KND数控系统的多轴控制技术:实现复杂形状加工的高级技巧
发布时间: 2025-01-04 18:57:33 阅读量: 17 订阅数: 34 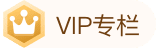
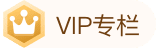
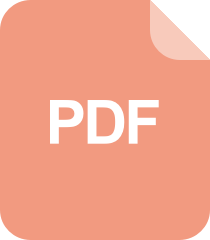
基于KND系统的四轴数控系统的开发

# 摘要
KND数控系统作为先进制造技术的关键支撑,其多轴控制技术在提高加工精度、优化加工路径及提升生产效率方面发挥着核心作用。本文首先概述了KND数控系统的架构及多轴数控的基本原理,接着详细探讨了多轴加工路径的规划方法与控制技术。在实践中,通过编程技巧的介绍与仿真验证,阐述了如何有效进行多轴编程及加工过程的质量控制。最后,本文分析了KND数控系统多轴控制技术的发展趋势,包括智能化数控系统的特征及技术创新方向,展望了KND系统在集成解决方案与行业应用中的前景。
# 关键字
KND数控系统;多轴控制;路径规划;编程实践;加工质量;技术创新
参考资源链接:[KND数控系统KAPILib开发文档:网络交互与API接口](https://wenku.csdn.net/doc/o155sdrgp7?spm=1055.2635.3001.10343)
# 1. KND数控系统概述
## 1.1 数控系统的定义与发展
数控系统(Numerical Control System),简称NC系统,是现代制造业中不可或缺的技术之一。它通过预编程,自动控制机械加工设备的运动和操作。随着工业自动化的推进,数控技术已经从早期的单轴控制发展到今天的多轴联动系统,极大提高了加工的精度和效率。
## 1.2 KND数控系统的市场地位
KND数控系统作为我国自主研发的数控系统,在市场上占有重要地位。它集成了先进的控制技术,满足从简单到复杂的各种加工需求。KND系统不仅适用于传统的金属加工,也被广泛应用于汽车、航空航天、模具制造等多个领域,有效提升了这些行业的生产力。
## 1.3 KND数控系统的技术特点
KND数控系统以其强大的多轴控制能力、良好的用户界面和稳定的系统性能著称。它支持多种编程语言,易于操作,具有良好的兼容性和扩展性。同时,KND系统在加工过程中的精度控制、误差补偿以及实时监控等方面具有显著优势,这也是其赢得市场认可的关键因素之一。
# 2. 多轴控制技术理论基础
在现代制造业中,多轴控制技术为复杂形状零件的加工提供了可能。多轴数控机床通过多个旋转轴的协调运动,可以实现对工件进行多面或复杂路径的加工。本章将深入探讨多轴控制技术的理论基础,包括多轴数控系统的原理、多轴加工路径规划,以及多轴控制的关键技术。
## 2.1 多轴数控系统的原理
### 2.1.1 多轴控制的基本概念
多轴控制技术通常指的是在数控机床上,通过至少三个独立的旋转轴进行协同控制的加工技术。这允许刀具沿着多个轴线进行运动,可以同时对工件的多个面进行加工,大幅提高了加工复杂零件的精度与效率。与传统的三轴机床相比,多轴控制可以进行五轴甚至更多轴的联动,从而实现更复杂的加工路径,缩短生产周期,提高材料利用率。
### 2.1.2 多轴联动与插补技术
联动技术是多轴控制的核心之一。多轴联动意味着所有轴线的运动相互关联,实时响应,能够使刀具沿着预定的路径移动。插补技术则负责计算刀具路径中的无数点,确保路径的平滑性以及加工的精度。数控系统使用插补算法,如线性插补或圆弧插补,通过计算产生步进信号来驱动各轴电机,进而控制刀具按预定轨迹移动。
## 2.2 多轴加工路径规划
### 2.2.1 路径规划的基本方法
在多轴加工中,路径规划的目的是确定刀具移动的最优路线,以提高加工效率、减少加工时间和降低工具磨损。路径规划的基本方法包括轮廓加工、螺旋进刀、等高线加工等。轮廓加工适合加工平面或曲面边界;螺旋进刀则能有效避免刀具切入点的冲击;等高线加工通过跟随等高线路径,实现对复杂曲面的均匀加工。
```mermaid
graph TD
A[开始] --> B[确定工件模型]
B --> C[选择加工策略]
C --> D[轮廓加工]
C --> E[螺旋进刀]
C --> F[等高线加工]
D --> G[优化刀具路径]
E --> G
F --> G
G --> H[模拟加工]
H --> I[输出刀具路径数据]
I --> J[结束]
```
### 2.2.2 轨迹优化的策略
轨迹优化对于提高加工质量和生产效率至关重要。优化策略包括刀具路径的平滑化处理、避免不必要的抬起和下刀动作,以及减少空程移动。通过优化,可以减少机床运动的时间,避免刀具撞击工件或夹具,从而延长刀具寿命并提升加工品质。
## 2.3 多轴控制的关键技术
### 2.3.1 同步控制技术
在多轴数控机床上,各轴之间的同步控制至关重要。同步控制技术确保所有运动轴协调动作,任何时刻各轴的位置和速度都满足预定的路径要求。高精度的同步控制技术可以减少机械误差,提高零件加工的精度和表面质量。
### 2.3.2 加工误差补偿技术
由于机床自身的机械误差、热变形、刀具磨损等因素,加工过程中会产生误差。误差补偿技术通过提前计算并补偿这些误差,可以提高最终加工的精度。常见的补偿方法包括数控系统内部的软件补偿、实时误差补偿和基于模型的补偿策略。
```mermaid
graph LR
A[误差分析] --> B[误差类型判断]
B --> C[软件补偿]
B --> D[实时补偿]
B --> E[模型补偿]
C --> F[设定补偿值]
D --> G[动态调整指令]
E --> H[建立误差模型]
F --> I[加工执行]
G --> I
H --> I[最终产品]
I --> J[精度检查]
```
在本章中,我们详细探讨了多轴控制技术的理论基础,包括多轴联动的原理、路径规划的基本方法和优化策略,以及同步控制技术和加工误差补偿技术。通过这些技术的深入理
0
0
相关推荐







