【HOLLiAS MACS-K硬件剖析】:自动化控制系统的核心秘密与升级策略
发布时间: 2024-12-25 08:37:26 阅读量: 18 订阅数: 16 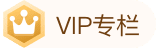
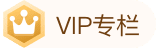
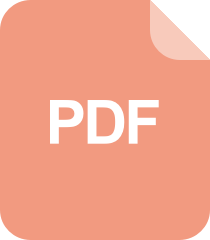
HOLLiAS MACS-SM 系列硬件.pdf
# 摘要
自动化控制系统是工业技术进步的重要标志,涉及硬件架构、软件支持以及性能优化等多个方面。本文首先概述了自动化控制系统的概念,然后深入分析了HOLLiAS MACS-K系统在硬件架构上的核心模块、连接通讯机制以及维护策略,并探讨了软件层面的操作系统、控制算法以及用户界面设计。在性能优化章节中,本文介绍了评估、调优方法和系统升级策略,并通过案例研究揭示了自动化升级项目的实际操作和效益。最后,本文展望了自动化控制系统面向工业物联网、智能制造以及预测性维护的发展趋势,阐述了大数据分析在自动化系统中的应用前景。通过全面的分析和讨论,本文旨在为自动化控制系统的开发和应用提供理论支持和实践指导。
# 关键字
自动化控制系统;HOLLiAS MACS-K;系统架构;性能优化;工业物联网;智能制造;预测性维护;大数据分析
参考资源链接:[HOLLiAS MACS-K系列DCS硬件详细指南](https://wenku.csdn.net/doc/42ijch983s?spm=1055.2635.3001.10343)
# 1. 自动化控制系统概述
自动化控制系统是现代工业的基石,它通过集成电子技术、信息技术、控制技术等手段,实现生产过程的自动化和智能化,大幅度提高生产效率和产品质量,减少人力资源的需求。在这一章节中,我们将介绍自动化控制系统的定义、组成、分类以及它在工业生产中的重要性。我们会浅谈自动化控制系统如何优化生产流程,降低成本,并探讨它在实现智能制造和工业物联网中的关键作用。这些内容将为读者提供一个关于自动化控制系统的全面视角,为进一步探讨硬件架构、软件支持和性能优化打下坚实的理论基础。
# 2. HOLLiAS MACS-K硬件架构解析
### 2.1 核心模块的功能与特点
#### 2.1.1 控制器单元分析
控制器单元作为自动化控制系统的“大脑”,负责整个系统的运行逻辑和决策处理。在HOLLiAS MACS-K系统中,控制器单元具备以下几个关键功能与特点:
- **高性能处理能力**:控制器单元采用高性能的处理器,确保了复杂的控制算法能够实时执行,满足高精度控制要求。
- **冗余设计**:为了保证系统的高可靠性,控制器单元往往采用主备双机热备的冗余设计,即便主控制器出现故障,备用控制器可以立即接管控制任务,不中断生产过程。
- **模块化扩展**:控制器单元支持模块化扩展,用户可以根据实际需要增加控制器资源,以适应系统规模的扩大。
以下是一个控制器单元的示例代码块,说明其如何通过冗余配置来确保系统稳定运行:
```c
// 控制器配置代码示例
// 设定主备控制器地址
primary_controller = {"IP": "192.168.1.1", "Port": 502};
backup_controller = {"IP": "192.168.1.2", "Port": 502};
// 在控制任务中实施冗余切换逻辑
function run_control_task() {
active_controller = primary_controller; // 默认使用主控制器
try {
// 尝试与主控制器通信执行任务
connect(active_controller);
execute_control_algorithm();
} catch(error) {
// 主控制器故障,切换到备用控制器
active_controller = backup_controller;
connect(active_controller);
execute_control_algorithm();
}
}
```
### 2.2 硬件连接与通讯机制
#### 2.2.1 系统总线技术
系统总线技术是确保自动化控制系统高效稳定运行的关键,它负责各个模块间的数据传输和指令执行。HOLLiAS MACS-K系统采用的系统总线技术具备以下特点:
- **高带宽**:支持高数据传输速率,满足实时数据采集和指令下发的需求。
- **高可靠性**:设计有数据校验机制和错误检测处理,确保数据传输的准确性。
- **易扩展性**:能够支持通过增加总线扩展模块,轻松扩展系统规模。
示例的系统总线技术参数说明:
```plaintext
- 总线类型:工业以太网
- 传输速度:100 Mbps 至 1 Gbps 可选
- 接口标准:符合 IEEE 802.3 标准
- 物理介质:支持双绞线、光纤等多种介质
- 网络拓扑:星型、环形、总线型等多种结构
```
#### 2.2.2 现场通讯接口标准
现场通讯接口标准定义了控制器与现场设备之间的通信协议,它是自动化控制系统现场层的关键组成部分。HOLLiAS MACS-K系统遵循以下通讯接口标准:
- **Modbus RTU/TCP**:广泛用于工业设备之间的通讯。
- **Profibus**:主要用于大型分布式控制系统。
- **HART**:适用于模拟信号设备的数字通信。
在实现这些接口时,必须确保每个现场设备都已正确配置和调试,以保证通讯的稳定性和准确性。下面是一个Modbus通讯的简单示例代码:
```python
# Python示例代码:使用PyModbus库进行Modbus TCP通讯
from pymodbus.client.sync import ModbusTcpClient as ModbusClient
# 实例化Modbus客户端
client = ModbusClient('192.168.1.10', port=5020)
# 连接到服务器
client.connect()
# 读取从设备地址为1的保持寄存器的值,从地址0开始读取1个寄存器的值
result = client.read_holding_registers(0, 1, unit=1)
# 打印结果
if not result.isError():
print(result.registers)
else:
print("读取失败")
# 关闭连接
client.close()
```
### 2.3 硬件的可靠性与维护策略
#### 2.3.1 硬件故障的诊断方法
为了保证自动化控制系统稳定运行,硬件故障的及时诊断至关重要。HOLLiAS MACS-K系统提供了多种故障诊断方法:
- **自检功能**:系统启动时进行自检,检查硬件是否正常。
- **状态监控**:实时监控硬件运行状态,记录故障事件。
- **模块化检测**:故障发生时,对各个独立模块进行单独检测,快速定位问题。
在实现故障诊断功能时,通常会使用嵌入式系统或者专用的诊断工具。以下是一个简单的硬件故障诊断流程示例:
```plaintext
1. 系统自检:启动时执行自检程序,检查所有硬件模块。
2. 运行监控:在系统运行过程中,实时监控各模块的状态。
3. 故障指示:任何异常情况,系统会通过指示灯或屏幕显示故障信息。
4. 日志记录:记录详细的故障发生时间、类型和可能的原因。
5. 定位故障:根据记录的故障信息,使用专用工具或模块化测试方法进行故障定位。
```
#### 2.3.2 维护周期和更新计划
硬件维护周期和更新计划的制定,对于保证系统长期稳定运行有着重要的作用。主要考虑以下因素:
- **设备老化周期**:不同硬件设备有不同的平均使用寿命和老化周期,需要定期检查和更换。
- **技术更新换代**:随着技术的发展,硬件设备也需要进行升级,以保证系统的先进性。
- **维护成本**:维护成本和更新成本需要纳入计划,保证投入产出比最优化。
在维护周期和更新计划制定时,可以参考以下表格:
```markdown
| 硬件模块 | 常规检查周期 | 预期使用寿命 | 更新频率 | 维护成本 |
|----------|---------------|---------------|-----------|-----------|
| 控制器 | 每月 | 10年 | 5年 | 中等 |
| I/O模块 | 每季度 | 7年 | 3年 | 低 |
| 总线组件 | 每半年 | 8年 | 4年 | 高 |
```
通过合理安排硬件的维护周期和更新计划,可以有效地降低突发故障的发生,提高整个自动化控制系统的可靠性。
# 3. 自动化控制系统的软件支持
## 3.1 HOLLiAS MACS-K的操作系统
### 3.1.1 操作系统的选择与特点
在自动化控制系统中,操作系统作为底层软件的基石,为上层应用提供支持和服务。HOLLiAS MACS-K系统选择了嵌入式Linux操作系统,这种选择是基于其稳定性、可扩展性和丰富的开发资源。
Linux操作系统以其开源、稳定性、高效性和灵活性著称,这些都是自动化控制领域所必需的。尤其在需要长时间运行的控制系统中,Linux的稳定性能够确保系统的不间断工作。此外,其多样的开发工具链和社区支持,为开发者提供了极大的便利,有利于系统的定制化开发和维护。
嵌入式Linux可以裁剪到非常小的体积,这使得它可以适应各种控制硬件,而无需占用过多的系统资源。同时,由于Linux内核的模块化设计,开发者可以根据具体需求,灵活地添加或删除内核模块,实现系统的高度定制化。
### 3.1.2 系统管理与资源调度
系统管理是确保自动化控制系统可靠性和稳定性的关键。Linux内核提供了强大的进程管理功能,包括进程调度、内存管理、文件系统和设备驱动等。这些功能共同确保了控制任务可以高效、公平地分配资源并执行。
Linux的进程调度算法是高度优化的,它能够在保证系统响应速度的同时,实现CPU资源的均衡分配。这对于需要实时反馈的自动化控制系统来说至关重要。内存管理机制可以处理大量数据的快速流动,而不会导致系统卡顿或崩溃。文件系统则保证了数据的持久性和可靠性,特别是在系统遇到故障时数据的恢复能力。
资源调度是指操作系统如何分配有限的计算资源给多个进程,包括CPU、内存和I/O设备。Linux使用的是完全公平调度器(CFS),这是一种基于虚拟运行时间的调度算法,它尝试给每个进程公平的CPU时间片,同时考虑到进程的优先级。在自动化控制系统中,一些控制任务可能需要实时响应,因此Linux内核还支持实时调度策略,以满足这些任务的特殊需求。
```c
// 示例代码:Linux下创建一个新进程
#include <stdio.h>
#include <unistd.h>
int main() {
pid_t pid = fork(); // 使用fork()函数创建子进程
if (pid < 0) {
// fork失败的处理
fprintf(stderr, "Fork Failed");
return 1;
} else if (pid == 0) {
// 子进程
printf("Hello from the child process!\n");
} else {
// 父进程
wait(NULL); // 父进程等待子进程结束
printf("Hello from the parent process!\n");
}
return 0;
}
```
**代码逻辑解读:** 在上面的示例代码中,我们使用了`fork()`函数创建了一个新进程。这是Linux系统管理中的一个基础操作,允许我们复制当前运行的进程(父进程),以产生一个子进程。父进程与子进程可以执行不同的代码路径,子进程在此例中打印一条消息。父进程使用`wait()`函数等待子进程结束,以保证不会出现僵尸进程。
**参数说明:** `pid`是进程ID,`fork()`函数调用成功时返回子进程的ID,失败则返回-1。父进程和子进程的代码执行流程是通过返回值的不同来进行分支处理的。
### 3.2 控制算法与数据处理
#### 3.2.1 控制算法的应用实例
控制算法是自动化控制系统的核心,它是实现自动调节和控制的基础。HOLLiAS MACS-K系统中实现了多种控制算法,包括PID控制、模糊控制和先进控制策略等。在各种工业应用中,这些控制算法根据不同的工艺要求和控制目标,被应用在温度、压力、流量、液位等多个控制环节中。
PID控制算法是最常用的反馈控制算法,它包含了比例(P)、积分(I)和微分(D)三个组成部分,能够对系统的动态响应进行调节,以达到控制目标。模糊控制则是对那些难以用精确数学模型描述的复杂系统,通过模糊规则进行控制。而先进控制策略如模型预测控制(MPC)则能够处理多变量、具有复杂约束的控制问题。
以PID控制算法为例,其在温度控制系统中的应用可以如下图所示:
```mermaid
graph LR
A[设定温度] -->|反馈| B[PID控制器]
B -->|控制信号| C[执行机构]
C -->|加热| D[温度控制对象]
D -->|反馈| A
```
#### 3.2.2 数据采集与实时处理
实时数据采集和处理是自动化控制系统的重要组成部分。系统需要能够快速准确地从各个传感器和执行器采集数据,并进行实时处理和分析。
在HOLLiAS MACS-K系统中,数据采集模块通常与硬件接口紧密集成,能够以固定的时间间隔或事件触发的方式读取传感器数据。这些数据经过实时处理后,可用于更新系统状态,调整控制参数或触发报警。
实时处理数据的一个挑战在于确保数据处理的实时性。为此,通常会使用中断或轮询机制来实现快速响应。在Linux系统中,实时性可以通过实时内核补丁和实时调度策略来提高。例如,可以将控制循环设置为实时线程,并分配一个较高的优先级,以确保它们能够在指定的时间内得到处理。
```c
// 示例代码:使用Linux实时调度策略的实时任务
#include <stdio.h>
#include <stdlib.h>
#include <unistd.h>
#include <sys/time.h>
#include <sched.h>
#define DELAY 1000000
int main(void) {
int policy;
struct sched_param param;
struct timeval start, stop;
unsigned long startusec, stopusec;
// 获取当前策略和参数
if (sched_getparam(0, ¶m) == -1) {
perror("sched_getparam");
exit(EXIT_FAILURE);
}
// 获取当前调度策略
if (sched_getscheduler(0, &policy) == -1) {
perror("sched_getscheduler");
exit(EXIT_FAILURE);
}
// 设置调度策略为FIFO,并将任务的优先级设置为最高的1
param.sched_priority = 1;
policy = SCHED_FIFO;
if (sched_setscheduler(0, policy, ¶m) == -1) {
perror("sched_setscheduler");
exit(EXIT_FAILURE);
}
gettimeofday(&start, NULL);
for (int i = 0; i < 100; ++i) {
struct timespec req = { 0, 0 };
req.tv_sec = 0;
req.tv_nsec = 1000000; // 1 millisecond
nanosleep(&req, (struct timespec *) NULL);
}
gettimeofday(&stop, NULL);
startusec = (start.tv_sec * 1000000) + start.tv_usec;
stopusec = (stop.tv_sec * 1000000) + stop.tv_usec;
printf("Time difference = %lu\n", (stopusec - startusec));
return EXIT_SUCCESS;
}
```
**代码逻辑解读:** 在这个示例中,程序执行了一个实时调度策略,将当前进程设置为FIFO(先进先出)策略,并赋予了最高优先级。程序使用`nanosleep()`函数实现了高精度的延时,这对于需要严格时序控制的应用非常重要。示例代码也测量了程序执行的时间,以展示实时性。
**参数说明:** `policy`变量用于设置调度策略,这里设置为`SCHED_FIFO`,表示先进先出的实时调度策略。`param`结构体中的`sched_priority`字段设置了进程的优先级,数字越小优先级越高。`gettimeofday()`函数用于获取当前时间,用于计算延时后的总时间差。
### 3.3 用户界面与远程控制
#### 3.3.1 人机界面设计原则
人机界面(HMI)是自动化控制系统与操作人员交互的界面。一个良好的HMI设计可以大大提高操作效率和准确性,降低操作错误的可能性。HOLLiAS MACS-K系统的人机界面设计遵循以下原则:
- **简洁性**:界面应尽可能简单清晰,避免不必要的复杂性。
- **直观性**:操作应直观易懂,尽量减少操作人员的培训时间。
- **灵活性**:界面设计应具有灵活性,能够根据用户需求或工艺变化快速调整。
- **可靠性**:界面应确保操作指令能够准确无误地传达给控制系统。
#### 3.3.2 远程监控与故障管理
远程监控是现代自动化控制系统的重要组成部分。通过网络连接,操作人员可以在任何有网络覆盖的地方监控和控制自动化过程。HOLLiAS MACS-K系统支持多种远程监控技术,包括Web界面、移动应用和远程桌面等。
远程监控的优势在于,它使工程师能够在办公室或远程地点对现场设备进行监控和维护。这对于需要快速响应的场合尤为重要。此外,远程监控还可以作为故障管理和预防性维护的一部分,系统可以实时监控到各种异常情况,并通过报警机制通知相关人员。
```markdown
| 功能 | 描述 |
|------------|--------------------------------------------------------------|
| 状态监控 | 实时显示系统和设备的运行状态 |
| 参数配置 | 允许远程设置和调整系统参数 |
| 报警管理 | 通过邮件或短信通知远程操作员,实现故障的快速响应 |
| 数据记录 | 收集和存储历史运行数据,用于系统分析和故障排查 |
| 用户管理 | 远程管理用户账户和权限,确保系统的安全性 |
| 远程升级 | 支持远程软件更新,确保系统功能和安全性的持续更新 |
```
在表格中总结了远程监控与故障管理的一些关键功能及其描述。表格是将信息进行清晰展示的有效方式,特别是在列出功能时。通过表格,操作人员可以快速查阅和理解系统功能和对应的操作方法。
远程监控和故障管理功能不仅使得系统的维护更加便捷,而且还能够提高整个生产线的可靠性。通过及时的监控和预警,可以预防许多潜在的系统故障,从而减少生产损失和维护成本。同时,这种远程管理能力也使得企业可以更好地应对全球化的竞争和挑战。
上述内容为第三章“自动化控制系统的软件支持”中第三小节“用户界面与远程控制”的部分介绍。由于本小节内容量较大,以上仅展示了一部分,详细内容会包含在完整的章节中。完整的章节还会包括更多对实际应用和操作的深入分析以及相关的图表、示例代码和步骤说明。
# 4. 自动化控制系统的性能优化
自动化控制系统的性能优化是一个持续的过程,它涉及对系统的关键性能指标(KPIs)的持续评估,并根据评估结果对系统进行调优。本章节将深入探讨性能优化的不同方面,包括系统评估、调优方法、系统升级以及兼容性问题,并通过案例研究展示一个成功的自动化升级项目。
## 4.1 性能评估与调优方法
### 4.1.1 关键性能指标分析
在进行性能优化之前,首先需要明确的关键性能指标(KPIs)。对于自动化控制系统来说,通常关注以下几个方面:
- **响应时间**:系统从接收到输入信号到输出控制响应之间的时间。
- **吞吐量**:系统在单位时间内能够处理的任务数量。
- **资源利用率**:包括CPU、内存和网络等资源的使用率。
- **可靠性和可用性**:系统无故障运行时间和从故障中恢复的能力。
- **准确性**:控制系统的输出与预期目标的偏差大小。
准确地识别和测量这些KPIs是性能评估的基础。它们可以帮助我们确定系统瓶颈所在,以及调优的方向。
### 4.1.2 系统调优工具和技术
一旦确定了关键性能指标,我们可以采用各种工具和技术来进行系统调优。以下是一些常见的调优手段:
- **代码优化**:检查和优化程序代码,去除冗余逻辑,使用更高效的数据结构和算法。
- **参数调整**:调整操作系统和应用程序的配置参数,如缓冲区大小、线程数量等。
- **资源管理**:合理分配和管理系统资源,确保关键任务获得必要资源。
- **负载均衡**:通过负载均衡技术来分配工作负载,避免单个节点过载。
系统调优是持续的过程,应定期进行性能评估,并根据评估结果调整优化策略。
## 4.2 系统升级与兼容性问题
### 4.2.1 硬件升级的策略和步骤
硬件升级是提高自动化控制系统性能的重要手段。在制定升级策略时,需要考虑以下几个步骤:
1. **性能评估**:首先评估现有硬件的性能,确定是否满足当前和未来的需求。
2. **选择升级方案**:根据性能需求选择合适的硬件组件进行升级,如更强大的处理器、更多的内存等。
3. **实施升级**:按照预定计划和步骤进行硬件替换或添加,并确保数据和系统的连续性。
4. **测试验证**:升级后进行彻底的测试,确保新硬件与旧硬件和软件的兼容性,并验证系统性能提升。
### 4.2.2 软件兼容性测试与解决方案
随着硬件的升级,软件的兼容性也成为了一个重要考虑因素。软件兼容性测试通常包括以下几个方面:
- **操作系统兼容性**:确保新硬件支持当前的操作系统版本。
- **应用程序兼容性**:升级后,检查自动化控制软件是否能够正常运行在新硬件上。
- **驱动和固件更新**:安装必要的驱动和固件更新以支持新硬件。
兼容性问题通常可以通过及时的更新和补丁来解决,但是需要提前规划并做好数据备份。
## 4.3 案例研究:成功的自动化升级项目
### 4.3.1 升级前的系统评估
在自动化控制系统升级项目开始之前,项目团队对现有系统进行了彻底的评估。评估内容包括:
- **硬件资源利用率**:监控显示,许多硬件资源并未得到充分利用,存在性能浪费。
- **响应时间与吞吐量**:某些关键任务的响应时间较长,吞吐量无法满足高峰期的需求。
- **历史故障分析**:频繁发生硬件故障,且与过时的硬件有关。
基于评估结果,项目团队决定进行硬件升级,重点优化响应时间和吞吐量,并更换易故障硬件。
### 4.3.2 实施过程与遇到的挑战
升级过程分为几个阶段:
1. **硬件采购**:根据评估结果,采购了新的服务器、存储设备和网络硬件。
2. **系统迁移**:将旧硬件上的服务迁移到新硬件,并确保数据完整性和连续性。
3. **兼容性测试**:执行了详尽的兼容性测试,确保所有关键软件能够在新硬件上正常运行。
4. **性能优化**:根据测试反馈进行了一系列性能优化。
在实施过程中,团队遇到了以下挑战:
- **数据迁移的复杂性**:确保数据从旧系统迁移到新系统时的一致性和完整性。
- **应用兼容性问题**:部分旧版应用软件在新硬件上存在兼容性问题,需要额外的调试和补丁安装。
### 4.3.3 升级后的效益分析
升级完成后,系统性能有了显著提升:
- **响应时间缩短**:关键任务的响应时间从之前的几秒减少到毫秒级别。
- **吞吐量增加**:系统能够处理更多的并发任务,提升了处理能力。
- **故障率降低**:更换了更高性能和稳定性的硬件,故障率大幅下降。
此外,系统的维护成本也因为硬件的提升和优化而有所降低。项目总体实现了预期目标,为公司带来了更多的经济效益。
性能优化是自动化控制系统持续演进的一部分,通过上述案例可以看出,一个周密的性能评估、升级和优化流程,对提升整个系统的效率和可靠性至关重要。
# 5. 面向未来的自动化控制系统发展
随着科技的不断进步,自动化控制系统也在不断地演进,逐渐向智能化、网络化、服务化的方向发展。未来,自动化控制系统将如何适应工业4.0带来的新挑战和机遇,本章节将从工业物联网、智能制造以及预测性维护与大数据分析三个方面进行深入探讨。
## 5.1 工业物联网与自动化控制
### 5.1.1 工业物联网的基本概念
工业物联网(Industrial Internet of Things,IIoT)是指将具有网络连接能力的传感器、设备和其他物品嵌入到制造设备、供应链和生产流程中,通过数据分析与智能决策支持,从而提高效率、减少成本并增强产品和服务的附加值。IIoT的目标是实现更加智能、自动化的生产系统,它不仅涉及到技术层面的革新,还包括业务流程、商业模式甚至是整个工业生态系统的变革。
### 5.1.2 物联网与自动化控制的结合
将物联网技术与自动化控制结合,意味着要在传统的自动化控制系统中加入网络通讯能力。这要求控制系统具备更加高效的处理和分析数据的能力,以及能够与其他系统和设备无缝集成的开放性。例如,通过无线传感器网络收集数据,然后通过云计算平台进行分析,可以实现对生产过程的实时监控和预测维护。
## 5.2 智能制造与自动化控制系统
### 5.2.1 智能制造的内涵与趋势
智能制造是一种全新的制造模式,它综合了信息技术、制造技术和智能技术,通过物联网、大数据分析、人工智能、云计算等手段,实现制造过程的智能化。智能制造的趋势在于高度自动化、灵活性和可持续性,能够应对快速变化的市场需求和生产条件。
### 5.2.2 自动化控制系统在智能制造中的角色
在智能制造中,自动化控制系统是实现生产过程智能化的核心。控制系统不仅需要高度的集成能力和互操作性,还要具有一定的自主决策能力,以适应复杂多变的生产场景。例如,在智能工厂中,自动化控制系统能够自动调整生产线,以满足不同产品的定制化需求。
## 5.3 预测性维护与大数据分析
### 5.3.1 预测性维护的原理和优势
预测性维护(Predictive Maintenance)是通过实时监控设备状态,分析历史和实时数据,预测设备可能发生的故障,并在故障发生前进行维护。与传统的预防性维护(定期维护)相比,预测性维护能够减少意外停机时间、延长设备寿命、减少维护成本,并提高系统的整体可靠性。
### 5.3.2 大数据分析在自动化系统中的应用前景
大数据分析技术在自动化控制系统中的应用,使得系统可以处理和分析海量的生产数据。通过分析这些数据,可以识别出设备的潜在问题,优化生产过程,甚至实现对未来趋势的预测。举例来说,通过分析机器运行的历史数据,系统可以预测设备何时需要维护,从而避免生产中断和减少维护成本。
通过本章节的探讨,我们可以看到,未来的自动化控制系统将不再是单一的控制系统,而是集成了工业物联网技术、智能制造理念以及大数据分析能力的复合型系统。这将极大地提升制造业的生产效率和质量,同时也为自动化控制系统的发展提出了更高的要求和挑战。
0
0
相关推荐







