【半导体制造流程深度剖析】:光刻技术的关键5步揭秘
发布时间: 2024-12-20 21:34:47 阅读量: 4 订阅数: 4 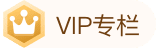
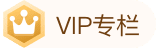
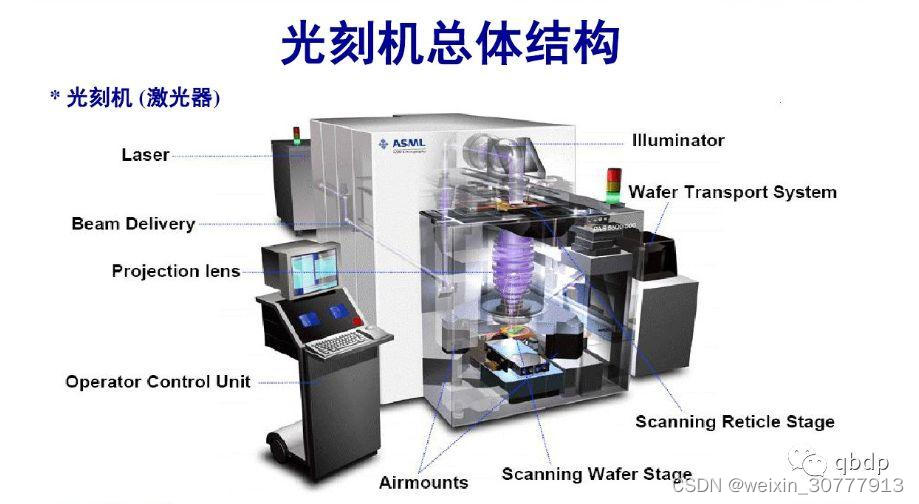
# 摘要
光刻技术是现代半导体制造业的核心工艺,它涉及将复杂的电路图案精确地转移到硅片上。本文从理论基础到实际应用,详细介绍了光刻技术在半导体制造中的作用和关键流程。通过分析光刻过程的物理化学原理、关键材料和设备,以及精度控制方法,深入探讨了光刻技术的实践挑战和创新。本文还探讨了先进光刻技术,如极紫外光刻(EUV)和多重图案化技术的应用,并讨论了光刻技术的未来趋势,包括摩尔定律的挑战和新型光刻技术的探索。
# 关键字
光刻技术;半导体制造;物理化学原理;精度控制;先进光刻;摩尔定律
参考资源链接:[ASML 2007光刻工艺4x/5x 6英寸光罩操作手册](https://wenku.csdn.net/doc/6412b718be7fbd1778d49114?spm=1055.2635.3001.10343)
# 1. 光刻技术在半导体制造中的作用
半导体产业被誉为现代工业的“心脏”,而光刻技术正是这心脏的核心动力。光刻技术不仅关系到芯片的集成度和性能,还直接决定了整个半导体制造工艺的先进程度和成本效益。随着摩尔定律的推动,光刻技术不断突破物理和化学的界限,将集成电路的精细化程度推向新高。通过本章,我们将探讨光刻技术是如何在芯片制造中发挥作用,以及它对整个行业带来的深远影响。
# 2. 光刻技术的理论基础
### 2.1 光刻过程的物理和化学原理
#### 2.1.1 光学成像与衍射极限
光刻技术的核心在于光学成像,通过曝光和显影步骤在半导体晶片上转移电路图案。这一过程涉及到复杂的物理原理,特别是衍射极限的概念。衍射极限是光学成像系统可以分辨的最小特征尺寸,它由光波的波长和光学系统的数值孔径决定。
一个基本的物理公式来描述衍射极限是:
```
d = k * λ / NA
```
其中,`d` 代表可分辨的最小特征尺寸,`k` 是工艺常数,`λ` 是曝光光源的波长,`NA` 是光学系统的数值孔径。数值孔径的提高或使用更短波长的光源能缩小特征尺寸,这也是为什么光刻技术趋向于使用极紫外光(EUV)的原因之一。
**参数解释:**
- `k`:此因子代表工艺过程中的误差容限和光源的相干性。对于先进的光刻技术,`k` 值可接近 0.25。
- `λ`:传统光刻技术使用的光源波长约为 193 纳米,而 EUV 光刻技术使用波长约为 13.5 纳米的光源。
- `NA`:数值孔径是一个无单位的数,它取决于成像系统的几何结构和介质(如空气或水)的折射率。数值孔径的提高可以增强系统的分辨率,但也增加了制造难度。
在实际操作中,提高分辨率并不只是简单地减小波长和增加数值孔径。还需要考虑光学系统的整体设计、光源的相干性,以及光刻胶层的化学性质等因素。
#### 2.1.2 光敏材料的反应机制
光刻胶(Photoresist)是光刻过程中至关重要的化学材料,它的基本功能是在曝光过程中发生化学变化,从而允许或阻止后续的刻蚀过程。光敏材料的主要类型包括负性和正性光刻胶,它们对光的反应机制不同。
负性光刻胶在曝光区域发生交联反应,使得这些区域变得难以溶解于显影剂;而正性光刻胶则在曝光区域发生降解反应,使得这些区域在显影时更容易被溶解。
**逻辑分析:**
光刻胶的化学反应通常涉及以下步骤:
1. **曝光**:光束通过掩模照射到涂覆有光刻胶的硅片上,根据掩模图案投射光束。
2. **显影**:显影剂被应用于硅片上,未曝光的正性光刻胶区域以及曝光的负性光刻胶区域会从硅片上被移除,形成负图案。
3. **后处理**:显影后,硅片上的图案可进一步用于刻蚀过程,去除未被光刻胶覆盖的硅片区域。
### 2.2 光刻技术的关键材料与设备
#### 2.2.1 光刻胶的种类与特性
光刻胶根据不同的需求可以分为多种类型,其中最常见的是正性光刻胶和负性光刻胶。
**参数说明:**
- **正性光刻胶:** 这类光刻胶在曝光后所受区域会在显影过程中被移除,留下负向图像。其优点是分辨率高、灵敏度好,缺点是在高温和强光照条件下稳定性较差。
- **负性光刻胶:** 负性光刻胶在曝光区域变得不易溶解,产生正向图像。这类光刻胶的稳定性高、抗蚀刻能力强,但分辨率较正性胶低。
**代码块示例:**
```mermaid
graph TD;
A[光刻胶分类] --> B[正性光刻胶]
A --> C[负性光刻胶]
B --> D[高分辨率]
B --> E[良好灵敏度]
B --> F[稳定性较差]
C --> G[高稳定性]
C --> H[强抗蚀刻能力]
C --> I[分辨率较低]
```
#### 2.2.2 光刻设备的发展与分类
光刻机是执行光刻工艺的设备,其技术进步推动了整个半导体工业的发展。依据光源波长和分辨率的不同,光刻设备可分为深紫外光(DUV)、极紫外光(EUV)和多重图案化等几种类型。
**逻辑分析:**
- **DUV光刻机** 使用深紫外光源(通常是 193 纳米的 ArF 激光),能够达到几十纳米的特征尺寸。
- **EUV光刻机** 使用极紫外光源(13.5 纳米波长),适用于更先进的制程节点,实现单纳米的特征尺寸。
- **多重图案化设备** 是指将原本超出光学分辨能力的图案通过多次曝光和刻蚀,间接制造出来。
**代码块示例:**
```mermaid
graph TD;
A[光刻设备分类] --> B[DUV光刻机]
A --> C[EUV光刻机]
A --> D[多重图案化设备]
B --> E[典型波长193nm]
B --> F[特征尺寸几十纳米]
C --> G[典型波长13.5nm]
C --> H[特征尺寸单纳米级别]
D --> I[间接制造高密度图案]
D --> J[提升制程节点的可行性]
```
### 2.3 光刻过程中的精度控制
#### 2.3.1 对准和曝光技术
为了确保电路图案正确地转移到硅片上,光刻过程必须通过精密对准和曝光技术来控制。对准技术是指如何精确地将掩模上的图案对准到硅片上已经存在的图案。
在现代光刻机中,这一过程包括使用特殊的光学标记和先进的对准传感器。而曝光技术的发展则从单片掩模曝光发展到扫描曝光,以应对更大尺寸的晶片和提高生产效率。
**逻辑分析:**
- **对准技术**:现代对准系统可以达到亚纳米级的对准精度,关键在于对准标记的设计和对准算法的优化。
- **曝光技术**:扫描曝光通过相对移动掩模和晶片来实现,它允许使用更大的掩模和提高吞吐量,而先进的光源控制技术则可以提高曝光的均匀性和准确性。
**代码块示例:**
```python
# Python示例代码:对准和曝光优化算法的简化模拟
class LithographyAlignment:
def align(self, existing_marks, new_marks):
# 对准算法,假设是一个简单的匹配过程
pass
def exposure(self, mask, wafer):
# 模拟曝光过程
pass
# 初始化设备
litho_machine = LithographyAlignment()
# 模拟对准
aligned = litho_machine.align(existing_marks, new_marks)
# 模拟曝光
litho_machine.exposure(mask, wafer)
```
#### 2.3.2 环境因素对光刻质量的影响
光刻过程非常敏感,受多种环境因素的影响,如温度、湿度、化学气体成分以及振动等。严格控制这些因素是保证光刻质量的关键。
**逻辑分析:**
- **温度和湿度**:环境中的温度和湿度变化会对光刻胶和硅片的热膨胀产生影响,从而影响最终图案的质量。因此需要维持恒温恒湿的生产环境。
- **化学气体成分**:光刻胶的反应需要特定的化学环境,任何化学杂质都可能影响其反应效果。
- **振动**:设备的微小振动也可能导致光刻图案的错位或模糊,因此精密光刻设备通常配备有减震系统。
**代码块示例:**
```mermaid
graph LR;
A[环境控制因素] --> B[温度控制]
A --> C[湿度控制]
A --> D[化学气体控制]
A --> E[减震系统]
B --> F[热膨胀控制]
C --> G[光刻胶稳定性]
D --> H[化学反应效率]
E --> I[图案定位精度]
```
以上章节内容为光刻技术理论基础的详细介绍,包括了物理化学原理、关键材料与设备,以及精度控制的各个方面。通过深入分析这些主题,读者可以更好地理解光刻技术在半导体制造过程中的重要性和挑战性。
# 3. 光刻技术的关键五步流程详解
光刻技术是半导体制造中的核心步骤,每一步都至关重要。本章将深入探讨光刻技术的关键五步流程,并对每一步骤进行详细的解析。我们将从表面准备与光刻胶涂覆开始,进而分析曝光与显影过程,最后总结硬刻蚀与清洗的重要性。
## 3.1 表面准备与光刻胶涂覆
在光刻过程中,衬底表面的准备和光刻胶的涂覆是极其关键的步骤。这一步骤的目的是为了确保光刻胶能够均匀地涂覆在干净且光滑的衬底表面,以便后续的曝光过程能够精确地转移图案。
### 3.1.1 衬底清洁与脱水处理
在光刻开始之前,必须对半导体衬底表面进行彻底的清洁和脱水处理。这个步骤的目的是去除任何可能影响光刻胶附着的污染物和自然氧化层。常见的清洁方法包括使用化学溶剂、等离子体清洗以及超临界流体清洗等。
```plaintext
// 化学溶剂清洁示例代码块
清洗液: H2SO4 + H2O2
比例: 3:1
温度: 120°C
时间: 10分钟
```
化学溶剂清洁的逻辑分析:
在上述代码块中,我们使用硫酸(H2SO4)和过氧化氢(H2O2)的混合溶液进行清洗。这种混合液通常被称为“piranha”清洁液,能够有效地去除有机物和金属污染。需要注意的是,在操作过程中必须遵守严格的安全措施,因为这种混合液具有很强的腐蚀性。
脱水处理通常使用氮气(N2)或者热板来完成,以确保衬底表面干燥无水。
### 3.1.2 光刻胶涂布技术
光刻胶(Photoresist)是光刻过程中的关键材料,它对光敏感,并能够在化学处理后保留或去除图案。涂覆光刻胶的方法多种多样,包括旋转涂覆、喷涂、浸涂等。其中,旋转涂覆是工业上最常用的方法。
```plaintext
// 旋转涂覆技术示例代码块
旋转速度: 2000转/分钟
加速时间: 5秒
持续时间: 30秒
```
旋转涂覆技术逻辑分析:
上述代码块展示了旋转涂覆过程中的一些基本参数。旋转涂覆利用离心力将光刻胶均匀地涂布在衬底表面。速度快慢、加速度以及涂覆时间都会直接影响光刻胶的厚度和均匀性。太快会导致光刻胶向边缘流失而太慢则无法达到所需的均匀度。
## 3.2 曝光与显影过程
曝光和显影是形成最终电路图案的关键步骤。曝光是使用光源照射涂覆有光刻胶的衬底,而显影则是使用特定的溶剂去除曝光后的光刻胶部分。
### 3.2.1 曝光过程的精确控制
曝光过程中,光源的选择和曝光时间的控制至关重要。常用的光源包括深紫外光(DUV)、极紫外光(EUV)和电子束(EB)。曝光时间的长短取决于光刻胶的类型和所需的图案精度。
```plaintext
// 曝光机操作示例代码块
光源类型: 深紫外光
曝光剂量: 10 mJ/cm²
曝光时间: 15秒
```
曝光机操作逻辑分析:
在该代码块中,我们指定了使用深紫外光作为光源,并设定了曝光剂量和时间。曝光剂量需要根据光刻胶的感光特性来设定,以确保曝光后图案的精确性。曝光时间过长或过短都会影响图案的质量。
### 3.2.2 显影技术及其对电路图案的影响
显影过程需要将未曝光的光刻胶部分溶解,从而实现图案转移。显影液的选择取决于光刻胶的类型,例如,对于正性光刻胶,显影液通常是碱性的。
```plaintext
// 显影液配比示例代码块
显影液: TMAH(四甲基氢氧化铵)
浓度: 2.38%
温度: 22°C
时间: 60秒
```
显影液配比逻辑分析:
在显影过程中,显影液的浓度和温度都会对显影速度和质量产生影响。过高的温度和浓度可能造成过度显影,而过低则会导致显影不完全。时间控制也是关键,太短可能无法完全移除未曝光的部分,而时间过长则可能导致图案边缘模糊。
## 3.3 硬刻蚀与清洗
硬刻蚀是将光刻胶上的图案转移到半导体衬底上的过程。而清洗则是移除残留的光刻胶和刻蚀后的副产品。
### 3.3.1 硬刻蚀技术的选择与应用
硬刻蚀技术包括等离子体刻蚀、反应离子刻蚀(RIE)和湿法刻蚀等。选择何种技术通常取决于所需图案的精度、成本和生产效率。
```plaintext
// 反应离子刻蚀(RIE)示例代码块
气体种类: CF4
气流量: 100 sccm
功率: 150 W
时间: 30秒
```
反应离子刻蚀(RIE)逻辑分析:
RIE是一种等离子体刻蚀技术,它通过控制气体种类、气流量、功率和时间来实现对衬底材料的选择性刻蚀。这种精确控制允许创建出复杂的三维图案。
### 3.3.2 清洗过程的重要性与方法
清洗过程是为了去除硬刻蚀后在表面残留的光刻胶、刻蚀副产品和任何可能影响设备性能的微粒。常用的清洗方法包括等离子体清洗、超临界流体清洗和化学溶剂清洗。
```plaintext
// 化学溶剂清洗示例代码块
清洗剂: N-Methyl-2-pyrrolidone (NMP)
温度: 150°C
时间: 30分钟
```
化学溶剂清洗逻辑分析:
NMP是一种常用的化学溶剂清洗剂,尤其适用于去除硬质光刻胶。通过加热使清洗剂温度升高,可以提高溶解力,从而在规定时间内有效清除残胶。但是需要注意的是,化学溶剂清洗可能对环境产生污染,因此需要妥善处理。
在本章节中,我们详细探讨了光刻技术的五步关键流程,并通过示例代码块、参数设置和逻辑分析的方式,揭示了每个步骤背后的技术细节。这些信息将为理解更高级的光刻技术打下坚实的基础,同时也为可能出现的问题提供了解决的方向和方法。在接下来的章节中,我们将进一步探索光刻技术的实践挑战以及未来的发展趋势。
# 4. 光刻技术的实践挑战与创新
### 4.1 先进光刻技术的实践应用
光刻技术作为半导体制造的核心工艺之一,其发展速度与创新应用直接影响着整个集成电路产业的进步。随着摩尔定律的不断推进,传统的光刻技术正面临着分辨率的物理限制。为突破这一极限,先进光刻技术,如极紫外光刻(EUV)和多重图案化技术,逐渐成为业界的关注焦点。
#### 4.1.1 极紫外光刻(EUV)技术的应用
极紫外光刻(EUV)技术是一种使用13.5纳米波长的极紫外光进行光刻的技术,它能有效突破传统193纳米波长光刻的衍射极限。EUV技术的使用,使得单次曝光可以制造更细小的电路图案,从而减少多重图案化的需要,极大地提高了生产效率。
```mermaid
graph LR
A[设计集成电路图案] -->|数据转换| B[图案生成器]
B -->|EUV光源| C[光刻机]
C -->|EUV曝光| D[光敏材料反应]
D -->|显影| E[形成电路图案]
```
#### 代码解释:
- `设计集成电路图案`:设计师通过EDA工具完成电路图案设计并将其转换为光刻机可以识别的数据格式。
- `图案生成器`:在EUV系统中,图案生成器通常指掩模或反射镜,用于控制光线传播路径。
- `光刻机`:指利用EUV光源进行光刻的设备。
- `EUV曝光`:极紫外光源照射在光敏材料上,使得材料发生化学反应。
- `显影`:将反应后的光敏材料中未曝光的部分溶解掉,露出图案。
#### 参数说明:
- `EUV光源`:波长为13.5纳米,具有极高的分辨率和穿透力。
- `光敏材料`:能够对EUV波长的光敏感,常用的是化学放大光刻胶。
### 4.1.2 多重图案化技术的发展
多重图案化技术(Multiple Patterning Lithography, MPL)是一种通过多次光刻和刻蚀步骤来形成一个图案的工艺。该技术允许193纳米浸没式光刻技术在更小的节点上继续使用,通过精细地控制每一步的图案和对齐,可以实现更小尺寸的电路制造。
### 4.2 光刻技术面临的问题与应对策略
#### 4.2.1 光刻技术中的缺陷管理
随着技术节点的不断缩小,光刻过程中的缺陷管理变得更加复杂。缺陷不仅来源于光刻胶和掩模等材料,还可能由光刻设备的不稳定性引起。因此,对于缺陷的检测、分类和修复成为保证光刻质量的关键环节。
#### 4.2.2 制程整合与设备协同优化
光刻技术与前后制程的整合要求越来越高,需要实现不同设备间参数的精准对接和协同优化。例如,光刻设备与刻蚀设备之间必须有高度的协同,才能确保图案转移的一致性和精确性。
### 4.3 光刻技术的未来趋势与发展
#### 4.3.1 摩尔定律与光刻技术的极限挑战
摩尔定律预测了集成电路中晶体管数量的指数增长趋势,这对光刻技术的分辨率提出了更高的要求。然而,随着光刻波长接近物质的原子尺度,传统的光学光刻方法已经接近物理极限。
#### 4.3.2 新型光刻技术的探索与研究
为了克服这一挑战,研究人员正在探索新型光刻技术,如电子束直接写入、纳米压印光刻和X射线光刻等。这些技术在未来可能会成为半导体制造中的主流,但它们目前还面临着成本、速度和可行性等实际问题。
本章节内容是对光刻技术的实践挑战和创新方向进行了深入探讨,同时以EUV技术和多重图案化技术为实践应用案例,分析了光刻技术目前面临的主要问题,并展望了光刻技术的未来发展方向。通过技术图表、代码块和逻辑分析,本章为读者提供了一个全面深入的技术视角。
# 5. 光刻技术案例研究与分析
## 5.1 光刻技术在芯片制造中的实际案例
### 5.1.1 高性能计算芯片的光刻过程
高性能计算(HPC)芯片对光刻技术提出了极高的要求,因为这些芯片通常具有更高的晶体管密度和更小的特征尺寸。以7纳米工艺为例,EUV光刻技术成为了实现这一工艺的关键。EUV光刻利用波长为13.5纳米的极紫外光,可以实现更小的特征尺寸和更高的图案精度。
在实际生产中,7纳米工艺的光刻过程涉及以下步骤:
1. **光刻胶涂覆**:首先,将带有抗蚀剂的衬底进行涂覆,确保抗蚀剂层厚度均匀。
2. **曝光**:使用EUV光源,对涂有光刻胶的衬底进行曝光。这一过程中,需要极高的精度来控制光源的位置和能量。
3. **显影和刻蚀**:曝光后,通过显影过程移除曝光区域的光刻胶,随后通过刻蚀过程将图案转移到衬底上。
4. **测量和检查**:使用扫描电子显微镜(SEM)等工具对图案进行测量,确保特征尺寸符合设计要求,并检查缺陷。
通过上述步骤,光刻技术能够实现复杂且高精度的电路图案,为高性能计算芯片的生产提供技术保障。
### 5.1.2 移动设备芯片的光刻优化实例
随着移动设备的普及,对于移动设备中使用的芯片,低功耗和高集成度成为了设计的关键。以5纳米芯片为例,光刻技术的优化集中体现在能效和成本控制上。
在这一芯片的光刻过程中,优化措施通常包括:
1. **多重图案化技术**:使用多重图案化技术,可以在一定程度上绕开光刻分辨率的限制,实现在更小的芯片上刻蚀更复杂的电路图案。
2. **工艺集成优化**:通过优化工艺流程,例如,缩短曝光时间,提高生产效率,降低功耗,同时减少了生产成本。
3. **缺陷管理**:通过提高光刻胶和设备的性能,减少缺陷率,提高芯片良率。
优化后的光刻技术不仅满足了移动设备芯片低功耗和高集成度的需求,还降低了生产成本,提高了市场竞争力。
## 5.2 光刻技术的创新应用分析
### 5.2.1 3D集成电路的光刻技术应用
随着集成电路的发展,3D集成电路(3D IC)技术逐渐成为行业热点。3D IC通过堆叠多层芯片以增加功能密度,对光刻技术的挑战在于如何实现层与层之间的精确对准和连接。
在3D IC的生产中,光刻技术应用的关键环节包括:
1. **通过硅孔(TSV)技术**:在芯片制造过程中,使用光刻技术形成垂直硅通孔,这些孔可以作为芯片内部和不同层次之间的连接通道。
2. **多层对准技术**:在堆叠多个芯片层次时,需要精确对准,以保证电路的连贯性和可靠性。
3. **高密度互连(HDI)技术**:为了实现高密度的互连,光刻技术必须能够刻蚀更细小的特征尺寸。
这些技术的创新应用使得3D IC可以更加有效地利用空间,实现更高性能。
### 5.2.2 纳米级光刻技术的未来展望
随着摩尔定律的不断推进,光刻技术正逼近其物理极限。纳米级光刻技术的研发正在成为行业的重要发展方向。包括纳米压印光刻(NIL)、自组装单层(SAM)等技术都为未来的纳米级光刻提供了新的可能性。
对这些新兴技术的研究焦点包括:
1. **自组装单层技术**:通过化学方法形成有序的分子层,这些分子层可以作为自然的光刻模板,以实现高精度的图案转移。
2. **纳米压印光刻技术**:利用模具直接压印图案到抗蚀剂上,这种方法能够突破传统光刻技术的分辨率限制。
未来纳米级光刻技术的发展将可能为半导体行业带来革命性的变化,为更高密度、更低功耗的芯片制造提供技术基础。
0
0
相关推荐
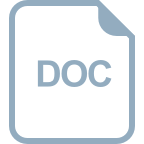
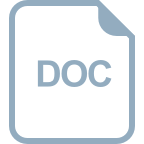
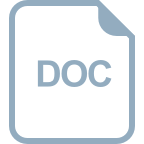
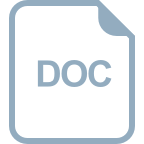
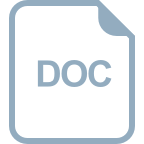
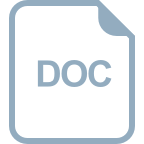