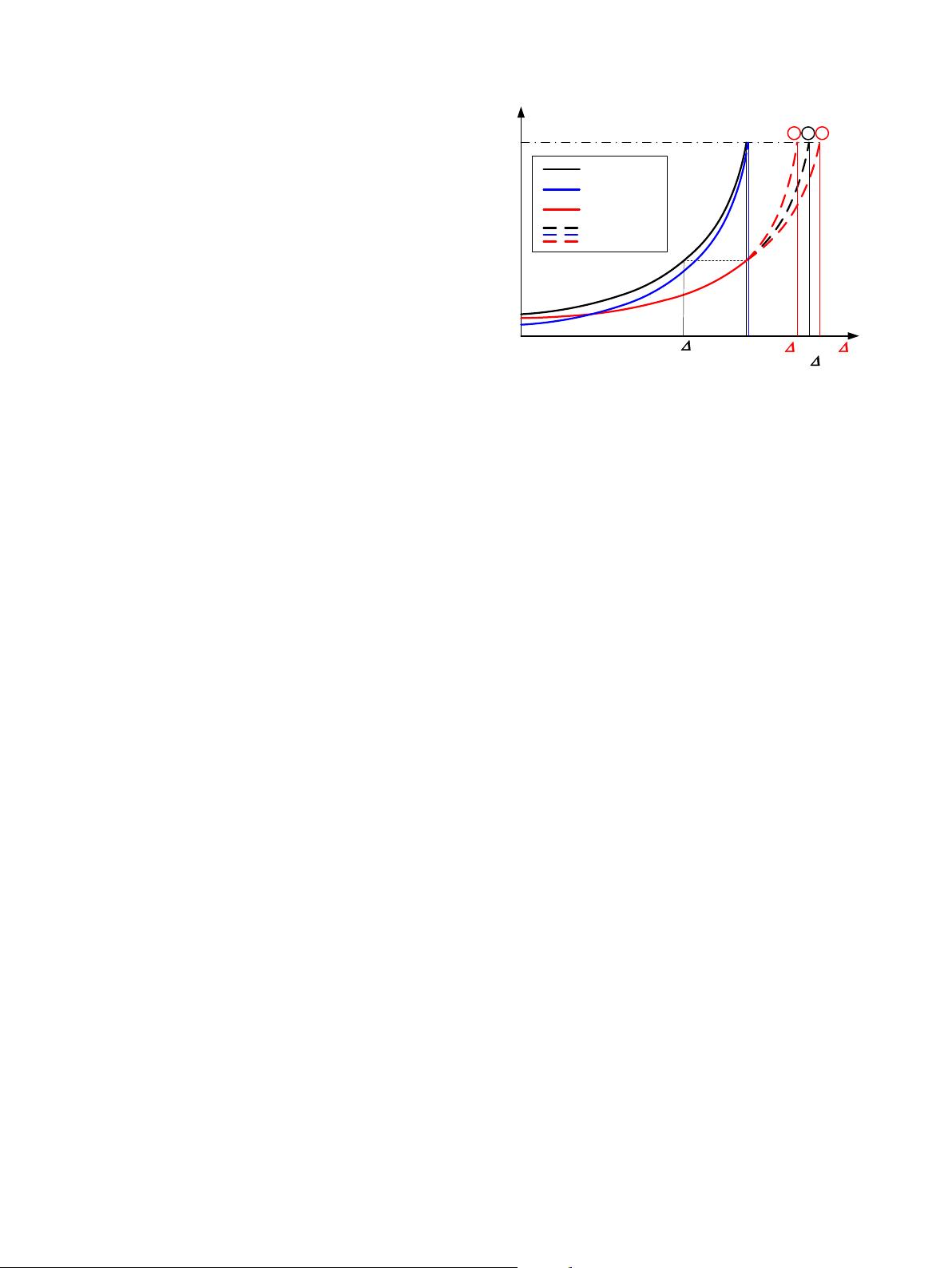
However, the NDCE theoretical pack capacity is achieved with
appropriate EAs which should ensure all the cells were fully
charged and discharged and no energy loss should occur during
energy transfer from cell to cell. If the pack is constructed with
cell screening and cell capacity difference is less than 5% during
cycling, pack capacity difference between DCE and NDCE with an
appropriate EA is less than 2.5% (Section 5.1 shows one example).
The cost of NDCE is high and both hardware and EAs are difficult
to realize, but pack capacity attributed by NDCE is small if cell
capacities are properly screened.
Therefore we suggest that DCE is suitable for on-line battery
pack equalization in EVs and NDCE should be applied for off-line
equalization for the purpose of battery pack maintenance.
2.2. Equalization algorithms
As mentioned in Chapter 1, EAs are divided into three categories,
i.e. voltage-based, SOC-based and pack capacity-based EAs.
Voltage-based EAs are the most feasible to realize because of the
direct measured cell voltages. However, real time voltage-based EAs
[15e21] would suffer from over-equalization when the cell capac-
ities and internal resistances are different: some cell need to be
charged by the equalizer for a while, but it is discharged by the
equalizer later/earlier in the same cycle. To solve the problem,
single-point voltage-based EAs are proposed: when the mean cell
voltage reaches a certain voltage, EAs compare the voltages and
begin to equalize [22]. Fully discharged or fully charged voltage-
based EAs which ensure cells are discharged or charged to the
same target voltage are cases of single-point voltage-based EAs. For
SOC-based EAs, over-equalization would also happen because of
the cell capacity variation: The cell with the minimum cell capacity
tends to have a higher SOC when cells are near fully charged state
and it will have a lower SOC when cells are near the fully discharged
state. Similar to single-point voltage-based EAs, single-point SOC-
based EAs are proposed. Fully discharged and fully charged SOC-
based EAs are also cases of single-point SOC-based EAs.
As voltage- and SOC-based EAs cannot directly represent the
ultimate purpose of the equalization (to maximize pack capacity),
pack capacity-based EAs are proposed [14]. However, pack capacity-
based EAs need accurate cell SOC and capacity estimation and thus is
difficult for on-line application.
3. The RCCEeDCE algorithm
As analyzed in Chapter 2, we suggest that DCE is suitable for on-
line battery pack equalization in EVs. The objective of pack
capacity-based EAs for DCE is to make full use of the cell with the
minimum capacity. Nevertheless accurate cell SOCs and capacities
are difficult to estimate on-line. In this part, by RCCE we try to use
DCE to make all the cells with the same RCCs and finally fully charge
all the cells. Once all the cells are fully charged, the cell with the
minimum capacity is fully used and pack capacity will be the DCE
theoretical pack capacity.
The key idea of RCCE is based on the uniform CCVC hypothesis
which believes that different internal resistances are eliminated by
CCVC vertical translations, different initial remaining cell capacities
are compensated by CCVC horizontal translations and by horizontal
scaling, influence of different cell capacities are eliminated [13].
We first investigate a schematic scene of CCVCs under constant
current charging in the battery pack as shown in Fig. 1.Cell1inthe
solid black curve in Fig.1 reaches the charge cutoff voltage, and it is set
as the reference cell. The internalresistance of Cell 2 is lower than that
of Cell 1 but they have the same capacities and SOCs. According to the
uniform CCVC hypothesis, CCVC of Cell 2 shown in the solid blue curve
(in the web version) is a downward vertical translation of Cell 1’s
CCVC. Because the internal resistance of Cell 2 is lower, the voltage of
Cell 2 does not reach the charge cutoff voltage when pack is fully
charged at time t
0
. Nevertheless, the slope of Cell 2’s CCVC at time t
0
is
large, and if we continue to charge Cell 2, the charging curve would be
a very short blue curve as shown in Fig.1. That indicates the RCC of Cell
2 is so small that we may ignore the influence of the different internal
resistance for simplicity. Hence, we do not consider the influence of
the different internal resistance for Cell 3. Instead, we suppose a scene
thatSOC of Cell 3 islower than thatof Cell 1 and the capacity of Cell 3 is
undetermined. According to the uniform CCVC hypothesis, similarly,
CCVC of Cell 3 shown in the solid red curve is a right horizontal
translation and horizontal scaling of Cell 1’s CCVC. If we continue to
charge Cell 3, the possible charging curve might be the black or red
dashed curves as shown in Fig. 1. The dashed black curve ⓪ is a direct
right horizontal translation of Cell 1’s CCVC. Because the capacity ratio
between Cell 3 and Cell 1 k is unknown, the remaining charging curve
of Cell 3 could be scaled as the dashed red curve ① or ②. N evertheless,
the RCC of Cell 3 can be expressed as follows
C
RC
¼ kI
D
t
0
(2)
where C
RC
is the RCC, I is the constant charging current and k is the
capacity ratio as well as the scaling factor. Because capacity dif-
ference in a battery pack is generally less than 20%, we can set the
bound of scaling factor k ˛ (0.8 1.2). The calculation of
D
t
0
is
demonstrated as an example in Fig. 1 with dotted black lines:
D
t
0
is
the difference between pack fully charged time t
0
and the time
achieved by interpolation of Cell 3’s voltage at t
0
in CCVC of Cell 1.
As k is undetermined, RCC cannot be precisely calculated. If the
pack is properly constructed with cell screening, k is approximately
1. Thus, we set k ¼ 1 in Equation (2) for RCCE,
b
C
RC
¼ I
D
t
0
(3)
8 cells in the same batch with a nominal capacity of 7.5 Ah are
tested to verify the precision of RCCE. Cells are initially fully charged
and afterward are released approximately 1 Ah. Finally the cells are
charged at the same constant current until they reach the charge
cutoff voltage. CCVCs of the final charging process are shown in
Fig. 2. If we connect these 8 cells in series, Cell 1 would be fully
charged at t
0
as depicted in Fig. 2. Other cells could not be further
charged and the charging curves after t
0
would be unavailable.
Thus, by independently charging the cells with the same current,
the pack charging process can be easily simulated till t
0
, and the
charging curves of other cells after t
0
are also available for RCCE
verification. Take Cell 6 for instance in Fig. 2, the precision of RCCE
of Cell 6 can be achieved by comparing
D
t
0
and
D
t which are
U
t
Charge cutoff Voltage
Cell 1
Cell 2
Cell 3
Possible
charge curves
t
0
t
0
- t
0
t
0
+ t
0
t
0
+ t
1
t
0
+ t
2
1 2
0
Fig. 1. Schematic diagram of RCCE based on CCVCs.
Y. Zheng et al. / Journal of Power Sources 247 (2014) 676e686678