Minitab 17故障模式与影响分析(FMEA)实用指南
发布时间: 2024-12-16 11:00:15 阅读量: 5 订阅数: 16 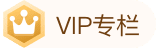
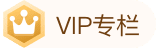
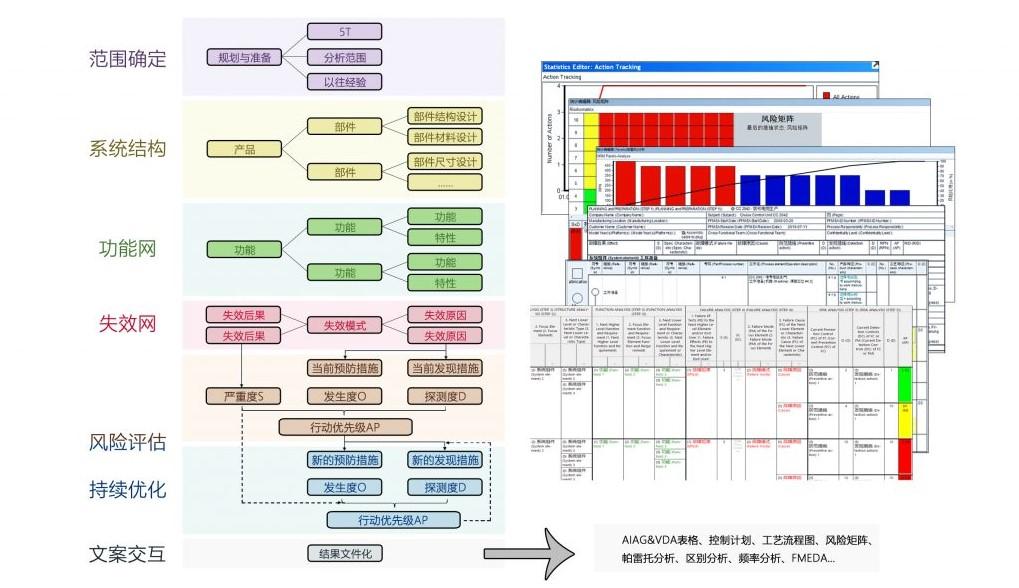
参考资源链接:[Minitab 17入门:数据处理与统计分析教程](https://wenku.csdn.net/doc/60uth6sng3?spm=1055.2635.3001.10343)
# 1. Minitab 17与故障模式与影响分析(FMEA)概述
## 1.1 FMEA的定义和背景
故障模式与影响分析(FMEA)是一种系统化的、前瞻性的质量工具,用于评估产品设计或制造过程中潜在的故障模式及其对客户的影响。FMEA帮助组织识别和消除故障或风险,从而提升产品的可靠性和安全性。自上世纪60年代首次被美国国家宇航局(NASA)采用以来,FMEA在全球范围内被广泛应用于工程、制造、服务等多个行业中。
## 1.2 FMEA的目标和价值
FMEA的总体目标是通过提前识别和处理潜在的故障模式来预防产品故障,减少维修成本,并提高客户满意度。它使得风险评估更加客观和系统化,进而能够制定出更为精确的风险缓解措施。实施FMEA可增强团队对故障模式影响的理解,为持续改进提供数据支持,并在企业内建立风险意识文化。
## 1.3 FMEA在软件分析中的应用
随着质量问题分析技术的数字化和软件化,Minitab 17等统计软件的引入,使得FMEA的执行和分析过程更加高效和精确。在Minitab中,用户可以通过内置的工具和模板轻松地导入和分析数据,进行风险评估和报告输出,从而为质量控制和产品改进提供了强有力的支持。下一章将深入探讨FMEA的基础知识。
# 2. 故障模式与影响分析(FMEA)基础
## 2.1 FMEA的核心概念与目标
### 2.1.1 FMEA的定义和背景
故障模式与影响分析(Failure Mode and Effects Analysis, FMEA)是一种预防性的、系统性的设计评估工具。它的目的是识别产品或过程设计中的潜在故障模式,评估故障的潜在影响,进而采取措施,降低或消除故障发生的可能性或严重性。FMEA 最初是由美国国家航空航天局(NASA)在20世纪60年代发展起来的,随着其在航空航天领域的成功应用,FMEA 迅速传播到其他行业,如汽车、制药、医疗器械和消费品等。
FMEA 的核心理念是通过团队协作的方式来识别问题。它要求一个跨学科的团队一起工作,考虑产品的每个组件、每个组件的每个故障模式、每个故障模式的潜在原因以及影响。通过这种结构化的风险评估方法,可以早期发现设计上的问题,并在问题成形前采取措施。
### 2.1.2 FMEA的目标和价值
FMEA 的主要目标可概括为以下几点:
1. **识别潜在的故障模式**:通过深入分析产品设计和制造过程中的每一个细节,FMEA 能够揭示那些可能导致产品功能障碍的潜在故障。
2. **分析故障影响**:每一种故障模式都会被评估其对产品性能的影响,以及这些影响的严重程度。
3. **确定风险优先级**:FMEA 通过风险优先级数(Risk Priority Number, RPN)来量化风险,从而确定哪些风险需要优先处理。
4. **促进团队合作**:FMEA 过程鼓励不同部门和不同背景的人员合作,从而在早期阶段就识别并解决问题。
5. **持续改进**:FMEA 是一个持续的过程,不仅在产品设计阶段使用,而且在整个产品生命周期中不断更新和改进。
FMEA 的价值在于它能够通过结构化的方式提前发现问题,减少后期的返工和维修成本,提升产品质量,最终使企业能够更好地满足客户需求,增强市场竞争力。
## 2.2 FMEA的类型与应用领域
### 2.2.1 设计FMEA(DFMEA)与过程FMEA(PFMEA)
FMEA 有两个主要类型,分别是设计FMEA(Design FMEA, DFMEA)和过程FMEA(Process FMEA, PFMEA),它们应用在不同阶段的分析中:
1. **设计FMEA(DFMEA)**:这个类型的FMEA关注的是产品设计阶段可能出现的故障。它涉及评估设计的各个部分,包括材料选择、组件交互和使用条件,来确定可能造成产品功能失效的故障模式。
2. **过程FMEA(PFMEA)**:PFMEA 则关注制造或服务过程中可能出现的故障。它包括评估产品从原材料到成品的整个生产流程,以发现过程中的潜在问题和缺陷。
DFMEA 和 PFMEA 都需要团队的共同努力来完成,通常会包括设计师、工程师、生产人员、质量控制人员等。尽管两者关注的焦点不同,但它们都遵循相同的分析流程和原则,以确保产品或服务的质量和可靠性。
### 2.2.2 FMEA在不同行业的应用案例
FMEA 的应用领域非常广泛,其核心价值在于帮助不同行业的企业识别风险,提高产品和服务的质量。以下是一些FMEA应用的行业案例:
1. **航空航天**:FMEA 在航空航天行业中最初被使用,目的是确保飞行器及其部件的安全和可靠性。在设计复杂系统时,如火箭发动机,FMEA 能够识别出可能导致灾难性后果的潜在故障。
2. **汽车制造**:汽车制造商利用PFMEA 来优化生产线,确保每个生产环节的质量和效率。DFMEA 则用于新车型的设计阶段,以提高车辆的安全性和耐用性。
3. **医疗设备**:在医疗设备行业,FMEA 被用来保证设备的安全性和有效性。对于救命设备,如心脏起搏器,FMEA 分析尤为重要。
4. **电子消费品**:电子产品制造商使用FMEA 来确保产品设计的可靠性和用户的安全。例如,在智能手机的制造中,FMEA 可以帮助识别电池故障和充电问题等。
FMEA 的应用案例证明了其在多种工业标准中的重要性,如ISO 9001、IATF 16949(汽车行业)和ISO 14971(风险管理在医疗设备中的应用)。通过案例分析,我们可以看到FMEA 如何在不同行业中适应并发挥其功能。
## 2.3 FMEA的基本流程
### 2.3.1 FMEA分析步骤概览
进行FMEA分析时,通常遵循以下步骤:
1. **团队组建**:组建跨职能团队,确保各个部门的专业知识和经验都能被充分利用。
2. **范围和目标确定**:明确分析的范围,比如特定的产品、部件或过程。同时,设定分析的目标,比如预防故障的发生或者优化现有设计。
3. **数据收集与信息整理**:收集所有相关的设计、过程和操作信息,包括制造流程、使用条件、历史故障数据等。
4. **故障模式识别**:列出产品的每个组件或过程的每一个可能故障模式。
5. **影响评估**:分析每一个故障模式可能带来的影响,包括直接和间接的影响。
6. **风险分析**:计算RPN,这个数值是由故障发生的概率、严重程度和检测难易程度的乘积决定的。
7. **风险优先级排序**:根据RPN值对所有潜在故障进行优先级排序。
8. **风险处理措施制定**:针对高优先级的故障模式,制定相应的风险缓解措施。
9. **实施监控和控制**:将风险缓解措施实施到设计或过程中,并持续监控这些措施的有效性。
10. **文档记录和报告**:记录整个FMEA分析过程,并生成报告以供未来参考和持续改进。
### 2.3.2 FMEA表的编制与填写指南
FMEA 表是FMEA分析中用来记录所有分析信息的工具,通常包含以下关键部分:
- **编号**:为每个故障模式分配一个唯一编号。
- **潜在故障模式**:详细描述每一个故障模式。
- **潜在影响**:阐述故障模式对系统性能、功能、客户满意度等方面的潜在影响。
- **严重程度(S)**:评估故障模式发生时的最坏影响的严重程度,通常用1-10分来表示。
- **潜在原因**:列举可能导致故障模式发生的原因。
- **发生概率(O)**:评估原因发生的可能性,同样使用1-10分来表示。
- **当前控制方法**:描述目前预防或检测故障模式的措施。
- **检测概率(D)**:评估当前控制措施发现潜在故障的可能性。
- **风险优先级数(RPN)**:S x O x D 的乘积。
- **建议措施**:列出降低风险和优先级的改进措施。
- **责任人和实施日期**:记录实施改进措施的责任人和预定日期。
在编制FMEA表时,应确保所有数据的准确性和完整性。表格的格式要统一,以便于团队成员的理解和沟通。通过填写FMEA表,团队能够系统地识别风险,并制定行动计划来缓解这些风险。
通过本章节的介绍,我们对FMEA的基础知识有了一个初步的认识。下一章节,我们将深入探讨如何在Minitab 17中进行FMEA分析,并着重介绍其界面布局、数据收集与整理以及风险优先级评估等关键功能。
# 3. 使用Minitab 17进行FMEA分析
## 3.1 Minitab 17界面布局与功能介绍
### 3.1.1 Minitab 17的用户界面
Minitab 17 的用户界面设计直观易用,其布局清晰,主要分为以下几个区域:
- 菜单栏:包含了文件、编辑、视图、数据
0
0
相关推荐
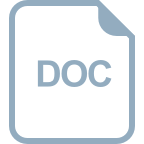
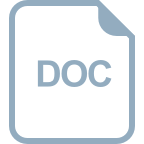
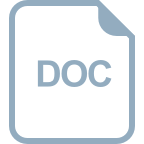
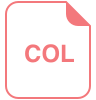
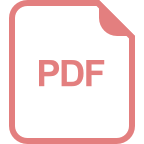
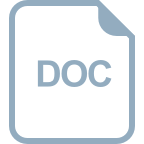
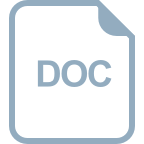
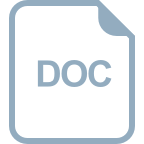