FANUC控制系统升级:提升兼容性与性能的终极指南
发布时间: 2024-12-15 01:39:43 阅读量: 13 订阅数: 17 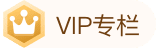
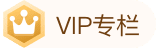
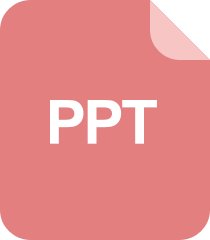
FANUC系统数控车床的编程与操作实例.ppt
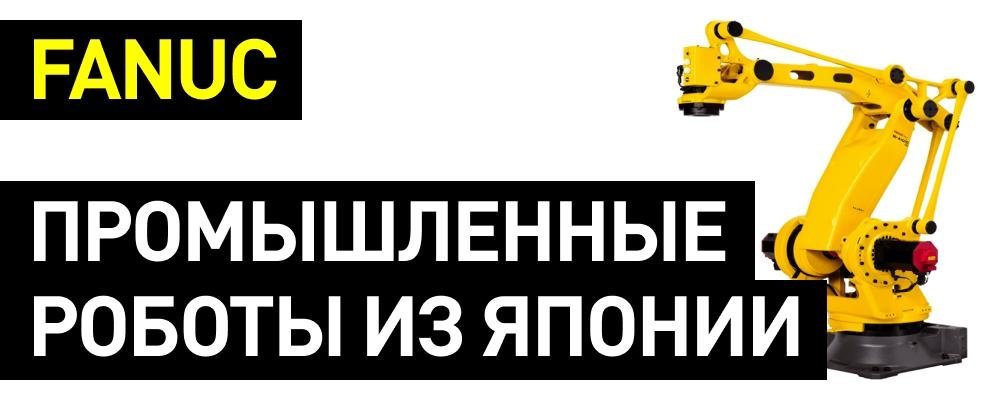
参考资源链接:[FANUC机器人点焊手册:全面指南与操作详解](https://wenku.csdn.net/doc/6412b763be7fbd1778d4a1f2?spm=1055.2635.3001.10343)
# 1. FANUC控制系统基础概述
FANUC控制系统是全球领先的工业自动化解决方案提供商,其产品广泛应用于机器人、CNC机床及自动化生产线等领域。FANUC系统以其高可靠性和用户友好的特点,在制造业内享有盛誉。本章节将简要介绍FANUC控制系统的基本架构,以及其在现代制造业中的应用价值。
## 1.1 FANUC系统概述
FANUC控制系统的本质在于其高度模块化和标准化的设计,这使得系统能够灵活地适应不同的应用场景。系统包括硬件部分和软件部分,其中硬件部分通常包括主控制单元、输入输出模块和伺服驱动器等,而软件部分则涉及到操作系统、用户界面和应用程序等。
## 1.2 系统架构
FANUC系统架构的核心是实时操作系统和多任务处理能力,它使得控制程序可以在严格的实时条件下运行。在硬件层面,FANUC系统通常采用双总线架构,即主总线用于核心控制单元与外围设备的数据交换,而从总线则用于与伺服电机和其他执行机构的通信。
## 1.3 应用价值
对于企业而言,FANUC控制系统提供了一种高效、精确和可靠的生产方式。它不仅提高了生产效率,减少了人为操作的错误,还能够通过自动化减少生产成本。随着智能制造的不断推进,FANUC控制系统已经成为实现工业4.0和自动化改造不可或缺的工具。
本章主要为读者提供FANUC控制系统的基础知识,为后续章节中兼容性升级、性能优化和安全性强化等内容打下理论基础。接下来的章节将逐步深入讨论FANUC控制系统的技术细节和实际应用案例。
# 2. FANUC控制系统的兼容性升级策略
FANUC控制系统作为自动化领域中的领先者,其在工业制造过程中的应用极为广泛。然而随着技术的快速发展与企业需求的升级,系统兼容性升级成为了保障生产效率和企业竞争力的必要步骤。在这一章节中,我们将探究FANUC控制系统的兼容性升级策略,从理论基础到实践方法,再到故障诊断与处理,深入分析如何在保障生产连续性的基础上,实现系统的平滑过渡。
## 2.1 兼容性升级的理论基础
### 2.1.1 FANUC系统架构解析
FANUC控制系统的核心架构可从物理层、控制层到信息层三个维度进行解析。物理层涉及机器硬件的接口与模块;控制层包括了CNC单元、PLC逻辑控制器等核心组件;信息层则是数据通信和人机界面所在。为实现兼容性升级,需要对各个层面上的组件与接口充分理解,确保新的系统能够与旧有硬件和软件保持无缝衔接。
### 2.1.2 兼容性问题的识别与分类
兼容性升级面临的问题可分为软件和硬件两大类。软件层面,需要考虑新旧系统间的数据格式、协议以及API的兼容性;硬件层面,则需注意电源接口、信号传输、物理尺寸等参数是否匹配。通过识别并分类这些兼容性问题,能够更加有针对性地设计升级方案。
## 2.2 兼容性升级的实践方法
### 2.2.1 升级前的准备工作
升级前,进行充分的准备至关重要。这包括但不限于:
- 制定详细的升级计划,明确升级的时间窗口、任务分工以及预期目标。
- 收集和备份现有系统的全部相关数据,包括生产数据和用户参数。
- 进行风险评估,识别可能对生产造成影响的关键点,并制定应对措施。
### 2.2.2 具体升级步骤与案例分析
FANUC兼容性升级的具体步骤可概括为以下几个关键环节:
1. **评估与规划**:对现有系统进行全面评估,确定升级范围与需求。
2. **组件替换或更新**:根据规划更换或升级硬件、软件组件。
3. **系统集成**:将新旧系统进行集成,保证软硬件间的兼容性。
4. **功能测试**:进行全面的功能测试,确保升级后的系统满足生产需求。
5. **生产迁移**:将生产过程迁移到新系统,实施监控与调整。
案例分析:
在某工厂的FANUC控制系统升级案例中,通过对现有系统进行详细评估后,工程师们发现CNC机器的老旧驱动器需要替换,同时也需要更新到最新的PLC软件。在实施过程中,工程师首先更新了控制程序,并对驱动器进行了替换。然后,通过逐步测试确保了新旧系统的平滑过渡,最终成功实现了升级。
### 2.2.3 升级后的测试与验证
升级后,测试验证是保证系统稳定运行的关键步骤。测试内容包括但不限于:
- 功能测试:对每一个功能模块进行验证,确保其按预期工作。
- 性能测试:进行系统性能基准测试,比较升级前后的性能差异。
- 压力测试:对系统施加高负载,评估其稳定性和极限性能。
## 2.3 兼容性升级中的故障诊断与处理
### 2.3.1 常见故障类型及排查方法
兼容性升级中常见的故障类型包括接口不匹配、硬件冲突、软件兼容问题等。故障排查方法应该系统化,例如使用诊断工具对系统进行全面扫描,利用日志文件定位问题发生的模块等。在故障发生时,应遵循从简至繁、从外围至核心的排查策略。
### 2.3.2 故障处理的实际操作流程
故障处理流程可以分为以下几个步骤:
1. **问题记录**:详细记录故障发生的时间、症状和操作历史。
2. **初步判断**:依据记录,进行初步的故障分析与判断。
3. **深入分析**:运用专业工具进行深入分析,比如硬件诊断工具。
4. **故障定位**:根据分析结果进行故障定位,确认问题所在。
5. **解决方案实施**:根据故障类型实施相应的解决措施。
6. **效果验证**:故障修复后进行验证,确保问题不再复现。
以具体案例说明,某企业在进行FANUC兼容性升级后,发现数控机床在某些操作下出现了异常停机。通过查看日志文件,工程师们发现异常是在某个特定的CNC指令序列执行时发生的,初步判定是软件兼容性问题。进一步分析后发现是升级后的新驱动程序与旧的I/O模块存在兼容问题。最终通过安装官方提供的更新包解决了该问题。
升级兼容性是确保FANUC控制系统长期稳定运行的关键,本章节从理论到实践,再到故障处理,提供了一套全面的升级策略和方法,旨在帮助企业在面对控制系统升级时能够做到有备无患,顺利完成从旧到新的过渡。
# 3. FANUC控制系统的性能优化
性能优化是任何工业控制系统持续改进的重要环节。对于FANUC控制系统来说,通过精确的调优和硬件升级可以显著提升整个系统的运行效率和可靠性。在这一章节中,我们将深入探讨性能优化的理论基础,随后重点分析如何在实际操作中应用这些理论进行系统升级和性能监控,最终通过案例研究来具体说明优化的效果。
## 3.1 性能优化的理论基础
性能优化不仅仅是提高设备运行速度,它包括了系统响应时间、可靠性、稳定性和可维护性等多个维度的评估与改进。有效的性能优化需要建立在对系统评估指标体系和关键影响因素有深刻理解的基础之上。
### 3.1.1 性能评估指标体系
在对FANUC系统进行性能评估时,有多种指标是需要关注的。其中包
0
0
相关推荐






