编程案例分析:S7 PLC在制造业中的3大应用场景
发布时间: 2025-01-08 14:38:59 阅读量: 9 订阅数: 12 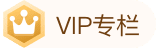
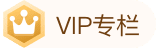
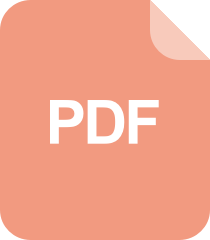
S7-300 400 PLC编程设计与案例分析(中)(设计与应用)37MB
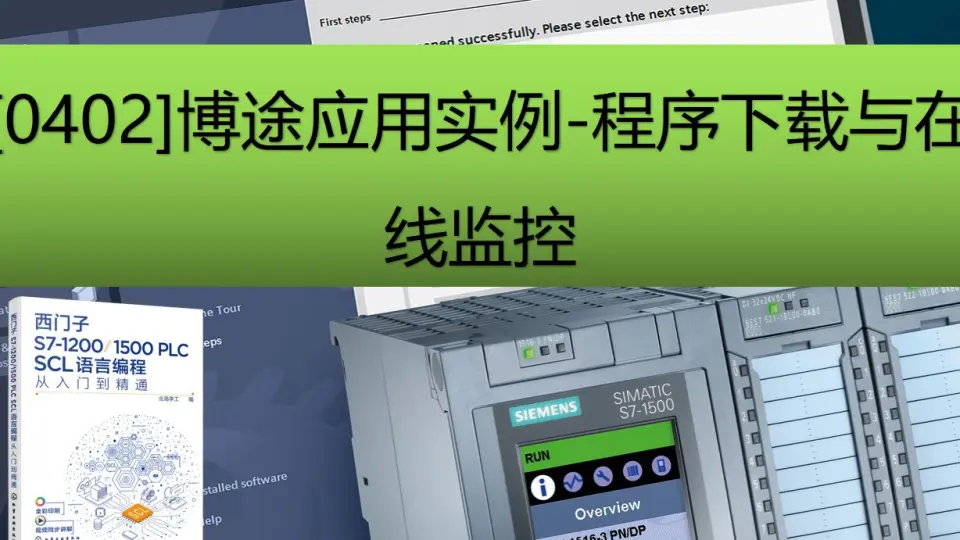
# 摘要
本文详细介绍S7 PLC的工作原理及其在制造业中的应用,探讨了它在自动化装配线控制、机器人协同作业和智能仓储管理中的关键作用。文章还阐述了S7 PLC的编程语言、故障诊断和系统优化等实践技巧,并通过案例分析展示了S7 PLC在实际制造业环境中的应用效果和优势。通过系统化梳理和深入分析,本文旨在为相关领域技术人员提供宝贵的知识和经验分享,以优化生产流程、提升系统效率。
# 关键字
S7 PLC;制造业应用;自动化控制;机器人通信;智能仓储;系统优化
参考资源链接:[Sharp7:C#与西门子PLC通信的参考手册](https://wenku.csdn.net/doc/64657c145928463033ce2e37?spm=1055.2635.3001.10343)
# 1. S7 PLC的简介和基本原理
## 1.1 S7 PLC的简介
S7 PLC是西门子公司生产的一款广泛应用于工业自动化的可编程逻辑控制器。它具有强大的处理能力,灵活的配置方式,以及丰富的指令集,使其在复杂的工业控制任务中表现出色。
## 1.2 S7 PLC的基本原理
S7 PLC的基本工作原理是通过输入/输出模块接收和发送信号,根据用户编写的控制程序,执行逻辑运算、计时、计数等功能,从而控制各种工业设备和生产线。它的核心是中央处理单元(CPU),负责执行程序和管理数据。
## 1.3 S7 PLC的优势
S7 PLC的优势在于它的稳定性和可靠性,能够长时间在恶劣的工业环境中稳定运行。同时,它的编程语言标准化,使得工程师能够快速学习和使用。另外,它还具有强大的网络功能,可以方便地与其他系统进行数据交换和通信。
通过以上内容的介绍,我们可以看到,S7 PLC在工业自动化领域具有非常重要的地位。接下来的章节,我们将深入探讨S7 PLC在制造业中的应用,以及如何进行编程和实践。
# 2. S7 PLC在制造业中的应用
## 2.1 自动化装配线控制
### 2.1.1 装配线的工作流程和控制需求
自动化装配线是制造业中不可或缺的环节,其工作流程包括从原料的供给、产品的组装、检测、到最后的打包出货。由于生产线上的产品种类繁多,生产节奏快,因此对控制系统的响应速度、准确性和可靠性提出了很高的要求。
工作流程中涉及到各种传感器、执行器、以及搬运设备。例如,光电传感器用于检测物料到位状态,伺服电机执行精确的位移控制,而机械手臂则负责物料的抓取和搬运工作。此外,装配线上的每个环节都需要严格的时间控制,以确保整个装配过程的同步和流畅。
一个典型的装配线控制系统通常包含以下控制需求:
- 实时监控:对生产线运行状态进行实时监控,及时发现异常。
- 数据采集:采集生产过程中的各种数据,进行质量控制和分析。
- 过程控制:精细控制各个执行元件,确保生产过程的准确执行。
- 故障诊断:迅速诊断并处理故障,最小化生产线停机时间。
在所有这些需求中,PLC作为中央处理单元,承担着协调和执行各种控制任务的角色。
### 2.1.2 PLC在装配线控制中的应用
PLC(可编程逻辑控制器)是自动化装配线控制的核心,它的主要作用是接收来自传感器的信号,根据预设的逻辑控制执行器的动作,从而实现对装配线的精确控制。
在装配线控制中,PLC主要通过以下方式实现其作用:
- 输入/输出管理:PLC通过输入端口接收来自传感器的信号,并根据这些信号通过预设的程序来控制输出端口,驱动执行器动作。
- 程序逻辑控制:PLC执行编写好的控制程序,根据装配线当前状态和预设的控制逻辑决定输出信号。
- 通讯功能:PLC可以与生产线上的其他设备通讯,如交换数据、同步工作或者接收远程指令。
下面是一个简化的装配线控制流程的示例:
```plaintext
1. PLC接收传感器S1的信号(物料到位)。
2. PLC执行内部程序判断。
3. PLC根据程序逻辑输出信号到驱动器D1(控制机器人手臂动作)。
4. 物料被机器人手臂搬运到指定位置。
5. PLC控制检测设备E1进行质量检测。
6. 检测结果反馈给PLC,PLC根据结果输出信号到指示灯L1(合格/不合格指示)。
```
在上述流程中,PLC不仅保证了装配线的自动化运行,还实现了对装配质量的实时监控和反馈,大大提高了生产效率和产品的一致性。
## 2.2 机器人协同作业
### 2.2.1 机器人与PLC的通信机制
在现代制造系统中,机器人与PLC的协同工作越来越常见。机器人负责完成复杂的动作任务,而PLC则负责处理更高层次的控制逻辑和系统协调。它们之间的通信机制是确保协同作业顺利进行的关键。
通常,机器人与PLC之间的通信可以通过以下几种方式进行:
- **串行通信**:使用RS-232/RS-485等标准进行点对点通信。
- **现场总线**:如Profibus、Profinet、Ethernet/IP等,它们支持多设备间的网络通信。
- **工业以太网**:通过TCP/IP协议实现设备间的数据交换。
在实际应用中,通信协议的选择需要根据实际的系统需求和设备兼容性来决定。例如,若控制系统要求高速度和高可靠性,可能会选择支持实时通信的Profibus或Profinet协议。
### 2.2.2 PLC在机器人协同作业中的角色和作用
在机器人协同作业中,PLC的作用至关重要。PLC需要做到以下几个方面:
- **信号管理**:通过输入/输出接口管理机器人的各种信号,如启动、停止、急停等。
- **状态监测**:实时监测机器人状态,包括位置、速度和力矩等,确保机器人的动作符合生产需要。
- **协调控制**:根据生产工艺流程,指挥机器人进行恰当的协同操作。
- **故障处理**:检测到异常后,PLC能够及时进行故障诊断,并采取相应措施,减少停机时间。
PLC与机器人协同作业的流程通常如下:
```plaintext
1. PLC接收生产任务指令。
2. PLC根据任务需求,发送控制信号给机器人。
3. 机器人执行动作,如移动到特定位置,抓取物料。
4. 机器人完成动作后,向PLC发送完成信号。
5. PLC根据机器人的完成信号,发送下一阶段的指令。
```
在整个流程中,PLC作为指挥中心,确保了机器人的动作与生产节拍相协调,同时保证了整个生产过程的稳定性和可靠性。
## 2.3 智能仓储管理
### 2.3.1 仓储管理的挑战和需求
随着现代制造业的发展,仓储管理面临着越来越多的挑战。例如,订单量的增加、产品种类的增多、以及对快速配送的需求提升,这些都对仓储管理提出了新的要求。传统的仓储管理方式已经难以满足这些需求,因此,智能仓储的概念应运而生。
智能仓储管理系统需要解决的主要挑战包括:
- **库存准确性**:确保库存信息的准确性,减少过剩或缺货的情况。
- **出入库效率**:提高物品的入库和出库效率,缩短库存周转时间。
- **空间利用率**:优化仓库空间的使用,提高存储密度。
- **作业安全性**:确保作业过程的安全,降低事故发生的可能性。
为了满足这些需求,智能仓储系统通常会集成多种技术,包括自动化设备、信息技术和人工智能等。其中,PLC作为控制核心,在自动化设备的运行和协调中扮演着关键角色。
### 2.3.2 PLC在智能仓储中的应用和优势
PLC在智能仓储中的应用广泛,包括但不限于对自动化的堆垛机、输送带、分拣系统等的控制。PLC的应用给智能仓储管理带来了以下优势:
- **高可靠性和稳定性**:PLC作为成熟的工业控制产品,具有高度的稳定性和可靠性,保证了智能仓储系统的长时间稳定运行。
- **快速响应能力**:PLC的响应速度快,可以即时处理仓储过程中的各种实时事件。
- **强大的扩展性**:PLC系统具有良好的扩展性,随着仓储系统规模的扩大,可以方便地进行系统升级和扩展。
一个典型的PLC在智能仓储系统中的应用场景如下:
```plaintext
1. PLC接收上位机的库存管理指令。
2. PLC根据指令控制堆垛机将货物放到指定货位。
3. 当有出库需求时,PLC控制输送带将货物运至分拣区。
4. 分拣完成后,PLC指挥装卸机械臂将货物装载到配送车辆
```
0
0
相关推荐







