炉温控制系统案例分析:全过程问题解决策略
发布时间: 2025-01-05 00:03:12 阅读量: 48 订阅数: 20 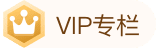
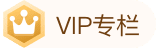
# 摘要
炉温控制系统是工业热处理过程中至关重要的技术设施,其性能直接影响产品的质量和生产效率。本文首先概述了炉温控制系统的基本概念,随后深入探讨了其理论基础,包括工作原理、硬件组成和软件架构。接着,本文着重分析了炉温控制系统在实际应用中可能遇到的问题及其解决方法,强调了问题诊断和维护升级的重要性。此外,通过设计实践部分,本文展示了控制系统设计、模拟测试到现场实施的整个过程。最后,本文展望了炉温控制系统未来的发展趋势,包括智能化、自动化、节能减排以及标准化和规范化的重要性,为相关领域的研究和应用提供了指导。
# 关键字
炉温控制系统;理论基础;问题诊断;设计实践;智能化自动化;节能减排
参考资源链接:[炉温控制系统设计:串联滞后-超前校正与Matlab仿真](https://wenku.csdn.net/doc/644b859bfcc5391368e5efe0?spm=1055.2635.3001.10343)
# 1. 炉温控制系统概述
炉温控制系统是工业生产中确保产品质量的关键技术之一,通过精准控制炉内温度,来达到优化生产过程和提高产品一致性的目的。本章将简要介绍炉温控制系统的概念、其在不同工业应用中的重要性以及基本工作流程。
## 1.1 炉温控制系统的定义和作用
炉温控制系统主要由传感器、控制器和执行机构组成。它根据设定的温度曲线,实时监测炉内的实际温度,并自动调整加热功率或冷却速率,以达到或保持理想的温度水平。通过精确控制炉温,可以减少产品缺陷、提高生产效率,以及优化资源消耗。
## 1.2 炉温控制在工业中的应用
在冶金、陶瓷、玻璃、半导体等多个行业中,炉温控制都是不可或缺的技术。例如,在半导体制造中,炉温控制影响到晶圆的品质和良率;而在陶瓷行业,温度的稳定直接关系到产品的强度和外观质量。炉温控制系统的精准性直接关联到企业的经济效益。
## 1.3 炉温控制系统的发展历程
从最初的简单手动控制到现在的计算机自动化控制,炉温控制系统经历了快速的发展。如今,先进的炉温控制系统已经整合了智能算法和物联网技术,实现更高级别的自动化与远程监控,进一步提升了温度控制的精确度和生产效率。
# 2. 炉温控制系统的理论基础
## 2.1 炉温控制系统的工作原理
### 2.1.1 温度传感器的工作机制
温度传感器是炉温控制系统中感知温度的关键部件。它利用物理、化学、电子等原理实现对温度的测量。例如,热电偶传感器通过塞贝克效应将温度变化转换为电压信号,而热电阻(RTD)则通过金属导体电阻随温度变化的性质来测量温度。
```mermaid
graph LR
A[温度变化] --> B[热电偶产生电压]
A --> C[热电阻电阻变化]
B --> D[温度转换为电信号]
C --> D
```
在实际应用中,传感器会将信号传输给控制器,控制器根据设定的控制算法将信号转换为控制指令,进而驱动执行机构对炉温进行调节。
### 2.1.2 控制算法的选择与优化
控制算法是炉温控制系统的核心,它根据传感器的反馈信息,计算出控制指令。常见的控制算法包括PID(比例-积分-微分)控制、模糊控制、自适应控制等。PID控制因其简单有效,广泛应用于炉温控制系统。算法的选择和优化直接影响系统的响应速度、稳定性和准确性。
一个典型的PID控制器的控制方程为:
```
u(t) = Kp * e(t) + Ki * ∫ e(t) dt + Kd * de(t)/dt
```
其中,`u(t)` 是控制器的输出,`e(t)` 是偏差信号(期望值与实际值之差),`Kp`、`Ki`、`Kd` 分别是比例、积分、微分系数。
在优化方面,需要对PID参数进行调整以适应不同工作条件。调整过程可以通过经验法、Ziegler-Nichols方法等来进行。在实际操作中,通过软件工具或现场测试,逐步优化PID参数,以达到最佳控制效果。
## 2.2 炉温控制系统的硬件组成
### 2.2.1 硬件选型的标准和考虑因素
炉温控制系统硬件的选择是确保系统稳定运行的基础。在选型时需考虑以下标准和因素:
1. **温度范围**:传感器和执行机构应能覆盖炉内温度变化的范围。
2. **精度和稳定性**:所选硬件必须保证温度测量和控制的精度及长期稳定性。
3. **响应时间**:控制系统需要快速响应温度变化,及时进行调整。
4. **兼容性和扩展性**:硬件应能与现有的系统兼容,并留有扩展空间。
5. **成本效益**:在满足以上条件的同时,还需考虑经济成本,进行性价比分析。
### 2.2.2 主要部件的功能解析
炉温控制系统的核心部件包括温度传感器、控制器、执行器和通信接口等。
- **温度传感器**:负责实时监测炉内温度,将温度信号转换为电信号。
- **控制器**:接收传感器信号,根据控制算法进行计算,并输出控制指令。
- **执行器**:执行控制器发出的指令,调节炉温,如调节气体流量、炉门开关等。
- **通信接口**:负责将各部件连接起来,实现数据的交换和通信。
## 2.3 炉温控制系统的软件架构
### 2.3.1 控制软件的设计要求
炉温控制软件需要满足实时性、可靠性和用户友好性的设计要求。软件设计应保证以下几点:
- **实时监控**:能够实时采集传感器数据,并迅速作出响应。
- **用户界面**:提供直观的用户界面,方便操作人员进行监控和设置。
- **数据记录**:记录操作日志和温度变化数据,用于后续的分析和优化。
- **远程控制**:支持远程访问和控制,便于远程诊断和维护。
- **系统安全**:具备必要的安全防护措施,防止未授权访问和数据泄露。
### 2.3.2 软件与硬件的协同工作方式
炉温控制系统软件和硬件的协同工作需要依赖于有效的通信协议。典型的软件架构包括三个层次:感知层、处理层和应用层。
- **感知层**:负责与传感器和执行器通信,获取数据和执行指令。
- **处理层**:包含控制算法,负责处理数据和生成控制指令。
- **应用层**:提供用户界面,显示数据,接收用户指令,并与处理层交互。
这样的架构设计有利于系统的模块化和扩展性,便于维护和升级。在设计时,需要对各层之间的通信机制进行详细规划,确保数据传输的准确性和实时性。
# 3. 炉温控制系统的问题诊断与解决
炉温控制系统的稳定运行对于生产质量和效率至关重要。然而,系统可能遇到各种问题,如温度波动、响应迟缓或完全故障,都会对整个生产过程造成负面影响。因此,能够快速准确地诊断和解决这些问题,对于维护生产连续性和保障产品质量是必不可少的。本章将深入探讨炉温控制系统中可能出现的问题,并提供诊断和解决方案,以及系统的维护和升级策略。
## 3.1 炉温不稳定的分析与调整
炉温的不稳定是炉温控制系统中遇到的常见问题。温度波动可能由多种因素引起,包括传感器故障、控制算法不匹配、硬件故障或外部干扰等。
### 3.1.1 常见不稳定因素的排查
排查炉温不稳定因素的第一步是检查温度传感器的准确性。传感器可能因为老化、污染或损坏而导致读数误差。可以使用已知温度的参考点校准传感器,或更换新的传感器以确认是否为传感器问题。
其次,控制算法的优化也是关键。传统的PID控制算法可能不适用于所有情况,特别是在复杂的热工过程中。使用先进的控制算法如模糊逻辑、神经网络或自适应控制方法,可能提供更好的结果。通过调整控制参数,如PID的P(比例)、I(积分)、D(微分)值,可以改善系统的响应性与稳定性。
### 3.1.2 稳定炉温的策略和方法
在确认传感器和控制算法无误后,就需要考虑其他可能的不稳定因素。例如,炉内的加热元件可能由于老化或损坏导致加热不均匀,需要检查和维护加热元件。此外,炉内的气流分布也是一个重要的考虑因素。气流不均匀会导致温度不均,需要优化气流设计或调整风门设置以实现均匀的热分布。
对于稳定炉温的策略,可以采用以下几种方法:
1. **动态补偿**:根据实时温度反馈动态调整控制输入,以抵消系统内部和外部的干扰。
2. **预测控制**:使用数学模型预测未来的系统行为,并预先调整控制策略以应对预期的变化。
3. **模糊控制**:针对不确定性环境采用模糊逻辑来优化控制决策,尤其是在难以用精确数学模型描述的过程。
## 3.2 炉温控制系统故障的排除流程
炉温控制系统出现故
0
0
相关推荐








