【西门子840DSL NC初探】:成为数控专家的快速入门指南
发布时间: 2024-12-15 12:04:11 阅读量: 4 订阅数: 5 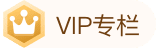
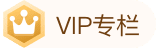
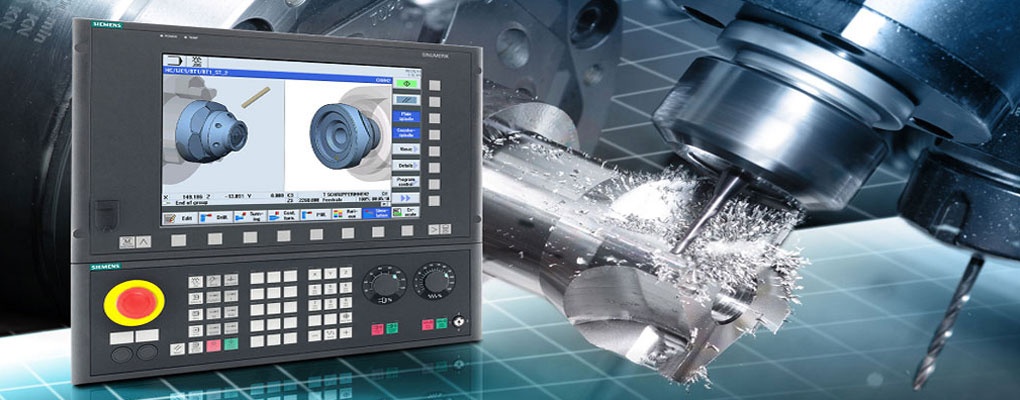
参考资源链接:[西门子840DSL-NC变量与接口信号详解与安全指南](https://wenku.csdn.net/doc/5j8hswi27x?spm=1055.2635.3001.10343)
# 1. 西门子840DSL NC概述
## 1.1 西门子840DSL NC简介
西门子840DSL数控系统(NC)是工业自动化领域的经典之作,广泛应用于金属加工、木材加工及其他高精度制造领域。作为一个成熟的数控解决方案,840DSL提供了一个功能强大且灵活的平台,能够满足各种复杂的加工需求。
## 1.2 系统的特点与优势
840DSL NC系统的主要特点包括:
- **模块化设计**:方便用户根据需要选择和升级组件。
- **高度的用户自定义性**:允许用户定制操作界面与功能以适应特定的工业环境。
- **开放式通讯协议**:支持多种工业通讯协议,便于与其他系统集成。
通过这些优势,840DSL NC系统能够在保证加工精度的同时,提高生产效率和设备的可维护性。
## 1.3 应用场景
840DSL NC在众多制造环境中发挥关键作用,包括但不限于:
- 车床、铣床和磨床等传统数控机床。
- 复杂多轴加工中心和专业制造设备。
- 自动化生产线,特别是需要高度同步与精确控制的场合。
下一章节将详细介绍840DSL NC的系统架构和组件,揭示其背后的强大技术支撑。
# 2. 840DSL NC的系统架构和组件
## 2.1 硬件组成分析
### 2.1.1 控制器与驱动器
在840DSL NC系统中,控制器和驱动器是整个数控机床的核心。控制器负责解析加工程序,并发送指令给驱动器来控制机床各轴的移动。西门子840DSL控制器采用了模块化的设计,使得系统可以根据不同应用需求进行配置。
驱动器方面,西门子提供了与其控制器相匹配的交流伺服驱动器。这些驱动器具有高性能的动态响应能力和较高的精度,确保了加工过程中的精确控制。驱动器通过数字化控制,实现了更加稳定和高效的运动控制。
### 2.1.2 输入/输出模块
输入/输出模块在数控系统中起着连接机床控制逻辑与外部信号的桥梁作用。通过这些模块,数控系统可以接收来自机床的传感器信号,并根据这些信号控制机床的动作,如开关冷却系统、启动紧急停止等。输入输出模块通常包含有数字量输入输出模块、模拟量输入输出模块以及高速计数器模块等。
### 2.1.3 人机界面(HMI)
人机界面(HMI)是数控机床与操作者交互的界面。西门子840DSL的HMI提供了一个直观的操作和监控平台,支持多语言界面,方便操作者快速了解机床状态,并执行相应的操作。界面设计考虑到了操作的便捷性,包含了诸如图形化操作、触摸屏控制和状态指示灯等功能。
### 2.1.4 硬件组件的协同工作
所有硬件组件之间通过内部总线系统协同工作。控制器向驱动器发送指令,驱动器负责将指令转换为机械动作;同时,输入输出模块不断地从机床中收集信号并传递给控制器;而HMI则将整个系统的状态和控制指令通过可视化的形式展示给操作者。这种硬件组件之间的高效协同是实现高精度加工的基础。
## 2.2 软件结构详解
### 2.2.1 操作系统的角色
西门子840DSL NC系统采用了操作系统来管理整个数控系统的资源。操作系统负责任务调度、内存管理以及文件系统等。良好的操作系统设计可以保证数控系统运行的稳定性和可靠性,同时操作系统还可以提供用户程序的运行环境。
### 2.2.2 标准软件包功能
标准软件包包含了一系列预设的加工程序和功能,比如标准循环、图形模拟、刀具补偿等。这些功能使得操作者能够更加便捷地进行编程和操作,无需从头开始编写复杂的程序代码。标准软件包内还包含了多种工艺参数的设置,适用于不同的加工场合。
### 2.2.3 用户自定义功能和扩展
虽然标准软件包提供了许多便利功能,但在实际应用中,用户可能需要根据自己的特定需求进行功能的定制和扩展。用户可以利用西门子提供的开发环境和API来编写自定义功能,实现特定的控制逻辑或加工策略。
## 2.3 系统集成与网络通讯
### 2.3.1 工业以太网集成
随着工业自动化的发展,网络通讯变得越来越重要。西门子840DSL NC系统支持工业以太网通讯协议,可实现与工业自动化系统的无缝集成。通过工业以太网,数控机床可以与其他生产设备或管理系统进行数据交换,提升整个生产线的自动化和智能化水平。
### 2.3.2 总线通讯技术
总线通讯技术是数控机床内部各个模块之间高效数据交换的基础。西门子840DSL NC系统兼容多种总线技术,如Profibus和Profinet,确保了不同设备和模块间可以稳定、快速地通讯。总线技术的引入,使得机床可以组成更加复杂而灵活的制造系统。
### 2.3.3 远程诊断与维护
远程诊断和维护技术让制造商能够即使不在现场也能对数控机床的状态进行监测和故障排查。通过连接到互联网,技术专家可以远程访问机床的控制系统,对机床进行优化调整或远程修复,极大提高了服务效率和生产连续性。
通过本章节的介绍,读者应该对840DSL NC系统的硬件组成、软件结构以及系统集成与网络通讯有了深入的了解。接下来章节将进一步探索840DSL NC的编程基础和高级功能应用。
# 3. 840DSL NC的编程基础
## 3.1 数控编程语言
数控机床的核心在于其编程,使得机床能够按照预定的程序执行相应的动作。在这一部分中,我们将深入探讨数控编程语言,特别是G代码和M代码的使用,以及参数化编程和循环的基础知识。
### 3.1.1 G代码和M代码的使用
G代码(几何代码)和M代码(辅助功能代码)是数控编程中最基础和至关重要的元素。它们是向数控系统发送控制指令的手段,告诉机床如何移动,以及在加工过程中需要执行哪些功能。
- **G代码**用于定义机床的运动轨迹。例如,G01表示直线插补,G02和G03分别表示顺时针和逆时针圆弧插补。
- **M代码**用于控制机床的其他操作,比如开关主轴(M03启动,M05停止),冷却液的开关(M08启动,M09停止)等。
**代码块示例:**
```gcode
G21 ;设置单位为毫米
G90 ;使用绝对坐标系统
G17 ;选择XY平面
M06 T01 ;换到工具号1
M03 S1200 ;以1200转/分钟的速度启动主轴
G00 X0 Y0 Z5 ;快速移动到起始位置
G01 Z-5 F100 ;以100毫米/分钟的进给率下刀到Z-5mm
G02 X10 Y10 I5 J5 ;顺时针画一个半径为5mm的圆弧到X10 Y10
M05 ;停止主轴
```
在这段示例代码中,首先通过G代码设置了工件坐标系、平面选择和单位,然后使用M代码选择工具并控制主轴的启动和停止。G代码被用来控制工具的移动路径,包括快速定位和线性插补。
### 3.1.2 参数化编程和循环
参数化编程和循环是提高数控编程效率和灵活性的有效手段。参数化编程允许编程者使用变量,这使得程序能够适应不同的工件尺寸和加工条件。循环可以简化重复性任务,减少代码量,提高加工效率。
**代码块示例:**
```gcode
#100=5.0 (定义一个变量 #100,初始值为5.0)
#101=10.0 (定义一个变量 #101,初始值为10.0)
#102=5.0 (定义一个变量 #102,初始值为5.0)
WHILE [#102 LT #101] DO1 (如果#102小于#101,执行循环)
G00 X#102 (移动到X轴位置#102)
G01 Z-#102 F100 (Z轴向下移动#102单位,以100mm/min的进给率)
#102=[#102+#100] (变量#102自增#100)
END1
```
在这个循环结构中,刀具以100mm/min的进给率在Z轴方向连续下移5mm,直到X轴的位置达到10mm。每次循环结束后,X轴的位置增加5mm。
## 3.2 工具和刀具管理
管理工具和刀具是确保加工质量和效率的关键步骤。本小节将重点讲解工具数据的定义和管理,以及刀具寿命和补偿。
### 3.2.1 工具数据的定义和管理
数控机床能够高效、精确地运行的关键之一是准确的工具数据。工具数据通常包括工具长度、直径、类型、材质和切削参数等。
- **工具数据定义**:通常通过机床的HMI或者使用专业的工具管理软件来完成。
- **工具数据管理**:涉及到工具寿命的监控、刀具磨损补偿和刀具寿命的自动替换。
**代码块示例:**
```gcode
T1 D1 M06 ;选择工具号1,并从刀具库中加载
#103=150.0 ;定义变量#103为当前刀具的长度补偿值
G43 Z10 H1 ;应用长度补偿,并移动到Z轴10mm的位置
```
在这里,我们使用T和D指令定义了一个工具号和刀具直径,然后通过G43指令结合H参数应用了长度补偿。
### 3.2.2 刀具寿命和补偿
刀具寿命管理是确保加工质量的重要环节。通过追踪刀具的使用时间和加工件数,能够及时进行刀具更换,避免因刀具磨损过度而影响工件质量。刀具补偿功能允许操作者对刀具磨损造成的尺寸偏差进行校正,以维持加工精度。
**表格展示刀具磨损管理:**
| 刀具编号 | 加工件数 | 使用时间 | 更换周期 |
|----------|----------|----------|----------|
| T1 | 200 | 120小时 | 250件 |
| T2 | 100 | 150小时 | 200件 |
| ... | ... | ... | ... |
通过上表可以简单地追踪不同刀具的磨损状态,并根据既定的更换周期进行刀具更换。
## 3.3 加工程序的创建和调试
创建和调试加工程序是数控编程中的重要环节。这一节将介绍编写和测试加工程序、使用模拟功能进行验证以及程序优化和效率提升的方法。
### 3.3.1 编写和测试加工程序
编写加工程序时,需要考虑工具路径、切削参数、夹具设置以及工件固定方式等多个因素。测试加工程序通常在机床上分步执行,以确保每一步都是正确的。
**代码块示例:**
```gcode
O1000 ;程序开始
(加工程序内容)
M30 ;程序结束
```
在编写程序时,应该利用好注释(用圆括号()包围的文本),这将有助于理解和调试程序。
### 3.3.2 使用模拟功能进行验证
现代数控系统通常具备仿真功能,能够在实际加工前对程序进行模拟,检查路径错误和潜在的碰撞。使用模拟功能能够显著提高编程的效率,并降低因错误而导致的风险。
### 3.3.3 程序优化和效率提升
优化加工程序通常涉及对刀具路径的再分析、减少不必要的移动和提升切削参数。效率的提升不仅体现在加工时间的减少,还包括延长刀具寿命、降低能耗和提高加工质量。
**mermaid流程图展示程序优化过程:**
```mermaid
graph TD
A[开始优化] --> B[刀具路径分析]
B --> C[减少非切削移动]
C --> D[调整切削参数]
D --> E[模拟验证]
E --> F{是否满足要求}
F -- 是 --> G[程序优化成功]
F -- 否 --> B
```
该流程图展示了从刀具路径分析开始,通过减少非切削移动,调整切削参数,然后进行模拟验证,最后确定是否达到优化目标,从而构成了一个持续改进的循环。
在本章节中,我们探讨了数控编程语言的基础,包括G代码和M代码的使用,参数化编程和循环的实现方法。同时,我们也深入理解了工具和刀具管理的重要性,以及如何创建和调试加工程序,并利用程序优化提升加工效率。
# 4. 840DSL NC的高级功能应用
## 4.1 多轴控制与加工
### 4.1.1 五轴加工技术
五轴加工技术是当今高端数控机床中的关键技术之一,它允许刀具在三维空间内以五个独立轴进行复杂的运动。与传统的三轴加工相比,五轴加工能够加工出更加复杂和精确的零件形状,尤其适用于航空航天、汽车制造和模具加工等高精度要求的领域。
实现五轴加工的关键在于多轴机床和相应的数控系统。840DSL NC提供了一套高级的多轴控制功能,使得机床能够对复杂的几何形状和轮廓进行精确加工。通过高级的路径规划和运动学算法,五轴加工技术能够确保加工过程的平滑过渡和高精度定位,从而减少工具磨损、避免碰撞,并缩短加工周期。
在编程时,五轴加工需要使用专门的后处理器来生成适合多轴控制的NC代码。这些代码必须包含用于所有五个轴运动的指令,确保在加工过程中各个轴协调运动。例如,刀具的倾角和方位角需要与主轴的移动共同考虑,以避免干涉和提高切削效率。
### 4.1.2 高效路径优化
路径优化是指在保证加工质量的前提下,通过对刀具路径进行科学规划,以缩短总的加工时间,提高机床的使用效率。在多轴加工中,路径优化尤为重要,因为不合理的刀具路径不仅会降低加工效率,还可能造成机床过载和刀具损坏。
840DSL NC提供的高效路径优化功能可以通过软件算法来自动调整刀具的运动轨迹。这些算法考虑了切削参数、刀具类型、材料特性、机床动力学限制以及工件的几何形状等因素,能够生成平滑、连续且无冗余运动的加工路径。结果是,加工过程中的空程移动和切削时间被大幅减少,同时保持了加工精度。
路径优化的一个关键方面是避免快速移动(G0或G00)的频繁使用,因为这会导致加工速度的降低和机床动能的浪费。此外,优化还涉及刀具路径的平滑过渡,以减少机床的动态负载并延长刀具寿命。通过使用840DSL NC的高级路径优化功能,用户可以显著提高生产效率和产品质量。
## 4.2 自动化和定制化解决方案
### 4.2.1 自动换刀系统(ATS)
自动换刀系统(Automatic Tool Changer,ATS)是提高数控机床生产效率的重要组成部分。它能够自动更换加工过程中需要使用的不同刀具,从而避免了手动换刀时所花费的停机时间,使得加工过程更加连续和高效。
在840DSL NC数控系统中,ATS的实现依赖于专门的硬件和软件设计。硬件包括刀库、刀具交换装置和相应的驱动器与传感器。软件方面,840DSL NC提供了一整套刀具管理和刀具寿命跟踪功能,确保刀具在需要时能够被及时更换,并且在更换过程中遵循预定的流程,避免可能出现的错误。
840DSL NC提供的ATS解决方案不仅仅局限于刀具的自动更换,它还包括了刀具寿命管理、刀具磨损补偿以及刀具失效的即时反馈。这些功能允许系统在刀具磨损到一定程度时自动安排换刀,并根据刀具的实际状态自动调整切削参数,从而保证加工质量的一致性。
ATS的实现对加工过程的稳定性和可靠性有着直接的影响。通过减少人为干预和提高换刀效率,ATS为实现连续无人值守的生产提供了基础,这对于提高生产效率、降低生产成本和增强市场竞争力都具有重要意义。
### 4.2.2 用户界面定制和宏编程
用户界面定制和宏编程是840DSL NC数控系统中提高操作便捷性和灵活性的重要功能。通过定制用户界面,操作者可以根据自己的习惯和特定任务的需求来组织和显示界面元素。这使得操作者能够更快地访问常用的功能和指令,提高操作效率,并减少出错的可能性。
宏编程则允许用户创建能够执行一系列复杂操作的自定义宏程序。这些宏程序可以包括一系列的G代码和M代码,甚至可以嵌入条件判断和循环结构,以实现更加复杂的自动化任务。宏编程功能极大的扩展了数控系统的功能,使得用户可以根据特定的应用场景编写自己的加工程序,满足特殊加工需求。
例如,在生产批量较大的情况下,可以预先编写宏程序来自动完成一系列加工任务,减少操作者的重复劳动。在定制用户界面上,可以将经常使用的宏程序按钮放在显眼的位置,使得操作人员能够迅速启动宏程序,加快生产节拍。
用户界面定制和宏编程不仅能够提高操作的便捷性,还能够显著提高机床的生产效率。通过减少操作者的操作步骤,降低了人为失误的概率,进一步提升了加工的一致性和可靠性。对于生产管理者来说,这些高级功能的应用也使得生产过程更加可控,便于实现数据的收集和分析,为持续改进提供了依据。
## 4.3 高级诊断与维护技术
### 4.3.1 预防性维护策略
预防性维护是指在设备出现故障之前,通过定期检查和维护,以避免突发故障的发生。在数控机床领域,预防性维护策略对于保证机床的长期稳定运行至关重要。通过采取一系列预防性维护措施,机床可以减少意外停机时间,延长设备的使用寿命,并确保加工质量的一致性。
840DSL NC数控系统具备强大的预防性维护功能,提供了多种工具和监测点来帮助用户及时发现可能的设备问题。例如,系统可以监测到刀具的磨损程度、主轴的振动情况、以及各运动轴的定位精度等关键参数。通过这些监测数据,用户可以得到关于机床健康状态的早期预警。
预防性维护策略的关键在于制定合理的维护计划和周期。根据机床的使用频率和加工任务的复杂性,用户需要制定具体的检查和维护流程,并将其纳入日常的生产计划中。840DSL NC系统能够帮助用户建立维护日程,并通过系统日志来跟踪维护活动的执行情况,确保每一项维护任务都不会被遗忘。
另外,预防性维护还涉及定期更换易损件和润滑系统。通过使用840DSL NC系统的维护功能,用户可以设置定时提醒,确保在部件达到预期寿命前进行更换,从而避免潜在的机床故障。
### 4.3.2 实时监控和故障排除
实时监控系统是提高数控机床运行效率和故障处理能力的关键技术。在840DSL NC数控系统中,实时监控功能允许操作者和维护人员持续监测机床的运行状态,及时发现并处理异常情况。
系统会实时收集机床的各种运行参数,如主轴转速、刀具负载、冷却系统状态以及各运动轴的位置和速度等。这些数据会以图形化的方式展示在用户界面上,使得操作者能够直观地了解机床的当前状态。一旦发现有参数超出正常范围,系统会立即发出警报,并提供可能的原因和解决方案,帮助操作者迅速定位问题并采取措施。
840DSL NC数控系统还提供了故障排除工具,能够根据已知的机床历史数据和现有的故障代码库进行自动诊断。通过这种方式,操作者可以快速识别故障发生的原因,并根据系统提供的步骤指导进行故障排除。这不仅降低了机床的停机时间,也减少了对高技能维修人员的依赖。
实时监控和故障排除功能是840DSL NC数控系统高级维护技术的重要组成部分。它极大地提高了机床的可靠性,降低了故障维修的成本,并提升了整体的生产效率。通过实时监控和故障排除,数控机床能够保持最佳的运行状态,实现长期的高效生产。
在实际应用中,实时监控和故障排除功能可以与预防性维护策略相结合。通过定期的系统检查和维护,以及实时的数据监控,可以有效减少机床的故障发生概率,同时确保生产过程的连续性和高效率。随着技术的不断发展,实时监控和故障排除技术也在不断进步,为数控机床的高效稳定运行提供了更加强有力的保障。
# 5. 优化数控机床性能
## 现场案例分析
### 问题诊断与性能瓶颈
在工业生产中,数控机床的性能至关重要。性能瓶颈会直接影响生产效率和加工质量。案例中,某机床在执行复杂工件加工时表现出的振动、精度下降和加工周期延长的问题,引起工厂管理层的重视。进行初步检查后,发现机床的刀具磨损严重,切削参数设置不合理,以及机床本身的维护周期未得到遵守。为了更深入地诊断问题,我们对机床进行了全面的性能评估。
为确定问题的根源,通过监控系统收集了机床运行数据,包括切削力、切削温度、振动频率和功率消耗。数据显示,在特定加工阶段,切削力和振动频率明显升高,这通常指示刀具磨损或切削参数不当。接着,工程师对刀具管理系统进行检查,确认存在刀具寿命计算错误,并发现部分刀具确实已经达到或超过了其推荐使用次数。
### 解决方案的实施
为了优化性能,我们实施了以下步骤的解决方案:
1. **刀具更换和优化**:立即更换磨损的刀具,并对刀具管理系统进行了优化,确保刀具寿命计算的准确性。
2. **切削参数调整**:根据机床和材料的特性,重新设定切削速度、进给率和切深等参数,以减少不必要的振动和延长刀具寿命。
3. **维护计划更新**:更新了机床的维护计划,包括定期检查和更换刀具、导轨润滑以及检查主轴状态,以保持机床最佳性能。
4. **操作员培训**:对操作员进行重新培训,确保他们能够正确地使用机床,并理解维护计划的重要性。
通过这些措施,我们期望提高机床的运行效率,并达到提升加工质量和产量的目的。
## 性能优化案例
### 提升加工精度
加工精度直接影响产品的质量和生产成本。在案例中,我们通过精确校准数控系统和改善工艺流程来提升加工精度。首先,重新校准了机床的测量系统,包括导轨、丝杆和传感器,确保测量数据的准确性。其次,优化了刀具路径,减少刀具的径向和轴向跳动,并应用了补偿技术来最小化加工误差。
### 增强加工速度和效率
提高加工速度是另一个关键目标。我们对加工程序进行了优化,减少空行程时间,并采用了更高效的刀具和切削策略。同时,通过使用高速切削技术和智能控制,有效地缩短了加工周期。此外,升级了机床的控制系统软件,提高了数据处理能力和响应速度,进一步提高了生产效率。
## 持续改进与最佳实践
### 持续改进的策略
性能优化是一个持续的过程。在这个案例中,我们建立了一个持续改进的框架,这包括定期的技术审查会议、性能监控和反馈机制。技术审查会议为团队成员提供了一个交流想法和最佳实践的平台。通过性能监控,可以及时发现问题并迅速响应。而反馈机制确保操作员能够对机床的运行状况提出意见,为持续改进提供第一手资料。
### 行业最佳实践分享
最后,我们鼓励分享行业内的最佳实践,以促进整个行业的进步。与同行交流是获取新思路和方法的有效方式。在案例中,我们与业界专家合作,通过参加行业会议和研讨会,学习了最新的数控技术和管理方法。例如,通过采用新的刀具材料和涂层技术,可以显著提高刀具的耐用性和加工效率。此外,使用先进的预测性维护技术,如基于AI的机床状态监测,可以进一步减少意外停机时间并提高生产安全。
通过这些策略的实施,我们不仅优化了单个机床的性能,也为整个工厂的长期发展奠定了坚实的基础。
# 6. 未来趋势与挑战
随着科技的迅速发展,数控技术也在不断地进步与革新,作为数控领域的专家,我们需要预见到未来的趋势,并准备好迎接挑战。
## 6.1 数控技术的发展前景
数控技术的未来发展与数字化转型和智能制造息息相关。了解这些趋势对于数控工程师来说至关重要,以便更好地适应未来的变革。
### 6.1.1 数字化转型的影响
随着工业4.0的推广,数字化转型已成为众多制造企业必须面对的课题。数字化不仅改变了产品设计、生产、管理和服务的流程,也为数控机床的操作和维护带来了新的机遇。
* 通过数字化技术,企业可以更有效地进行生产计划和资源分配,提高生产的灵活性和效率。
* 数字化工具如3D打印技术、模拟软件和实时数据分析等,正在成为数控机床领域创新的重要推动力。
* 在数控机床的操作上,采用数字化操作界面和控制软件,可以提高操作便利性和精度。
### 6.1.2 智能制造与工业4.0
智能制造依托于工业物联网(IIoT)、大数据分析和人工智能等技术,推动了数控机床向更高级别的自动化和智能化方向发展。
* 工业4.0强调的是制造过程的智能化,它包括了通过互联网实现设备的互连互通,以及生产过程中的自我优化和自我决策。
* 在数控机床领域,智能制造能够实现生产过程中从原材料到成品的全程质量追踪,降低废品率。
* 智能制造还包括对生产过程中的故障预测和维护,利用大数据分析和机器学习算法,提前发现问题并采取措施。
## 6.2 面临的挑战与应对策略
尽管数控技术的发展前景广阔,但同时也会面临许多挑战,这需要我们从现在开始做好准备。
### 6.2.1 技术更新换代的挑战
随着技术的快速迭代,数控技术也在不断更新换代。这意味着我们需要不断学习新的技能和知识,才能保持竞争力。
* 工程师需要时刻关注技术的最新发展动态,比如新型数控系统、软件和工具。
* 除了学习,还需要定期进行技能的升级和认证,以满足行业和客户的高标准要求。
* 实践是掌握新技术的最佳途径,要通过参与实际项目来检验和深化所学的理论知识。
### 6.2.2 技能提升与人才培养
数控技术领域的专家必须具备多元化的技能,包括编程、机械设计、电子技术和计算机应用等。
* 技能提升的关键在于跨学科学习,尤其是软技能,如问题解决、团队协作和领导力。
* 企业应该为员工提供培训和继续教育的机会,以促进个人和组织的成长。
* 吸引和保留人才也需要为专业技术人员提供有竞争力的薪酬福利和职业发展路径。
## 6.3 结语:成为数控领域的专家
要想在数控技术领域中脱颖而出,成为真正的专家,需要长期的投入和学习。
### 6.3.1 综合技能的重要性
专家不仅仅是在某一领域有深入的了解,还需要有综合应用各方面技能的能力。
* 持续学习新的技术和方法,以保持与时俱进。
* 学会整合多学科知识,解决复杂的工程问题。
* 培养良好的沟通能力和团队合作精神,这对于领导项目和管理团队至关重要。
### 6.3.2 不断学习与适应未来
适应未来不断变化的环境和市场需求,是每一位数控领域专家的必备素质。
* 预测未来的变化趋势,并制定相应的学习计划和职业发展策略。
* 通过不断的学习和实践,积累经验,提高判断力和决策能力。
* 建立一个专业网络,与同行交流,吸收最新的行业信息和知识。
随着技术的快速发展,数控领域的专家面临着前所未有的机遇与挑战。为了在未来的竞争中站稳脚跟,我们需要不断学习和适应。只有这样,才能确保我们的技能与时俱进,为制造行业的发展做出更大的贡献。
0
0
相关推荐
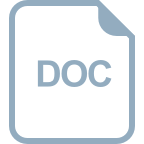
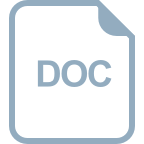
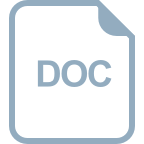
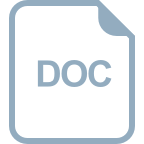
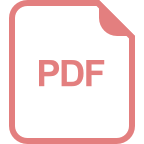
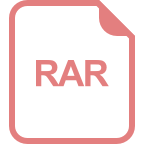
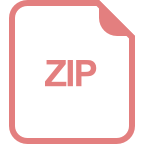
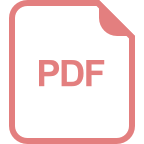
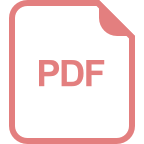