生产管理与排程优化方案
发布时间: 2024-11-29 15:43:38 阅读量: 29 订阅数: 48 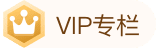
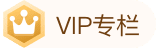
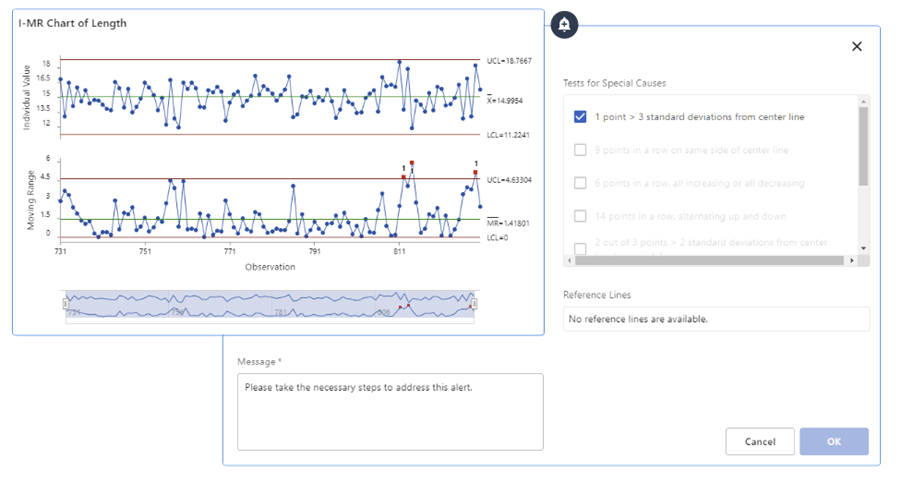
参考资源链接:[鼎捷ERP全套操作参考手册](https://wenku.csdn.net/doc/6412b6e6be7fbd1778d485f0?spm=1055.2635.3001.10343)
# 1. 生产管理与排程优化基础
生产管理是企业运营的核心部分,其主要目标是确保产品和服务的高效和有效生产。排程优化在这一过程中扮演着关键角色,通过合理安排资源和活动,减少浪费、提高生产效率。本章节将从基础层面探讨生产管理与排程优化的核心概念和基础实践。
## 1.1 生产管理与排程优化的定义
生产管理是指运用科学的方法对生产过程中的人员、物料、设备、资金等资源进行计划、组织、指挥、协调和控制,以达到既定生产目标的一系列活动。而排程优化是生产管理中的一项关键环节,其目的是通过各种方法与策略,合理安排生产活动,以最小的成本达到最优的生产效率。
## 1.2 排程优化的重要性
在不断变化的市场环境中,一个企业的竞争力很大程度上取决于其生产过程的灵活性和效率。排程优化能够帮助企业在资源有限的情况下,做出最合理的生产安排,实现成本的节约、交货期的缩短以及产品质量的提升,从而提高整体竞争力。
## 1.3 基础实践:优化步骤和方法
实现排程优化需要遵循以下基础步骤:
1. 明确生产目标和资源限制。
2. 收集和分析生产数据。
3. 设计和评估排程方案。
4. 执行最优排程并进行实时监控和调整。
不同的生产环境和需求可能需要不同的优化方法,例如线性规划、约束满足问题(Constraint Satisfaction Problem, CSP)或模拟技术等。
本章总结了生产管理与排程优化的基本概念,为后续章节深入探讨理论框架、核心算法及实践案例奠定了基础。
# 2. 生产管理理论框架
### 2.1 生产管理的定义和目标
生产管理是企业运营管理的核心部分,它涉及规划、组织、指导、协调和控制生产过程中的各项活动。其目的是提高生产效率,降低成本,确保产品质量,满足客户需求,提升市场竞争力。
#### 2.1.1 生产管理的五大职能
生产管理的五大职能通常包括:计划、组织、人事、指导和控制。
- **计划(Planning)**:确定生产目标、生产规模、生产方法和时间表。涉及物料需求计划(MRP)、生产能力和生产进度的计划。
- **组织(Organizing)**:构建生产所需资源的结构,包括人员、设备、原材料等。
- **人事(Staffing)**:招聘、培训和管理生产人员,确保团队技能和知识水平与生产需求相匹配。
- **指导(Directing)**:指挥和引导生产活动,确保生产过程顺利进行。
- **控制(Controlling)**:监控生产活动,确保生产按计划进行,调整偏差,保障生产目标的实现。
#### 2.1.2 生产管理的目标与任务
生产管理的最终目标是创造效益,具体包括以下几个方面:
- **效率最大化**:通过资源的合理分配和生产流程的优化,提高生产效率。
- **成本控制**:降低生产成本,提高成本效益。
- **质量保证**:确保生产出的产品或服务符合质量标准。
- **交期保证**:确保按时完成生产任务,及时交付产品。
- **持续改进**:持续改进生产方法和流程,提升整体竞争力。
### 2.2 生产流程与作业设计
生产流程的设计和作业的设计是生产管理中的重要组成部分,它直接关系到生产效率和产品质量。
#### 2.2.1 生产流程的划分与优化
生产流程可以从宏观和微观两个层面进行划分和优化:
- **宏观层面**:涉及生产过程的整体设计,如选择生产技术、布局生产线、安排生产周期等。
- **微观层面**:关注具体工序的安排,优化作业顺序,减少不必要的等待和移动时间。
优化生产流程时,可以运用价值流图(Value Stream Mapping, VSM)来识别和消除浪费。
#### 2.2.2 作业设计的原则和方法
作业设计旨在确保工作人员能够高效、安全地完成生产任务。设计原则包括:
- **人机工程学原则**:考虑人的身体和心理特点,设计合适的作业环境和工具。
- **工艺原则**:确保作业设计与生产工艺要求相匹配。
- **经济原则**:追求投入与产出比最大化。
作业设计的方法主要有作业分解和作业组合。例如,可以利用作业组合矩阵(Job Combination Matrix)来分析不同作业的组合效率。
### 2.3 生产计划与控制
生产计划与控制是生产管理的日常工作,确保生产活动按照既定计划进行,并及时调整偏差。
#### 2.3.1 生产计划的基本类型
生产计划主要分为以下类型:
- **长期计划**:涉及企业产能扩张、重大设备投资等战略性决策。
- **中期计划**:涉及年度或季度的生产目标设定、资源分配等。
- **短期计划**:包括周计划、日计划,关注具体的生产任务安排。
#### 2.3.2 生产控制的关键要素
生产控制涉及的关键要素包括:
- **进度控制**:确保生产按照既定时间表进行。
- **库存控制**:有效管理原材料、在制品和成品库存。
- **质量控制**:防止不合格品流入下一生产环节或市场。
运用生产信息系统(如MES、ERP系统)是实现生产计划与控制的关键。例如,MES系统可以帮助实时跟踪生产进度,并及时作出调整。
以上是生产管理理论框架的主要内容,为生产管理提供了系统性的分析框架和方法论,为后续章节中关于排程优化的深入讨论奠定了基础。接下来的章节将探讨排程优化的核心算法,为生产管理的实践操作提供理论依据。
# 3. 排程优化的核心算法
## 3.1 排程优化问题概述
### 3.1.1 排程优化的重要性
排程优化在生产管理中占据了核心地位,原因在于它直接影响到企业的生产效率和成本控制。在高度竞争的市场环境中,企业必须以最小的资源消耗生产出最大数量的产品,同时保证产品质量和交付时间。这就要求企业必须对其生产过程中的各个环节进行细致的规划和调整,而排程优化正是达成这些目标的有效手段。
排程优化不仅可以减少资源的浪费,提高设备的利用率,还可以缩短生产周期,提升对客户需求的响应速度。有效的排程优化能够使生产过程更加灵活和敏捷,以适应市场的快速变化。
### 3.1.2 排程优化的常见问题
尽管排程优化对企业的重要性不言而喻,但在实际操作中仍然存在许多问题和挑战。常见的问题包括:
- 数据不准确:排程优化需要大量的准确数据作为支持,但现实中往往难以获得完整准确的数据。
- 环境多变:生产环境可能会受到突发事件的影响,如设备故障、原材料短缺等,给排程带来不确定性。
- 系统复杂:现代生产系统具有高度的复杂性,其中涉及的变量众多,使得优化模型和算法的选择与应用变得更加困难。
- 优化过度:过度优化可能会导致生产系统的脆弱性增加,对系统的微小变动过于敏感,反而降低了整体的适应能力。
## 3.2 排程优化算法理论
### 3.2.1 算法分类与选择
在排程优化领域,存在多种算法可供选择,包括启发式算法、元启发式算法、混合算法等。这些算法通常针对不同类型的排程问题,如单机排程、流水线排程、作业车间排程等。
启发式算法如优先规则法、最近邻居法等,它们通常基于简单的规则或者局部搜索,适用于求解规模较小或者对解的质量要求不高的问题。而元启发式算法,如遗传算法(GA)、模拟退火算法(SA)、蚁群算法(ACO)、粒子群优化算法(PSO)等,则适用于求解更复杂的优化问题。
选择何种算法往往需要根据实际问题的特点和要求来决定。在选择算法时,需要考虑问题的规模、复杂度、是否需要实时优化以及计算资源的限制等因素。
### 3.2.2 算法的数学模型
排程优化问题通常可以表示为一个数学模型,包括目标函数和约束条件。目标函数定义了优化的目标,如最小化总延迟时间、最大化设备利用率或者最小化生产成本等。约束条件则指定了问题的限制,包括资源限制、时间限制、技术限制等。
在建立数学模型后,可以使用不同的优化技术来求解模型,得到一个或一组最优解。例如,线性规划用于可线性化的目标函数和约束条件;整数规划或混合整数线性规划(MILP)适用于那些决策变量需要为整数的问题;动态规划适用于多阶段决策问题。
## 3.3 实践中的排程优化技术
### 3.3.1 遗传算法在排程优化中的应用
遗传算法是一种模拟自然选择和遗传机制的搜索算法,非常适合用于解决复杂的优化问题。在排程优化中,遗传算法通过模拟种群的进化过程来寻找最优的排程方案。
遗传算法的基本步骤如下:
1. 初始化:随机生成一组候选解作为初始种群。
2. 选择:根据适应度函数对种群中的个体进行评估,并选择较好的个体遗传到下一代。
3. 交叉(杂交):将选定的个体配对,通过交换部分基因产生后代。
4. 变异:以一定的概率对个体的部分基因进行随机改变,以增加种群的多样性。
5. 重复执行2到4步,直至满足终止条件(如达到预设的迭代次数或解的质量达到标准)。
通过不断的迭代进化,遗传算法能够逐渐逼近最优解或者找到一个足够好的近似解。
```python
# 示例代
```
0
0
相关推荐








