机器设备评估:维护与操作参数的最佳实践指南
发布时间: 2025-01-05 23:47:41 阅读量: 9 订阅数: 17 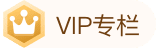
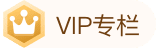
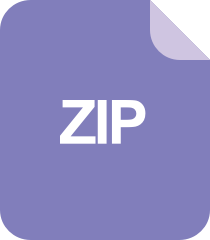
MachineLearningInAction:机器学习实战源代码管理
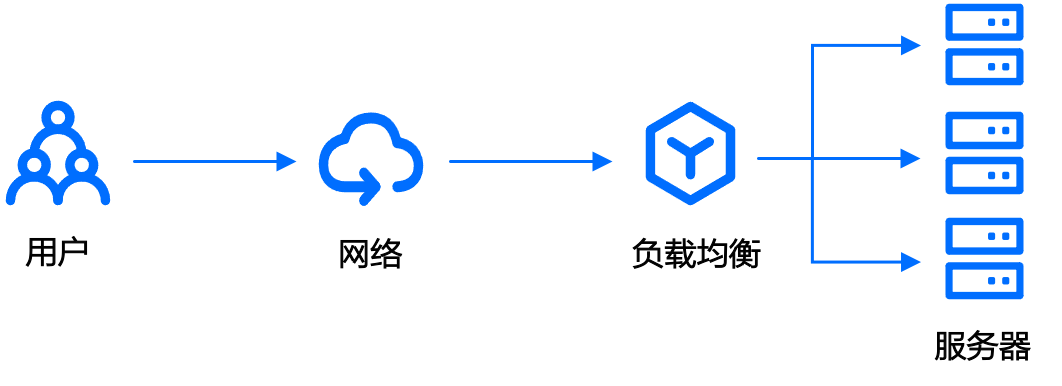
# 摘要
在现代工业生产中,机器设备的评估、维护、操作和故障处理是确保设备稳定运行和生产效率的关键环节。本文系统地探讨了机器设备评估的重要性及其基本概念,详细论述了维护策略的制定与执行,包括预防性与预测性维护的区别、维护周期的确定、实践中的维护技巧,以及维护效果的评估与优化。同时,本文还介绍了操作参数的设定与监控,故障诊断与应急响应,以及设备评估软件工具的应用。通过案例研究,本文分析了不同行业在设备评估方面的实践,并预测了人工智能、物联网和大数据技术在未来机器设备评估中的应用趋势,为相关领域的技术进步和战略决策提供了参考。
# 关键字
设备评估;维护策略;操作参数;故障诊断;应急响应;软件工具;人工智能;物联网;大数据技术
参考资源链接:[机器设备评估常用数据与参数.pdf](https://wenku.csdn.net/doc/6ep56jup3a?spm=1055.2635.3001.10343)
# 1. 机器设备评估的重要性与基本概念
在现代工业生产过程中,机器设备是企业运营的基石。设备评估作为维护管理的核心环节,对确保设备长期稳定运行、延长使用寿命以及保障生产安全具有不可或缺的作用。本章将探讨设备评估的基本概念、重要性,以及评估流程,为后续章节关于维护策略制定、操作参数优化和故障诊断等内容的深入分析奠定基础。
首先,我们必须理解机器设备评估的本质。评估是一个多方面、多维度的过程,它不仅涉及到设备的技术状态,还包括其潜在的经济价值和环境影响。对于企业来说,通过对设备进行定期的评估,可以及时发现潜在问题,预防可能的生产故障,从而降低运营成本,提高生产效率和质量保证。
接下来,我们将详细探讨设备评估的重要性,这包括对设备性能的提升、维护成本的降低以及生产计划的准确制定等方面的贡献。通过对比设备在不同工作条件下的性能,管理者能够做出更加明智的决策,比如是否更换旧设备、调整维护计划或是进行生产流程的优化。
然后,我们会介绍设备评估的基本概念,包括评估的标准和方法。设备的技术性能评估通常涉及性能指标的测量,如精度、速度、载荷能力和可靠性等。同时,经济评估将考量设备的投入产出比、折旧情况以及维护费用等经济因素。此外,评估还应考虑环境因素,如设备对环境的影响、是否符合环保法规以及节能减排的潜力。
总结来说,本章的内容旨在提供一个全面而基础的设备评估框架,为企业开展有效的设备管理提供理论基础和实践指导。在后续章节中,我们将深入分析各种评估策略和应用案例,使读者能够全面掌握设备评估的精髓。
# 2. ```
# 维护策略的制定与执行
## 2.1 设备维护理论基础
### 2.1.1 预防性维护与预测性维护的区别
在设备的维护管理中,预防性维护(Preventive Maintenance, PM)和预测性维护(Predictive Maintenance, PdM)是两种核心策略,它们都旨在减少设备故障的发生,提高设备的运行效率和生产企业的经济效益。两者的主要区别在于维护的时机和方法。
预防性维护是定期对设备进行检查、润滑、更换磨损部件等操作,以减少设备故障的发生,通常按照预先设定的时间间隔执行,不考虑设备的实际运行状况。它的优点是简便易行,能够较为系统地保证设备的运行状态。然而,这种策略可能会导致过多或过少维护的情况发生,因为它是基于时间而非设备实际工作状况的。
预测性维护则利用先进的监测技术实时跟踪设备的运行状态,通过分析设备的振动、温度、压力等指标来判断设备是否处于正常运行状态,以此来确定是否需要进行维护。预测性维护的优点在于它可以根据设备的实际状况来决定维护时机,从而优化维护成本并延长设备的使用寿命。
### 2.1.2 维护周期的确定方法
确定设备维护周期是维护管理中非常重要的一个环节,不同的设备和不同的维护方法,其周期的确定方法也有所差异。一般来说,确定维护周期有以下几种方法:
1. 设备制造商推荐:设备在出厂时,制造商通常会提供一个基于设备性能和设计寿命的推荐维护周期。这些周期往往是基于大量的测试和历史数据,因此是确定维护周期的一个良好起点。
2. 运行数据分析:通过对设备运行数据的收集和分析,包括运行时间、负载条件、维护历史等,可以进一步细化并优化维护周期。这种方法通常需要使用数据分析软件来支持。
3. 经验法则:在没有足够数据支持的情况下,可以根据经验对维护周期进行设定。例如,对于某些设备可以根据实际运行情况和行业通用标准,设定一个经验周期。
4. 条件监测技术:对于一些高价值的设备,可以采用如振动分析、温度监测、油液分析等条件监测技术来动态地评估设备的运行状态,从而更加精准地决定维护周期。
在制定维护策略时,企业应综合考虑上述方法,结合自身的生产需求和资源状况,制定出适合自身发展的维护周期。
## 2.2 实践中的维护技巧
### 2.2.1 常用的维护工具和技术
在维护实践中,有多种工具和技术可以被采用来保证设备的正常运行和延长其使用寿命。以下是几种常用的工具和技术:
1. **润滑技术:** 润滑对于防止设备磨损和降低能耗至关重要。合理使用润滑剂和润滑方式能够提高设备运行效率和可靠性。
2. **非破坏性检测(NDT):** NDT 包括磁粉检测、渗透检测、超声波检测等方法,用于评估设备材料的完整性而无需损坏设备。
3. **条件监测工具:** 如振动分析仪、红外热像仪等,用于监测设备运行状态和识别潜在故障。
4. **维护管理系统软件:** 使用维护管理系统(如 CMMS 或 EAM)能够帮助企业自动化维护流程,提高维护工作的计划性和效率。
5. **可靠性中心维护(RCM):** RCM 是一种综合性的维护管理策略,它着重于通过评估设备的潜在故障模式来确定维护需求。
6. **5S 管理方法:** 5S 方法强调整理(Seiri)、整顿(Seiton)、清扫(Seiso)、清洁(Seiketsu)和素养(Shitsuke),是实现工作环境和设备维护的系统化和标准化。
使用这些工具和技术可以帮助维护人员高效准确地完成维护工作,同时通过持续优化维护流程来提升企业的生产效率。
### 2.2.2 维护过程中的问题分析与解决
维护过程中的问题多种多样,从规划不当到执行过程中的意外状况,及时而有效的诊断和解决这些问题对于保障设备的正常运行至关重要。以下是维护过程中可能遇到的一些问题以及相应的解决方法:
1. **维护规划与资源不足:** 这通常会导致维护工作延期,影响到生产的正常进行。解决这一问题需要通过维护管理系统进行资源优化和调度,合理安排维护计划。
2. **维护执行过程中的意外故障:** 这种问题可能由于维护人员的疏忽或者备件的短缺所导致。解决方法包括对维护人员进行定期培训以及建立完备的备件库存管理系统。
3. **重复性故障:** 如果设备频繁出现同一问题,那么问题可能出在设计或操作上。这时需要对设备进行彻底的检查,并根据检查结果进行设计调整或操作流程的优化。
4. **维护成本过高:** 过高的维护成本往往因为维护方法不恰当或预防性维护执行不足。采用预测性维护和数据分析工具,可以减少不必要的维护,降低成本。
5. **维护信息孤岛:** 多个系统和部门间信息传递不畅会导致维护决策失误。解决这一问题需要建立统一的信息平台,实现信息共享和数据分析。
## 2.3 维护效果评估与优化
### 2.3.1 设备运行数据的收集和分析
设备的运行数据是评估维护效果的关键,这包括设备的运行时长、负载、能耗、故障率、停机时间等。通过有效的数据收集和分析,企业可以准确把握设备运行状况,发现潜在问题,并据此制定维护策略。以下是进行设备数据收
```
0
0
相关推荐







