【S7200指令集全攻略】:自动化工程师必备的编程秘籍(20个核心指令速成)
发布时间: 2025-01-05 09:07:20 阅读量: 15 订阅数: 15 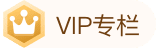
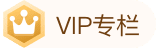
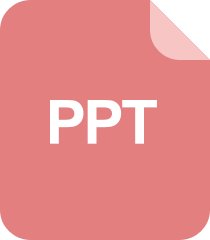
S7200PLC的指令系统ppt课件.ppt
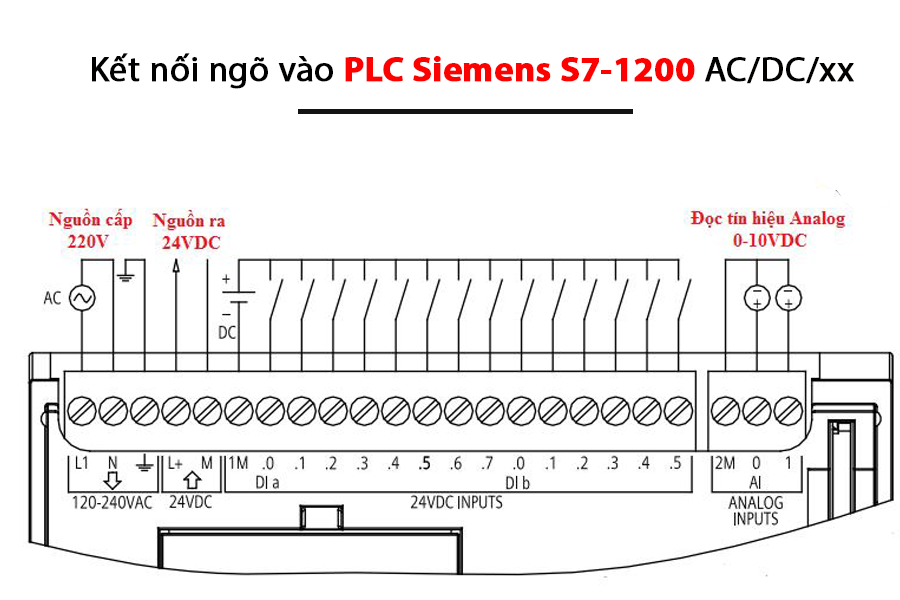
# 摘要
本文详细介绍了S7200 PLC及其指令集的基础知识和应用。第一章提供了S7200 PLC和其指令集的概述。第二章深入探讨了基础指令,包括输入输出指令、定时器和计数器指令、以及数据处理指令,并通过应用实例加深理解。第三章进一步讨论了进阶指令实践,如算术运算指令、程序控制指令和字符串处理指令,以及编程案例。第四章强调了S7200指令集在自动化项目中的应用,涵盖顺序控制编程、模拟量处理与PID调节,以及故障诊断与通信指令。最后一章着重于高级技巧与优化,包括编程技巧、指令集优化和安全编程,旨在提高程序性能和可靠性。本文旨在为读者提供全面的S7200 PLC指令集应用指南,以支持复杂的自动化解决方案。
# 关键字
S7200 PLC;指令集;输入输出;定时器;数据处理;程序优化
参考资源链接:[S7-200 PLC基本指令详解:梯形图与语句表](https://wenku.csdn.net/doc/4bak7gw0i0?spm=1055.2635.3001.10343)
# 1. S7200 PLC和指令集概述
## 1.1 S7200 PLC简介
西门子S7200系列PLC是一款广泛应用于工业自动化领域的可编程逻辑控制器。它以其卓越的性能、灵活的配置以及强大的指令集而闻名,能够满足从简单到复杂的自动化需求。S7200 PLC不仅具有高可靠性,还支持各种通讯方式,使其能够轻松集成到各种复杂的工业环境中。
## 1.2 指令集的作用与重要性
指令集是PLC编程的基础,它规定了PLC能执行的所有操作。一个强大的指令集可以极大地扩展PLC的功能,提升其处理任务的灵活性和效率。S7200指令集包含了许多基础和进阶指令,涵盖了数据处理、算术运算、程序控制等多个方面,是实现各种自动化控制逻辑的基础。
## 1.3 指令集的结构与分类
S7200指令集按功能划分为多个类别,例如基础逻辑指令、定时器和计数器指令、数据处理指令等。每类指令有其特定的应用场景。例如,输入输出指令用于控制外围设备与PLC的数据交换;定时器和计数器指令用于实现精确的时序控制与计数任务;数据处理指令则涉及数据格式转换和数值运算。
通过后续章节的深入讨论,我们将详细探究这些指令的具体使用方法和编程技巧。这将为读者构建扎实的S7200 PLC编程基础,为进一步探索自动化领域打下坚实的基础。
# 2. 基础指令详解
### 输入输出指令
#### I/O配置与读取方法
在自动化控制系统中,输入/输出(I/O)指令用于实现PLC与外部设备之间的数据交换。S7-200 PLC的I/O配置可以通过编程软件进行,例如Step7-Micro/WIN。I/O读取通常涉及到读取输入模块的状态(例如传感器信号)或写入输出模块以驱动执行元件(如继电器或马达)。
在配置I/O时,需要识别并设置每个I/O地址,确保外部设备与正确的I/O点相对应。在读取I/O信息时,PLC会根据地址读取或更新其I/O映像表,这个表存储了所有输入和输出的实际状态。
代码示例:
```plaintext
// 读取输入I0.0的状态并将其赋值给M0.0辅助继电器
L I0.0
T M0.0
// 向输出Q0.0发送信号
L M0.0
T Q0.0
```
在这个示例中,我们使用了两个简单的指令来读取输入I0.0并将其状态传递给辅助继电器M0.0。然后,我们检查M0.0的状态,并将其复制到输出Q0.0。这样,如果传感器接收到信号,相应的执行元件就会被激活。
#### 常用I/O指令及应用实例
在S7-200 PLC中,一些常用输入输出指令包括:
- `I` 读取输入
- `Q` 输出到模块
- `M` 辅助继电器(内部存储位)
下面是一个应用实例,说明如何在自动化控制系统中使用I/O指令。
假设我们需要控制一个启动/停止电路,其中包括一个启动按钮(连接到输入I0.0),一个停止按钮(连接到输入I0.1),以及一个控制马达的继电器(连接到输出Q0.0)。
代码示例:
```plaintext
// 检查启动按钮是否被按下,同时确保停止按钮未被按下
L I0.0
ANDN I0.1
= Q0.0 // 输出到马达继电器
// 反向逻辑,检查停止按钮是否被按下
L I0.1
= M0.1 // 使用辅助继电器作为锁存信号
// 如果停止按钮被按下,则停止马达
L M0.1
R Q0.0
```
在这个应用实例中,当启动按钮被按下且停止按钮未被按下时,马达继电器会被激活。辅助继电器M0.1被用来锁存停止按钮的状态,保证在停止按钮被释放后马达仍能停止。
### 定时器和计数器指令
#### 定时器的工作原理与编程
在PLC编程中,定时器(T)用于产生时间延迟或测量时间长度。在S7-200 PLC中,定时器可以通过编程软件预设时间参数,例如PT(预设时间)和ET(已经过去的时间)。定时器的工作原理是根据设定的时间值逐渐累加计数,直到达到设定值。
定时器有几种类型,如ON延时定时器(TON)、OFF延时定时器(TOFF),和脉冲定时器(TP)。在编程时,我们需要指定定时器的地址、预设时间,以及定时器完成时将执行的输出。
代码示例:
```plaintext
// 设置一个ON延时定时器,预设时间为2秒
LD 2
TON T0
// 当定时器完成时,输出到Q0.1
L T0
SE 100
= Q0.1
```
在这个例子中,我们使用了一个ON延时定时器(T0),当其输入条件(LD 2)满足时开始计时。一旦定时器的累计时间(SE 100)达到2秒,Q0.1将会被激活。
#### 计数器指令应用与案例分析
计数器(C)在PLC中用于计数输入事件,如物品通过计数器传感器的次数。在S7-200 PLC中,计数器同样需要设置地址和计数值。在编程中,计数器可以是增计数(CTU)、减计数(CTD)或增减计数(CTUD)。
假设我们有一个应用场景,需要计数通过某个检测点的物体数量,并在达到一定数量后激活一个报警信号。
代码示例:
```plaintext
// 增计数器
LD I0.2
CTU C0 K10
// 当计数器达到10时,激活报警信号
L C0
SE 10
= Q0.2
```
在这个示例中,每当地址I0.2检测到信号时,计数器C0就会加1。当计数器的累计值达到10(K10)时,Q0.2输出会被激活,触发报警。
### 数据处理指令
#### 数据移动与转换操作
数据移动和转换操作是S7-200 PLC编程的基础,它们允许数据在不同的存储位置之间传递和处理。常用的数据移动指令包括数据传送(T),数据交换(XCHG),以及将整数转换为实数(ITD)等。
在自动化控制系统中,数据处理用于实现数据转换、比较操作,以及逻辑运算等。数据处理指令使得PLC能够根据输入条件执行更复杂的控制任务。
代码示例:
```plaintext
// 将输入I0.0的状态移动到M0.2
L I0.0
T M0.2
// 将整数数据从数据块DB0的地址0移动到累加器中
L DB0.DBW0
T IW4
```
在这个例子中,我们使用了数据传送指令(T),将输入I0.0的状态赋值给辅助继电器M0.2,以及从数据块DB0中读取数据到累加器。
#### 二进制与BCD码的处理
在某些应用场景中,PLC需要处理数字的二进制和BCD(二进制编码的十进制)表示形式。S7-200 PLC提供了一系列的指令来转换这些数值,如二进制到十进制转换(BTD)和BCD到二进制转换(DTB)。
例如,当PLC需要将传感器读取的BCD码值用于数值计算时,就需要将BCD码转换为二进制数。这可以通过DTB指令实现。
代码示例:
```plaintext
// 将BCD码数据DB0.DBW0转换为二进制数并存储到累加器中
L DB0.DBW0
DTB
T IW4
```
这个示例中,我们首先使用“L”指令将BCD码数据加载到累加器,接着使用“DTB”指令将BCD码转换成二进制数,并最终将结果存入累加器。
以上内容展示了S7-200 PLC中基础指令的多样性和实用性,它们是构建更加复杂自动化系统的基础。接下来,我们将探索进阶指令在实践中的应用。
# 3. 进阶指令实践
在第三章中,我们将会深入了解S7200 PLC的进阶指令集,并提供实际编程案例和技巧。进阶指令集包括但不限于算术运算、程序控制、以及字符串处理等。这些指令扩展了PLC的功能,使得我们能够完成更为复杂的控制任务。本章内容会通过实际的应用实例来展示这些指令的用法,并解析如何在不同场景下选择和使用这些高级指令。
## 3.1 算术运算指令
算术运算指令是任何控制系统中不可或缺的一部分,它们在S7200 PLC中扮演着核心角色。算术运算包括加、减、乘、除以及逻辑运算等,它们使得PLC能够进行数值计算,并根据计算结果执行相应的控制动作。
### 3.1.1 加减乘除与逻辑运算
加减乘除是基本的算术运算,通常用于计算控制变量的值,如计算电机的加速时间、阀门的开启角度等。逻辑运算则通常用于处理布尔量,如传感器状态的组合,从而实现更复杂的控制逻辑。
#### 算术运算指令的应用示例
假设我们有一个温度控制系统,需要根据实时温度值与预设目标温度的差值来调整加热器的工作状态。这里就可以用到加减运算指令。
```plaintext
// 假设MW100存储的是实时温度值,MW102存储的是目标温度值
// MW104将用来存储温度差值,即MW100-MW102
L MW100 // 将MW100的值加载到累加器
- MW102 // 从累加器中减去MW102的值
T MW104 // 将累加器的结果存储到MW104
```
执行上述指令后,MW104将包含两个温度值的差,这个差值可以用来进一步控制加热器。
逻辑运算例如AND、OR等,它们可以将多个条件组合起来,执行如启动电机的逻辑判断。
```plaintext
// 假设M0.0是温度过低的传感器状态,M0.1是温度过高的传感器状态
// 如果温度过低且温度未过高,则M0.2为真,可以启动加热器
AN M0.1 // 如果M0.1为真,则结果为假(逻辑与非)
OR M0.0 // 如果M0.0为真,则结果为真
= M0.2 // 将结果赋值给M0.2
```
在这个例子中,我们使用了逻辑非操作(`AN`)和逻辑或操作(`OR`),实现了一个简单的控制逻辑。
### 3.1.2 实际编程案例与技巧
实际编程时,除了基本的运算操作外,还应考虑如何高效地使用这些指令来实现程序的优化。例如,在处理大批量数据时,可以利用数据块(DB)来存储中间结果,这样可以减少对累加器的依赖,提高程序效率。
```plaintext
// 将数据块DB1中的数据与寄存器中的数据进行加法运算
// 假设DB1.DBW0存储了要加的数,MW100是另一个要相加的数
L DB1.DBW0 // 加载DB1中的数据到累加器
+ MW100 // 将累加器中的数据与MW100相加
T DB1.DBW2 // 将结果存储到DB1的另一位置
```
这种操作可以避免不必要的中间变量,直接在内存中进行计算,提高程序性能。
## 3.2 程序控制指令
程序控制指令主要负责PLC程序的流程控制,包括条件分支、循环控制等。这些指令使得程序能够根据不同的输入执行不同的程序段,实现复杂的控制逻辑。
### 3.2.1 程序的分支与循环控制
分支控制通常是通过条件跳转指令实现的,如`JMP`和`JZ`(跳跃到标签,如果结果为零则跳跃)。循环控制则是通过循环开始和循环结束指令实现,如`FOR`、`NEXT`或`WHILE`、`REPEAT`等。
#### 分支控制示例
假设我们需要根据一个传感器的状态来决定是执行加热程序还是冷却程序。这可以通过分支控制指令来实现。
```plaintext
// 假设M0.0是传感器状态标志位
L M0.0 // 加载M0.0的状态到累加器
JZ Label1 // 如果M0.0为0(即传感器未触发),则跳转到Label1标签
CALL Heating_Routine // 调用加热程序
JMP End // 跳转到程序结束标签
Label1:
CALL Cooling_Routine // 调用冷却程序
End:
// 程序结束
```
#### 循环控制示例
循环控制指令可以用来反复执行一组指令,直至满足某些条件。下面的代码演示了如何通过循环控制来等待一个过程的结束。
```plaintext
// 循环读取状态直到完成标志位为真
LoopStart:
L State // 加载当前状态到累加器
JMP LoopEnd // 如果状态为完成,则跳到循环结束
// 循环体内操作
CALL Process // 调用过程函数
JMP LoopStart // 跳回循环开始,继续检查状态
LoopEnd:
// 循环结束后的操作
```
### 3.2.2 实现条件逻辑的高级指令
在实现条件逻辑时,可以使用一些高级指令来简化代码,例如条件传送指令(`MOVN` 和 `MOVZ`)和比较指令(`CMP`)。这些指令通过减少分支语句,可以简化代码逻辑,提升程序执行效率。
```plaintext
// 如果M0.0为真,则将MW100的值传送到MW102
// 否则,将0传送到MW102
L M0.0 // 加载M0.0的状态
JZ Skip // 如果为假(M0.0为0),跳过传送
MOVN MW102 MW100 // 如果不跳过,则执行传送非指令
JMP End // 跳转到程序结束
Skip:
MOV MW102 0 // 将0传送到MW102
End:
// 程序结束
```
## 3.3 字符串处理指令
S7200 PLC的进阶指令集还包括了一些用于处理字符串的指令,这些指令对于那些需要进行文本处理的工业应用非常有用。
### 3.3.1 字符串操作与应用实例
字符串操作包括字符串的比较、连接、替换等。这对于需要进行信息提示、日志记录或与外部系统交互的场合至关重要。
```plaintext
// 将两个字符串连接起来
L #String1
+ #String2
T #Result
```
在上面的示例中,`#String1` 和 `#String2` 被连接成一个新的字符串,并存储到 `#Result` 中。
### 3.3.2 字符串与数组的相互转换
在某些应用中,可能需要将字符串转换为数组,或者将数组转换成字符串,以便于进行其他处理。
```plaintext
// 将字符串转换为数组
L #String1
T #Array1
```
在实际应用中,这些转换操作可以根据具体需求进行更为复杂的数据处理。
在本章中,我们详细讨论了S7200 PLC的进阶指令集及其实际应用。通过算术运算、程序控制和字符串处理等实例,我们了解了如何将这些高级指令应用于解决实际问题。在下一章中,我们将进一步探讨这些指令集在自动化项目中的应用,包括顺序控制、模拟量处理以及故障诊断等主题。
# 4. S7200指令集在自动化项目中的应用
## 4.1 顺序控制编程
### 4.1.1 步进逻辑与状态机设计
在自动化项目中,顺序控制编程是实现复杂过程自动化的核心技术之一。通过步进逻辑(Sequential Logic)和状态机(State Machine)设计,我们可以构建一个能够处理一系列预先定义步骤的控制系统。这种方法确保了操作的有序性和可控性,使得整个自动化过程更加精确和高效。
状态机是顺序控制编程的基础,它包含一组状态和决定系统行为的转移条件。在S7200 PLC编程中,通常使用位存储器(M)来表示状态机中的各个状态,而程序的逻辑则负责根据输入条件和当前状态来决定转移和执行相应的操作。
下面是一个简单的状态机设计示例,演示如何使用S7200的位存储器来实现一个控制灯闪烁的简单状态机:
```plaintext
状态:
M0.0 - 初始状态
M0.1 - 灯亮状态
M0.2 - 灯灭状态
输入:
I0.0 - 启动按钮
I0.1 - 停止按钮
输出:
Q0.0 - 灯
```
```plaintext
// 初始状态,灯初始为关闭状态
IF I0.0 AND NOT M0.1 THEN
M0.0 := 1; // 初始状态
M0.1 := 0; // 灯亮状态未激活
M0.2 := 0; // 灯灭状态未激活
Q0.0 := 0; // 关闭灯
END_IF
// 初始状态 -> 灯亮状态
IF M0.0 AND I0.0 THEN
M0.1 := 1; // 激活灯亮状态
M0.0 := 0; // 初始状态退出
END_IF
// 灯亮状态 -> 灯灭状态
IF M0.1 AND NOT I0.1 THEN
M0.2 := 1; // 激活灯灭状态
M0.1 := 0; // 灯亮状态退出
Q0.0 := 1; // 点亮灯
END_IF
// 灯灭状态 -> 初始状态
IF M0.2 AND I0.1 THEN
M0.0 := 1; // 激活初始状态
M0.2 := 0; // 灯灭状态退出
Q0.0 := 0; // 关闭灯
END_IF
```
在实际的工业应用中,状态机可以设计得更加复杂,例如包括多个并行状态和更复杂的转移逻辑。这样的设计不仅限于简单的灯控制,还可以广泛应用于传送带控制、机械臂操作、化学品混合等工业过程。
### 4.1.2 实际工业控制案例分析
让我们来深入探讨一个实际的工业控制案例,以展示如何在实际项目中应用顺序控制编程。
假设我们需要控制一个包装生产线,其中包括了如下几个步骤:
1. 检测产品是否到位
2. 包装产品
3. 贴标签
4. 输出产品到输出托盘
在S7200 PLC程序中,我们可以用以下步骤实现这个过程的顺序控制:
```plaintext
// 步骤1:检测产品是否到位
IF I0.0 (产品传感器) THEN
M0.0 := 1; // 产品到位信号置位
END_IF
// 步骤2:包装产品
IF M0.0 THEN
Q0.0 (包装机械启动) := 1;
// 假设包装时间为5秒
TON T0 (5秒定时器);
IF T0.Q THEN
M0.0 := 0; // 完成包装
M0.1 := 1; // 进入贴标签步骤
END_IF
END_IF
// 步骤3:贴标签
IF M0.1 THEN
Q0.1 (贴标机械启动) := 1;
// 假设贴标时间为2秒
TON T1 (2秒定时器);
IF T1.Q THEN
M0.1 := 0; // 完成贴标签
M0.2 := 1; // 进入输出步骤
END_IF
END_IF
// 步骤4:输出产品到输出托盘
IF M0.2 THEN
Q0.2 (输出机械启动) := 1;
// 假设输出时间为3秒
TON T2 (3秒定时器);
IF T2.Q THEN
M0.2 := 0; // 完成输出
// 返回步骤1,等待下一批次产品
END_IF
END_IF
```
这个案例演示了如何使用S7200的定时器和状态位来控制一个包装线的顺序操作。实际应用中,可能需要加入更多的安全检查和故障处理逻辑,以保证生产线的稳定运行。
## 4.2 模拟量处理与PID调节
### 4.2.1 模拟输入输出的处理
在许多自动化应用中,除了数字量(开关量)信号的处理外,还需要处理模拟量信号,例如温度、压力、流量、速度等连续变化的物理量。S7200 PLC提供了模拟量输入输出模块,使得能够接入这类信号并将其转换为数字信号进行处理。
模拟量信号通常以4-20mA或0-10V的形式表示,PLC模块能够读取这些信号并将其转换为12位或16位的数字值。这样的转换过程被称为模拟到数字转换(ADC)。同样地,将处理后的数字信号转换回模拟信号的过程称为数字到模拟转换(DAC),用于控制执行机构如阀门和电机。
模拟输入和输出信号的处理是通过S7200指令集中的相应模块实现的,下面是一个模拟输入处理的示例代码:
```plaintext
// 读取模拟输入
AIW0 := AIW0; // 假设AIW0是连接到模拟输入模块的模拟信号输入地址
// 将读取到的模拟值转换为实际的物理量(例如温度)
// 假设使用4-20mA表示0-100度
MTEMP := ((AIW0 - 27648) / (32767 - 27648)) * 100;
// 根据实际物理量进行控制逻辑
IF MTEMP > 50 THEN
// 如果温度过高,打开冷却系统
Q0.0 := 1;
ELSE
// 如果温度适宜,关闭冷却系统
Q0.0 := 0;
END_IF
```
模拟输出信号的生成通常用于控制如调节阀这样的执行机构,调节流过系统的物料量。以下是模拟输出的示例代码:
```plaintext
// 设置模拟输出值
// 假设控制一个0-10V表示的阀门,我们需要将其设置为50%开度
AOV0 := 16384; // 16384是5V对应的12位数字值
```
### 4.2.2 PID控制指令的应用与调试
在自动化过程中,许多应用需要精确控制温度、速度、流量等物理量。比例-积分-微分(PID)控制是一种广泛使用的反馈控制算法,它可以实现精确的控制效果。S7200 PLC提供了PID控制指令,使得实现PID控制变得简单。
PID控制器通过计算设定点(SP)和实际过程变量(PV)之间的差值(偏差)来工作。它包含三个主要部分:
- 比例(P)部分负责根据当前偏差成比例地调整控制量。
- 积分(I)部分负责消除稳态误差,通过对偏差进行积分运算。
- 微分(D)部分负责预测未来的偏差,减少系统的超调和振荡。
下面是一个使用PID指令的基本示例:
```plaintext
// PID控制参数
Kp := 2.0; // 比例系数
Ki := 0.1; // 积分系数
Kd := 1.0; // 微分系数
// PID控制指令
PID SP, PV, Kp, Ki, Kd, CyCLE, P, I, D
// 假设设定点为75度
// 实际过程变量为模拟输入模块处理后的温度值
PID MW10, MTEMP, Kp, Ki, Kd, 100, QW0, QW2, QW4
// 输出控制量到模拟输出
AOV0 := QW0; // 将PID控制计算出的控制量输出到模拟输出模块
```
在实际应用中,PID参数(Kp、Ki、Kd)需要根据具体的控制系统进行调整,以获得最佳的控制性能。这通常通过调节器上的按钮、HMI或者程序中的参数调整功能来实现。
## 4.3 故障诊断与通信指令
### 4.3.1 指令集中的故障诊断功能
对于任何自动化系统来说,有效的故障诊断机制是至关重要的。S7200 PLC提供了多种故障诊断指令,使开发者能够检测、诊断和报告系统中的问题。在故障发生时,能够迅速定位和解决问题,减少了系统的停机时间,提高了系统的可靠性。
S7200 PLC的故障诊断指令集通常包括用于检测和处理如下问题的指令:
- PLC运行状态
- 诊断缓冲区的读取
- 模块状态检测
- 硬件或软件故障的识别
- 网络通信故障的诊断
下面是一个使用故障诊断功能的示例:
```plaintext
// 检查PLC是否正常运行
IF "Status" := 'Running' THEN
// PLC处于运行状态,继续处理正常逻辑
ELSE
// PLC处于停止或错误状态,启动故障诊断和处理程序
// 读取诊断缓冲区信息
// 显示错误代码和描述
// 执行错误处理逻辑,如重置PLC、发送报警信号等
END_IF
```
### 4.3.2 PLC之间的通信与数据交换指令
在更复杂的自动化应用中,可能需要多个PLC之间进行通信和数据交换。S7200 PLC支持多种通信方式,包括工业以太网、串行通信等。通过这些通信方式,可以实现多个PLC之间的数据共享,协调控制,以及系统集成。
一个常见的通信任务是读写远程PLC上的数据块。S7200提供了如GET、PUT等指令来实现数据的读写。下面是一个使用通信指令的基本示例:
```plaintext
// 从远程PLC读取数据块
GET DB 123, DBD 0, #DBDVar, #Size
// 将本地数据块中的数据发送到远程PLC
PUT DB 123, DBD 0, #DBDVar, #Size
```
其中,#DBDVar是需要读取或写入的数据变量,#Size指定了数据块的大小。
在实际应用中,通信指令的使用更加复杂,可能需要配置网络参数,处理通信错误,并确保数据交换的实时性和准确性。
本章节通过应用S7200指令集在自动化项目中的应用,讲述了顺序控制编程、模拟量处理与PID调节以及故障诊断与通信指令的深入实践。通过上述内容的详细分析,读者能够了解到如何在真实的工业项目中高效地运用S7200指令集,解决实际问题,并提升整个自动化系统的性能和可靠性。
# 5. S7200指令集的高级技巧与优化
## 5.1 高级编程技巧
### 5.1.1 功能块与数据块的构建
在编写S7200 PLC程序时,有效地使用功能块(Function Blocks, FB)和数据块(Data Blocks, DB)可以显著提高程序的结构化水平和模块化。功能块是一种封装了一组逻辑操作的代码块,可以通过参数输入和输出来控制。数据块用于存储程序中使用的临时数据。
- **创建功能块**:首先需要定义功能块的输入输出参数和局部变量,然后在块中编写逻辑。例如,创建一个报警功能块,它可以接收多个输入信号,并根据逻辑输出报警信息。
- **使用数据块**:数据块可以用来存储静态数据,如系统配置参数或计时器的预设值。数据块中的数据可以在多个程序块之间共享。
```plaintext
// 示例代码块:创建一个简单报警功能块
FUNCTION_BLOCK AlarmFB
VAR_INPUT
SensorValue : INT; // 传感器读数
Threshold : INT; // 阈值设置
END_VAR
VAR_OUTPUT
AlarmActive : BOOL; // 报警是否激活
END_VAR
VAR
// 内部变量
END_VAR
BEGIN
IF SensorValue > Threshold THEN
AlarmActive := TRUE;
ELSE
AlarmActive := FALSE;
END_IF;
END_FUNCTION_BLOCK
```
### 5.1.2 提升程序可读性的策略
编写可读性强的代码对维护和后续的故障排查至关重要。PLC程序的可读性可以通过以下策略来提升:
- **遵循命名约定**:使用有意义的变量名和注释来描述代码的功能和逻辑。例如,为每个计时器、计数器和数据块命名时,应反映其用途或控制的物理对象。
- **代码组织**:将功能类似的代码逻辑组织在一起,使用空行和缩进以区分不同的代码块或逻辑分支。
- **使用注释**:在每个重要代码块的开始处添加注释,说明该代码块的作用和主要逻辑。
- **常量定义**:将硬编码的数值定义为常量,这不仅使代码更易于维护,也便于理解和调试。
```plaintext
// 示例代码块:使用常量和注释提高代码可读性
CONST
MOTOR_STARTDELAY : TIME := T#10S; // 电机启动延迟时间常量
MAX_CURRENT : REAL := 15.0; // 最大电流值
END_CONST
// 程序代码
// 电机启动逻辑
IF NOT MotorRunning AND ElapsedTime >= MOTOR_STARTDELAY THEN
StartMotor();
MotorRunning := TRUE;
ELSEIF Current > MAX_CURRENT THEN
StopMotor();
MotorRunning := FALSE;
// 处理过载情况
// ...
END_IF;
```
## 5.2 指令集优化与维护
### 5.2.1 指令选择对性能的影响
在编程时,正确选择指令可以提升程序运行的效率。例如,在处理数组和循环时,使用专门的数据操作指令(如数据块操作指令)通常比逐个操作数组元素要高效。此外,避免使用会导致程序扫描周期变长的复杂或低效指令。
- **选择合适的指令**:对于常见的操作,尽量使用优化过的指令,如 `MOV`、`ADD`、`SUB` 等基本操作指令。
- **指令的执行时间**:了解不同指令的执行时间,对于循环或频繁执行的代码段,选择执行时间短的指令。
### 5.2.2 程序调试与性能优化技巧
调试是发现并修正程序错误的过程。S7200 提供了多种调试工具,如在线监视和诊断工具,可以帮助开发者快速定位问题。
- **在线监视**:使用编程软件的在线监视功能,实时查看寄存器、数据块和程序块的状态。
- **性能分析**:利用性能分析工具来检查程序中的瓶颈,如长循环或等待时间过长的I/O操作。
```plaintext
// 示例代码块:使用程序监视和诊断工具
PROGRAM MonitorAndDiagnose
// 伪代码,展示如何设置监视点
SET BREAKPOINT ON LINE 5; // 在行号5设置断点
SET WATCHPOINT ON VAR MotorState; // 监视MotorState变量的变化
// 程序主体
IF StartButton AND NOT MotorState THEN
SET MotorState := TRUE;
// 电机启动逻辑...
ELSEIF StopButton THEN
SET MotorState := FALSE;
// 电机停止逻辑...
END_IF;
```
## 5.3 安全编程与异常处理
### 5.3.1 编程中的安全考虑与实现
安全编程是指在编写程序时采取预防措施,确保系统在遇到错误或异常时能够安全运行或安全停机。这包括使用看门狗定时器、监控关键变量和实施紧急停止逻辑。
- **看门狗定时器**:在程序中加入看门狗定时器,以确保程序在规定的时间内运行。如果程序运行延迟或停止响应,看门狗定时器会触发并执行安全措施。
- **关键变量监控**:对关键变量进行持续监控,并在变量值超出预期范围时触发警报或安全措施。
- **紧急停止逻辑**:设计紧急停止逻辑,确保在任何异常情况下,系统能迅速安全地停机。
### 5.3.2 异常与故障处理的最佳实践
在程序中处理异常和故障时,最佳实践包括:
- **异常捕获**:为常见错误和异常设置异常处理程序,如使用 `ON_ERROR` 或 `TRY/CATCH` 语句捕获执行期间的错误。
- **故障记录**:在发生异常时,记录详细的故障信息,如错误代码、发生时间和相关变量状态,以便于后续的问题分析和调试。
- **恢复策略**:在异常处理中包含恢复策略,确保在异常发生后系统可以尽快恢复正常运行或安全地进入维护模式。
```plaintext
// 示例代码块:实现异常处理逻辑
TRY
// 正常程序逻辑
// ...
CATCH
// 异常处理逻辑
LogError("An error occurred with code " + ERROR_CODE);
// 执行错误恢复或系统停机操作
// ...
END TRY
```
安全编程和异常处理是确保自动化系统稳定运行和提高系统可靠性的关键方面。通过合理的安全措施和异常处理机制,可以最大限度地减少系统故障对生产和安全的影响。
0
0
相关推荐







