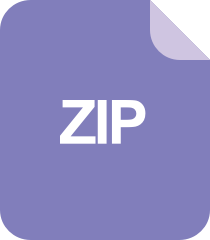
发那科_DCS_中文说明书解决一些FANUC安全配置方面的问题.zip
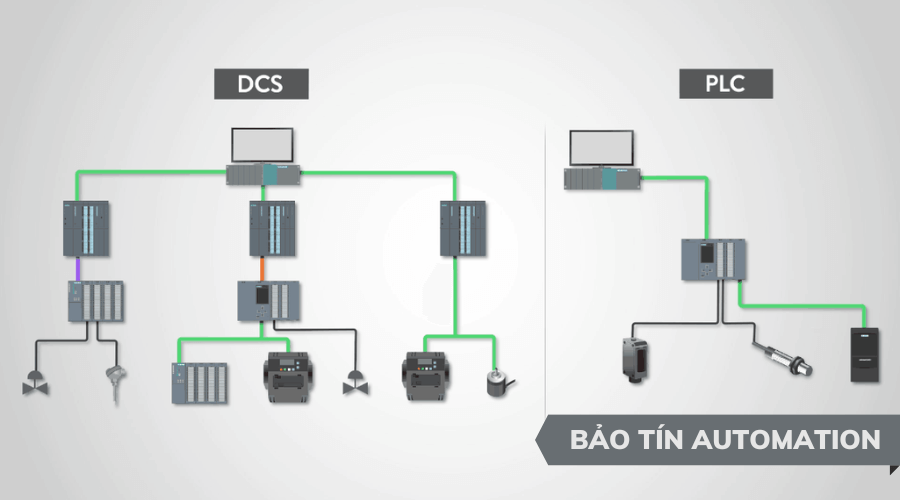
# 摘要
发那科DCS系统作为一种先进的分布式控制系统,广泛应用于工业自动化领域。本文首先介绍了发那科DCS系统的总体概述及其理论基础,深入探讨了系统架构、操作原理以及系统集成与网络通信。随后,本文着重描述了系统的配置、调试以及性能优化和维护策略,并结合实际案例分析,提供了模拟测试环境的搭建和案例解决策略。文章第五章分享了日常操作维护技巧与高级功能的应用,并通过案例实操演练,展示了系统的实用性和操作要点。最后,本文展望了发那科DCS系统未来的技术发展趋势和挑战,提出了发展策略和行业案例,为工业自动化领域提供了宝贵的参考。
# 关键字
发那科DCS;分布式控制系统;系统架构;操作原理;系统集成;性能优化;模拟测试;实操技巧;技术发展;工业自动化
参考资源链接:[发那科_DCS_中文说明书.pdf](https://wenku.csdn.net/doc/6412b6d8be7fbd1778d482f2?spm=1055.2635.3001.10343)
# 1. 发那科DCS系统概述
## 1.1 发那科DCS系统简介
发那科DCS(Distributed Control System,分布式控制系统)是发那科公司在工业自动化领域推出的一款先进的控制解决方案。它集成了数据采集、处理、控制、通信等多种功能,通过分布式架构实现了对工业生产过程的精确控制与管理。
## 1.2 系统特点与优势
该系统具有高性能、高可靠性、易操作和扩展性好等特点。它能够处理大量实时数据,确保生产过程的稳定性和安全性。同时,它的模块化设计使得系统易于扩展,能够满足不同规模工业企业的需要。
## 1.3 应用领域
发那科DCS广泛应用于石油、化工、电力、冶金、造纸等多个行业。在这些行业中,系统负责监控复杂的生产流程,确保各项工艺指标达到最佳状态,以提高生产效率和产品质量。
# 2. 发那科DCS系统的理论基础
## 2.1 DCS系统架构解析
### 2.1.1 分布式控制系统概念
分布式控制系统(DCS)是一种将控制功能分散到多个控制单元的自动化控制技术。在DCS中,每一个控制单元可能承担特定的控制任务,通过网络与其他单元进行通信,共同完成整个系统的监控和控制。DCS的特点在于它的可扩展性、可靠性以及灵活性,使其在各种工业应用中得到了广泛的使用,如石化、钢铁、电力等行业。
分布式控制系统与集中式控制系统相对,后者所有的控制功能都集中在单一的控制室或处理器上。DCS的设计理念能够更好地适应工业生产中不断变化的过程条件,并且能够实现局部故障不会影响整个系统的稳定运行,提高了系统的鲁棒性。
### 2.1.2 发那科DCS的硬件组成
发那科DCS的硬件组成包括多个层面的设备。从底层的传感器和执行器,到中间层的控制器,再到顶层的操作站和工程师站。传感器负责采集现场数据,执行器负责根据控制命令实施动作。控制器作为核心处理单元,通常分为现场控制器(Field Controller)和区域控制器(Area Controller),它们负责执行控制策略和数据处理。
操作站(Operator Station)提供人机交互界面,允许操作人员进行监控、控制以及数据的分析。工程师站(Engineer Station)则是系统设计和配置的平台,用于对系统进行维护和故障诊断。在发那科DCS系统中,所有的硬件设备通过高速工业通信网络相连接,确保数据的实时性和可靠性。
### 2.1.3 发那科DCS的软件平台
发那科DCS系统中的软件平台提供了一个完整的编程和配置环境,允许工程师进行系统开发和维护。其核心是实时数据库(Real-time Database)和控制引擎(Control Engine),实时数据库用于存储和管理过程数据,控制引擎则是执行控制策略和算法的中心。
软件平台通常包含以下几部分:
- **控制语言和编程工具**:提供定制控制策略的编程语言和开发工具,如梯形图、功能块图、顺序功能图等。
- **人机界面(HMI)软件**:用于设计和实现操作员和系统之间的交互界面。
- **数据管理和分析工具**:用于存储历史数据、生成趋势图和报表,帮助进行数据分析和决策。
- **网络管理和通信配置工具**:确保系统内部以及与其他系统的通信顺畅和安全。
## 2.2 发那科DCS的操作原理
### 2.2.1 数据采集与处理流程
数据采集与处理是DCS系统的首要功能,其流程始于从现场采集到的模拟或数字信号,这些信号通过传感器和I/O模块被传送到控制器。控制器内的数据采集模块负责对这些信号进行解析和转换,使之成为系统能够处理的格式。
处理流程的关键在于数据的同步和实时性。采集到的数据需要实时地被处理并存入实时数据库中,供后续的控制算法调用。数据处理包括过滤噪声、转换单位、应用数学模型等步骤,以确保数据的准确性和可用性。
### 2.2.2 控制算法与策略
控制算法是DCS系统的大脑,它决定着整个系统的控制逻辑和输出。发那科DCS系统支持多种控制算法,包括但不限于PID控制、先进过程控制(APC)、模糊逻辑控制等。
控制策略的制定依赖于对过程的理解和对生产目标的设定。工程师会根据控制对象的特点和工艺要求,编写相应的控制程序,实施如PID控制的参数调整,以及根据需要集成更为复杂的控制逻辑。
### 2.2.3 人机界面(HMI)与操作逻辑
人机界面(HMI)是工程师和操作员与DCS系统交互的界面。一个良好的HMI设计可以提高操作效率,减少错误操作的风险。在发那科DCS系统中,HMI不仅显示过程数据和控制状态,还允许操作员直接对现场设备进行控制和调整。
HMI的设计需要遵循人类工程学原则,操作逻辑应当直观易懂,确保操作员能够快速地识别系统状态和做出响应。例如,在系统发生异常时,HMI能够提供报警信息,并指导操作员进行必要的操作步骤。
## 2.3 系统集成与网络通信
### 2.3.1 系统集成的基本概念
系统集成是指将分散的系统、设备、传感器、控制器等通过网络连接起来,形成一个统一、协调工作的整体。在发那科DCS系统中,集成不仅包括硬件的连接,还包括软件的整合和数据的流动。
系统集成的目标是实现一个自动化、智能化的过程控制系统,提高生产效率和产品质量,同时降低运营成本。为了实现有效的系统集成,需要对整个系统进行详细的设计规划,包括硬件选择、网络架构、数据通信协议等。
### 2.3.2 网络通信协议与标准
网络通信是连接DCS系统各个组成部分的纽带,而通信协议则是它们之间交流的语言规则。发那科DCS系统支持多种工业通信协议,包括Modbus、OPC(OLE for Process Control)、以太网/IP等,确保了与各种设备和系统的兼容性。
通信标准确保了不同制造商的设备能够无缝集成,简化了系统配置和维护过程。在实施网络通信时,需要考虑到数据传输的速度、可靠性以及安全性,采用适当的网络拓扑结构,如星型、环型或混合型。
### 2.3.3 发那科DCS与其他系统的交互
发那科DCS系统并不孤立存在,它通常需要与其他系统如企业资源规划(ERP)、制造执行系统(MES)以及上层的信息系统进行交互。数据的共享和交换能够使得企业的生产活动更加协调一致,实现资源优化配置。
交互的关键在于数据的准确性和实时性。例如,DCS可以向MES系统提供实时的生产数据,以便进行生产调度和优化;同时,MES系统也可以向DCS传递计划和排程信息,使得DCS能够及时调整控制策略。这种双向的数据交互依赖于标准化的接口和协议。
```mermaid
graph LR
A[发那科DCS系统] -->|数据/控制信息| B[ERP系统]
B -->|生产计划信息| A
A -->|实时生产数据| C[MES系统]
C -->|排程信息| A
```
通过上述的表格、mermaid流程图以及对分布式控制系统架构、操作原理和系统集成的解析,我们可以更好地理解发那科DCS系统的基础理论。这些理论是进行系统配置、调试和优
0
0
相关推荐
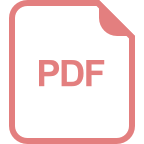
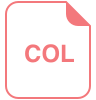
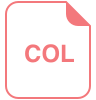
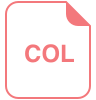
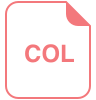
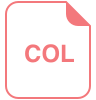
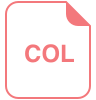
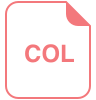