【产品质量保证】:SMIC 180nm工艺测试与验证的关键步骤
发布时间: 2024-11-29 13:09:14 阅读量: 31 订阅数: 47 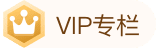
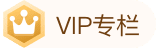
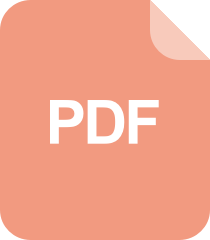
SMIC 180nm工艺使用手册

参考资源链接:[SMIC 180nm工艺使用手册:0.18um混合信号增强SPICE模型](https://wenku.csdn.net/doc/4hpp59afiy?spm=1055.2635.3001.10343)
# 1. SMIC 180nm工艺概述
半导体制造国际公司(SMIC)的180nm工艺标志着深亚微米技术的一个重要里程碑。该工艺代表了在20世纪末至21世纪初,集成电路制造技术从微米级向纳米级演进的过渡点。180nm工艺不仅为更高密度的集成电路提供了可能,还为后续更先进的工艺节点奠定了基础。
## 1.1 技术背景
180nm工艺的命名来源于其晶体管门的最小特征尺寸。这一技术在当时为诸如内存、微处理器、以及多种专用集成电路(ASICs)的设计和生产提供了前所未有的电路密度。180nm工艺允许芯片设计者集成数百万甚至更多的晶体管,从而提供了更高的处理能力和集成度。
## 1.2 工艺特点
该工艺节点具有几个显著特点,包括其引入的深沟道隔离(STI)技术,这有助于减少晶体管间的串扰和漏电流。此外,180nm工艺支持双层金属互连,为电路布局提供了更大的灵活性,并为高速信号的传输和功耗管理打下了基础。这些特点使得180nm工艺成为当时通信、消费电子和汽车电子等众多领域广泛采用的技术。
通过对SMIC 180nm工艺的概述,我们为读者建立了一个对这一关键半导体技术节点的基本理解,并为后续章节中关于工艺理论、测试、优化和案例研究等内容的讨论奠定了基础。
# 2. 理论基础与工艺参数
## 2.1 半导体工艺的基础知识
半导体工艺是电子技术发展的基石,其核心是晶体管。晶体管的发明开启了现代电子设备小型化、高效率和高可靠性的时代。理解晶体管的工作原理对于深入掌握SMIC 180nm工艺至关重要。
### 2.1.1 晶体管的工作原理
晶体管,一种可控制电流流动的半导体设备,主要有两种类型:双极型晶体管(BJT)和金属氧化物半导体场效应晶体管(MOSFET)。MOSFET因其低功耗和高输入阻抗在集成电路中被广泛使用。MOSFET的工作原理基于电场控制半导体通道中载流子(电子或空穴)的流动。
MOSFET有两个主要部分:栅极(Gate)和源极/漏极(Source/Drain)。当在栅极上施加电压时,会在栅极下方的半导体材料中形成一个电场。根据电场的强度和方向,这可以吸引或者排斥载流子,从而控制源极和漏极之间的电流。在N型MOSFET中,增加负电压时,栅极下方形成一个电场,它排斥电子,从而减少了从源极流向漏极的电子数量,这样就减少了电流。相反,在P型MOSFET中,增加正电压时会吸引电子,增加了从源极流向漏极的电子数量。
### 2.1.2 工艺参数对性能的影响
半导体工艺的参数直接影响到晶体管以及集成电路的性能。这些参数包括但不限于晶体管的尺寸、阈值电压、工作电压、通道长度和宽度。随着工艺节点的缩小,晶体管尺寸也相应缩小,这带来了更高的速度和更低的功耗。
例如,阈值电压(Vth)是使MOSFET从截止状态转变为导通状态所需要的最小栅极电压。阈值电压的优化可以减少静态功耗并提高开关速度。通道长度直接关联到晶体管的开关速度,通道长度越短,晶体管的开关速度就越快。然而,当尺寸缩小到一定程度时,量子效应和短沟道效应会影响晶体管的性能。
## 2.2 180nm工艺特点
180nm工艺,是半导体行业中一个重要的里程碑,它在当时推动了高性能电子设备的发展。该工艺节点的特点不仅在于它实现了更高的集成度,还在于它引入了多项改进技术,如铜互连和低介电常数材料,以减少寄生电容和提高信号传输速度。
### 2.2.1 工艺节点的技术要求
180nm工艺节点的技术要求比之前的工艺节点更为严格。例如,为了确保电路的性能,需要对晶体管的尺寸进行精确控制,并且对杂质分布的控制也变得更加关键。随着特征尺寸的缩小,晶体管的开关速度和信号传输速度得以提高,但同时导致了更高的功耗和更难以管理的漏电流。
为了满足这些要求,180nm工艺采用了更先进的光刻技术,允许更小的特征尺寸的创建。此外,对杂质的掺杂水平、退火处理和化学机械抛光(CMP)技术等工艺步骤也进行了细化和改进,以提高晶体管的一致性和可靠性。
### 2.2.2 特征尺寸与电路密度
特征尺寸是半导体制造工艺中定义晶体管最小尺寸的指标。180nm工艺中,特征尺寸指的是晶体管通道长度的最小尺寸。在这一尺度下,可以实现更高的电路密度。电路密度的提高意味着在相同面积的芯片上可以集成更多的晶体管,从而提高了芯片的功能和性能。
更高的电路密度也带来了散热和电源管理的挑战。随着晶体管数量的增加,芯片上的功耗密度也相应增加,这要求更有效的热管理解决方案。此外,更高的晶体管密度对互连结构提出了更高的要求,以确保电路中各个部分的信号能高效传输。
## 2.3 工艺流程解析
半导体制造过程分为前端制程和后端制程,前端制程主要是晶体管的制造,而后端制程关注的是互连结构的构建以及封装。
### 2.3.1 前端制程的关键步骤
前端制程包括多个关键步骤,从开始的晶圆制备到晶体管的最终形成。这一过程包括氧化、光刻、蚀刻、离子注入、化学气相沉积(CVD)、物理气相沉积(PVD)等步骤。
- **氧化**是形成硅氧化物层的关键步骤,它提供了绝缘层,对晶体管的栅极构建至关重要。
- **光刻**是利用光刻掩模将电路图案转移到晶圆上的过程。180nm工艺需要使用更短波长的光源,例如深紫外(DUV)光,以实现更小的特征尺寸。
- **蚀刻**将未被光刻胶保护的材料去除,形成晶体管等结构。
- **离子注入**是将掺杂元素注入硅晶片中,形成P型和N型区域,进而形成源极和漏极。
- **化学气相沉积(CVD)**和**物理气相沉积(PVD)**是在晶圆表面沉积各种材料层的方法。
前端制程的每一个步骤都需要精细控制,以确保晶体管具有正确的物理和电学特性。
### 2.3.2 后端制程的关键步骤
后端制程是在晶体管制造完成后进行的,包括金属层的沉积和图案化,形成用于连接各个晶体管的铜互连。
- **金属层沉积**主要通过化学气相沉积(CVD)和物理气相沉积(PVD)技术,将铜沉积到晶圆上,之后通过CMP技术将铜层磨平。
- **图案化**使用光刻技术,将铜互连图案转移到光刻胶上,然后通过蚀刻过程实现铜互连的精确形成。
后端制程的挑战在于如何处理由于缩小特征尺寸带来的串扰问题,以及铜互连的可靠性问题。此外,确保互连层之间绝缘、减少信号延迟和散热量是后端制程设计的关键考虑因素。
以上是第二章
0
0
相关推荐







