【公差分析必备技巧】:掌握ASME Y14.5-2018,提升设计精确度
发布时间: 2024-12-19 05:50:17 阅读量: 4 订阅数: 3 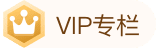
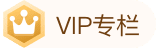
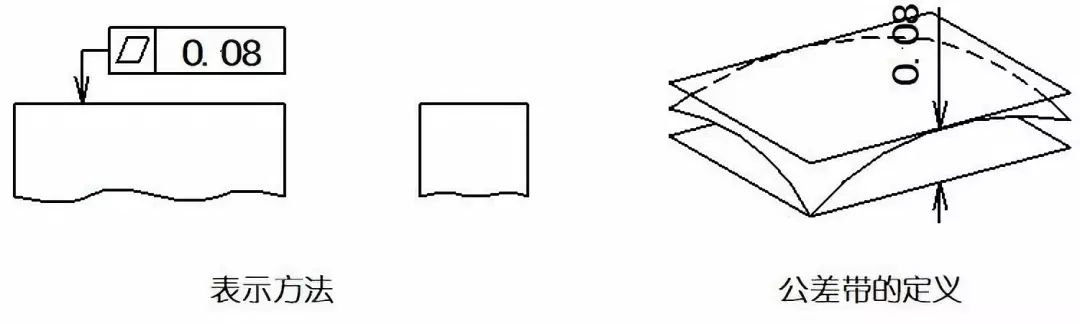
# 摘要
本文重点介绍了公差分析的重要性和相关标准,特别是ASME Y14.5-2018标准在现代工程设计中的应用。文章首先概述了公差分析的必要性和标准的演进。接着,对ASME Y14.5-2018标准中的术语、公差原则、符号和计算规则进行了基础性解读。第三章详细讨论了公差分配技术、统计公差分析和计算机辅助公差分析的计算方法和实践应用。文章第四章探讨了公差分析在多学科设计优化、DFMA和六西格玛设计中的高级应用,并展望了其未来趋势,包括人工智能、机器学习以及新材料技术的潜在影响。最后,第五章通过案例分析展示了如何将ASME Y14.5-2018标准应用于实际工程项目,包括机械零件设计与电子组件制造中的公差管理和优化过程。
# 关键字
公差分析;ASME Y14.5-2018;设计优化;统计公差;计算机辅助设计;六西格玛
参考资源链接:[ASME Y14.5-2018 中文版:尺寸与公差标注指南](https://wenku.csdn.net/doc/6401ad1bcce7214c316ee4f5?spm=1055.2635.3001.10343)
# 1. 公差分析的重要性及标准概述
在制造领域,公差分析是保证产品质量的关键步骤。公差表示尺寸的可接受波动范围,对于确保产品功能和寿命至关重要。本章节将概述公差分析的重要性,并介绍其在制造标准中的位置,为后文详细探讨ASME Y14.5-2018标准打下基础。
## 1.1 公差分析的重要性
公差分析涉及对制造过程中可能出现的尺寸偏差进行预测和控制。这些偏差可能来自机器公差、材料属性变化或操作误差。通过对这些偏差的分析,设计师能够确保装配件、机械零件等在规定的公差范围内正常工作,降低返工率、提高生产效率。
## 1.2 公差分析的标准概述
全球范围内存在多个公差和配合的标准,如ISO、DIN、ANSI和ASME Y14.5等。其中,ASME Y14.5-2018标准是由美国机械工程师学会发布的,专门针对几何公差的公差标准。该标准详细定义了用于制造和工程设计的术语、公差原则、符号和计算规则,是行业广泛应用的标准之一。
下一章将深入探讨ASME Y14.5-2018标准的基础知识,包括其术语和定义,公差原则及符号,以及公差计算的基本规则。这将为读者提供一个稳固的基础,以便进一步理解公差分析在设计和制造过程中的实际应用。
# 2. ASME Y14.5-2018标准基础
## 2.1 ASME Y14.5-2018的术语和定义
### 2.1.1 了解几何公差中的基本概念
在机械设计和制造领域,几何公差是确保零件与组件精确配合的关键因素。几何公差,也称为形状与位置公差,包含了对零件形貌、方向、位置和轮廓度的定义,旨在控制零件上的几何要素与理想状态之间的差异。ASME Y14.5-2018 标准提供了精确的术语定义和符号来表述这些公差。
在详细学习这些公差之前,必须掌握以下基础概念:
- **基准**:一个或一组理论精确的参考点、线、面,用来定义其他要素的位置。
- **特征**:几何上的点、线、面或它们的组合,通常与功能有关。
- **公差带**:对一个要素允许的最大和最小极限尺寸范围。
这些概念是理解和应用几何公差的基础。基准用于确定特征的位置和方向,而公差带则定义了特征在空间中的可变范围。
### 2.1.2 理解特征控制框架的组成
特征控制框架是ASME Y14.5-2018 标准中用于表达几何公差要求的结构化方法。它由一系列字符、符号和数字组成,表明了公差应如何应用于特定的特征。
一个典型的特征控制框架包括以下几个组成部分:
- **几何特征符号**:指出要控制的几何特性,例如平面度、圆度、同轴度等。
- **公差值**:以数值形式给出的公差大小。
- **基准标识**:如果需要,会在此表明控制特征相对于哪个基准进行。
- **修饰符**:用来进一步详细说明公差的应用条件,例如MMC(最大材料条件)、LMC(最小材料条件)等。
要正确地理解特征控制框架,我们可以用以下的例子进行解读:
```
位置公差框:
位置公差
直径符号
公差值
基准1
基准2
基准3
```
一个完整的位置公差框中,可能包含一个位置公差值(如0.05mm),一个直径符号(如ø),以及一个或多个基准。理解这个框架的结构,对于正确应用几何公差至关重要。
## 2.2 公差原则和符号
### 2.2.1 公差原则的分类及其应用
ASME Y14.5-2018 标准中的公差原则分为两大类:独立原则和相关原则。这些原则是决定如何应用几何公差以确保零件正确配合的指导方针。
- **独立原则(Individual Tolerance)**:独立原则意味着每个特征必须单独满足其公差要求,不考虑与其他特征的关系。这意味着,如果一个特征的公差为0.05mm,则它必须在独立的情况下处于0.05mm的公差范围内,而不考虑与其他特征的相对位置。
- **相关原则(Related Tolerance)**:相对应的,相关原则是指一组特征要一起满足公差要求,确保它们之间的相对位置或关系是准确的。例如,在一个零件的孔和轴组合中,孔的轴线和轴的轴线可能需要相关位置公差来确保它们的对齐。
对于设计人员和制造工程师来说,了解这两个原则的适用场景至关重要。选择适当的原则可以减少制造成本、提高部件的功能性,并在设计时为零件的公差分配提供灵活性。
### 2.2.2 标准中的符号解读和使用
在 ASME Y14.5-2018 标准中,有许多符号用于定义几何公差。这些符号不仅包括了基本的几何特征(如平面度、圆度等),还有修饰符号和基准符号等,它们共同构成了特征控制框架的一部分。
- **基本几何特征符号**:这些是用于指定公差类型的符号,例如平面度符号(三角形)、圆度符号(圆形)、同轴度符号(两条平行线)等。
- **修饰符号**:修饰符号用于改变或增加对公差的应用规则,例如MMC修饰符表示最大材料条件,而RFS表示自由状态。
- **基准符号**:基准符号用于指定公差应用的参考点或参考线。例如基准A、基准B、基准C。
正确地解读和使用这些符号是确保设计意图准确传达给制造部门的基础。例如,如果没有正确使用修饰符号来表示最大材料条件(MMC),那么制造出来的零件可能无法正确装配。
为了帮助读者更好地理解,下面是一个表,展示了几个常用的几何公差符号及其含义:
| 符号 | 名称 | 描述 |
|------|------|------|
| ⊥ | 垂直度 | 表示要素必须与基准要素保持90度角。 |
| // | 平行度 | 表示要素必须与基准要素保持平行。 |
| ∅ | 直径公差 | 表示一个圆柱形要素必须符合规定的圆柱度和尺寸公差。 |
## 2.3 公差计算的基本规则
### 2.3.1 最大实体要求和最小实体要求
在ASME Y14.5-2018 标准中,有两种重要的公差要求与零件的物理尺寸直接相关:最大实体要求(Maximum Material Condition, MMC)和最小实体要求(Least Material Condition, LMC)。
- **最大实体要求 (MMC)**: 这是指在考虑尺寸公差时,零件的尺寸应尽可能接近其最大极限尺寸。例如,如果一个孔的公差是H7,那么在MMC条件下,孔的最大实体直径应尽可能接近其上限,即H7。
- **最小实体要求 (LMC)**: 相对的,LMC指在考虑尺寸公差时,零件的尺寸应尽可能接近其最小极限尺寸。如果一个轴的公差是d9,则其最小实体直径应尽可能接近下限,即d9。
在设计和制造过程中正确应用MMC和LMC可以显著提高部件的互换性和制造效率。例如,使用MMC原则,可以保证在零件最小尺寸时仍能满足形状和位置公差,从而减少因尺寸变化导致的额外加工和调整。
### 2.3.2 调节和固定要求的比较与应用
在几何公差领域,除了MM和LMC原则外,还有一对重要的概念需要理解:调节要求(Tolerance of Position, TP)和固定要求(Floating Fastener Rule, FFR)。
- **调节要求(TP)**:指的是公差与基准的关系是固定的,不论基准实际处于其公差带中的哪个位置。例如,一个轴上的孔必须始终在某个位置固定,即使轴的实际位置有变动。
- **固定要求(FFR)**:在这种情况下,零件上的一部分与另一部分的公差是“浮动”的,即它们之间的相对位置可以变化,但整体功能仍然得到保持。例如,固定在板上的一个螺丝孔。
理解调节和固定要求之间的差异至关重要,因为它们决定了零件在装配时的灵活性和功能性的平衡。在实际应用中,例如在装配发动机的零件时,可能会使用TP来确保关键部件的精确对齐,同时使用FFR来允许其他部件在一定范围内浮动,以适应不同的工作条件。
在下面的表格中,我们将概括几个关键点,以便于读者更清楚地了解调节要求和固定要求:
| | 调节要求(TP) | 固定要求(FFR) |
| --- | ---------------- | ---------------- |
| 定义 | 公差是固定的,与基准位置无关 | 允许公差随着基准位置的变化而变化 |
| 优点 | 提供精确的位置关系,适合关键零件的装配 | 提高装配的灵活性,适应不同工作条件 |
| 应用 | 精密机械、航空发动机 | 通用机械、汽车 |
| 示例 | 发动机中齿轮的装配 | 车辆底盘上螺丝的固定 |
通过对比分析调节要求与固定要求,设计者能够更灵活地应用标准,确保最终产品既符合设计规范,又能够满足实际使用的需求。在实际制造过程中,这种灵活运用公差原则的方法可以显著提高产品的质量与效率。
# 3. 公差分析的计算方法与实践
在现代制造业中,公差分析不仅仅是制图和设计的标准要求,它还在生产过程中发挥着至关重要的作用。通过精确的公差分析,可以确保产品在制造和装配过程中达到预期的精度和性能。本章节将深入探讨公差分析的计算方法和实践,包括公差分配技术、统计公差分析以及计算机辅助公差分析的运用。
## 3.1 公差分配技术
公差分配技术是确保制造和装配过程中各部件能够协同工作的重要工具。它涉及到一系列复杂的计算,旨在平衡成本和功能性,以确定每个部件的公差大小。
### 3.1.1 如何进行公差链分析
公差链分析是公差分配过程中的核心环节。它包括识别所有影响最终产品功能的独立公差,并且确保这些公差在允许的范围内。为了进行有效的公差链分析,需要先构建公差链模型。
#### 公差链模型构建步骤
1. **定义功能要求**:识别产品中关键功能要求的公差,如尺寸、形状、方向和位置。
2. **识别公差链**:在产品或装配过程中,确定哪些部件直接或间接地影响这些功能要求。
3. **绘制公差链图**:利用流程图表示部件间的关系和公差的传递路径。
4. **评估影响**:量化各个公差对于最终功能的影响。
5. **优化分配**:根据评估结果,调整每个部件的公差,以最小化总成本并满足功能要求。
### 3.1.2 公差合成与分配的案例研究
在真实世界的应用中,公差链分析会涉及到复杂的计算和决策。下面将通过一个案例来展示公差链分析和公差合成的实际操作过程。
#### 案例:轴承座装配公差分析
1. **问题描述**:假设我们有一个轴承座装配,它由三个主要部件组成:轴承座本身、轴承和螺栓。每个部件都有自己的加工公差。
2. **目标公差**:轴承座装配的最终目标是确保轴承的外径与轴承座的内径之间有一个精确的配合间隙,以保证运行的平稳性和承载能力。
3. **计算过程**:首先,确定每个部件的公差对最终装配的影响。例如,轴承座的内径公差和轴承的外径公差直接影响配合间隙。接下来,使用概率方法合成这些公差,以得出装配的总公差。
4. **优化公差分配**:分析显示某些部件的公差过大或过小,可能会导致装配成本增加或装配质量下降。通过适当的调整,可以达到最优的成本效益比。
## 3.2 统计公差分析
统计公差分析是根据统计数据来预测产品功能的概率分布,而不是仅仅依赖于单一的最大和最小公差限制。这种方法可以提供更加真实的产品性能评估。
### 3.2.1 统计公差的原理与优势
统计公差分析原理主要基于概率论和统计学。它允许设计者考虑过程变异性,并预测产品在真实条件下运行的性能。这种分析方法的主要优势在于提供更精确的风险评估和成本节约。
#### 统计公差分析优势具体表现在:
- **减少保守设计**:减少不必要的过度公差,从而降低成本。
- **更准确的风险评估**:利用统计方法能更好地预测产品在实际使用中的性能。
- **优化制造过程**:有助于确定更合理的制造公差,改善过程稳定性。
### 3.2.2 实际案例中的统计公差应用
在实际应用统计公差分析时,我们需使用统计工具来完成以下步骤:
1. **收集数据**:从生产线上收集所有相关部件的尺寸数据。
2. **分析数据**:使用统计软件来分析数据分布、均值和标准差。
3. **计算概率**:基于统计数据确定产品功能的失效概率。
4. **公差优化**:根据概率分析结果调整公差设置,优化设计。
## 3.3 计算机辅助公差分析
随着计算机技术的发展,计算机辅助公差分析(Computer-Aided Tolerance Analysis,CATA)工具已经被广泛应用到工程实践中。这些工具可以极大提高公差分析的效率和精度。
### 3.3.1 CAD和CAE工具在公差分析中的运用
CAD和CAE工具的集成使得公差分析更加高效。它们可以帮助设计者在早期设计阶段进行公差分配和模拟。
#### CAD和CAE工具的运用细节:
1. **3D建模**:使用CAD工具创建产品和装配的3D模型。
2. **公差模拟**:通过CAE工具模拟实际的生产过程和装配条件。
3. **结果分析**:分析公差模拟结果,评估潜在的风险和问题。
4. **设计迭代**:根据结果调整设计,优化公差设置。
### 3.3.2 软件辅助优化公差的示例
一款有效的CATA软件可以提供以下功能:
1. **公差链分析**:软件自动识别并分析设计中的公差链。
2. **公差分配建议**:根据指定的质量目标和成本限制提出建议。
3. **装配模拟**:使用蒙特卡洛模拟等技术模拟装配过程,预测尺寸链的最终结果。
4. **优化算法**:集成优化算法,如遗传算法、模拟退火等,帮助找到最佳公差配置。
通过这些方法,公差分析工作变得更加高效和精确,为设计和制造过程提供有力支持。
在后续章节中,我们将深入探讨公差分析在设计中的高级应用,并通过案例研究展示ASME Y14.5-2018标准在实际项目中的应用。
# 4. 公差分析在设计中的高级应用
公差分析在设计领域内的应用是多方面的,涉及机械、电子、软件等多个学科。这一章节将深入探讨如何将公差分析融合于多学科设计中,并分析其在面向六西格玛设计以及未来设计趋势中的角色。
## 4.1 多学科设计优化与公差分析
### 4.1.1 融合机械、电子和软件领域的公差分析
在现代复杂产品的设计过程中,机械、电子和软件等不同学科的融合已成为常态。公差分析不仅在机械设计领域发挥着至关重要的作用,在电子组件的设计与装配以及软件工程中也同样重要。例如,PCB板上的元件位置公差必须严格控制,以确保电子设备的性能和可靠性。软件领域中,公差分析可以帮助开发人员理解数据的不精确性,并在算法中进行相应的容错设计。
公差分析在多学科设计中的应用,需要对各学科的公差要求进行综合考量。设计师需要在各个学科间建立一套共同的公差标准和评估机制,确保在不同领域中的公差相互兼容,避免在制造和装配过程中出现不必要的问题。
下面举例说明如何在多学科设计中应用公差分析:
**案例分析:**
某企业正在设计一款智能机器人,该机器人不仅包含机械臂、行走装置等机械部件,还有传感器、控制电路板等电子部件,以及负责决策和控制的软件系统。在设计过程中,设计师需要考虑到机械臂的关节公差、电路板上元件的布局公差以及软件算法中数值计算的精度。
**设计优化过程:**
1. **确定关键公差要求**:首先识别出机械、电子和软件设计中的关键公差参数。
2. **交叉分析**:分析不同领域中关键公差的相互影响,例如,电路板上元件的位置公差可能会影响机械臂的精准运动。
3. **建立公差模型**:使用CAD软件建立各部件的三维模型,并模拟公差对整个系统性能的影响。
4. **迭代优化**:根据模型分析结果,对设计进行多次迭代,优化公差分配,以达到最佳性能。
通过这种多学科融合的公差分析,设计师能够更全面地理解产品的性能表现,并在设计阶段做出更加合理的决策。
### 4.1.2 面向制造与装配的设计(DFMA)中公差的作用
面向制造与装配的设计(DFMA)是优化设计以提高产品制造和装配效率的一系列方法。在DFMA中,公差分析不仅有助于减少制造成本,还能提高产品质量和装配的可靠性。
公差分析在DFMA中的主要作用如下:
1. **减少零件数量和装配步骤**:通过精确的公差分析,可以设计出结构更简单、装配更方便的零件,从而减少整体装配工序。
2. **提高零件的互换性**:通过设定合理的公差范围,保证零件即使在生产过程中存在一定的尺寸偏差,仍然能够方便装配,提高装配效率。
3. **优化成本和质量**:精确定义的公差可以减少过度加工的需要,避免不经济的制造成本,同时保证产品质量。
**案例研究:**
某汽车制造商在设计一款新型汽车门锁时,运用DFMA的原则,通过严格的公差分析,优化了锁体和锁芯的配合公差。通过精确的配合,减少了零件数量和装配工序,同时还保证了锁具的高可靠性和安全性。这一优化不仅降低了制造成本,还提高了产品的市场竞争力。
## 4.2 面向六西格玛设计的公差分析
### 4.2.1 六西格玛方法论简介
六西格玛是一种旨在通过减少产品和服务流程缺陷达到近乎完美的质量管理方法论。在设计阶段,六西格玛关注于识别和控制设计中的变异性,确保产品在长期内能持续稳定地提供高质量的性能。
### 4.2.2 公差分析在实现六西格玛质量目标中的角色
公差分析在六西格玛设计中的作用主要体现在以下几个方面:
1. **确定关键质量特性(CTQs)**:首先识别对产品性能影响最大的质量特性,确定其合理的公差范围。
2. **减少变异**:通过公差分析,设计团队能够识别出设计中可能产生变异的环节,并采取措施减少这些变异。
3. **优化设计**:基于公差分析结果,对产品设计进行必要的优化,确保产品在全生命周期内均能满足质量要求。
通过将公差分析应用于六西格玛设计流程中,设计团队能够更有效地预防缺陷发生,从而在设计阶段就达到六西格玛的质量标准。
## 4.3 公差分析的未来趋势
### 4.3.1 人工智能与机器学习在公差分析中的潜力
随着人工智能(AI)和机器学习(ML)技术的快速发展,它们在公差分析中的应用潜力越来越受到业界的关注。AI和ML可以帮助设计工程师从大量历史数据中识别出影响公差的因素,并进行预测分析。
### 4.3.2 新材料和新技术对公差标准的影响
随着新材料的不断涌现和制造技术的进步,传统的公差标准可能无法完全适应新的应用场景。例如,3D打印技术能够实现极高的精度,但同时也需要新的公差标准来适应其独特的工作原理。
设计工程师需要不断更新自己的知识库,以适应新材料和新技术带来的挑战。通过参与标准制定组织的工作,工程师可以确保他们的意见被纳入到未来公差标准的制定中。
在未来,公差分析将会是一个动态的、不断发展变化的领域,它不仅会融合新技术和材料,还会与质量管理体系如六西格玛等紧密结合,共同推动制造和设计行业的进步。
# 5. 案例分析:将ASME Y14.5-2018应用于实际项目
## 5.1 案例研究:机械零件的设计与公差分析
### 5.1.1 实际零件设计中的公差应用实例
在机械设计领域,精确的公差应用对于确保零件的互换性和功能性至关重要。下面我们将通过一个具体的案例来展示ASME Y14.5-2018标准如何应用于机械零件设计。
假设我们需要设计一个轴组件,该组件包括一个齿轮和一个轴承座。齿轮必须能够与轴精确配合,而轴承座需要精确地安装在机架上。应用ASME Y14.5-2018标准,我们可以从以下几个步骤来执行设计和公差分析:
1. 确定功能要求:齿轮和轴之间的配合必须保证传递扭矩而无滑移,轴承座与机架的配合需要确保稳定的支撑和低摩擦。
2. 确定尺寸链:通过测量各个零件的尺寸和公差,建立尺寸链,确保整个组件的功能要求得到满足。
3. 应用特征控制符号:为齿轮的孔、轴承座的安装孔指定合适的几何公差,如位置度、同轴度和圆度。
4. 分析公差累积:使用最大实体原则,允许在不影响配合的条件下,适度放宽公差。
5. 进行公差仿真和验证:使用CAD软件进行公差仿真,确保设计公差范围内的零件能够正确装配和运行。
### 5.1.2 分析案例中的设计优化过程
在设计优化的过程中,我们遵循了以下步骤:
1. 初步设计:根据功能要求和载荷分析,确定零件的基本尺寸。
2. 应用公差:根据ASME Y14.5-2018标准,对零件关键尺寸应用适当的几何公差。
3. 制定公差方案:对轴和孔应用位置度公差,对齿轮和轴承座的接触面施加平行度和角度公差。
4. 利用CAD软件进行仿真:模拟在公差范围内的零件配合情况,验证齿轮的运转平稳性和轴承座的固定稳定性。
5. 分析公差敏感度:通过敏感度分析,找到影响零件配合性能的关键尺寸和公差。
6. 优化设计:根据仿真结果和敏感度分析,调整公差大小和位置,以减少成本同时保持性能。
通过这一系列的步骤,我们不仅保证了设计的质量和精确性,还为制造提供了明确的公差要求,从而实现了设计和制造的有效结合。
## 5.2 案例研究:电子组件的制造公差管理
### 5.2.1 制造过程中的公差管理策略
在电子组件制造领域,公差管理对于产品的质量和可靠性的提升具有重大意义。以下是一个电子组件公差管理的案例分析:
考虑到一个电路板装配过程,其中包含了多种类型的SMD(表面贴装设备)组件,以及一些复杂的焊接和安装步骤。为了保证电子组件的性能和稳定性,需要采用一套全面的公差管理策略。
1. 公差分析:对电路板上的每一个组件定位孔和焊盘进行公差分析,包括尺寸公差、位置公差和形状公差。
2. 制造公差确定:基于组件供应商的规范和制造能力,确定每个关键尺寸的制造公差。
3. 公差累积控制:利用统计公差分析方法,对可能发生的公差累积进行评估,并制定控制策略。
4. 持续改进:通过收集装配过程中的实际数据,不断优化公差管理策略,减少制造过程中的变异。
### 5.2.2 案例中实现高精度和高可靠性设计的关键因素
在电子组件制造过程中,实现高精度和高可靠性设计的关键因素包括:
1. 严格的公差标准:制定严格而合理的公差标准,确保关键尺寸和位置的精度。
2. 高效的生产流程:通过精益生产方法,减少生产环节中的变异和缺陷。
3. 自动化的装配设备:使用高精度的自动化装配设备,降低人为因素对公差精度的影响。
4. 质量控制和持续改进:建立一个全面的质量控制体系,不断收集数据,实施改进措施。
5. 统一的公差管理软件:采用统一的软件工具进行公差分析和管理,保持数据的一致性和准确性。
通过这些策略,我们确保了电子组件在高密度和高精度要求下,仍能保持高度的可靠性和功能性,满足现代电子产品的严格标准。
0
0
相关推荐
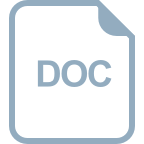
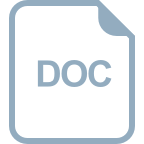
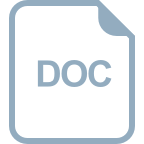
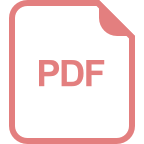
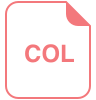

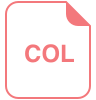
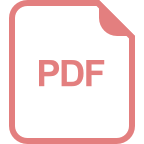
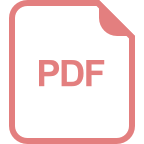