自动化控制系统:实现智能制造的核心技术全解析
发布时间: 2024-12-27 13:47:58 阅读量: 7 订阅数: 14 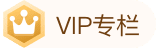
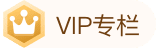
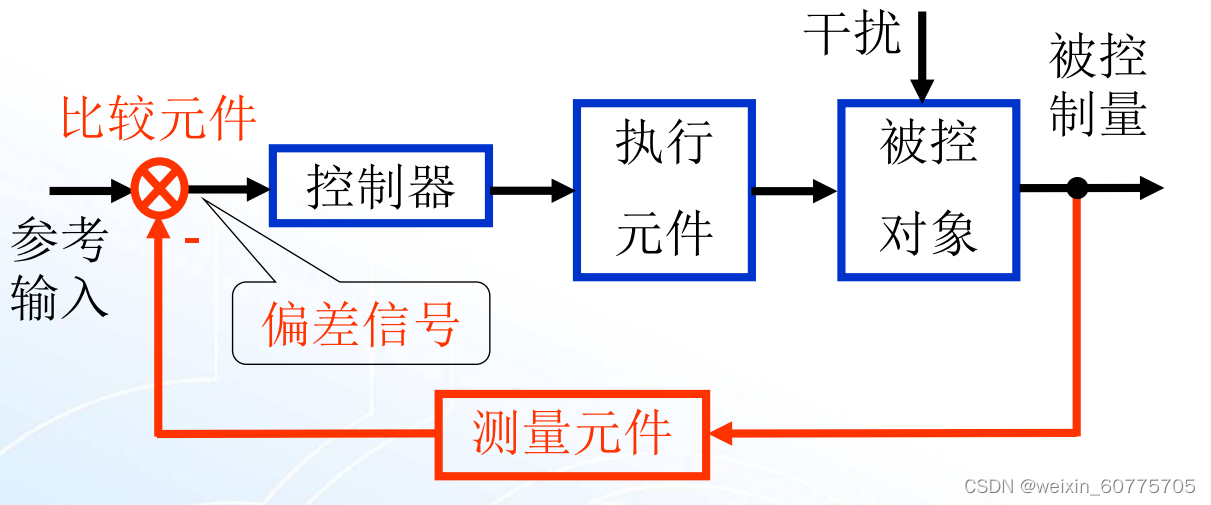
# 摘要
自动化控制系统是现代智能制造和工业自动化的核心技术,它不仅能够显著提升生产效率,还能对产品质量产生深远影响。本文首先概述了自动化控制系统的理论基础,包括控制系统的设计原则、模块化集成以及稳定性分析,并探讨了控制理论的应用。接着,分析了智能制造与自动化控制的关系,突出了自动化控制在提升生产效率和产品质量方面的作用。随后,通过实践案例,本文展示了自动化控制系统在制造业和物流行业的应用,以及面临的挑战和未来发展方向。最后,本文深入探讨了自动化控制系统的关键技术,包括通信技术、人工智能和机器学习在控制过程优化的应用,以及安全性和隐私保护的策略。本文旨在为自动化控制系统的设计者、开发者和使用者提供全面的技术参考和未来发展的指导。
# 关键字
自动化控制系统;智能制造;控制理论;稳定性分析;人工智能;信息安全
参考资源链接:[现代控制系统解决方案第12版详解](https://wenku.csdn.net/doc/6412b723be7fbd1778d4939f?spm=1055.2635.3001.10343)
# 1. 自动化控制系统概述
自动化控制系统作为工业生产和现代科技发展的重要组成部分,其核心目的在于通过技术手段实现生产过程和操作的自动化,提高效率和精确性,降低人工成本和错误率。从最初简单的反馈控制到如今的计算机网络控制系统,自动化技术不断进步,已经渗透到各行各业。理解自动化控制系统的基本概念,掌握其核心技术,对于提升系统的智能化、网络化和综合化水平至关重要。
# 2. 智能制造与自动化控制的关系
## 2.1 智能制造的基本概念和发展历程
### 2.1.1 智能制造定义与核心组成
智能制造,作为一种先进的制造模式,它通过深度融合信息技术和制造技术,使得生产过程更加灵活、高效和绿色。在智能制造的体系中,信息技术如物联网、大数据分析、云计算、人工智能和机器人技术等,与传统的制造流程相融合,形成了一个高度自治和优化的生产系统。
智能制造的核心组成主要包括以下几个方面:
- **智能设备**:采用传感器和控制器进行实时数据采集和过程控制的高精度、高效能生产设备。
- **智能物流**:使用自动化仓库、机器人和无人搬运系统来实现物料的自动存取和运输。
- **智能生产**:以计算机系统和优化算法为核心,实现生产线的动态调度和生产过程的自适应控制。
- **智能服务**:通过数据分析和机器学习等技术,提供预测性维护、远程监控和个性化服务。
- **智能决策**:基于实时数据和历史信息的决策支持系统,为企业管理层提供策略性建议。
### 2.1.2 智能制造的发展阶段和趋势
智能制造的发展经历了几个阶段,从初步的自动化和信息化,逐渐向高度集成和智能化发展。在过去的几十年中,以下几个阶段尤为明显:
- **自动化阶段**:通过程序化的指令,使机器取代人工进行重复性高的操作。
- **信息化阶段**:使用计算机辅助设计(CAD)、计算机辅助制造(CAM)以及企业资源规划(ERP)等系统,提高设计和管理的效率。
- **网络化阶段**:引入物联网技术,实现生产过程中设备与设备、设备与系统的互联互通。
- **智能化阶段**:融合人工智能技术,使得生产线可以自主学习和优化,以适应不断变化的生产需求。
未来,智能制造将更加注重以下几个方面:
- **自适应生产**:生产线能够根据订单的变化自动调整生产计划和流程。
- **可持续发展**:智能制造将致力于降低资源和能源的消耗,提高材料利用率,实现环境友好型制造。
- **深度集成**:不同生产环节和供应链环节将实现深度融合,形成协同高效的智能制造生态系统。
- **人机协作**:进一步探索机器人和人类工作者之间的协作模式,提升工作环境和工作体验。
## 2.2 自动化控制在智能制造中的作用
### 2.2.1 自动化控制系统的分类与特性
自动化控制系统是指利用计算机技术、通信技术、控制理论等技术手段,对生产过程实现自动控制的系统。根据控制范围和功能的不同,自动化控制系统大致可以分为以下几类:
- **过程控制**:用于连续生产过程,如化工、造纸和电力等行业中的自动调节控制。
- **分散控制**:也称分布式控制系统(DCS),每个控制点都有独立的处理能力,通过网络进行通信和协调。
- **计算机数控系统(CNC)**:广泛应用于机床、金属加工等制造业领域,实现对机床的精密控制。
- **机器人控制系统**:用于控制工业机器人或其他自动化设备的运动和作业流程。
自动化控制系统的特性主要体现在:
- **实时性**:自动化控制系统可以对生产过程进行实时监控和快速响应。
- **精确性**:系统可以实现对生产流程的高精度控制。
- **可靠性**:系统的稳定性和抗干扰能力是保证生产连续性和产品质量的关键。
- **灵活性**:通过编程和配置,自动化控制系统能够适应不同的生产任务和环境。
### 2.2.2 自动化控制与生产效率的提升
自动化控制系统的引入对生产效率的提升有着显著的影响。具体表现在以下几个方面:
- **生产周期缩短**:自动化控制系统可以实现快速的切换和调整,从而缩短产品的生产周期。
- **减少人为错误**:自动化的操作减少了由于人为操作不当造成的错误和损失。
- **提高设备利用率**:通过系统的调度和管理,可以提高关键设备的利用率和产出率。
- **灵活的生产调整**:当市场需求发生变化时,自动化控制系统可以快速响应,进行生产计划的调整。
例如,采用自动化装配线的工厂,与传统手工装配相比,生产效率可以提高数倍到数十倍不等。高度自动化的流水线可以连续作业,不受班次和疲劳的限制,显著提高了生产效率。
### 2.2.3 自动化控制对产品质量的影响
产品质量是制造业的核心竞争力之一。自动化控制对产品质量的影响主要体现在:
- **保证产品一致性**:自动化控制系统确保了生产过程的一致性和重复性,从而保证了产品质量的稳定性。
- **精准控制生产参数**:系统可以精确控制温度、压力、时间等关键生产参数,有效避免人为波动对产品造成的影响。
- **实时监测与反馈**:自动化系统能够实时监控生产过程,及时发现问题并进行调整,减少了不合格品的产出。
- **持续改进生产过程**:利用生产数据和反馈,系统可以持续优化生产过程,减少缺陷率。
例如,电子制造行业中广泛应用的SMT(表面贴装技术)生产线,通过自动化控制的高精度贴片机和检测设备,可以保证电子元件的精确放置和焊接质量,极大地提升了最终产品的质量。
在智能制造和自动化控制的背景下,未来的制造业将更加注重质量与效率的平衡,不断推进自动化控制技术的创新和应用,以达到更高的生产管理水平。
# 3. 自动化控制系统的理论基础
## 3.1 控制系统的设计原则和方法论
### 3.1.1 控制系统的模块化与集成
自动化控制系统的模块化设计原则是将复杂的控制系统拆分为一系列功能独立的模块,每个模块完成特定的控制任务。这种设计方式便于系统的组装、调试、维护和升级。模块化设计还能够针对特定的任务进行优化,提高系统的灵活性和可扩展性。
在模块化的基础上,集成是将多个模块按需组合成一个统一的控制解决方案。集成的目标是实现模块之间的高效通讯,确保数据流和控制命令可以无缝传输。在自动化控制系统中,集成设计需要考虑硬件接口、通信协议和软件接口等多个层面,以实现不同模块间协调一致的工作。
### 3.1.2 控制系统的反馈机制和稳定性分析
反馈机制是控制系统中的一个关键组成部分,它通过比较期望输出与实际输出,来调整控制输入,从而实现对过程的精确控制。一个典型的反馈控制系统包括一个反馈回路,用于检测输出并将其与设定的目标值进行比较。
在设计控制系统时,稳定性分析是不可或缺的。系统的稳定性是指当系统受到扰动后,能否自我调节并恢复到稳定状态。一个稳定的控制系统要求其控制参数必须在一定的范围内,以避免系统输出的无限增长或振荡。
为了确保控制系统的稳定性,工程师通常使用根轨迹法、奈奎斯特稳定性准则或劳
0
0
相关推荐
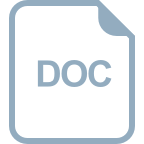
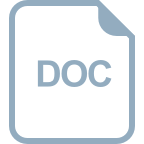
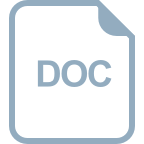
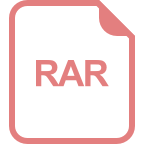
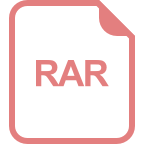
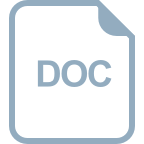
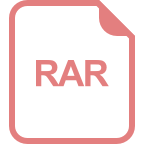
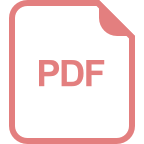
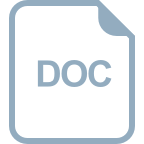