加工时间减半:CNC程序优化技巧大公开
发布时间: 2024-12-27 16:53:48 阅读量: 8 订阅数: 10 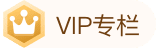
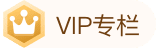
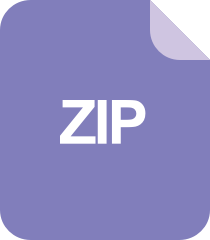
单变量优化的内部减半法:单变量优化的内部减半法-matlab开发
# 摘要
CNC(计算机数控)程序优化是提高数控机床加工效率和质量的关键环节。本文从CNC程序优化的基本概念入手,深入探讨了CNC机床的工作原理、编程语言以及理论与实践的结合。在优化策略方面,本文提出减少非切削时间、提高切削效率和程序结构优化三大方向,并通过具体实例分析展示了优化步骤与效果对比。此外,本文还介绍了CAM软件、仿真技术和人工智能在CNC程序优化中的应用,并展望了智能制造、3D打印技术与CNC技术的融合前景,以及未来面临的挑战和应对策略。
# 关键字
CNC程序优化;CNC机床原理;编程语言;刀具路径规划;智能制造业;人工智能;CAM软件
参考资源链接:[新代SYNTECCNC控制系统手册:轴卡与I/O配置](https://wenku.csdn.net/doc/3efzjegjos?spm=1055.2635.3001.10343)
# 1. CNC程序优化概述
随着制造业对高精度和高效率的不断追求,CNC程序优化成为了现代制造工艺中不可或缺的一环。它不仅仅涉及到机床操作技能,更依赖于对CNC编程语言的精通、材料特性及加工工具的深入理解。CNC程序优化的目标是提升生产效率,延长工具寿命,减少加工成本,最终实现高质量的产品加工。在本章中,我们将对优化的必要性及其对制造过程的影响做基本介绍,并探讨优化过程中的基本原则。
# 2. CNC程序理论基础
## 2.1 CNC机床的工作原理
### 2.1.1 CNC机床的组成和功能
CNC(Computer Numerical Control)机床是通过计算机数字控制技术实现高精度、高效率自动化的机床设备。其组成主要包括以下几个部分:
- 控制系统:核心为计算机,负责处理加工指令,控制机床运动。
- 驱动系统:包括伺服电机和步进电机,用于驱动机床的移动部件。
- 传动系统:涉及丝杆、齿轮等,将电机的旋转运动转换为直线运动。
- 执行部件:刀具、工件台等,直接参与加工过程。
- 传感器和反馈系统:用于实时监控机床状态并反馈给控制系统。
每个部分协同工作,按照预设的程序指令完成材料的加工,如切割、钻孔、铣削等。CNC机床通过精确控制这些机械部件,可以实现复杂轮廓和精细表面的加工。
### 2.1.2 CNC编程的基本概念
CNC编程是将加工过程转换为计算机可以理解的指令代码的过程。基本概念包括:
- G代码(G-code):用于指示机床操作指令,如移动指令(直线G01、圆弧G02/G03等)、速度设置(G94/G95)、刀具选择(T code)等。
- M代码(M-code):用于控制机床辅助功能,如开关冷却液(M08/M09)、主轴启动/停止(M03/M05)等。
- 坐标系:用于定义加工过程中的工件位置,常见的有工件坐标系(G54等)和机床坐标系(G53)。
- 刀具补偿:对刀具尺寸误差进行补偿的编程操作。
了解这些基本概念对于编写高效准确的CNC程序至关重要。
## 2.2 CNC编程语言与代码结构
### 2.2.1 G代码与M代码解析
G代码和M代码是CNC机床编程的基础语言,每一行代码都代表一个特定的操作或指令。以下为一些常用G代码与M代码解析示例:
```plaintext
G21 - 设置单位为毫米
G90 - 绝对编程
G91 - 增量编程
G00 - 快速定位
G01 - 直线插补
G02 - 顺时针圆弧插补
G03 - 逆时针圆弧插补
M03 - 主轴正转
M05 - 主轴停止
M08 - 冷却液开启
M09 - 冷却液关闭
```
每一行代码都必须严格遵循CNC机床的语法规则,正确使用这些代码可以确保机床的正确运动和安全操作。
### 2.2.2 程序段和子程序的作用
程序段是一组连续的代码行,负责执行一个特定任务。子程序是一种编程结构,它允许将经常使用的代码序列定义为一个单独的模块,通过调用子程序名即可执行这些代码。
```plaintext
O0001 (主程序开始)
...
G00 X0 Y0 Z0 (快速移动到起始位置)
...
M98 P0002 (调用子程序)
...
M30 (主程序结束)
O0002 (子程序开始)
...
G01 Z-5 F100 (按预设进给率切削)
...
M99 (返回主程序)
```
通过使用程序段和子程序,可以优化CNC程序的结构,提高代码的可读性和可维护性。
## 2.3 理论与实践:从理论到程序设计
### 2.3.1 刀具路径规划的理论基础
刀具路径规划是CNC编程中的核心环节,它决定了材料的去除方式和加工表面的质量。理论基础包括:
- 切削力理论:理解刀具在不同加工条件下的力的变化。
- 材料去除率:计算在特定条件下可以去除的材料体积。
- 热变形:了解刀具和工件在加工中产生的热量对加工精度的影响。
通过对这些理论的理解,工程师可以在编写程序时作出合理的判断,规划出高效的刀具路径。
### 2.3.2 编程时的物料与工具选择
选择合适的材料和刀具对加工效果和效率至关重要。要考虑以下几个方面:
- 材料的硬度、韧性和热膨胀系数。
- 刀具的材料、几何形状和涂层。
- 加工要求,如表面粗糙度、尺寸精度等。
例如,对于硬度高的材料,应选择硬质合金刀具或陶瓷刀具。而对于需要高表面质量的加工,应选择具有锋利切削刃的刀具。
在选择合适的刀具和材料后,编程时还需考虑刀具的径向和轴向切削深度,以及切削速度和进给速度,以实现最优的材料去除率和加工效率。
```plaintext
(示例代码:选择刀具和设置切削参数)
T1 M06 (选择刀具1)
G96 S200 M03 (设置恒定表面速度200米/分钟并开启主轴)
G00 X0 Y0 (快速移动到起始位置)
G01 Z-5 F0.2 (以0.2mm/rev的进给率进行直线切削)
```
通过综合考虑理论知识和实际加工需求,可以编写出既满足加工质量要求又高效率的CNC程序。
# 3. ```
# 第三章:CNC程序的优化策略
## 减少非切削时间
### 优化换刀和快速定位
在数控加工中,非切削时间包括换刀时间、快速定位时间以及工件装夹和卸载时间。通过优化这些环节,我们可以显著提高CNC机床的生产效率。针对换刀,选择合适的刀具库布局和刀具管理系统能够减少刀具选择和更换时间。此外,采用高速刀具更换技术可以进一步减少停机时间。对于快速定位,可以通过优化程序,减少定位时的移动距离和加减速次数,使用预设的参考点,或者提高控制系统的响应速度来缩短定位时间。
### 减少空运行和空走时间
空运行和空走时间是指在加工过程中刀具离开工件或即将开始切削前的移动时间。这包括刀具路径中的无用移动和在程序段之间的过渡移动。优化措施包括重新规划刀具路径,确保刀具在到达新的切削位置前尽可能减少移动距离;使用正确的插补指令,避免不必要的圆弧移动;以及利用子程序来简化重复的刀具动作。合理安排加工顺序和使用循环指令可以减少程序的复杂性和运行时间。
## 提高切削效率
### 选择合适的切削参数
选择合适的切削参数是提高加工效率和加工质量的关键。切削参数包括切削速度、进给率、切削深度和进给步距
```
0
0
相关推荐
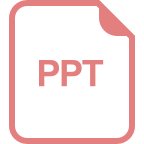
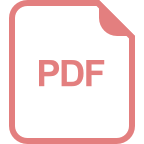
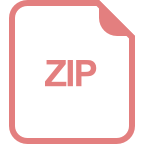
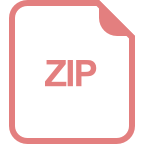
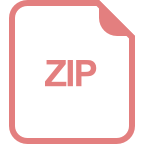
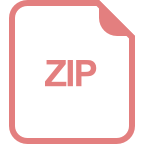
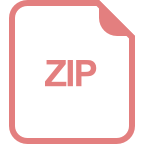
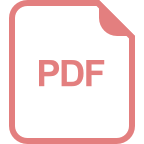