FANUC-0i-MC参数定制化秘籍:打造你的机床性能优化策略
发布时间: 2024-12-23 23:39:14 阅读量: 23 订阅数: 18 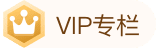
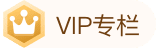
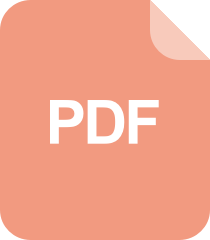
基于FANUC-0i-MC系统槽轮的数控加工
# 摘要
本文对FANUC-0i-MC机床控制器的参数定制化进行了全面探讨,涵盖了参数理论基础、实践操作、案例分析以及问题解决等方面。文章首先概述了FANUC-0i-MC控制器及其参数定制化的基础理论,然后详细介绍了参数定制化的原则、方法以及对机床性能的影响。接下来,本文通过具体的实践操作,阐述了如何在常规和高级应用中调整参数,并讨论了自动化和智能化背景下的参数定制化。案例分析部分则提供了实际操作中遇到问题的诊断与解决策略。最后,文章探讨了参数定制化的未来趋势,强调了安全考虑和个性化参数优化的重要性。通过对机床参数定制化的深入分析,本文旨在为机床操作者和维护人员提供指导和参考,以提升机床性能和生产效率。
# 关键字
FANUC-0i-MC;参数定制化;机床性能;自动化;智能化;安全风险
参考资源链接:[FANUC-0i-MC系统参数详解与操作指南](https://wenku.csdn.net/doc/647ad958d12cbe7ec3338b91?spm=1055.2635.3001.10343)
# 1. FANUC-0i-MC机床控制器概述
## 1.1 FANUC-0i-MC介绍
FANUC-0i-MC是FANUC公司生产的中高端数控系统,广泛应用于各种机床设备中。该系统以其高精度、高稳定性和强大的功能而受到业界的广泛赞誉。了解其基本工作原理和构成,对于进行参数定制化以及维护工作具有重要的指导意义。
## 1.2 FANUC-0i-MC的组成与功能
FANUC-0i-MC机床控制器主要包括控制单元、输入/输出单元、存储单元和伺服单元等几大部分。控制单元负责执行机床的数控程序,对输入信号进行处理;输入/输出单元负责接收操作者的指令,反馈机床的运行状态;存储单元用来存储数控程序和参数;伺服单元则根据控制单元的指令,驱动电机进行运动。
## 1.3 FANUC-0i-MC在工业中的应用
FANUC-0i-MC机床控制器在汽车、航空航天、精密制造等诸多行业中都有广泛的应用。凭借其高精度、高稳定性和强大的功能,该系列机床控制器帮助许多制造企业提升了生产效率,降低了生产成本,并且具有良好的系统扩展性和兼容性,可以满足不同规模生产需求。
以上内容为第一章的核心部分,后续章节将进一步深入探讨FANUC-0i-MC的参数定制化,并结合实际操作案例进行详细分析。
# 2. 参数定制化的理论基础
## 2.1 FANUC-0i-MC参数解析
### 2.1.1 参数的基本概念与分类
FANUC-0i-MC机床控制器拥有成百上千个可调参数,每个参数都对应着机床控制器或机床本身的特定功能。参数的分类多种多样,通常可分为以下几类:
1. 系统参数:控制机床操作系统的整体设置。
2. 位置参数:调整机床各轴的位置控制特性。
3. 进给速度参数:用于控制各轴的移动速度。
4. 主轴参数:与主轴转速和旋转方向等设置相关。
5. 刀具补偿参数:用于刀具长度和半径的补偿设置。
6. 加工参数:与材料切削相关的参数,如切削速度和进给率。
参数的设定依据机床的实际情况和加工需求来进行微调,以确保机床能够按照预期的性能稳定运行。通过调整参数,可以优化机床的精度、效率和稳定性。
### 2.1.2 参数与机床性能的关系
每个参数对机床性能的影响是多方面的。例如,进给速度参数调整得当,可以提高加工速度而不牺牲加工精度;而刀具补偿参数的精确设置能够确保加工尺寸的准确性。参数之间的相互作用和依赖性意味着,调整一个参数时,需要考虑到其他参数的相应变化。因此,参数定制化是一个需要精确计算和周全考虑的过程。
## 2.2 参数定制化的原则与方法
### 2.2.1 定制化前的准备工作
在开始进行参数定制化之前,需要进行一系列的准备工作,确保过程的顺利进行和最终效果。准备工作包括:
- 对机床的完整了解:包括机床的功能、限制以及已知的性能瓶颈。
- 数据收集:收集相关的机床操作数据和性能指标,如加工时间、废品率等。
- 定义目标:明确参数定制化的具体目标,比如提高精度、减少故障率或提升效率。
- 风险评估:评估参数调整可能带来的风险和影响,为后续的参数测试和验证做准备。
### 2.2.2 参数调整的基本原则
参数调整时需要遵循以下基本原则:
- 循序渐进:避免一次性进行大幅度的调整,而应该逐个参数、逐个功能地进行微调。
- 记录与备份:每一步的调整都应详细记录,并在调整前备份原参数,以便必要时恢复。
- 实际测试:调整后的参数应通过实际加工或模拟测试来验证其效果。
- 安全为先:任何调整都不能危害机床的安全操作和操作人员的安全。
### 2.2.3 参数调整的步骤与技巧
进行参数调整时,可以按照以下步骤进行:
1. **识别需要调整的参数:** 依据前述的准备工作,确定需要调整的参数范围。
2. **小范围调整:** 对选定参数进行小范围的递增或递减调整。
3. **观察结果:** 每次调整后观察并记录机床性能的变化。
4. **调整与优化:** 根据观察结果对参数进行微调,直至达到预定目标。
此外,一些高级的参数调整技巧包括:
- 使用统计分析方法来辅助参数优化。
- 利用机床控制器提供的高级功能进行更精细的调整。
- 借助专家系统或经验丰富的操作人员来指导参数定制化。
## 2.3 定制化对机床性能的影响
### 2.3.1 提高加工精度的参数调整
在生产过程中,提高加工精度是保证产品质量的关键。通过调整FANUC-0i-MC的刀具补偿参数、位置参数等,可以有效提高加工精度。例如,刀具半径补偿参数的精细调整可以减少加工误差,提高尺寸精度。位置参数则可以调整机床各轴的同步运动,使得加工过程中的位移更加精准。
### 2.3.2 提升加工效率的参数调整
加工效率直接关联到生产周期和成本。提升加工效率的参数调整通常包括:
- 进给速度参数的优化,以找到最佳的切削速度和进给率。
- 加工参数的调整,比如提高主轴转速来缩短切削时间。
- 在保证加工质量的前提下,对各轴加速度和减速度参数进行微调,以减少非加工时间。
### 2.3.3 增强机床稳定性的参数调整
机床长时间运行的稳定性是提高生产效率和降低成本的重要保证。通过调整系统参数、位置参数和进给速度参数,可以增强机床运行的稳定性。如设置合适的伺服参数,可以减少因热变形或负载变化导致的位移误差。
调整这些参数时,需要综合考量机床的实际情况,以及实际加工任务的需求。通过不断的测试和调整,可以确保机床在长时间运行中保持高效和稳定的性能。
# 3. FANUC-0i-MC参数定制化的实践操作
## 3.1 常规参数调整实践
### 3.1.1 常见功能代码与参数对照
在FANUC-0i-MC控制系统中,了解常见功能代码与对应参数是进行常规参数调整的前提。功能代码通常由数字和字母组合而成,而参数则是一系列预设的配置值,用以控制机床的行为。表3.1展示了几个常见的功能代码及其对应的参数及其功能描述:
表 3.1 常见功能代码与参数对照表
| 功能代码 | 对应参数 | 功能描述 |
|-----------|-----------|-----------|
| G02 | 1101 | 顺时针圆弧插补 |
| G03 | 1102 | 逆时针圆弧插补 |
| G04 | 1103 | 暂停插补 |
| G20 | 1201 | 英制单位设置 |
| G21 | 1202 | 公制单位设置 |
| M03 | 1001 | 主轴正转控制 |
| M04 | 1002 | 主轴反转控制 |
| T01 | 1301 | 刀具选择1 |
| T02 | 1302 | 刀具选择2 |
例如,如果需要调整主轴的转速,我们可以修改参数`1001`来控制M03指令下的主轴转速。每一个参数都有其详细的设定范围和使用说明,这些信息通常可以在机床的操作手册或FANUC的技术文档中找到。
### 3.1.2 实际加工案例中的参数调整
实际加工中,参数调整是确保加工质量与效率的关键步骤。例如,假设在加工一个铝合金零件时,发现工件表面出现了不规则的划痕,初步判断是由于刀具磨损导致。根据表3.1中功能代码与参数对照,首先确认使用的是T01刀具。然后,我们可以调整刀具寿命相关的参数,如参数`1301`,它控制了刀具寿命计数的阈值。通过增加该参数值,可以暂时推迟刀具更换的频率,但这可能会牺牲一些工件的表面质量。
在实际操作中,以下是调整参数的一般步骤:
1. 进入系统参数设置界面。
2. 根据需要修改的参数代码,找到对应的参数。
3. 输入新的参数值,并保存设置。
4. 进行试切或试运行,检查参数调整的效果。
5. 如果效果不理想,根据反馈再次调整参数值。
注意,在参数调整过程中,任何改动都应记录下来,以便出现问题时能够快速恢复到原始状态。
## 3.2 高级参数调整技巧
### 3.2.1 加工过程优化参数设置
在进行高级参数调整时,目的是为了优化加工过程,提高加工精度,增加加工效率,减少能耗等。例如,针对提高加工精度的参数调整,参数`121`(速度控制环比例增益)就是一个重要的参数。通过调整这个参数,可以改变伺服电机对指令速度的响应速度和稳定性。增加这个增益可以使加工路径更加精确,但过高的比例增益可能会引起振动,因此需要根据实际加工情况逐步调整以达到最优效果。
在实际应用中,高级参数调整通常需要结合机床的实时监控和动态调整,使用如下伪代码进行示例:
```python
# 伪代码,用于示例参数调整的逻辑
def adjust_processing_parameters():
# 读取当前的参数设置
current_gain = read_parameter(121)
# 增加一个增量以提升速度控制环的响应速度
adjusted_gain = current_gain + 10
# 检查是否超出设定的最大值
if adjusted_gain > MAX_GAIN:
print("已达到最大增益限制。")
return
# 应用调整后的参数
write_parameter(121, adjusted_gain)
print("速度控制环比例增益已调整至:" + str(adjusted_gain))
# 开始加工测试
test_processing()
# 根据加工结果进一步优化参数
# ...
# 调用函数
adjust_processing_parameters()
```
### 3.2.2 故障诊断与预防的参数应用
在高级参数调整中,参数同样可以用于故障诊断和预防。例如,参数`180`(主轴过载保护)可以帮助我们预防主轴因超负荷工作而导致的损坏。在设置该参数时,我们需要考虑主轴的最大功率,然后设置一个合理的阈值,当主轴负载超过该阈值时,系统会自动执行停止主轴运转的指令。通过这种方式,可以有效地防止主轴的过载损害,延长机床的使用寿命。
```python
# 伪代码,用于示例故障预防参数设置
def setup_overload_protection():
# 设定主轴最大功率
MAX_MOTOR_POWER = 10000
# 设定过载保护的阈值,例如为最大功率的80%
OVERLOAD_THRESHOLD = 0.8 * MAX_MOTOR_POWER
# 写入过载保护参数
write_parameter(180, OVERLOAD_THRESHOLD)
print("主轴过载保护已设置,阈值为:" + str(OVERLOAD_THRESHOLD))
# 运行监控程序,实时检测主轴状态
# ...
# 调用函数
setup_overload_protection()
```
## 3.3 自动化与智能化参数定制化
### 3.3.1 适应自动化生产线的参数调整
在自动化生产线中,机床的参数调整需与整个生产线的其他设备同步,以保证流程的顺畅和效率的最大化。例如,在一个自动化生产线上,多台机床协同工作时,可以通过参数调整确保每台机床的加工速度与生产节拍保持一致。参数`100`(进给速度倍率)是一个可以实时调整的参数,以匹配生产线的需求。通过修改这个参数,可以快速改变整个生产线的加工速度。
```python
# 伪代码,用于示例生产线参数同步调整
def sync_line_adjustment():
# 假定生产线基准速度为100%
BASELINE_SPEED = 1.0
# 计算需要设定的速度倍率
speed_rate = BASELINE_SPEED + 0.1 # 假设需要提高10%
# 应用新的进给速度倍率到所有相关机床
for machine in line_machines:
write_parameter(100, speed_rate * machine.current_speed_rate)
# 更新当前速度比率
for machine in line_machines:
machine.current_speed_rate = speed_rate
print("生产线上所有机床的进给速度倍率已调整至:" + str(speed_rate))
# 调用函数
sync_line_adjustment()
```
### 3.3.2 面向智能化升级的参数策略
随着工业4.0和智能制造的发展,参数定制化也需要面向智能化进行升级。智能机床应能根据实时的工作环境、加工材料、加工质量要求等因素自动调整参数。例如,使用机器学习算法优化刀具寿命参数(如`1301`)。智能化升级可能需要引入传感器数据,进行实时数据采集和分析,从而自动调整参数,减少人为干预,提高生产效率和产品质量。
```mermaid
graph TD
A[开始] --> B[读取实时加工数据]
B --> C[通过机器学习算法分析]
C --> D[预测刀具磨损程度]
D --> E[自动调整刀具寿命参数]
E --> F[继续加工]
F --> A
```
```python
# 伪代码,用于示例智能化参数调整流程
def intelligent_parameter_adjustment():
# 读取实时加工数据
real_time_data = read_real_time_data()
# 使用机器学习模型分析数据
tool_wear_prediction = machine_learning_model.predict(real_time_data)
# 根据模型预测结果调整刀具寿命参数
tool_life_parameter = calculate_new_tool_life_parameter(tool_wear_prediction)
write_parameter(1301, tool_life_parameter)
print("刀具寿命参数已根据智能化分析调整至:" + str(tool_life_parameter))
# 调用函数
intelligent_parameter_adjustment()
```
通过上述的示例,我们可以看到参数定制化正逐步从传统的人工设置和调整,向自动化和智能化的高级定制化发展。这样的智能化升级不仅提高了机床的加工性能,也进一步推动了制造业的效率和竞争力。
# 4. FANUC-0i-MC参数定制化案例分析
## 4.1 提升加工精度的案例分析
### 4.1.1 精密零件加工参数调优案例
在精密零件加工过程中,加工精度是至关重要的。本案例聚焦于如何通过参数调优来提升加工精度。案例背景为一家专门从事高精度零件生产的机床制造商,其加工的零件对表面粗糙度和尺寸精度的要求极高。
初始阶段,零件的表面质量不尽如人意,存在一些细微的划痕和不均匀的纹理。在进行系统性的参数分析之后,技术人员发现参数设置不当是造成该问题的主要原因。通过调整如下参数,获得了显著的改善:
- **进给速度(参数 No.1420)**:适当降低进给速度,减少了切削过程中的振动,改善了表面质量。
- **切削液流量(参数 No.1040)**:增加切削液流量,提高了冷却效果和润滑效果,避免了刀具与工件的热损伤。
- **刀具补偿(参数 No.5121)**:精确设置刀具补偿,以确保加工过程中刀具路径的准确性。
调优之后,再次加工的零件表面呈现出显著提高的精度和光洁度,满足了客户的高标准要求。
### 4.1.2 案例中的问题诊断与解决方案
在对机床进行参数调优的过程中,面对出现的各类问题,案例中所采用的问题诊断与解决方案的步骤可以总结如下:
1. **问题识别**:首先,通过零件成品的检测,识别出问题的性质和严重程度,比如是否存在过切或欠切等现象。
2. **数据收集**:收集相关加工参数数据以及机床状态信息,为分析问题提供基础数据支持。
3. **参数对比**:与已知的最佳加工参数进行对比,找出可能导致问题的参数偏差。
4. **调整与测试**:对疑似造成问题的参数进行调整,并进行小规模的加工测试。
5. **结果评估**:对调整后的加工结果进行评估,如问题已解决,则进行全批量生产;如问题依旧,需要进一步诊断。
案例中所采取的解决方案均基于对机床控制器参数的深入理解和正确的调整方法。对参数的准确调整,使得机床的加工性能得到充分发挥,最终确保了零件的加工精度。
## 4.2 提高加工效率的案例分析
### 4.2.1 大批量生产中的参数优化案例
在大批量生产中,提高加工效率意味着直接降低生产成本,提高市场竞争力。本案例中,一家汽车零部件制造企业面临生产效率低下的问题。
通过分析,确定提高加工效率的关键在于减少非加工时间,比如空行程时间和刀具换刀时间。通过参数调整,特别是针对刀具路径的优化和辅助功能的调整,实现了效率的显著提升。关键参数的调整如下:
- **快速定位速度(参数 No.1401)**:调整该参数,以提高机床快速移动的能力,减少了空行程时间。
- **刀具寿命管理(参数 No.5122)**:合理设置刀具寿命参数,避免因提前换刀而导致的生产中断。
- **多轴同步控制(参数 No.1501)**:针对多轴机床,优化同步控制参数,提高了多轴协同工作的效率。
调优之后,机床的空行程时间显著减少,整体生产节拍加快,从而大幅提升了加工效率。
### 4.2.2 案例中的效率提升策略
在提高加工效率的案例中,效率提升策略的制定和实施是至关重要的。具体步骤包括:
1. **效率评估**:对现有加工过程进行评估,确定提升空间。
2. **策略制定**:根据评估结果,制定包括参数调整在内的具体提升策略。
3. **参数优化**:应用机床控制器的参数优化功能,提高机床的运行效率。
4. **持续监控**:对生产过程进行持续监控,确保调整效果,并及时发现并解决新问题。
5. **经验总结**:将成功经验和教训总结,形成标准操作流程,为今后的效率提升提供参考。
通过上述策略,案例中的企业不仅在短期内提升了加工效率,更在长期的生产中建立了持续改进的机制。
## 4.3 增强机床稳定性的案例分析
### 4.3.1 长时间运行稳定性案例
长时间连续运行的稳定性对于保证生产进度和产品质量至关重要。本案例发生于一家自动化组件生产企业,其生产过程中需要机床长时间稳定运行。
机床在长时间运行后,出现了一定程度的性能波动,特别是在连续加工数百件零件后。通过对机床运行状态和参数的监控和分析,发现了以下关键因素导致了机床稳定性的下降:
- **伺服电机参数(参数 No.7501)**:由于长期使用,伺服电机的响应特性发生变化,需要调整相关参数以重新获得最佳性能。
- **热膨胀补偿(参数 No.5200)**:机床长时间运行会产生热变形,对加工件尺寸的准确性产生影响。通过合理设置热膨胀补偿参数,保证了加工件尺寸的一致性。
- **冷却系统参数(参数 No.1040)**:冷却系统对于机床的稳定运行同样重要,适当的冷却参数可以防止机床过热,延长设备寿命。
调整这些参数后,机床在长时间连续运行时表现出更高的稳定性和可靠性。
### 4.3.2 案例中的稳定性维护措施
为了应对长时间运行中的机床稳定性问题,案例中采用了以下稳定性维护措施:
1. **定期检查与调整**:定期对机床关键部件进行检查和维护,对关键参数进行调整。
2. **监控系统升级**:利用先进的监控系统实时监控机床运行状态,以便快速响应可能发生的稳定性问题。
3. **操作培训**:对操作人员进行系统培训,让他们了解参数调整的重要性和具体操作方法。
4. **维护记录与分析**:详细记录每次维护和调整的结果,对数据进行分析,找出潜在问题和改进点。
通过这些措施,案例中的企业确保了机床在长时间运行下的稳定性,为持续生产提供了坚实保障。
```mermaid
graph TD
A[开始案例分析] --> B[精密零件加工参数调优案例]
A --> C[提高加工效率的参数优化案例]
A --> D[长时间运行稳定性案例]
B --> B1[问题识别]
B --> B2[数据收集]
B --> B3[参数对比]
B --> B4[调整与测试]
B --> B5[结果评估]
C --> C1[效率评估]
C --> C2[策略制定]
C --> C3[参数优化]
C --> C4[持续监控]
C --> C5[经验总结]
D --> D1[定期检查与调整]
D --> D2[监控系统升级]
D --> D3[操作培训]
D --> D4[维护记录与分析]
```
```markdown
| 参数名称 | 初始值 | 调整后值 | 描述 |
|----------|--------|----------|------|
| 进给速度 | 1500 | 1200 | 降低速度以减少振动 |
| 切削液流量 | 150 | 200 | 增加冷却和润滑效果 |
| 刀具补偿 | 0.20 | 0.15 | 提高加工精度 |
| 快速定位速度 | 18000 | 20000 | 加速非加工移动 |
| 刀具寿命管理 | 100 | 150 | 延长刀具使用周期 |
| 多轴同步控制 | 0.5 | 0.3 | 提升轴间同步性 |
| 伺服电机参数 | 70 | 80 | 改善伺服响应 |
| 热膨胀补偿 | 0.05 | 0.03 | 确保加工件尺寸准确 |
| 冷却系统参数 | 100 | 120 | 优化冷却效果 |
```
```plaintext
# 参数调整代码示例
1. // 降低进给速度
1420 = 1200;
2. // 增加切削液流量
1040 = 200;
3. // 调整刀具补偿
5121 = 0.15;
4. // 提高快速定位速度
1401 = 20000;
5. // 设置刀具寿命管理
5122 = 150;
6. // 优化多轴同步控制
1501 = 0.3;
```
在上述案例中,我们通过具体的参数调整实例,展示了如何针对不同的生产需求和问题,通过FANUC-0i-MC机床控制器的参数定制化,实现加工精度的提升、加工效率的增加以及机床稳定性的增强。这些案例分析表明,通过科学的参数调优,机床的性能可以得到显著的提升,并且对于生产具有重大的积极影响。
# 5. FANUC-0i-MC参数定制化的问题与解决
## 5.1 常见参数定制化问题
### 5.1.1 参数调整不当引发的问题
参数的调整不当可能会引起一系列的问题,包括但不限于机床运动失常、加工精度偏差、甚至机床的损坏。由于FANUC-0i-MC控制器的参数众多,如果缺乏对机床特性和参数功能的充分理解,随意调整参数可能会导致不可预期的后果。例如,错误地修改了与伺服系统相关的参数,可能会引起机床抖动、定位不准确,严重时甚至可能损坏机床的关键部件。
### 5.1.2 参数记录与备份的重要性
在进行参数定制化时,记录和备份是一个关键步骤。每次修改参数后,都应该有详细的记录,包括修改前的参数值、修改后的新值、修改的具体原因及日期等。这些记录将作为未来问题追踪和系统恢复的重要参考。同时,定期备份参数配置能够防止由于意外情况导致参数丢失或损坏,确保机床能够在最短的时间内恢复到正常工作状态。
## 5.2 参数定制化中的安全考虑
### 5.2.1 参数调整的安全风险与防范
参数调整不仅影响机床的运行状态,也可能带来安全风险。不正确的参数设置可能会造成机床异常运动,增加操作员受伤的风险。因此,在进行参数调整时,必须采取严格的安全措施。这包括在进行任何参数调整前,确保机床已经完全停止运行,并解除任何可能的紧急停止。同时,应该在调整参数前,对操作员进行充分的安全培训,并确保他们了解相关风险和应对措施。
### 5.2.2 安全标准和最佳实践
遵循最佳实践和安全标准是保证参数定制化工作顺利进行的重要手段。这包括但不限于:使用经过验证的参数调整方法;对调整结果进行充分测试;在操作员间共享调整经验;确保所有的操作都符合行业安全标准。此外,对于参数调整过程的每一步都要进行文档记录,一旦出现问题可以快速回溯,找到原因并解决问题。
## 5.3 参数定制化的未来趋势
### 5.3.1 集成智能控制系统的参数策略
随着工业4.0的发展和智能制造概念的普及,未来的FANUC-0i-MC参数定制化将越来越侧重于智能控制系统集成。这意味着,参数策略不仅仅是为了满足当前的性能需求,更是为了与更智能的生产系统兼容。比如,集成先进的传感器和诊断工具,可以实现对机床性能的实时监控,并根据实时数据调整参数,以实现最优的加工效率和质量。
### 5.3.2 预测性维护与参数分析的结合
预测性维护是指通过分析历史数据和实时数据来预测设备故障,从而采取预防措施以避免意外停机。结合FANUC-0i-MC的参数分析,可以更准确地预测和预防机床故障。通过连续监测关键参数和分析趋势,可以对机床状态进行评估,并在问题发生之前调整参数,从而延长机床的运行时间和生产效率。
总结:
本章深入探讨了FANUC-0i-MC参数定制化过程中可能遇到的问题及其解决方案,并展望了参数定制化的未来趋势。通过理解参数调整不当带来的风险,并采取预防措施,以及遵循安全标准和最佳实践,可以确保参数定制化工作顺利进行。同时,结合智能控制系统和预测性维护的参数分析,预示着参数定制化在未来将更加智能化和自动化,为机床性能优化带来新的可能性。
# 6. 打造个人的机床性能优化策略
在现代制造行业中,持续优化机床性能是提升竞争力的关键因素。FANUC-0i-MC数控系统的参数定制化为机床操作者提供了深入调整和优化机床性能的机会。本章将探讨如何制定个性化的参数定制化方法,创建参数优化的流程与文化,并展望智能化和自动化趋势下的参数优化策略。
## 6.1 个性化参数定制化方法
### 6.1.1 根据机床特性的参数定制
每个机床都有其独特的特性,这些特性在参数定制化时必须得到充分考虑。以下是一个根据机床特性定制参数的步骤:
1. **机床评估:** 在调整参数前,首先对机床进行彻底的评估,包括它的使用频率、加工类型、负载特性及历史维护记录。
2. **基准参数获取:** 从机床手册或设备制造商处获取标准参数作为基准。
3. **数据记录:** 在调整前记录所有关键参数的原始值,以及任何与性能相关的测量数据。
4. **参数调整:** 根据评估结果调整参数。例如,如果机床在高速加工时出现抖动,可能需要调整伺服参数。
5. **性能验证:** 进行一系列测试加工以验证性能是否改善,同时监测参数变化对加工质量的影响。
### 6.1.2 结合生产需求的定制化
为确保定制化符合生产需求,以下步骤可能需要执行:
1. **需求分析:** 分析生产需求,如提升加工速度、提高加工精度或是减少能耗。
2. **参数仿真:** 在实际调整前,使用仿真软件预览参数变化可能带来的影响。
3. **小批量测试:** 在不影响生产的情况下,先在小批量的加工任务上测试调整的参数。
4. **反馈循环:** 依据测试结果调整参数,并收集操作员的反馈。
5. **持续监控:** 在参数定制后继续监控机床性能,确保优化效果持续。
## 6.2 创建参数优化的文化与流程
### 6.2.1 建立持续优化的组织文化
为了建立一个以持续优化为目标的组织文化,需要考虑以下几点:
1. **知识共享:** 鼓励知识共享,让每个操作员都能了解如何优化参数,并能够分享自己的经验。
2. **培训与教育:** 定期对操作员进行FANUC-0i-MC系统参数定制化的培训。
3. **激励机制:** 设计奖励制度,激励员工进行创新和优化工作。
### 6.2.2 参数优化的流程与方法论
一个有效的参数优化流程应该包括以下步骤:
1. **问题定义:** 明确优化的目标和期望的结果。
2. **方案制定:** 制定一个详细的操作计划,包括参数调整的范围和顺序。
3. **执行与监控:** 执行计划并监控参数调整过程中的性能变化。
4. **效果评估:** 定期评估优化效果,如果必要,回退并尝试其他方法。
## 6.3 走向智能化与自动化的参数优化
### 6.3.1 参数优化与机器学习的结合
机器学习在参数优化中的应用可以大大提升优化过程的效率和效果。以下是如何结合机器学习的步骤:
1. **数据收集:** 收集大量历史加工数据用于机器学习模型的训练。
2. **模型训练:** 使用收集的数据训练机器学习模型,识别影响加工性能的关键因素。
3. **预测与调优:** 利用模型进行预测,并根据预测结果自动调整参数。
### 6.3.2 未来技术对参数优化的影响
随着新技术的发展,例如物联网(IoT)和数字孪生技术,我们预见到以下趋势:
1. **远程监控:** 实现对机床性能的实时远程监控和调整。
2. **实时数据分析:** 利用大数据技术实时分析生产数据,快速做出参数调整决策。
3. **预测性维护:** 结合预测性维护技术,提前预测机床故障并优化参数设置,以预防潜在的停机时间。
在本章中,我们探讨了如何打造个性化的机床性能优化策略,如何创建以优化为核心的组织文化和流程,并展望了智能化与自动化在未来参数优化中的作用。通过不断探索和实践,机床操作者可以利用FANUC-0i-MC控制器的参数定制化功能,推动生产力的持续增长和制造业的创新。
0
0
相关推荐







